Group Assignment
- use the test equipment in your lab to observe the operation of a microcontroller circuit board
Individual Assignment
- redraw the echo hello-world board
- add (at least) a button and LED (with current-limiting resistor)
- check the design rules, make it and test it
- extra credit: simulate its operation
- extra credit: render it
Eagle, Art Cam, Grbl Controller, Adobe Illustrator, Google Chrome, Sublime Text, Photoshop, Git, Arduino

 

 

 

 

 

 

 

 
Fab Academy Week 6 - Electronics Design
Hello world eagle file .BRD              
Download
Hello world eagle file .SCH              
Download
Hello world image file .BRD              
Download
Hello world gcode .NC                     
Download
DESIGN ITThe first thing I had to do was create a board file using Eagle. I began by downloading and installing a library that includes the components I would be STUFFING the board with.
This is a great piece of software that allows you to create pcb layouts and connect them and test whether the circuits will work. You can do commands like:
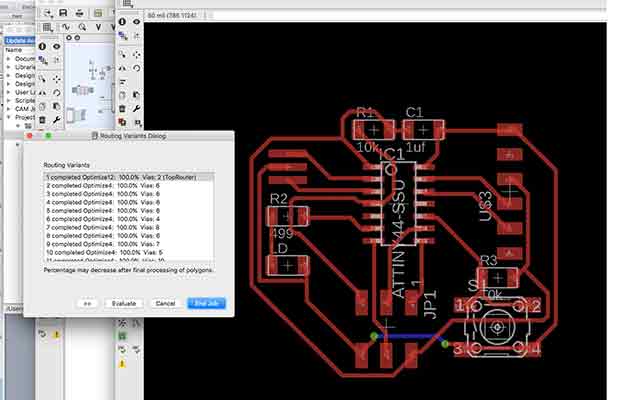
With a bit of patience I was able to recreate the board in the tutorial. I used auto-generate but it didn't resolve the paths so I had to manually position many routes.
Then I printied a .png (not export) and produced a .png that is to scale
MILL IT
I used our milling machine which doesn't have any sensors to cut out the paths. I made sure the bed was flat without any debris ontop. Next I manually positioned the head just above the copper board, loosened the bit and let it touch the surface of the board. Then I tightened the bit and set all the axis to zero. I clicked start and the mill cut out the paths into the copper board just as designed.
STUFF IT
Just like in Eagle, I went through the library of components and this time laid them out physically. It was a lot easier this time as I had done it before in Week 4.
In between components I would use a Voltmeter to test pathways and make sure there were only desired connections making contact.
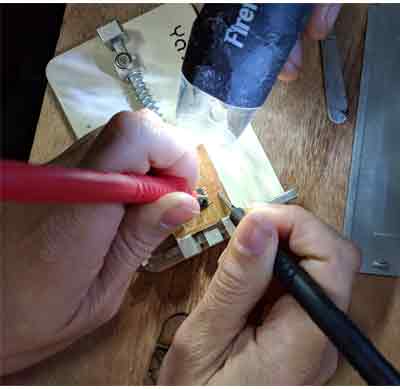
I decided to put the pins through the board and have the pins on the bottom because it would be easier for them to stay attached to the board.
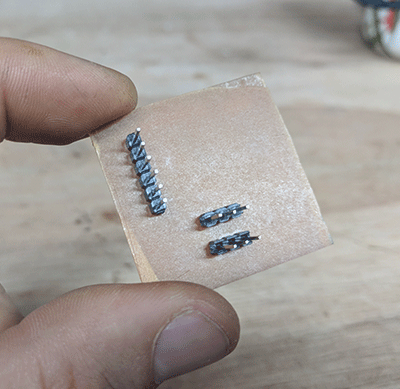
This time took me only a few hours of soldering to make the board.
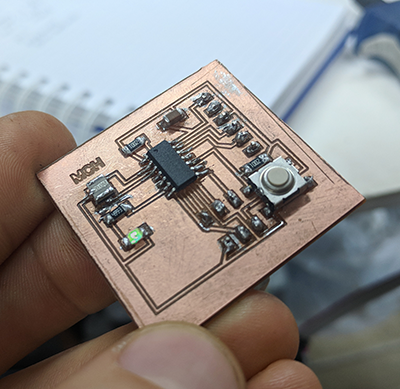
With my new board I plugged it in to our new AVRISP mkII (this tool is very useful for troubleshooting and identifying bad solders) and the light stayed red. I checked my connections and cleaned up any soldering that looked conspicuous. I tested paths with the voltmeter and after a few minutes of cleaning edges I had the light green.
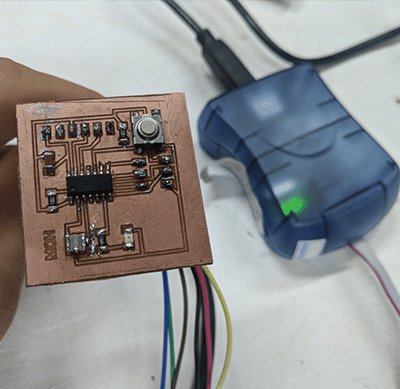
This week was well timed as I wanted to understand more about what components do on a PCB. When I started designing in Eagle, I was very impressed by the ability to troubleshoot electronic design. Eagle was fun to learn, I wanted the auto-generate to work but ended up having to draw the circuit paths myself (after some suggestions from the software). I had a little trouble soldering and will do research into advanced tips (both on the soldering gun and from professionals) on how to get better. I really enjoyed making the hello world and am looking forward to the bigger board designs.