About Group Assignment
Task for the group assignment is to Review the safety data sheets for each of molding and casting materials in our lab.Make and compare test casts with each of them.Discuss the parameters with the group members.For the Group assignment we are having different materials in our lab are HydroStone, Silicon Rubber, FlexWax, Machinable Wax, Epoxy Resin, Paraffin Wax etc. we divided the materials and test its proprties.One of our member also tried using Medimix soap for trials and testing.
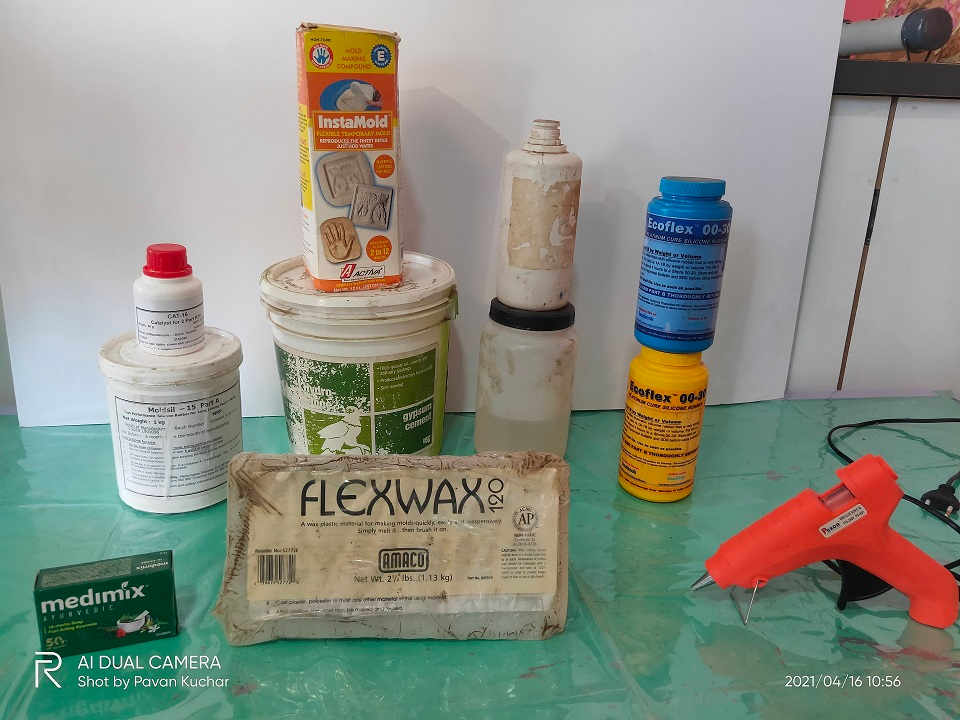
Molding and casting material.
About Moldsil Silicon(Part-A)
Moldsil 15 PLUS is a Room Temperature Vulcanizing Silicone Rubber for making strong and flexible molds for excellent reproduction of the master and having superb release characteristics. It is compatible with various master and casting material s. This grade has been specially designed to create molds with long life.For more details go through the Technical data sheet
Features
- Room temperature cure.
- Low viscosity - easy flow and excellent detail reproduction.
- Excellent mechanical properties - suitable for deep undercut moulding.
- Good chemical resistance - compatible with various casting materials.
Catalyst (Part-B)
The choice of catalyst depends on the application method and the speed of cure needed. Moldsil-15 can be cured in to elastomeric products using the following cure options:
- CAT-24 : Slow catalyst,Takes about 24 hours at room temperature .
- CAT-16 : Medium speed Catalyst,Takes about 16 hours at room temperature.
- CAT-04 : Rapid Catalyst,Takes about 4 hours at room temperature
Catalyst Properties
Handling Precautions and Safety
mouldsil-15 PLUS contains constituents that have been found to be safe. Hence special handing precautions except general industrial hygiene need to be followed. Catalysts (CAT-24, CAT-16 and CAT-04) contain organo-tin compounds and are flammable and might cause irritation upon contact with eyes and skin. Adequate protective measures are recommended. Refer to Material Safety Data Sheet (MSDS) for safe use of the product.
The result of mixing is as shown in the following image.
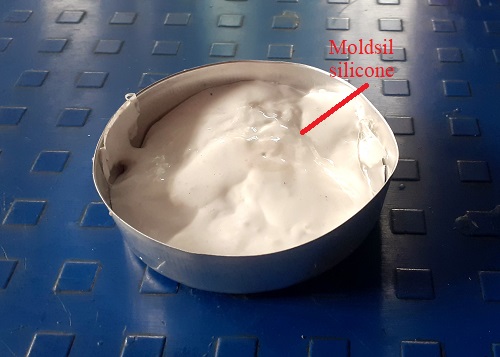
Casting moldsil silicone.
I also tried to make the mould by using mouldsil silicone the test reult is shown below.Note that take atleast 10% more than required material because at the time of measuring process some of the material stick to the container and we are not get required one.The mould is casted with hydrostone material.
Pouring Hydrostone.
Poured hydrostone
Silicone mould with cast material.
original coin and casted hydrogen coin.
About Flex Wax
A wax-plastic material for making molds quickly, easily, and inexpensively. Simply melt it, then brush it on or dip the object into it. Flexwax melts at 120°F (49°C) , a comfortably warm temperature. It cools in a few minutes to form a tough, flexible mold.
By using fles wax we can made the mould very easily.Take the piece of flex wax ,just heat the suraface ,it becomes soft to press the object have to make the mould.The result is shown in folowing image.
Cutting the wax in to pice.
Wax pice with coin.
Applying thumb pressure on coin.
Cion pressed in to the wax.
Removing coin fron the wax.
Flex wax coin mould is ready.
Summary
- Moldsil Silicone is the good moulding material for hard casting.
- The curing time is more than 16 hours if uesd catalyst-16.
- Take atleast 10% more material than required.
- safety precautions are very important while handling material.
- Flex wax is very soft do not apply much pressure on it.
- Removed the casted material slowly,other wise the mould get deformed.
About Hydrostone
Pawan sir used Hydrostone for Making and comparing test casts. The datasheets could be found here.
Hydro stone mixing Instructions.
Mixing perportion of water in hydrostone.
Read about the HydroStone and its properties.About the Mixing and Pouring Instructions for it. Few Notable Instructions given are:
- 32 lbs. water/100 lbs. product (Hydro-Stone Gypsum Cement)
- Hand Mix Vicat Set, Target is 19 - 25 minutes (But it actually takes longer somewhere from 35 minutes to 45 minutes.)
- Sift or strew USG Hydro-Stone Gypsum Cement into the water slowly and evenly.
- Longer mixing times result in higher mold strength and shorter set times.
- Agitation/vibration of the filled mold is a further step used to prevent air at or near the mold surface.
- All casts should be dried as quickly as is safely possible after manufacture so that maximum physical properties can develop.
- The temperature of the mixing flask increases after adding water and the Hydrostone.
Mistakes
- He didnt noted down the Instructions on the Notebook for Reference.
- He didnt wear Gloves while operating with HydroStone.
It was given in the Instruction to use 32 gms of Water for 100 gms of the HydroStone but while Weighing he forgot and did exactly opposite of the Instructions. He weighed only 32 gms of HydroStone and Mixed 100 ml Water from the beaker to it. It mixture became very thin / runny mixture. He kept on sheering / stirring and waited fir it to become viscous but Alas.
Mixing hydrostone in correct ratio.
Pouring Hydrostone in mold.
Test result of Hydrostone casting.
Summary
- If you want to Cast a Hard material like HydroStone, Use a Flexible mould like that of Silicone Rubber. This allows the Cast to come out of the mould easily.
- Drying and Curing Time is between 35 to 45 minutes. It is more than stated in the Brochure and Datasheet. It might be because of the the Quality of Water used, Heat/Temperature of the Room, Less Intense and Slow mixing etc.
- Use Handgloves while handling HydroStone as the temperature of the mixture increases. In case of Allergies, it may cause Skin Irritation as well.
- Add the HydroStone Powder Slowly to the Water for maintaining Consistency and proper mixing.
- Note down essential / critical information and keep it handy for reference.