7. I made a 45 degrees cellphone case for creating a more complex figure.
8. I exported the archives in .stl format and opened them in the Makerbot software
9. I moved the object using the 3 vertical buttons in the left.
10. Once opened in the Makerbot software, I exported the files to a SD card using this parameters:
Right: MakerBotPLA
Raft: Off
Supports. Right Extruder
Temperature:
Left Extruder: 210 °C
Right Extruder: 210 °C
Export!
11. Put the SD card in the Makerbot
12. Click the Centered Button
13. This will appear:
Replicator 2X
->Build from SD (Click here)
Preheat
Utilities
14. With the UP and DOWN arrows choose the archive you want
15. If you want to cancel the operation, clickeas in the left arrow
16. This will appear:
Pause
->Cancel build (Click here)
Waiting for Homing
Waiting for Homing
17. It didn't print well, because the
PLA tangled. I could not examine the printing carefully, because the
Fab Lab closed at 6:00 p.m. and the 3D Printer was going to finish
working by 8:00.
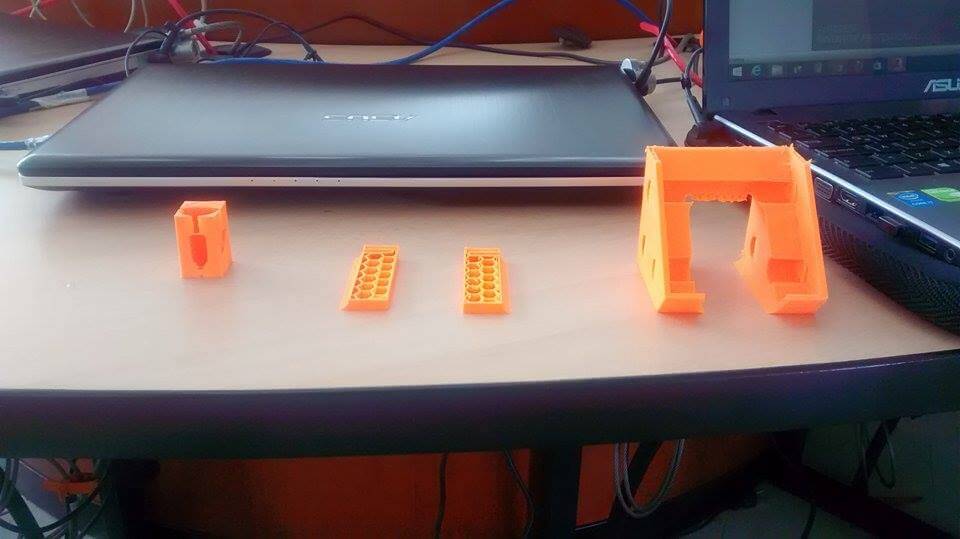
18.
Here is my idw. file that evidences my design in Inventor,
Here is my .stl file opened in MakerBot software and
Here is my .thing file.
CONCLUSIONS
1. Printing a safety or regular design instead of a reach design does not vary much on time investment.
2. You will feel much more satisfied if you attempt your reach design.
3. 3D Sense does not work as well as it is advertized.
4. Makerbot is really hard to calibrate and does not always paste the plastic efficiently.
5. It is not feasible to print a diagonal structure like my cellphone case.
6. You need to calibrate the machine everytime you use it.
7. You need to stay while the machine processes the PLA; otherwise it may be working in the air; thus, getting damaged.