Week 14Assignment: do the mechanical design for your final project
Programs/Machines: Rhino, Ultimaker, Cura
Lessons Learned: Be aware of uncontrollable variables when 3d printing, ie; humidity, temperature, direct-light, etc. Keeping in mind these things can help in the long run.
The main focus of my project was working the input of the environments interaction with an articulated inflatable to something more tangible.
The spring plays a big role in my work and as such I wanted to make sure it was as secure as possible. I started off by looking up precedents of how technical contraptions work regularly (pipe fittings) and adapted this existing object to hold the spring but even more importantly; be 3d printable.
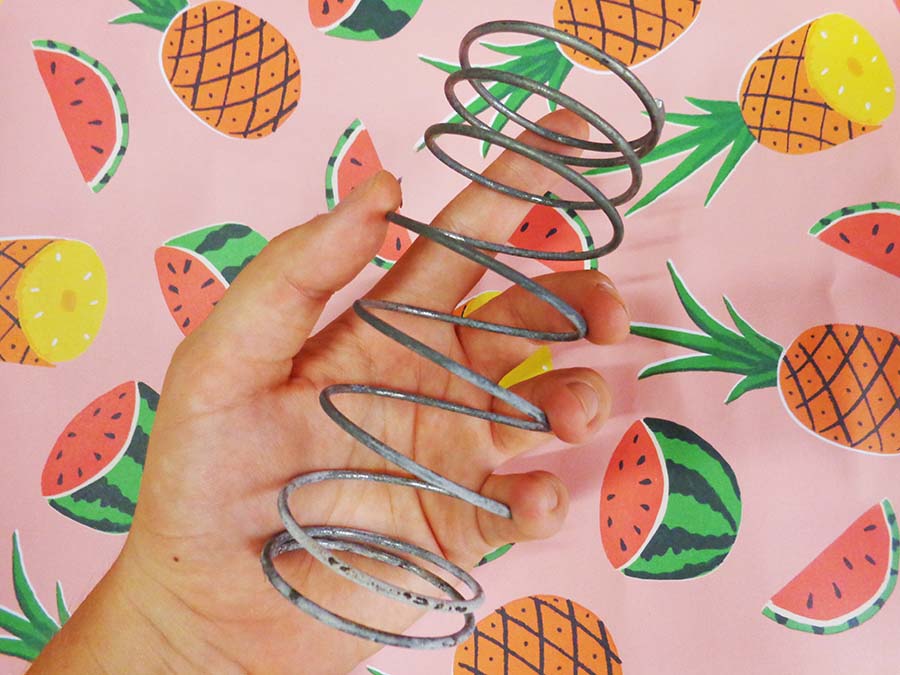

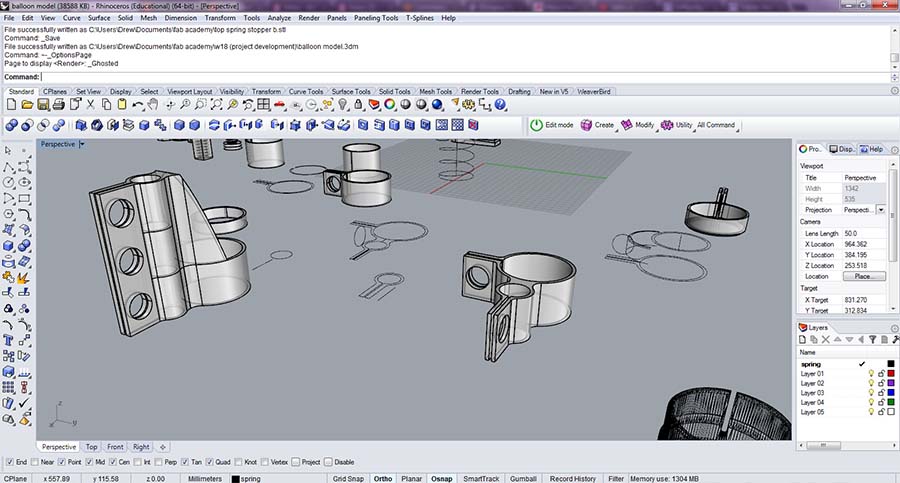
{1} Spring/Wooden stake coupler
{2} Filaflex cushion
{3} articulated spring
{4} Contraction joint
{5} Filaflex cushion
{6} Spring adapter
{7} ADXL335 Accelerometer
{8} translucent LED holder
{9} Case
{10} Balloon stopper
{11} Inflated balloon
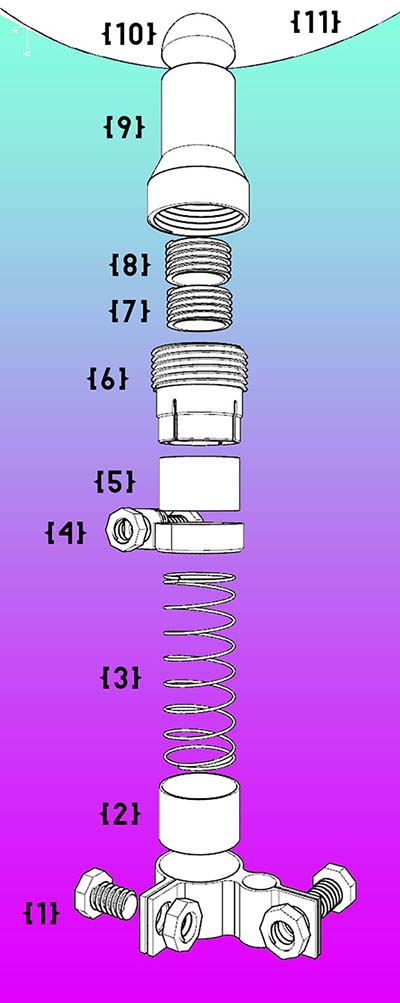
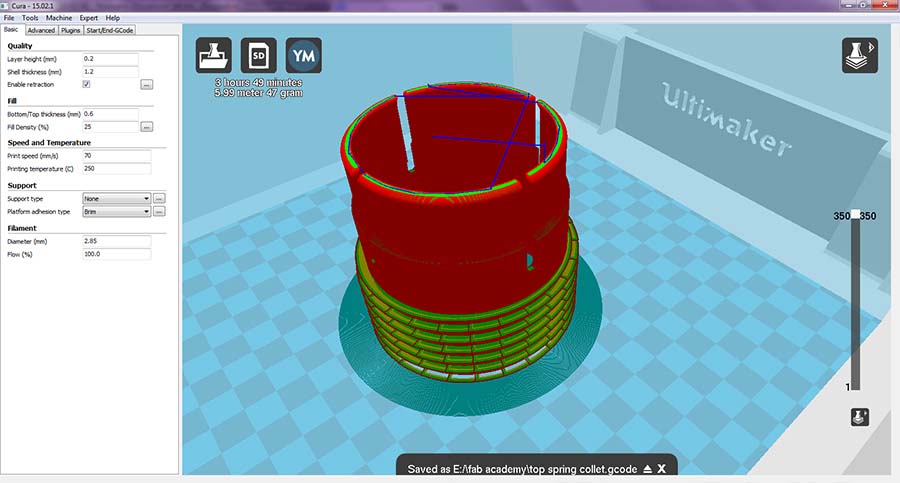
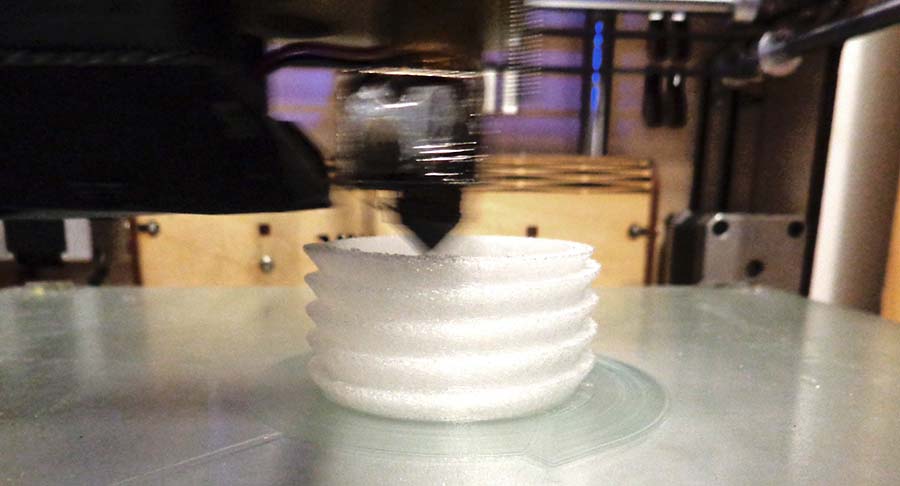
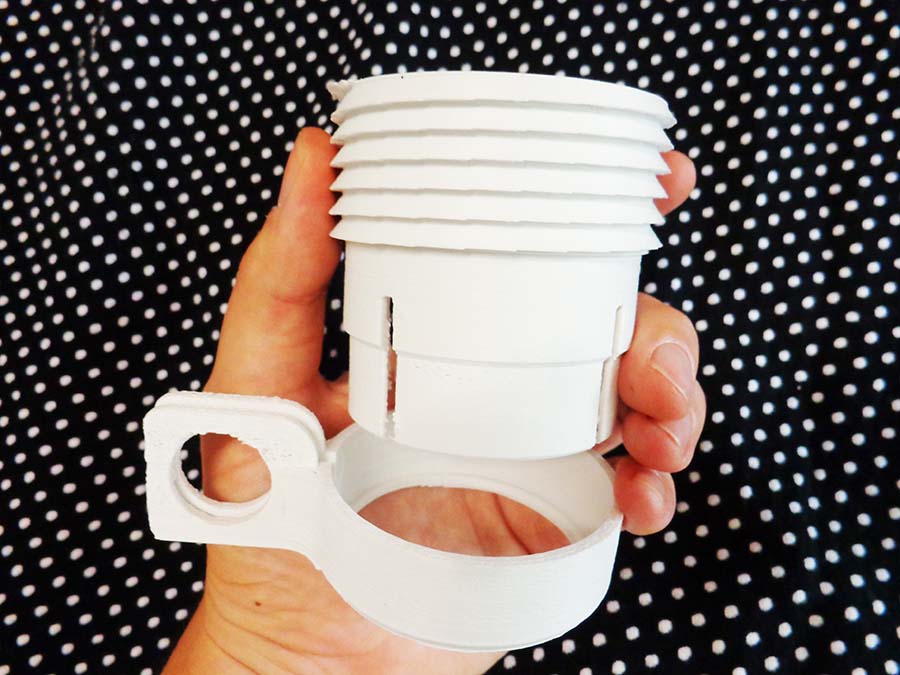
The spring plays rests easily withing the coupler. The 3d print came out exeptionally well. Each integrated leaf in the print is able to deform and grip the Filaflex isolator, thus forcing the spring into regidity while still letting the middle part of the spring move and bend. I used PLA with the bed @110' and the extruder @245' It was a pretty hot and humid day so I know when I print more I will need to play with the settings more. As it stands this exercise is successful in my mind. I had a lot of trouble looking up how springs are held, and many times they are not actually held but more put in a position to react to opposing forces in its own axis rather than face opposing forces perpendicular to its axis. Moving forward on design I could see a tri-formed fabrication with three different springs absorbing the forces that are perpendicular with greater success, as the spring always wants to warp and jump out of its housing currently.
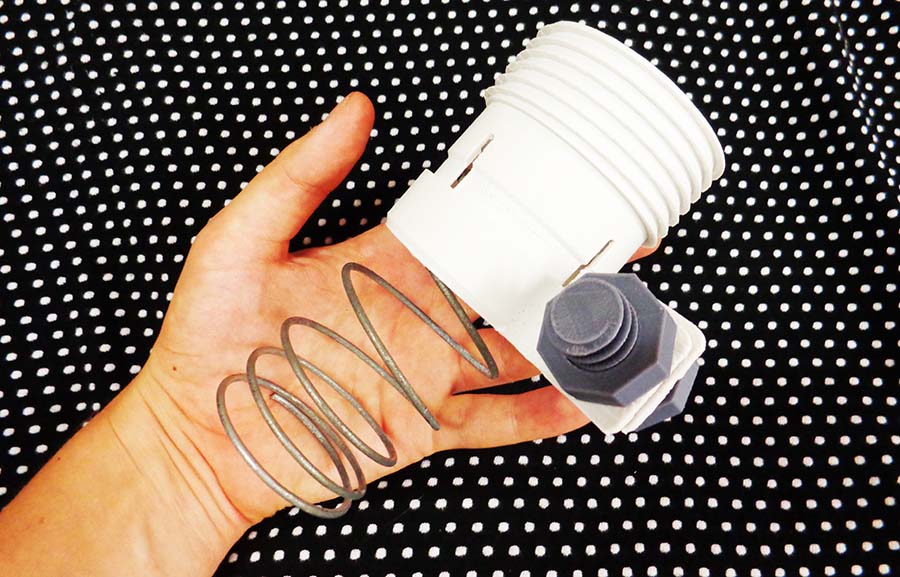
Downloads