Week 7
Make something big
Computer-Controlled Machining. Have you:
- Explained how you made your files for machining (2D or 3D)
- Shown how you made something BIG (setting up the machine, using fixings, testing joints, adjusting feeds and speeds, depth of cut etc)
- Described problems and how you fixed them
- Included your design files and ‘hero shot’ photos of final object
The group page assignment is:
Group Assignment PageI work with the Chiropractic Design inspired in Homer's idea
For design it I used Rhinoceros 3D and Grasshopper Definition that allows modify when the tests suggest changes .
After the design, I prepared the export with curves in two sheets and dxf format.
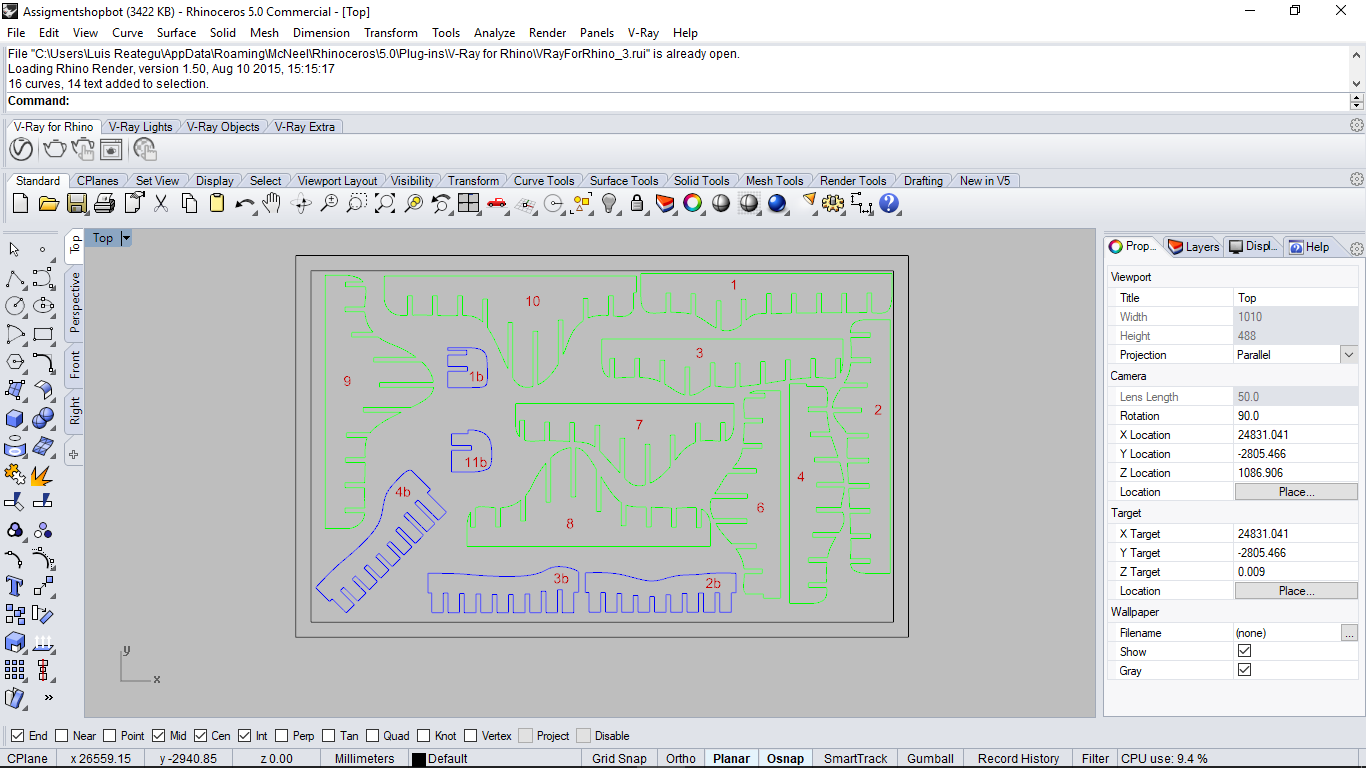
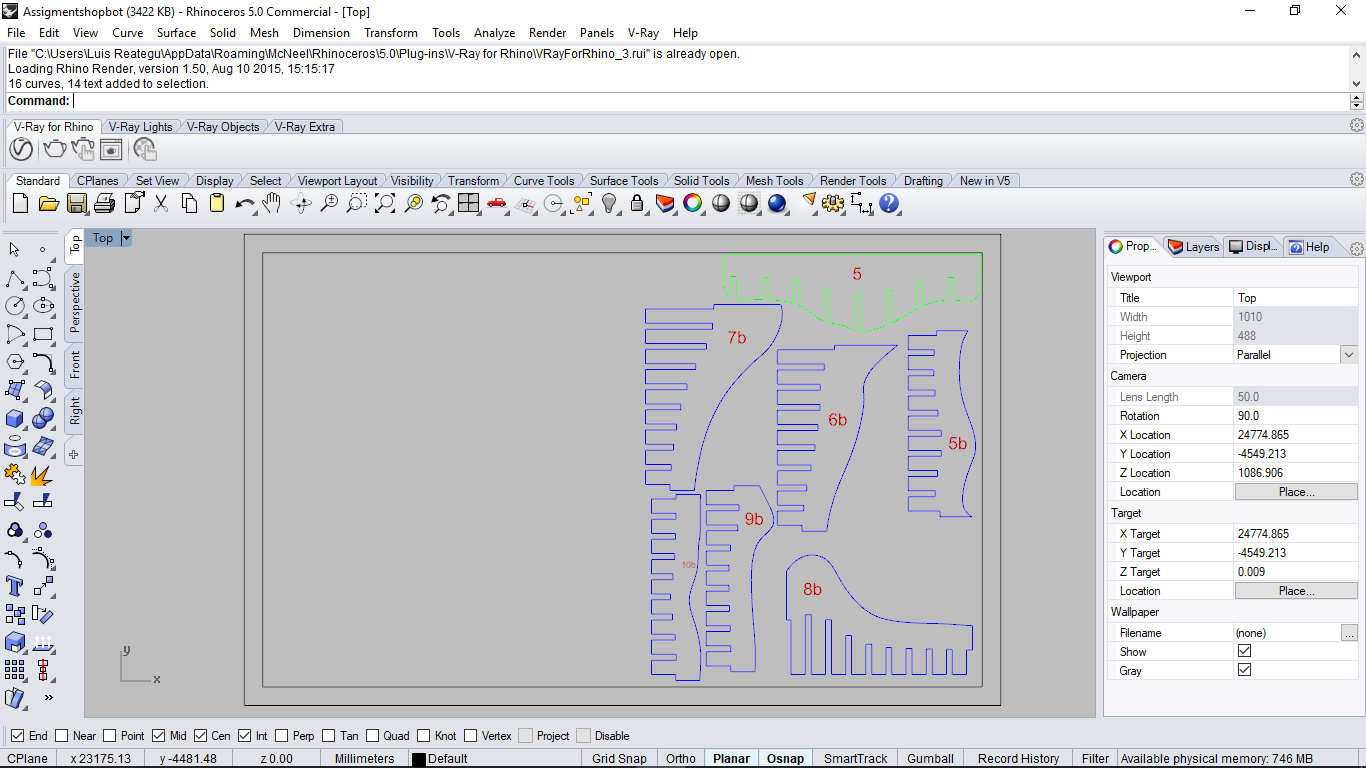
First I create a tolerance Test, designed in Rhinoceros3D and export in dxf format.
We create this rule of tolerances to find the most appropriate measures for joints between profiles. That is, the measurements on the computer have a different measurement when fabricate it, there is a range of measures that you can use, the choice depends on how much pressure you want to have in the system. Why does this happen? The answer is that the system have several surfaces in contact on both sides of the profile and on the lower faces. In my design there is a lot of surface in contact and therefore a lot pressure.
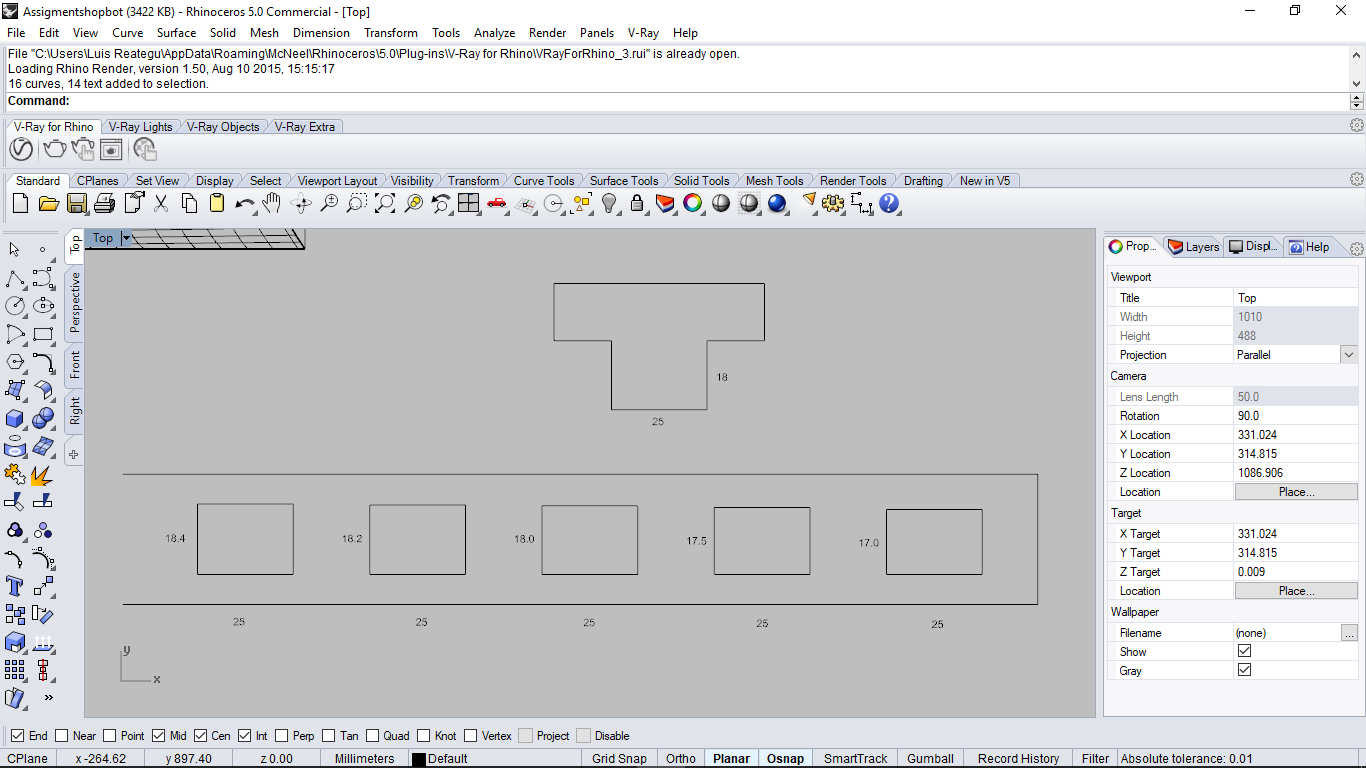
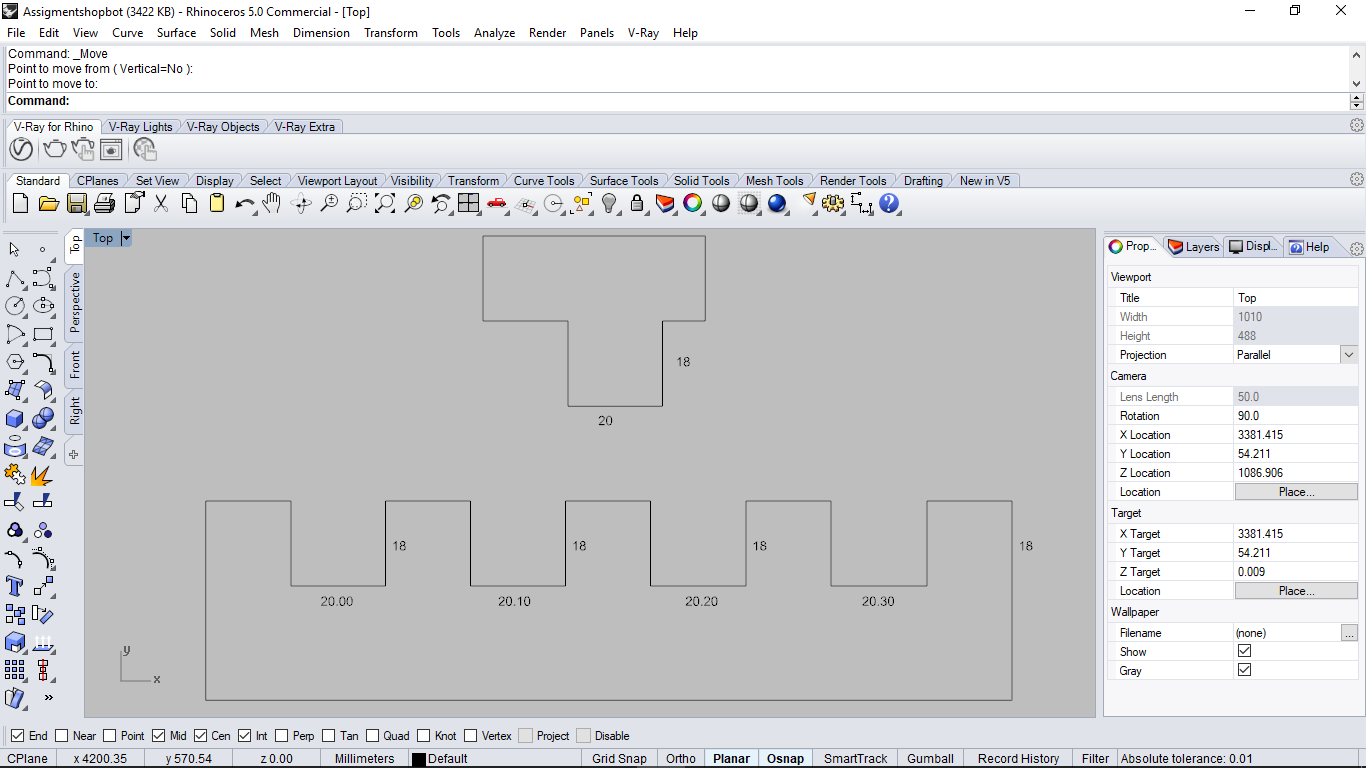
After that I used Vcarve to prepare the paths
Vcarve is a very useful program to define the "path" of the CNC milling machine, the first thing you have to do to use the program is the size of the plate to work, then import the file in .dxf format and place it on the virtual plate . After we have to define the tool to work the milling, this is 1/4" We generate the path" by the cutting line defining the number of repetitions on the same line "in our case it is 3 times", this repetition reduces the risk of breaking the milling tool. After this process it is necessary to place the tabs, which prevent the piece from leaving its site when it is active in the machining process. It is also important to consider whether the milling tool will have an internal or external path to the cutting polygon. For example, if there is an internal polygon that must be cut, you have to define the path of the tool milling inside the inner polygon and not outside.
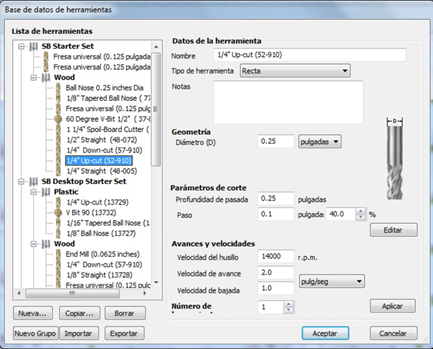
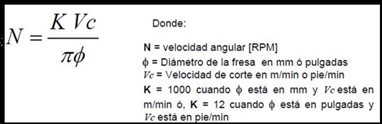
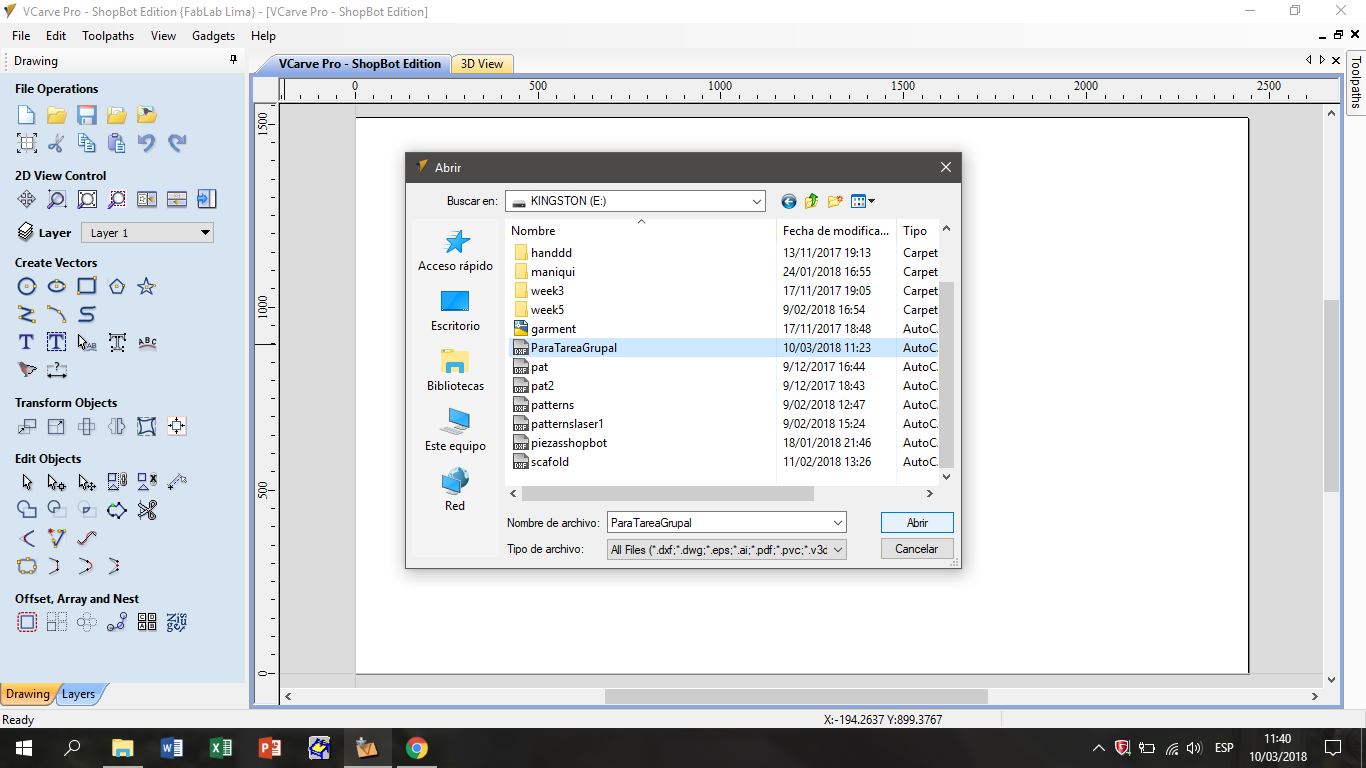
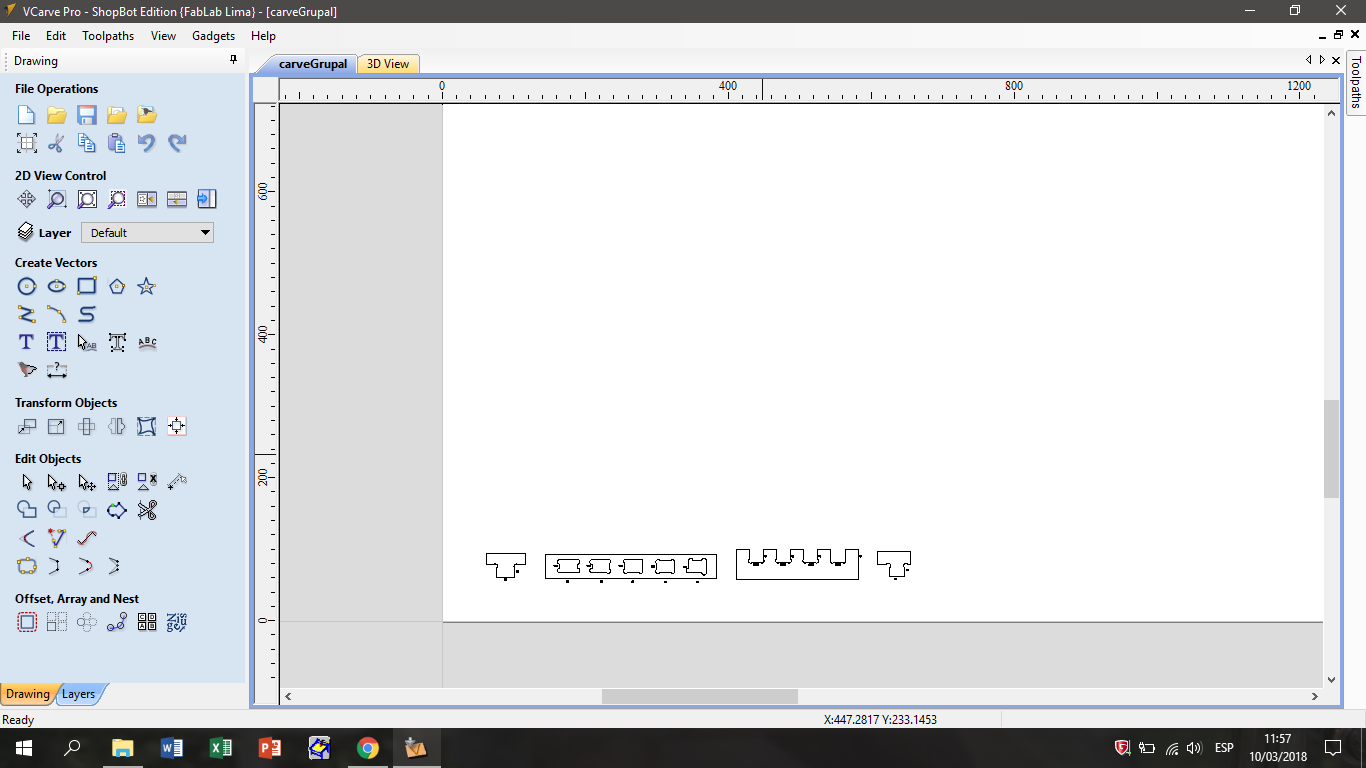
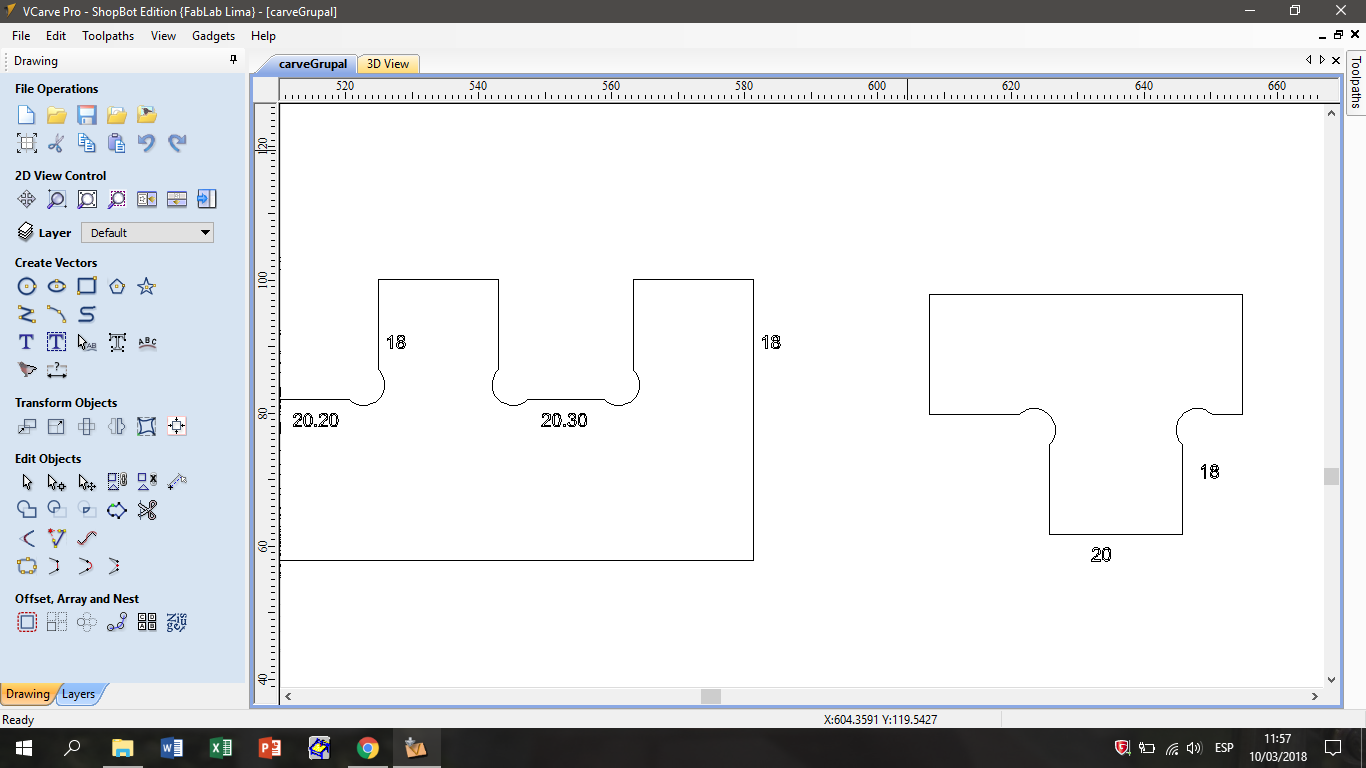
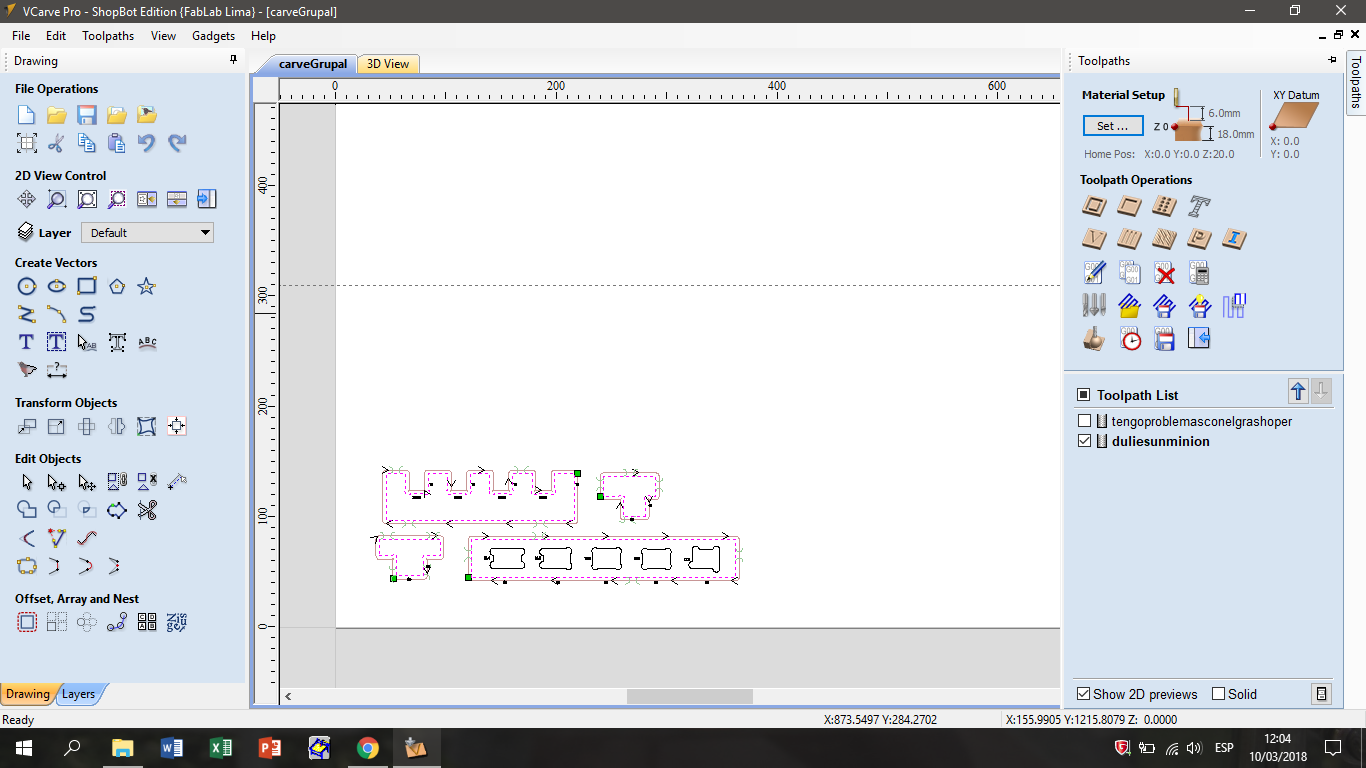

The paths are send to ShopBot CNC Machine
Prepare the ShopBot
To be able to use the CNC ShopBot it is necessary to calibrate the Z axis, this axis needs to be measured with a small metal plate that is on the side of the milling machine, also before this process we must place the coordinates of the Shopbot at 0,0,0 with the "Reset" button
Milling the Tolerance Test
Prepare the final design in Vcarve after create the tolerance test pieces
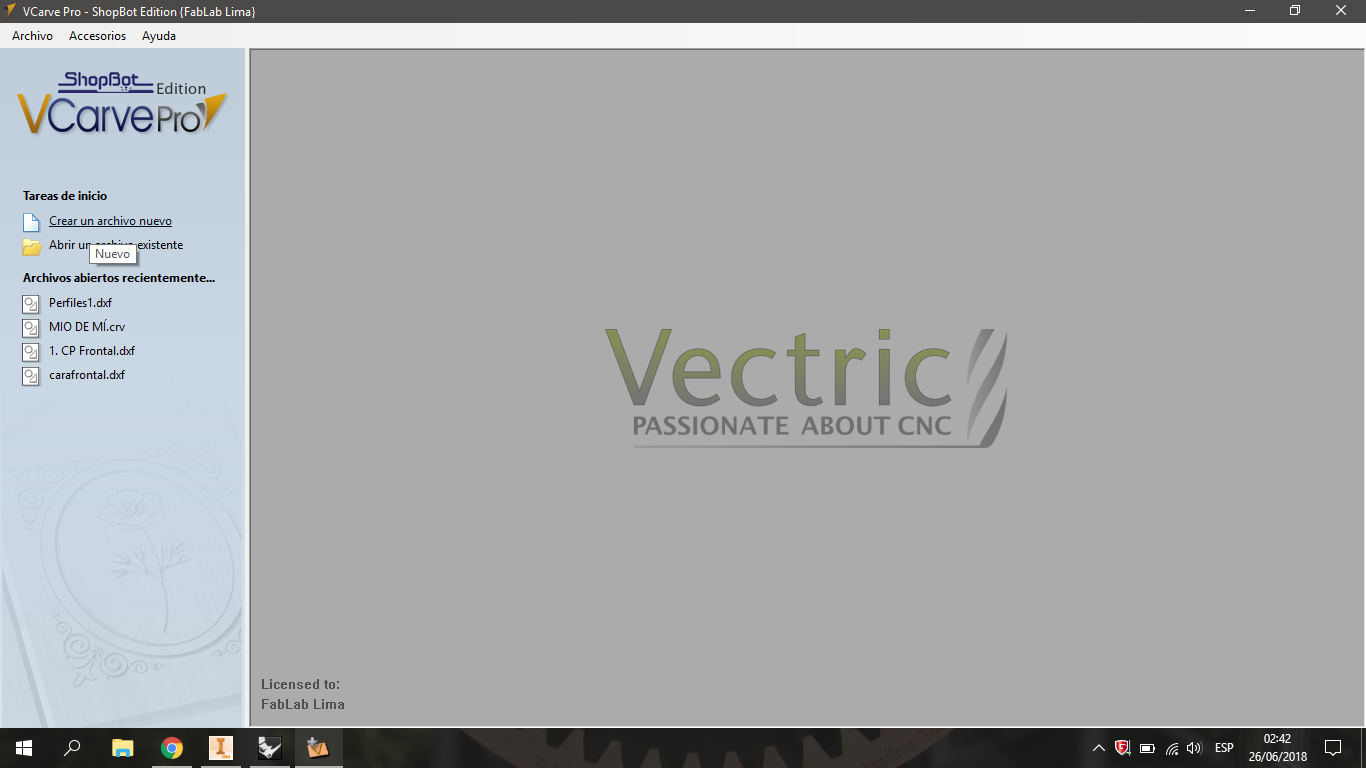
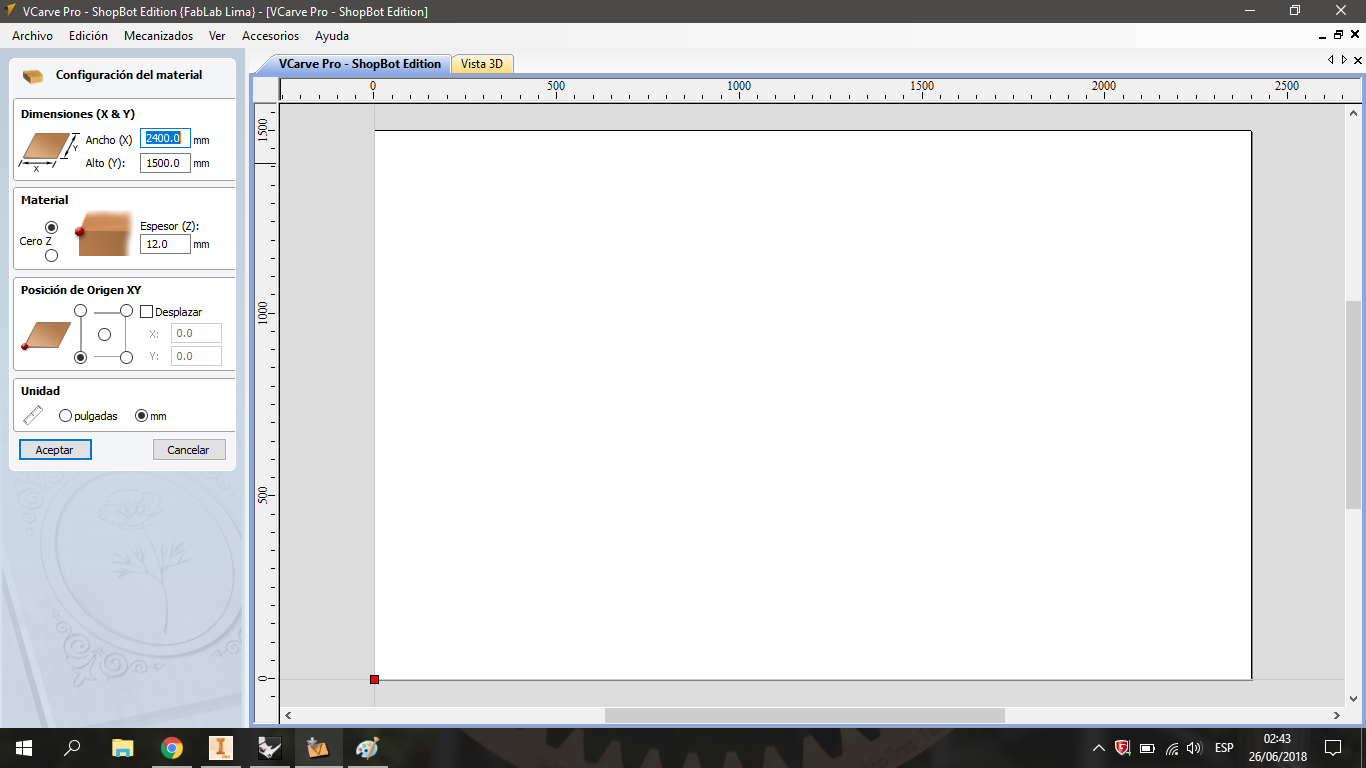
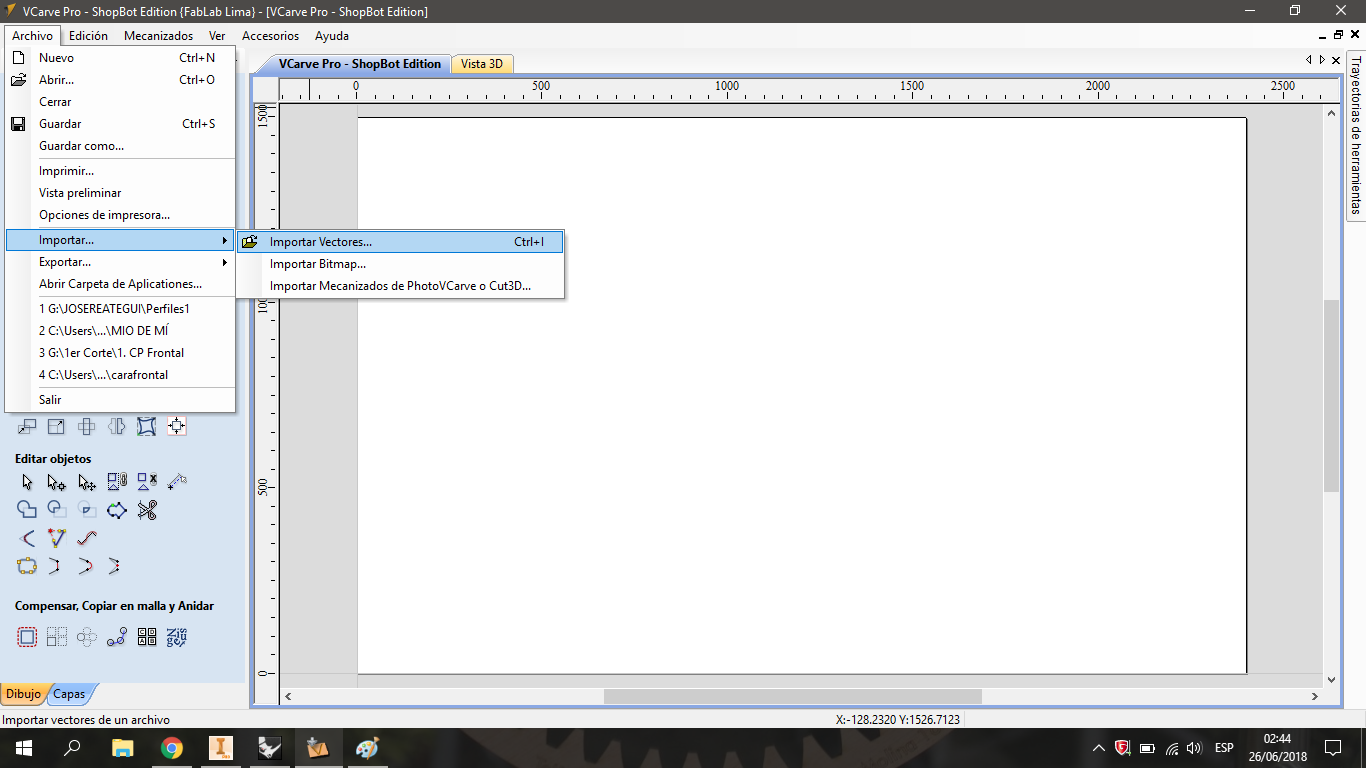
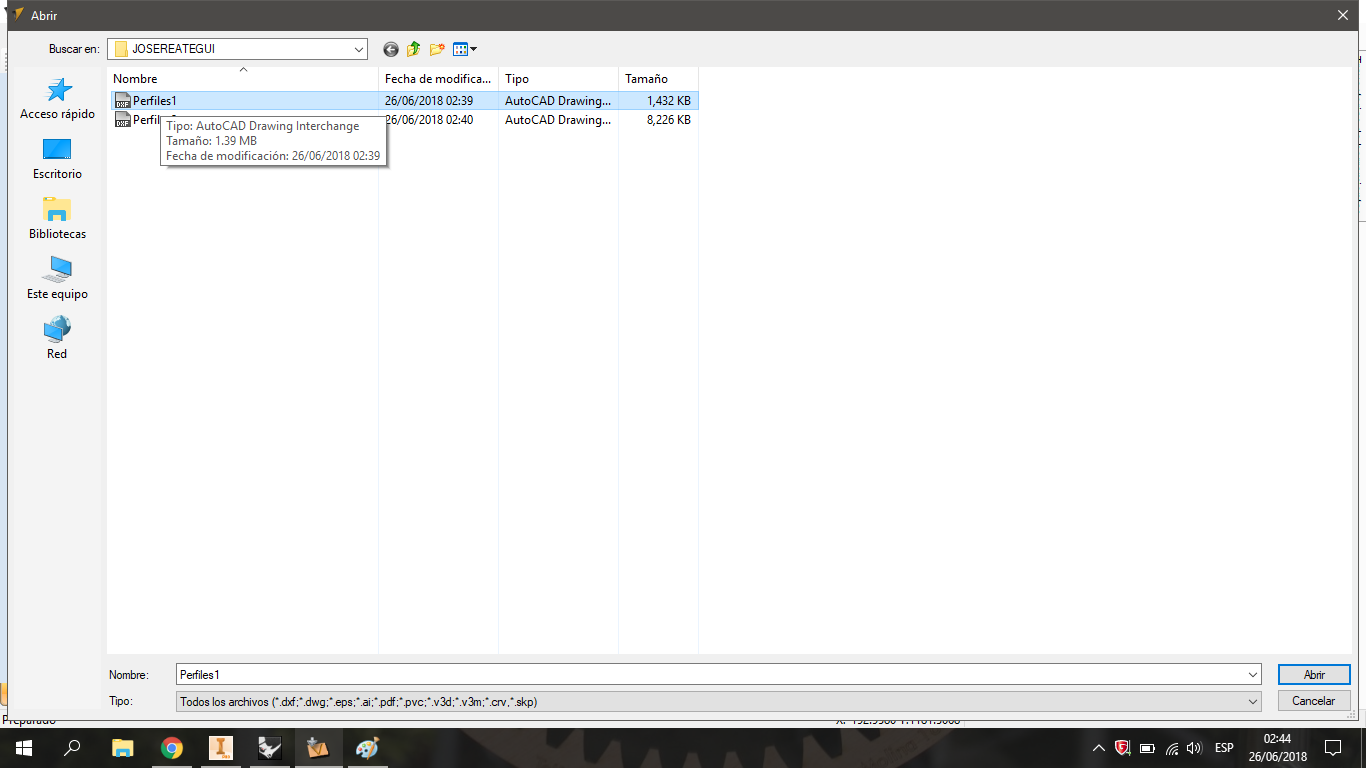
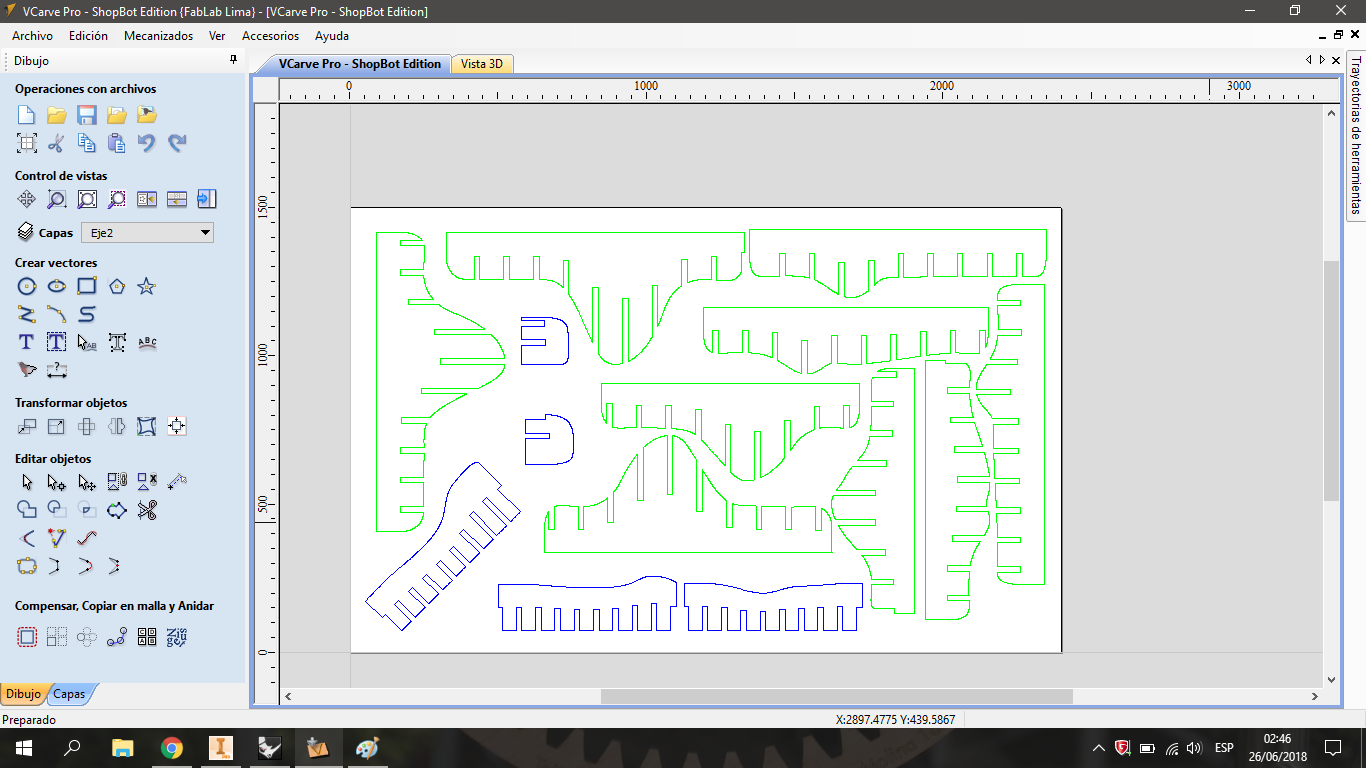
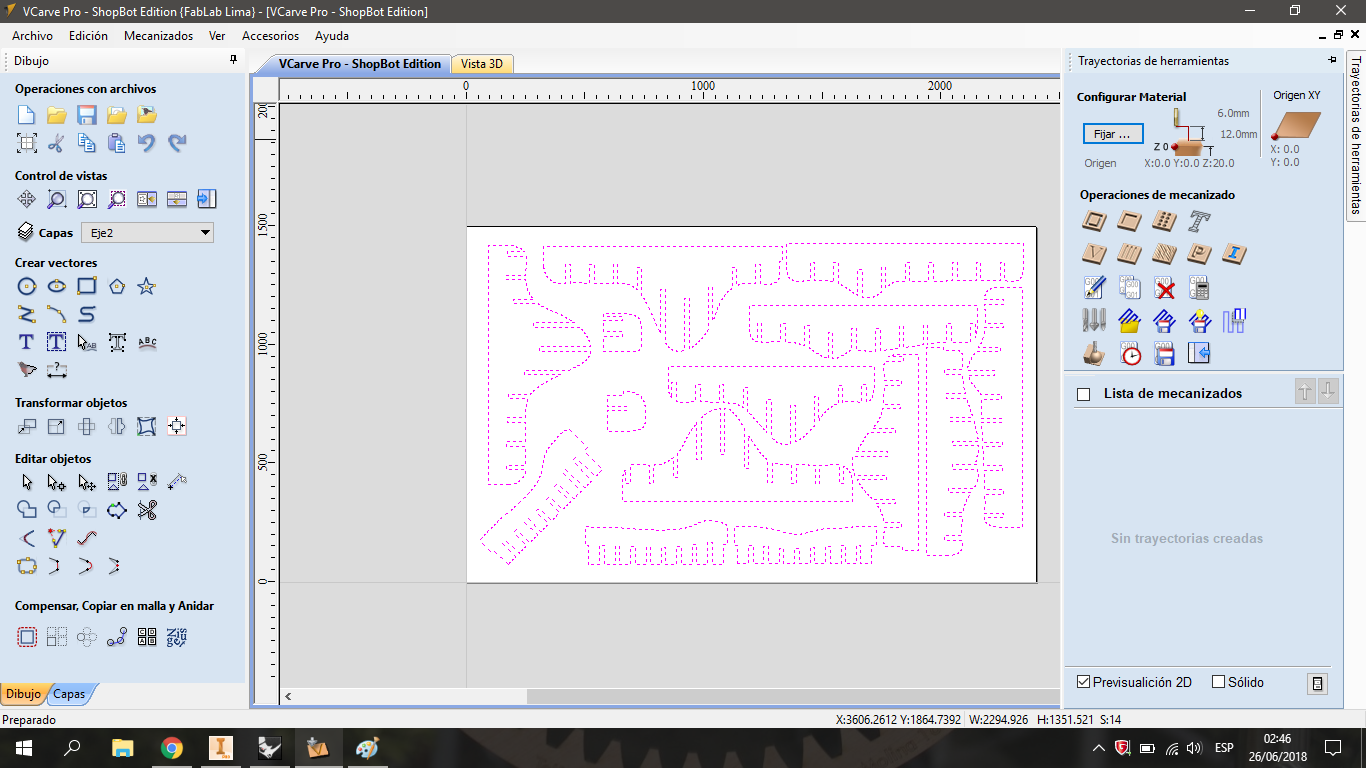
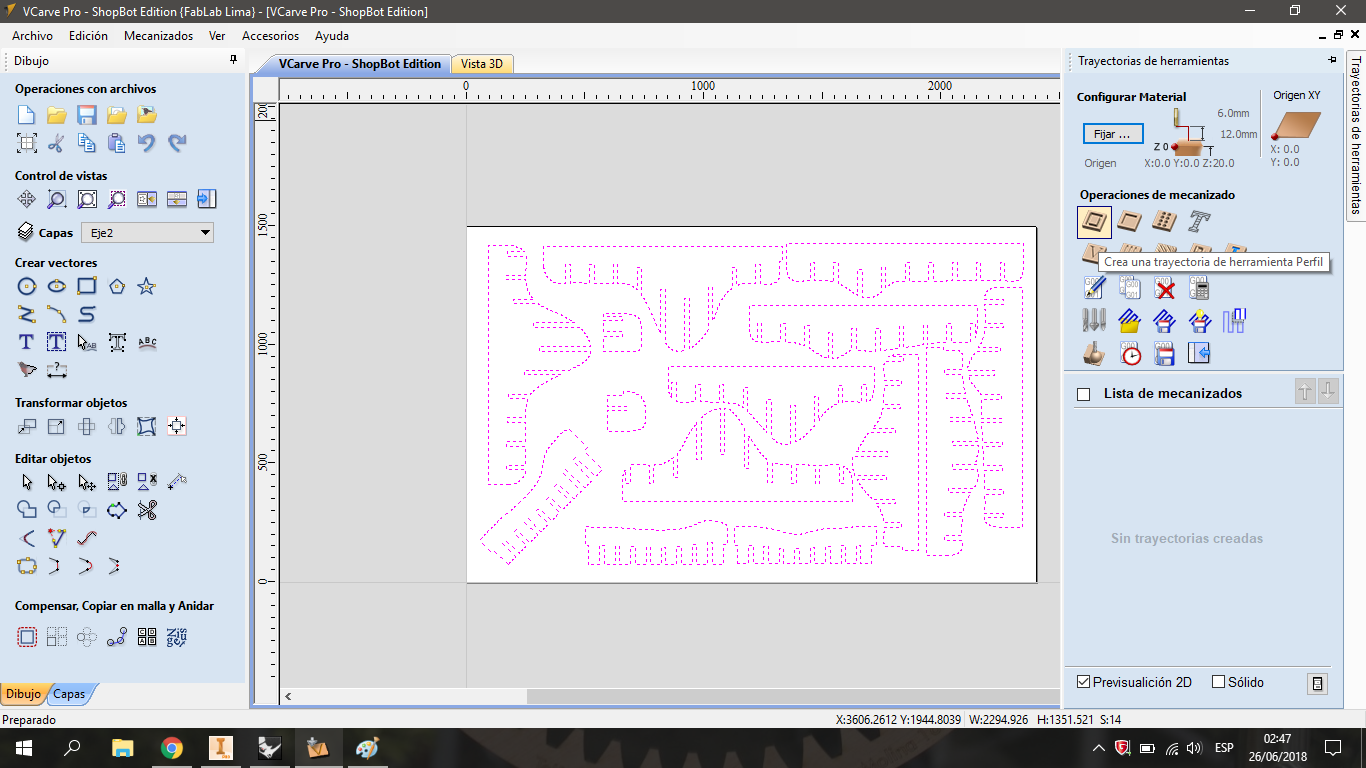
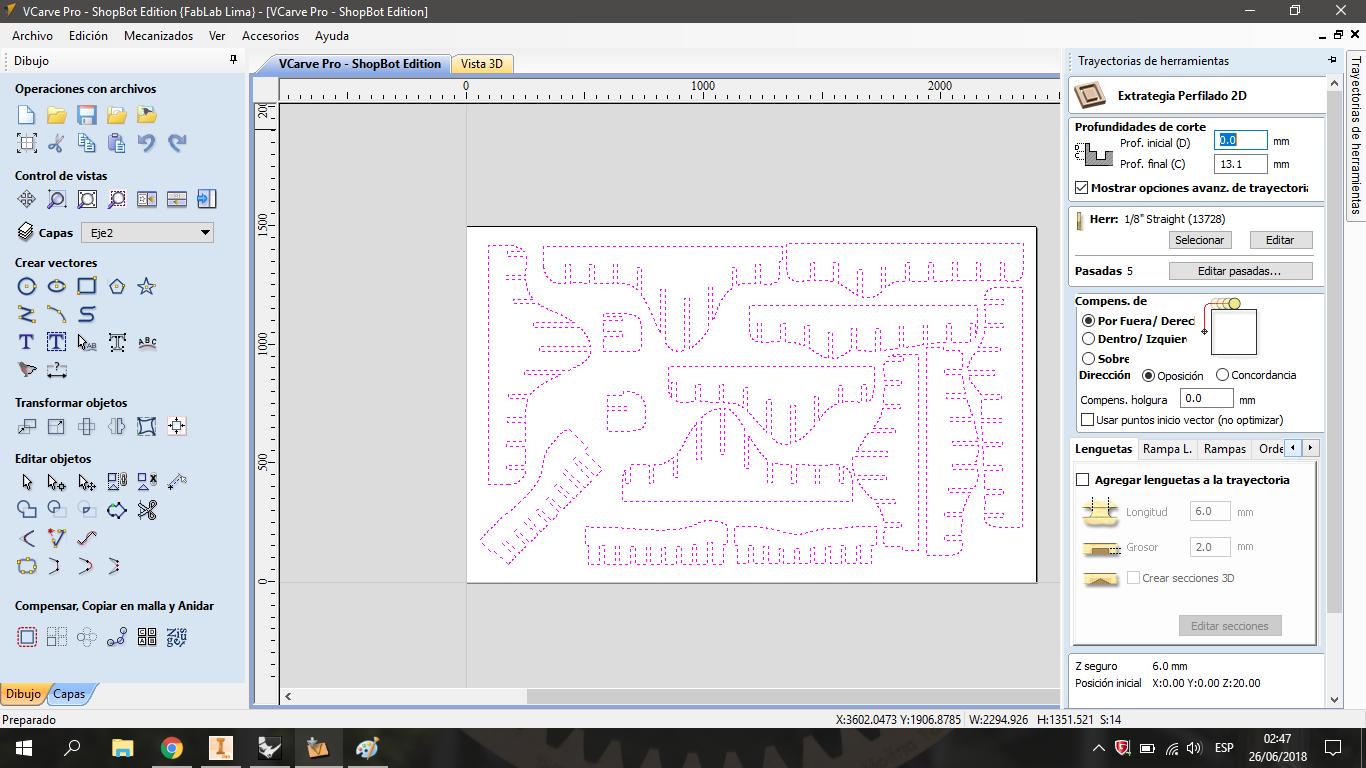
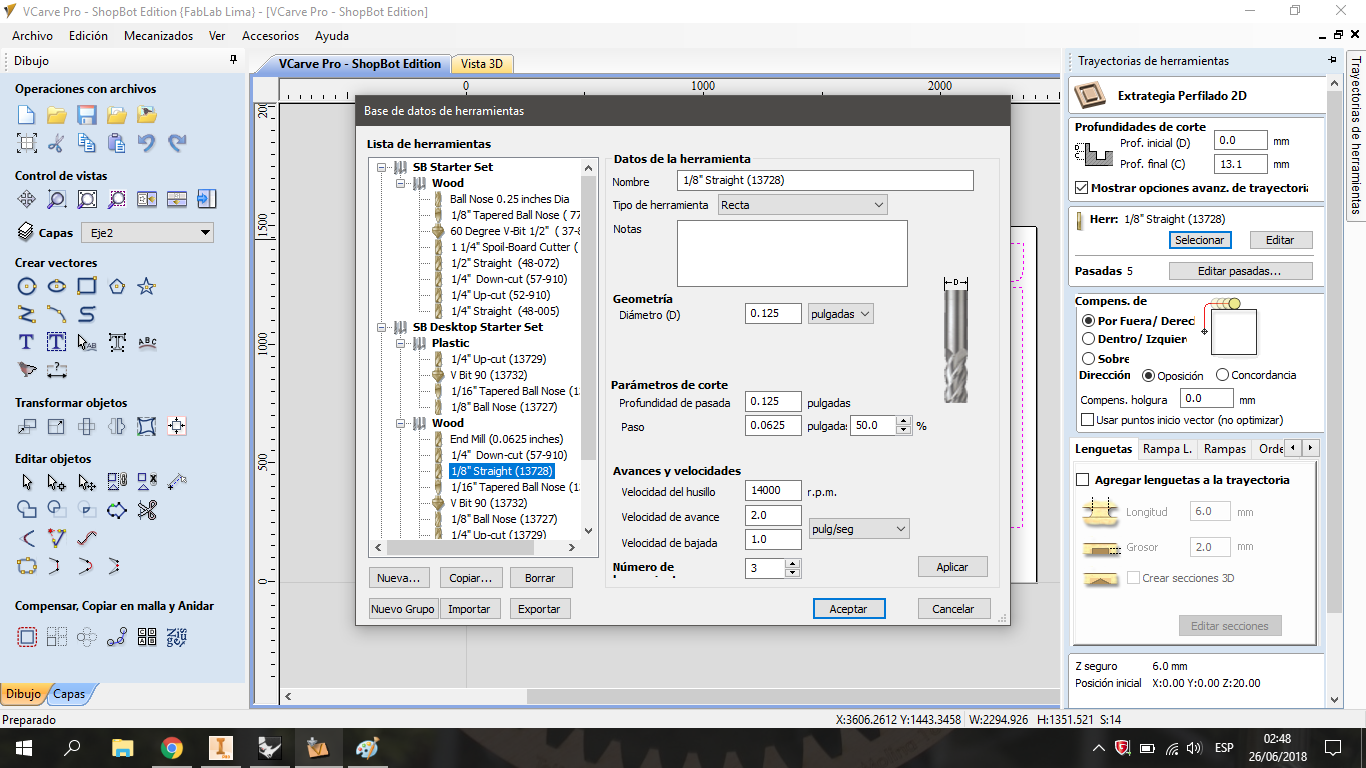
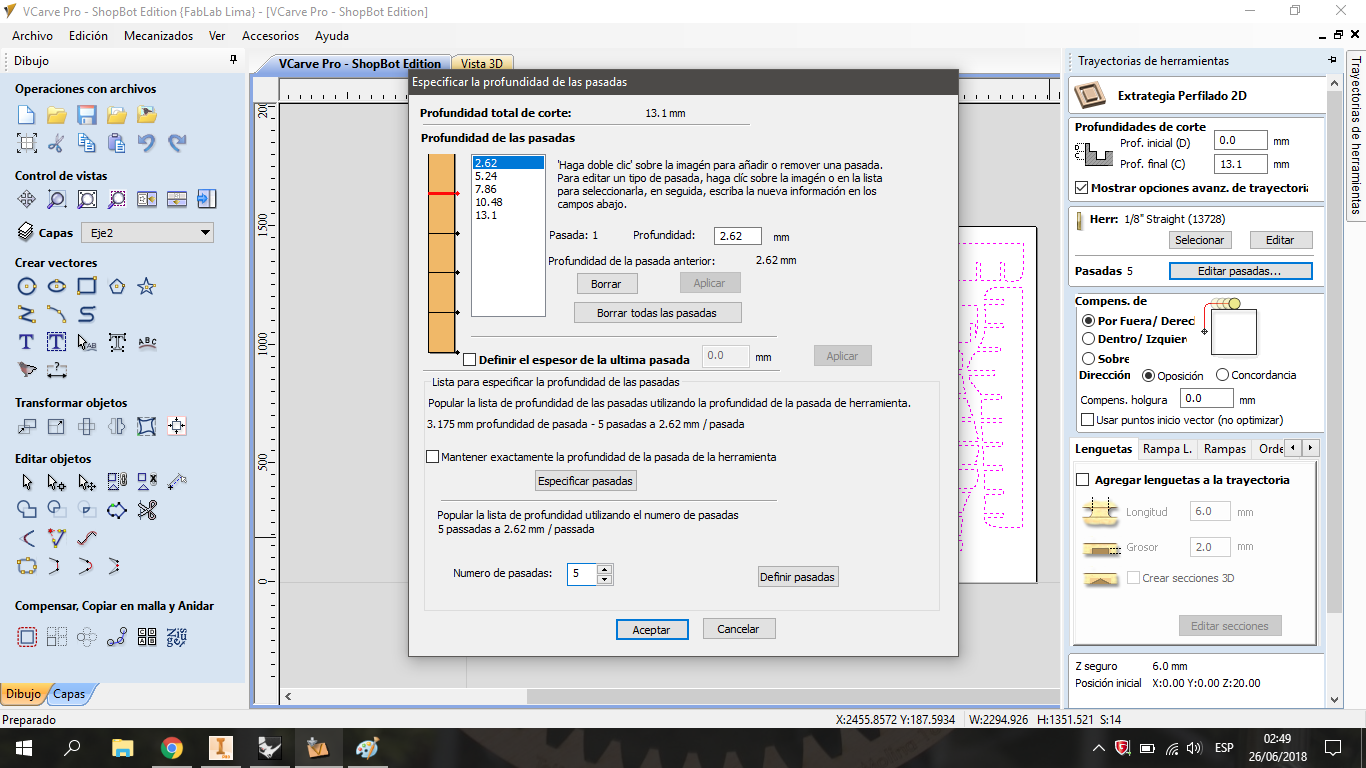
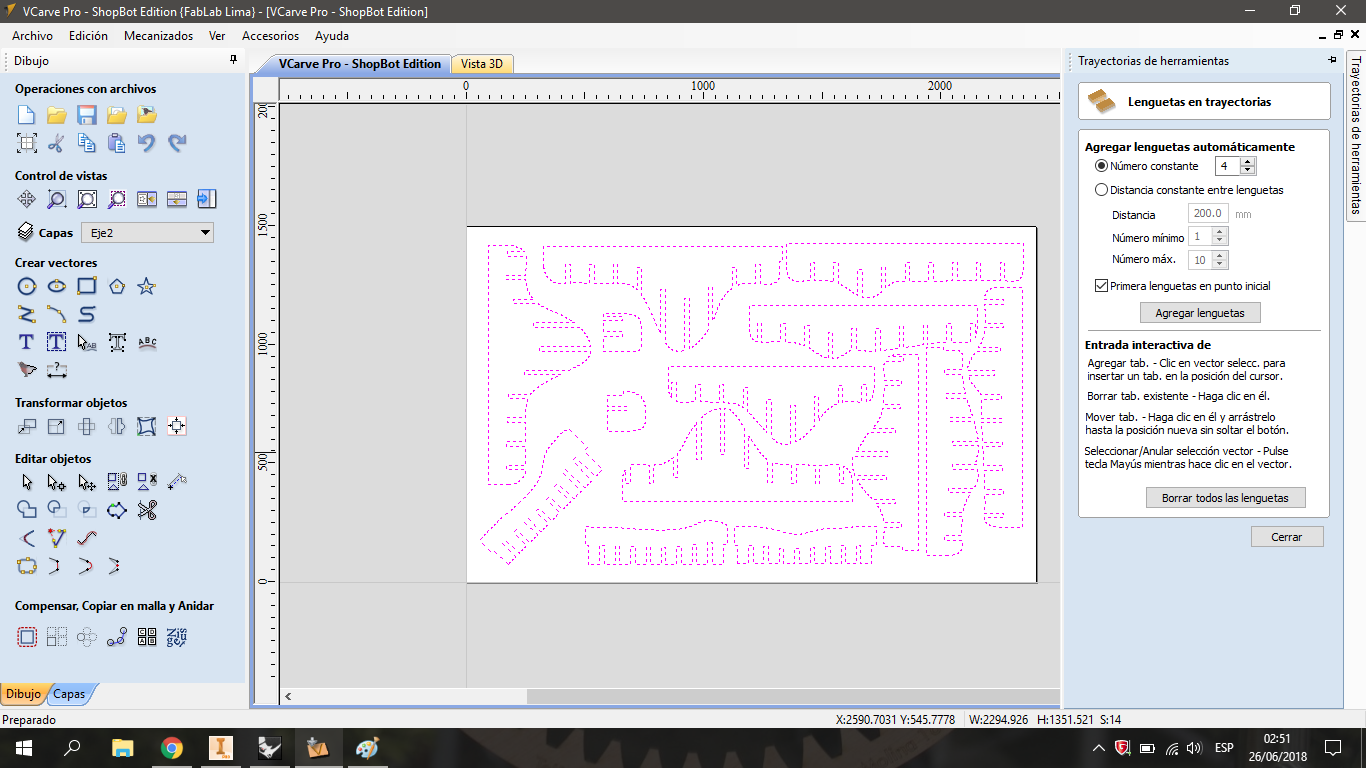
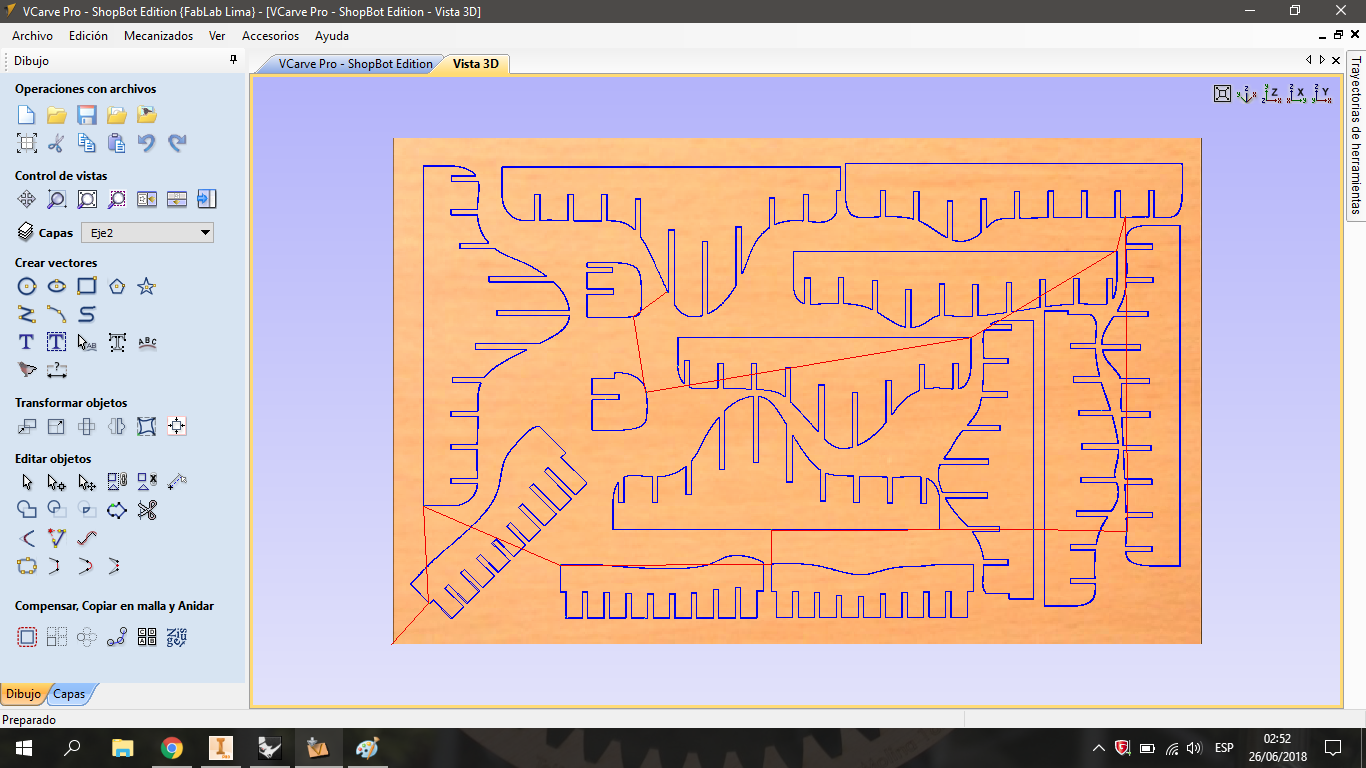
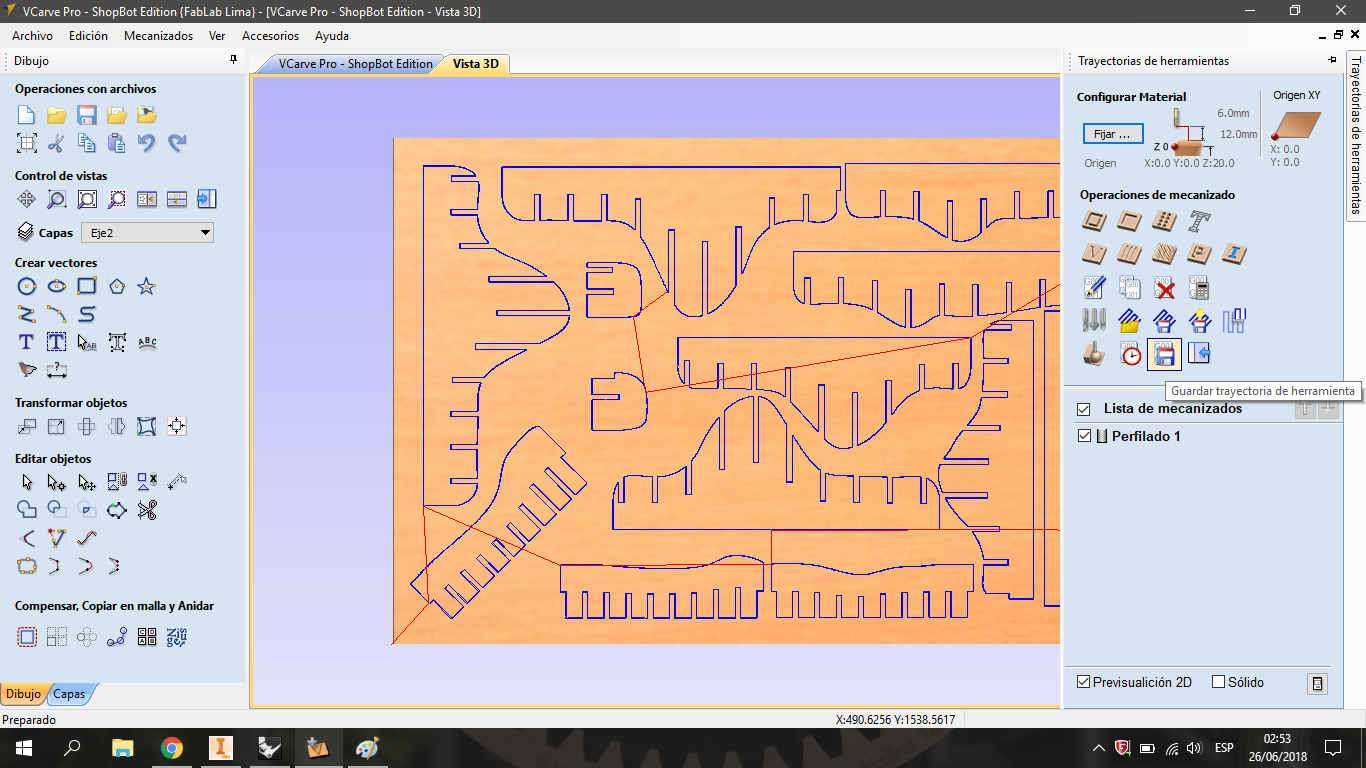
Prepare the pieces
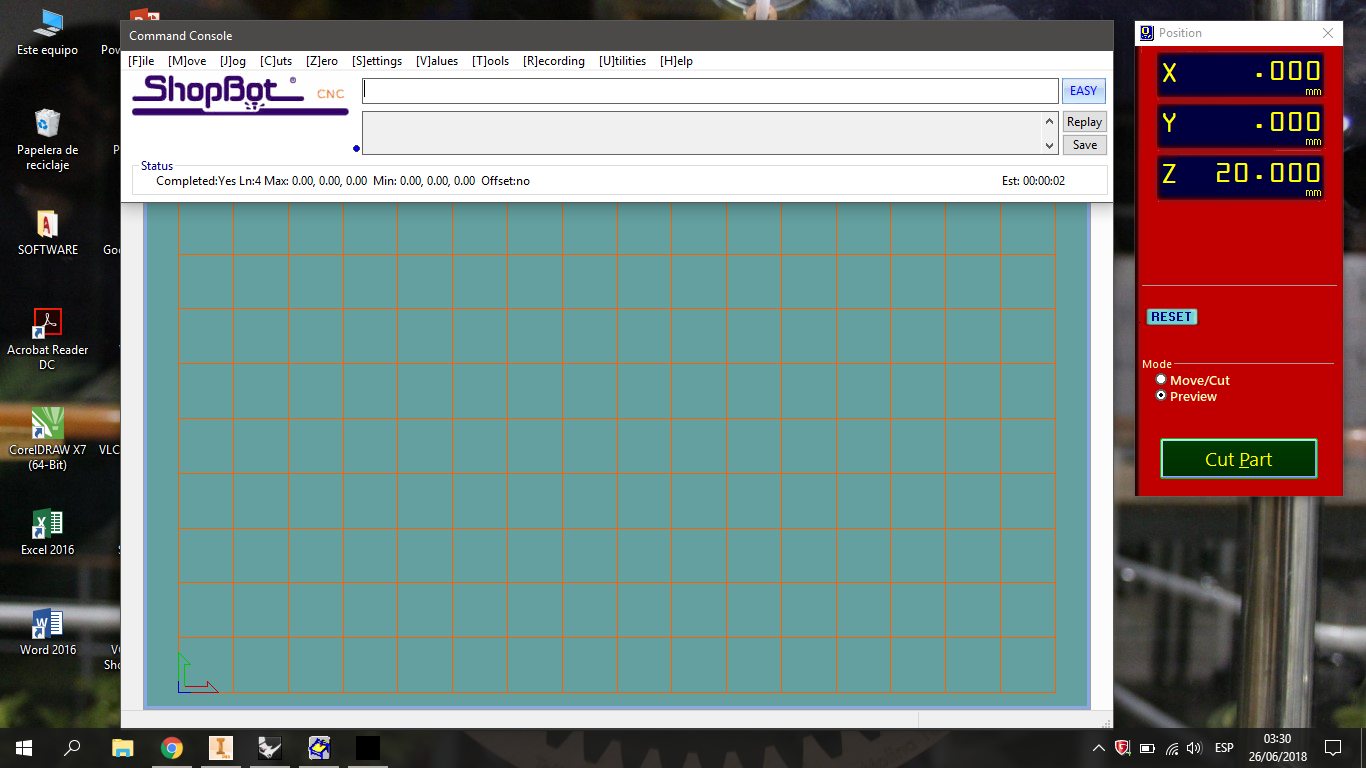
Test the furniture.
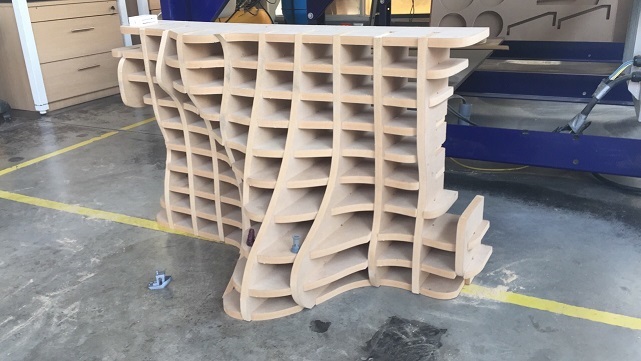