Summary
- Design Output Microcontroller Board
- Creat New Project & Sketch KICAD
- Import Fab Library
- Import Components
- Connect Components
- Give Compoents correct name and value
- Annotate the design
- Assign Footprint to Symbols
- Generate Netlist
- Open Pcb New
- Read in Generate netlist
- In Pcb New Set Design Rules (Setup -Design Rules)
- Rearrange Components and Make Traces
- Place your Auxillary Axis
- Plot Layers
- Flatcam
- Tool dia 0.4
- Cutz -0.1
- Travel Z 2.5
- Feed Rate 0.3
- Spindle speed 1000
- Passes 2
- Solder Output Microcontroller Board
- Programming Output Microcontroller Board
Designing
For input week I decided to make a microcontroller board using the attiny45 microcontroller and for my sensors I choose to use the phototransistor as my analogue sensor and the dht sensor for my digital input sensor.I also added the avrisp for programming my board and the 6 pin header for connecting my htdi cable to read from serial.
Component list
Atiny 45-A
Phototransistor
Dht sensor
2x10k Ohm Resistors
1x 1uF Capacitor
1x Avr Isp Connector
1x 6x 1 Pin Connector
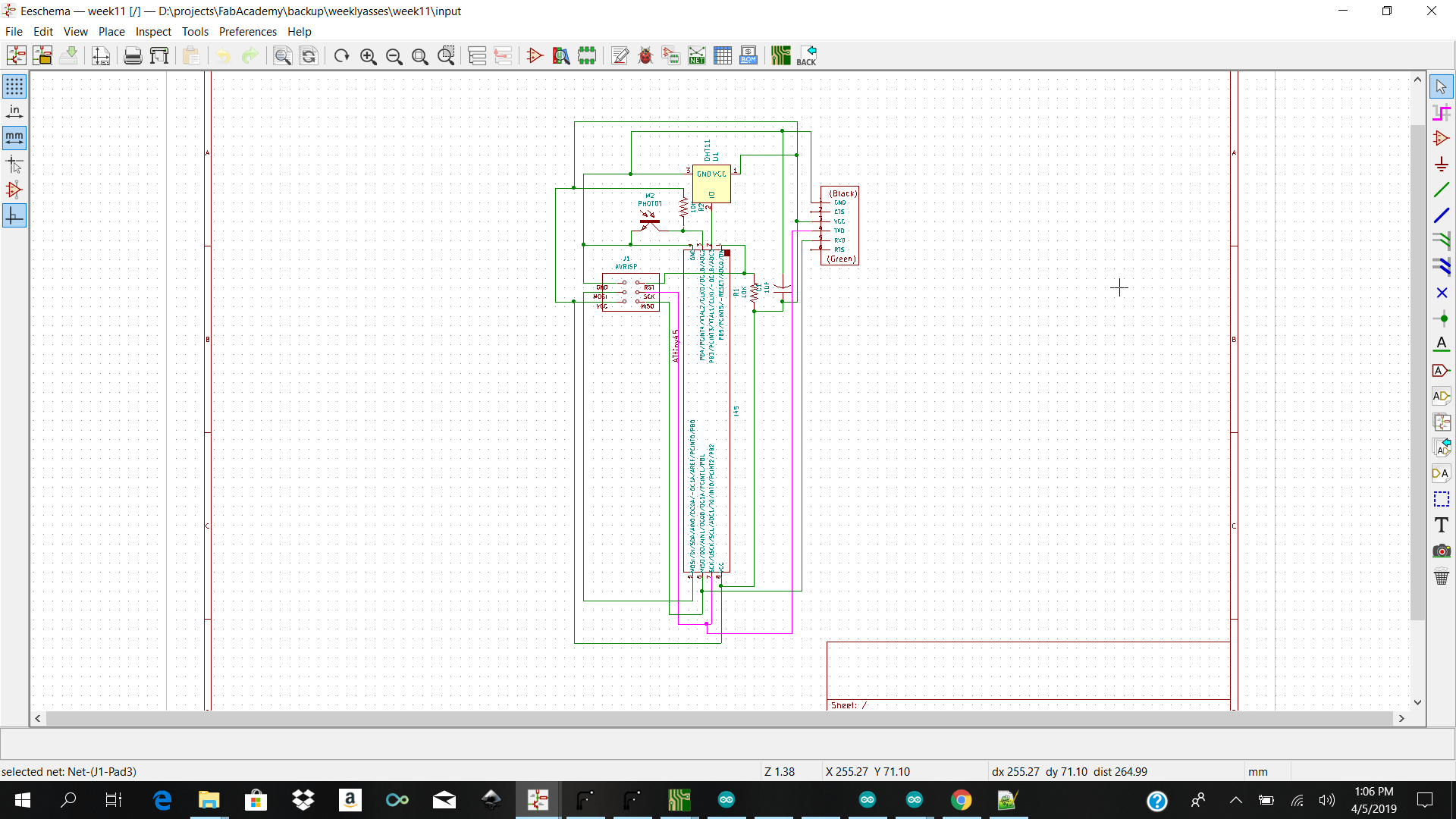
I then went ahead and started making my skematic in Kicad. I made a new project and started selecting my components from the fab library. I found most of my components from the fab library but I had to add my own library for the dht sensor. After making my schematic in kicad I went ahead and anotate to check if I had my tags labeled correctly.
After that I went ahead and selected assign footprint to pcb and added my footprint. I had an issue with my dht library which had 1 2 4 instead of 1 2 3 so I had to change the labels and save it as another library called sensor 2 then I selected that footprint for my dht sensor. I then selected on Generate netlist and imported my netlist for Pcbnew.
I then went ahead and choose my design rules from Setup → Design rules
My clearance was set to 0.2 and my track width was 0.35 because I was using a 0.4 mm bit for milling my pcb
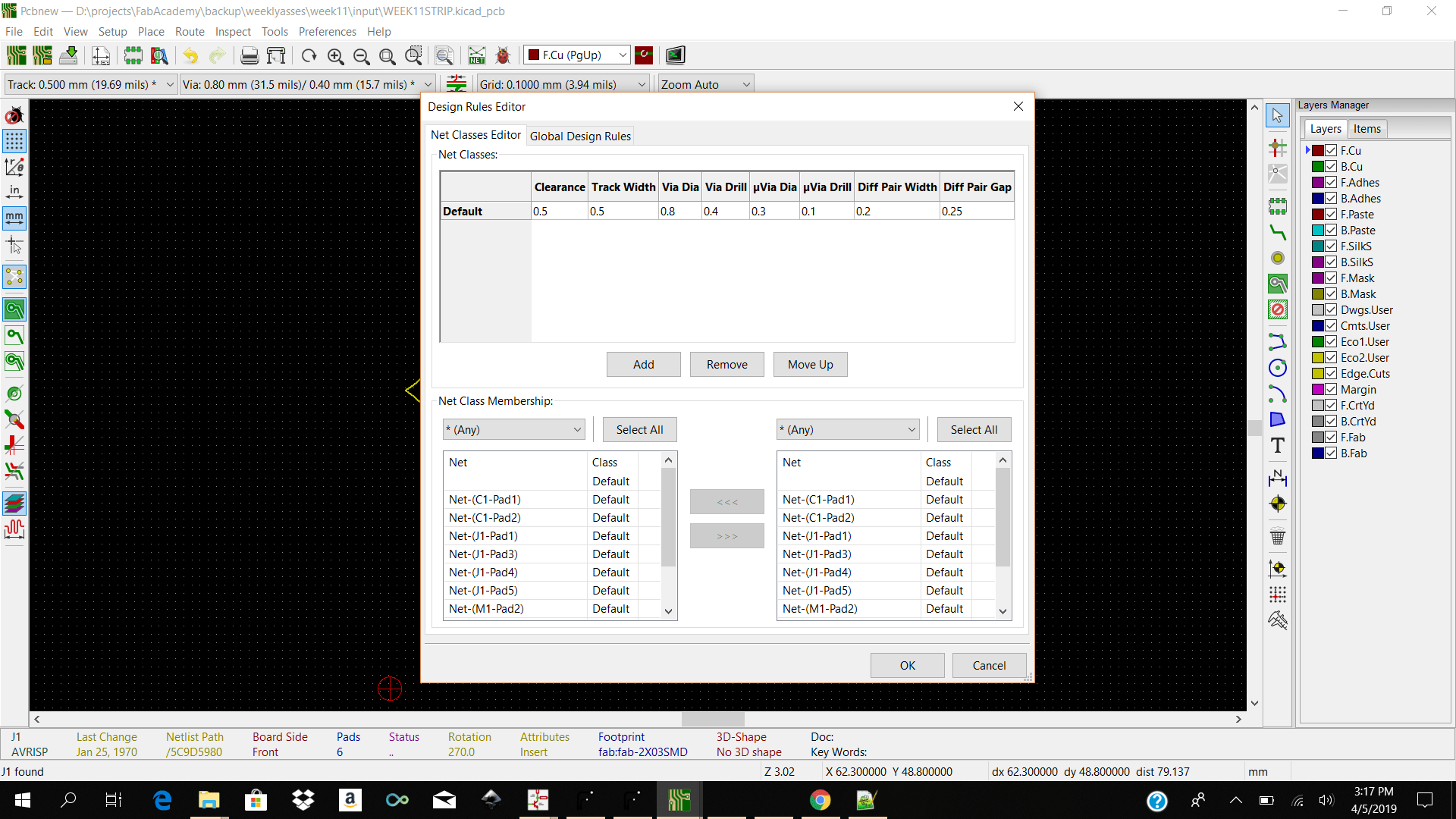
I had a stressful time routing my board initially but with the help of my local instructor I finally got the hang of it.
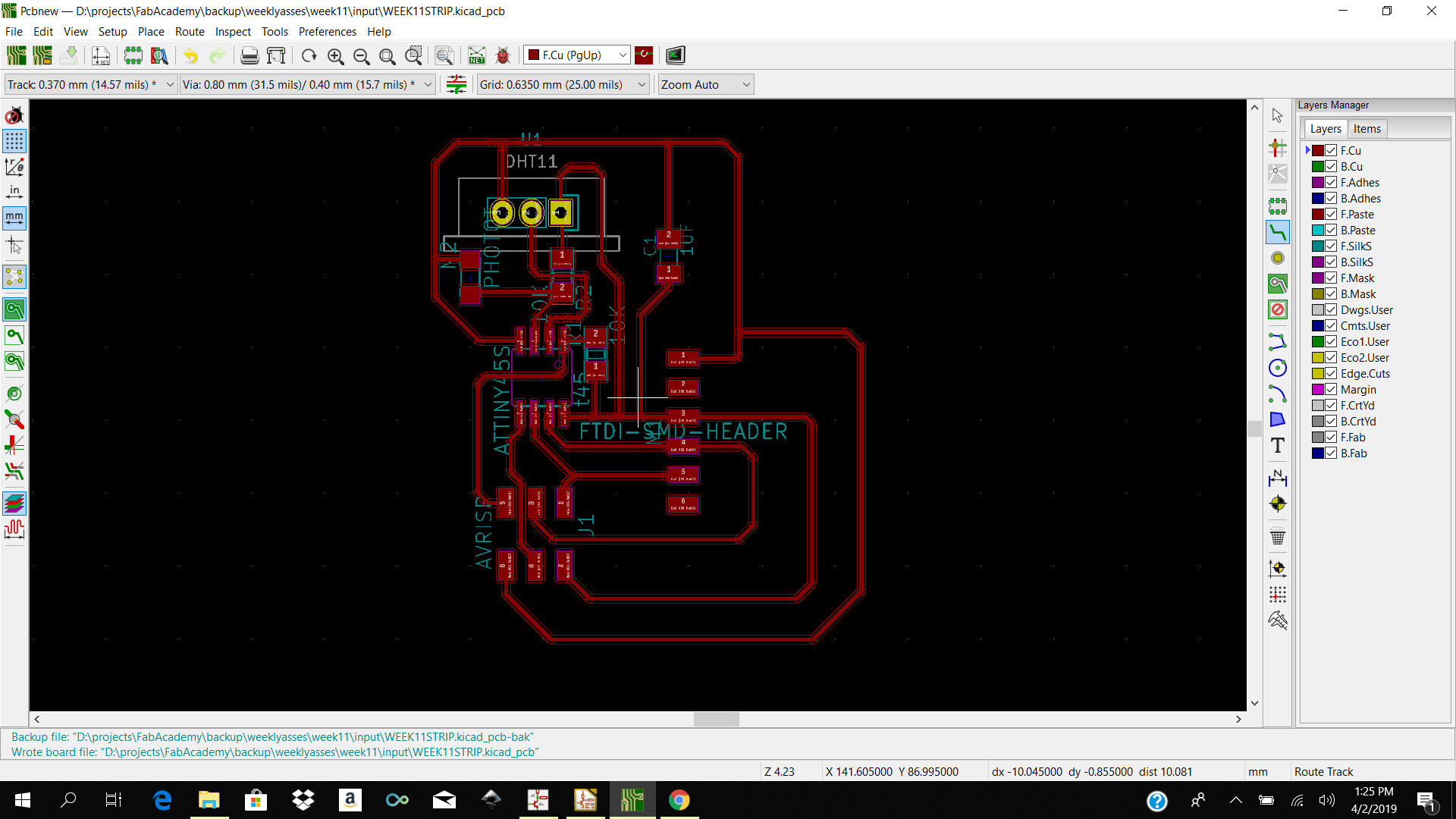
This week I wanted to try something new with my pcb design.Since I got the hang of working with kicad I decided to add a custom edge cut to my board.
I found a silhouette png which I liked from the internet I downloaded it and open it using Inkscape I then bittrace it using inkscape and resize it then export it as dxf. I then imported that dxf into librecad select the object and select explode to explode the traces.
I then saved my file from librecad to dxf and imported it as edgecut into kicad.The reason why I had to do so many steps is because when just bitracing my image in inkscape and importing it into kicad kicad does not detect all the lines.
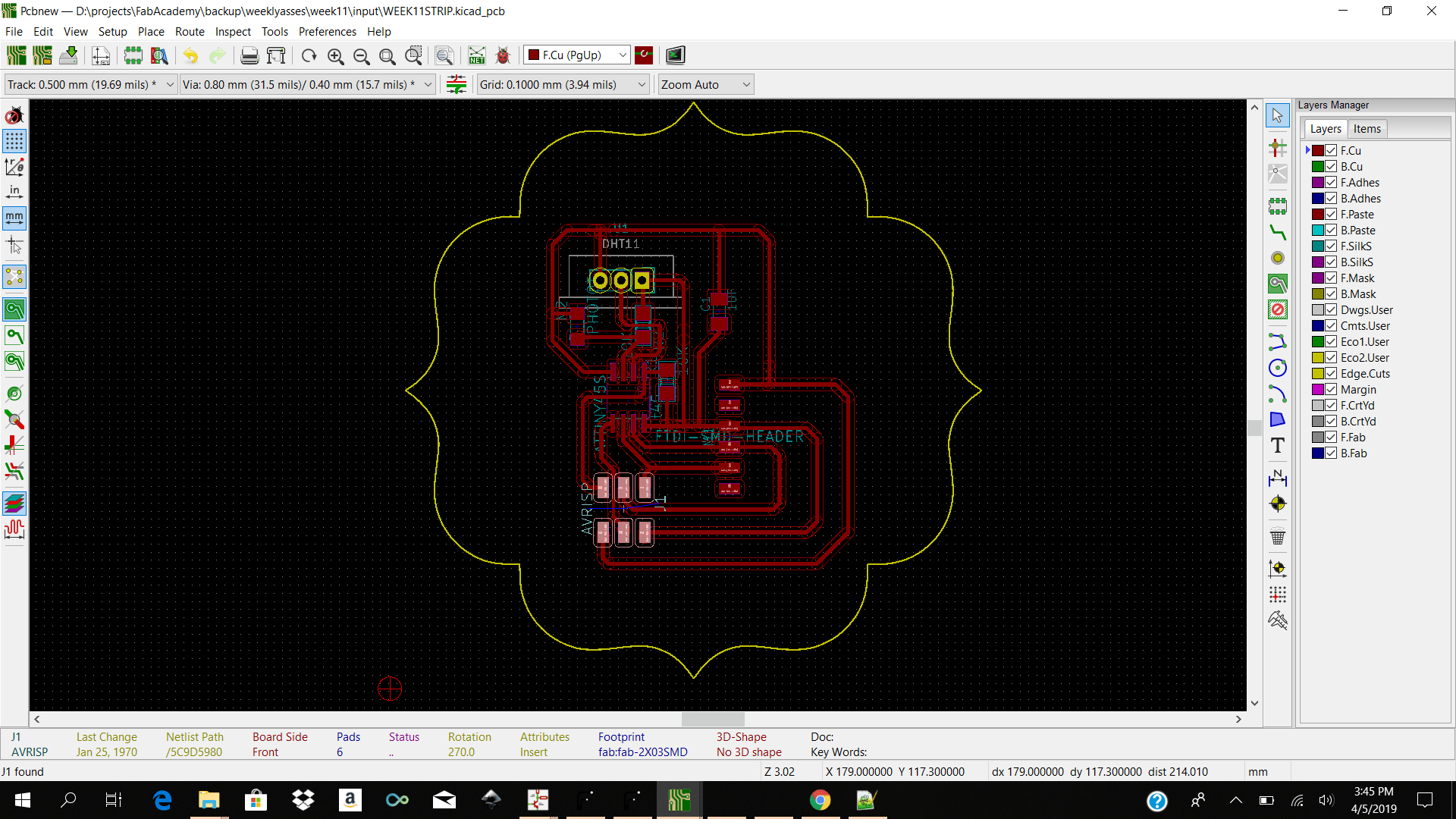
After importing my edge cut into kicad I then determined my auxillary origin using the place the auxiliary origin icon and went ahead and plot my layers. When plotting I checked off front and edge cut and if i wanted to get the file for making the holes in my pcb for the dht sensor I needed to select generate drill file. I did not want to make the hole in my pcb so I did not select generate drill files.
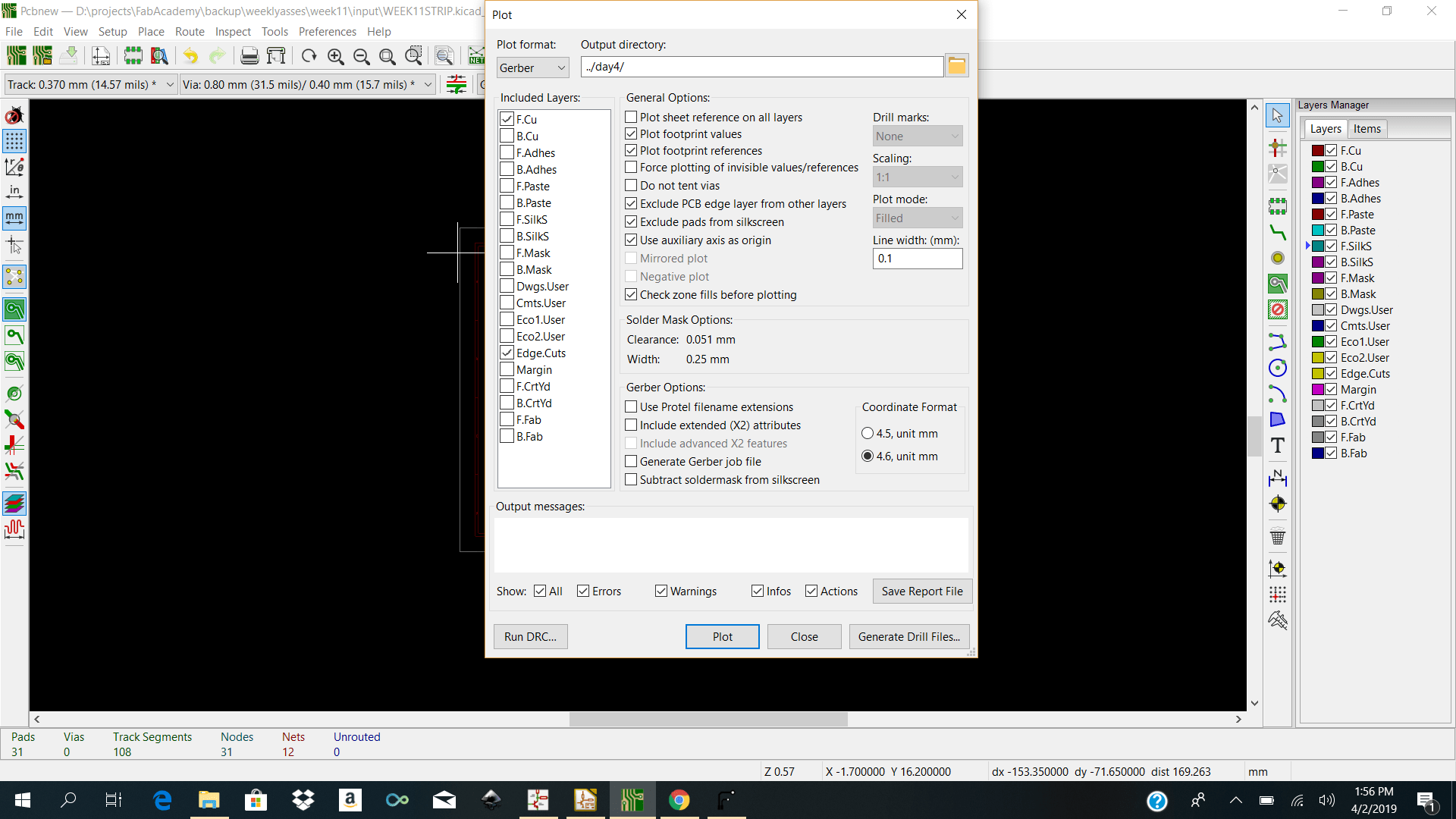
After generating my gerber files I then went ahead and open flatcam to add my parameters.
For the front cut I selected
Tool dia - 0.4
Passes -2
Cut Z -0.1
Travel Z- 2.5
Feed Rate 0.3
Spindle speed 1000
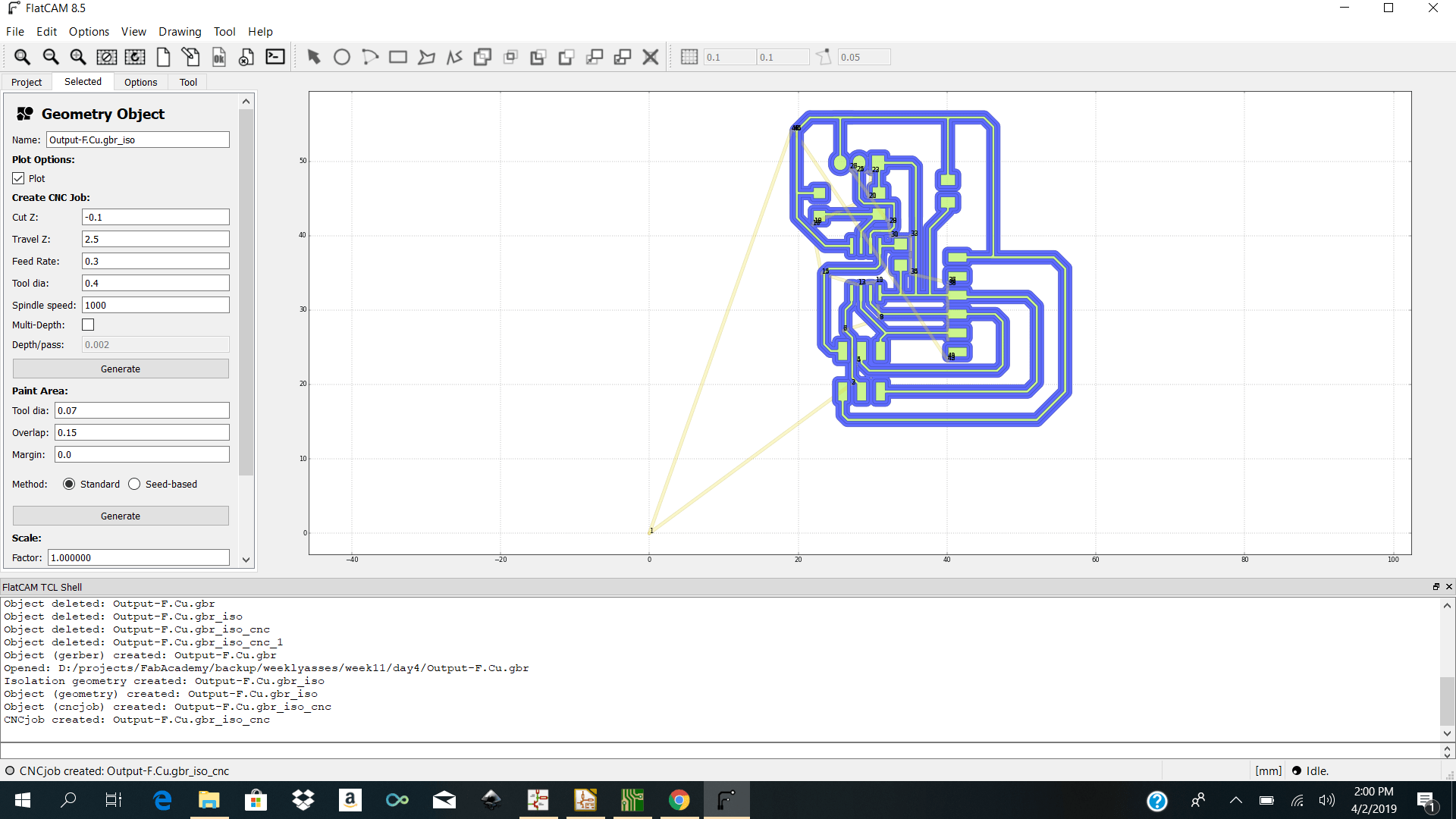
Edge Cut
Tool dia - 0.4
Passes -1
Cut Z - -1.5
Travel Z- 0.1
Feed Rate 3.0
Spindle speed 10000
Multip dept checked
Depth/Passes 0.5
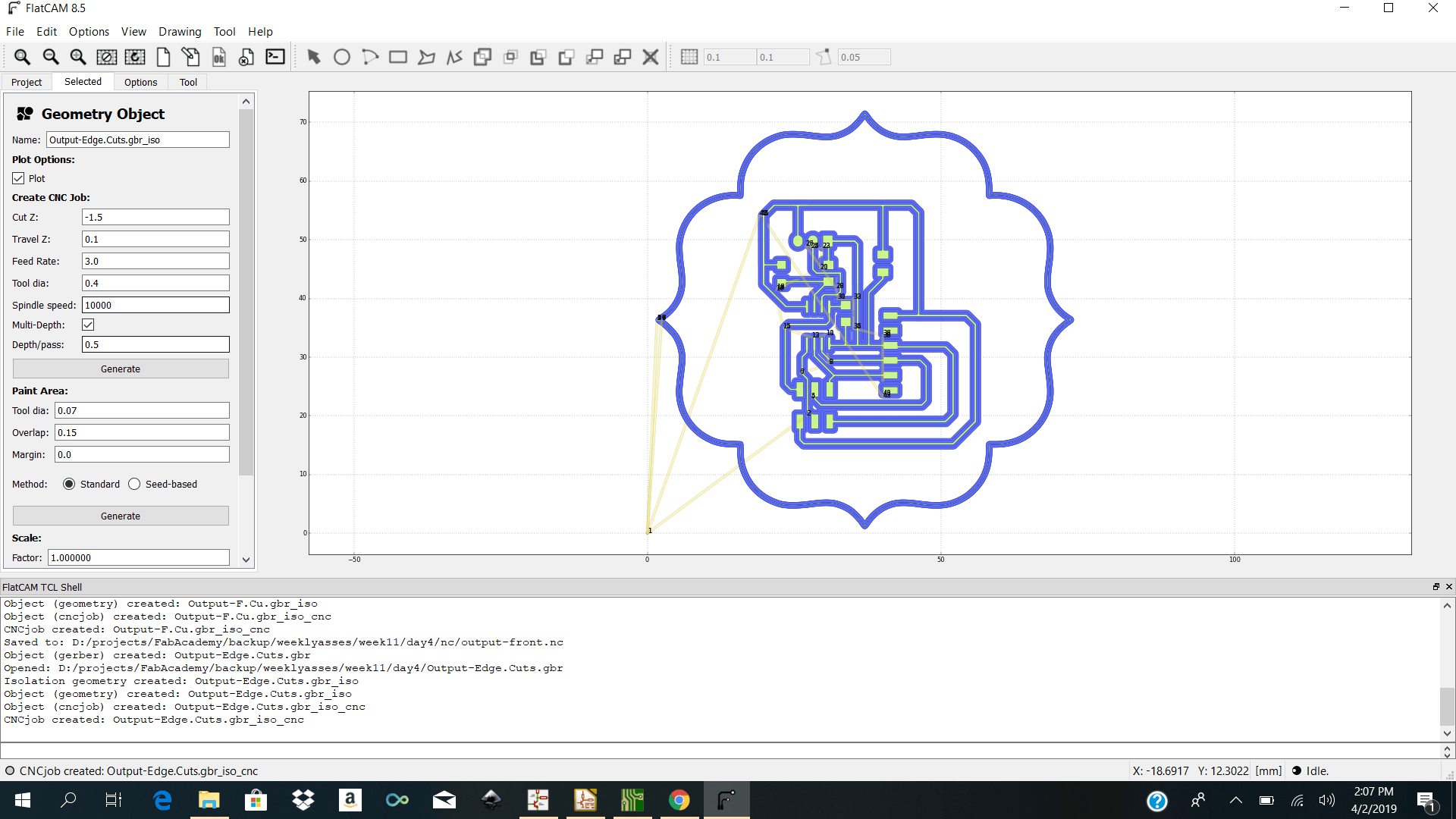
I then went ahead and generated my nc files for importing into winpc nc to control the stepcraft to cut the pcb.
Soldering
After I got my pcb milled I took the multimeter and checked my connections if all that needs to be connected is connected and all the does not need to be connected is not. I was so happy that all the connections were good.
I then went ahead and gathered my smd components and sensors and soldered my board.
Some things I had to keep in when soldering my pcb was that the phototransistor green connection was not the connection for gnd like the led instead it was the opposite.