Make Something Big
This weeks classof Fab Academy 2015 was about making something big. We learned about Milling for wood and foam for creating large scale objects.
To quote Prof Niel Gershenfeld:
When you mill you’ll cut out your part but often you’ll find you don’t want everything to come out right away because your nesting, so halving is where you leave a little bit of material so when your done cutting the part is still connected but can easily be snapped off.
My plan:
Day 1,2 - Design
Day 3 - Mill
Day 4 - Assembly
Design
I want to make my soon to be born son a bike so I am designing a childs tricycle/bike.
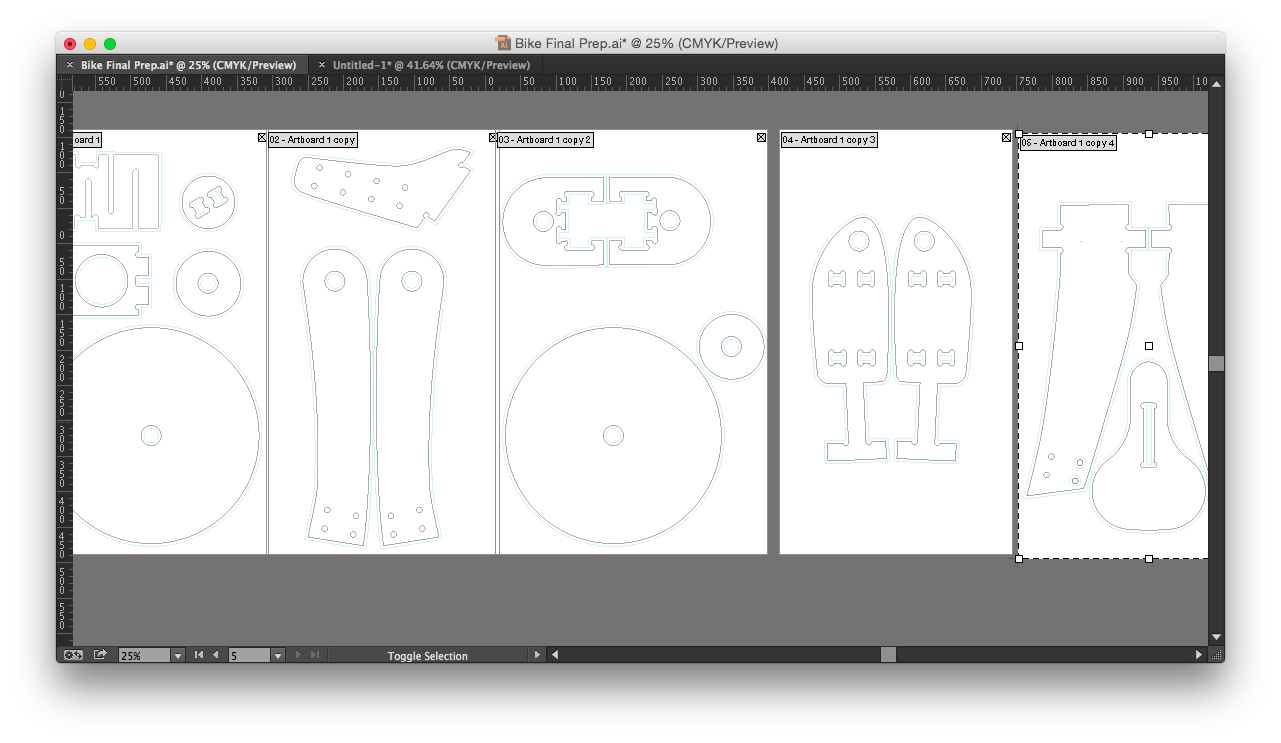
Production
The .dxf file was exported from Illustrator and imported into CamBam. Fiore walked me thru stock size, milling ends, post processors and depth settings. I was milling in half an hour on our mill that was originally a Shapeoko. I am running 800mmxMinute Horizontal Movement and 400 Vertical.
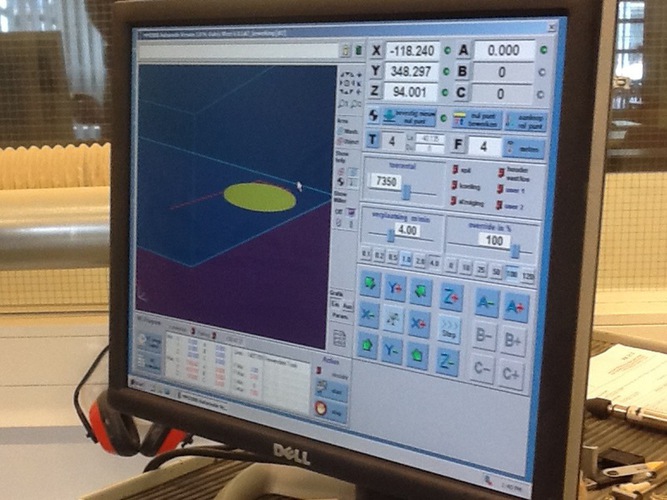
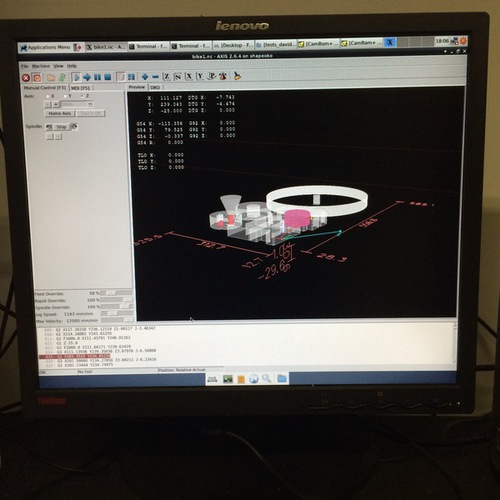
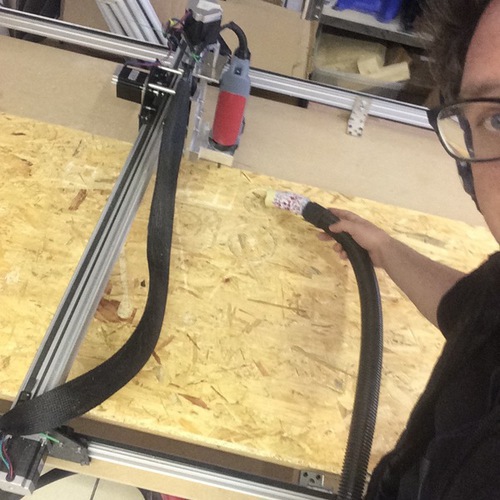
As I was the first person to use the mill their was a lot of Calibration. Fiore and I just spent 2 hours squaring the machine up. I ran the first plate only to discover that the Z needed calibrated as well. I messed up and didnt remember to save my origin so let's start again. This next ound we had problems with x slippage due to Servo motor amperage, It's 1amp even though the Servo says 2. (This is going to be a learning experience.
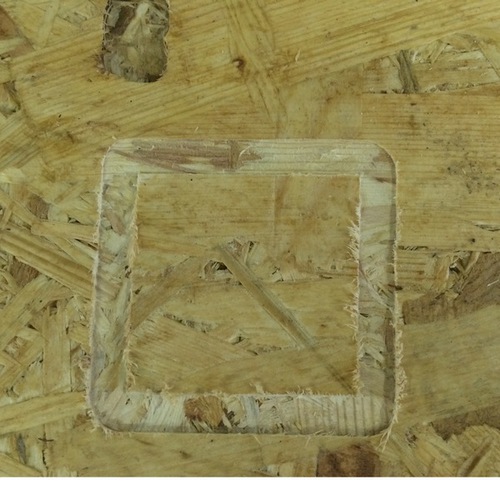
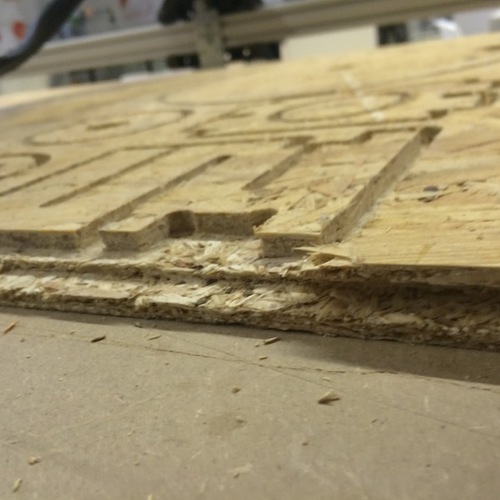
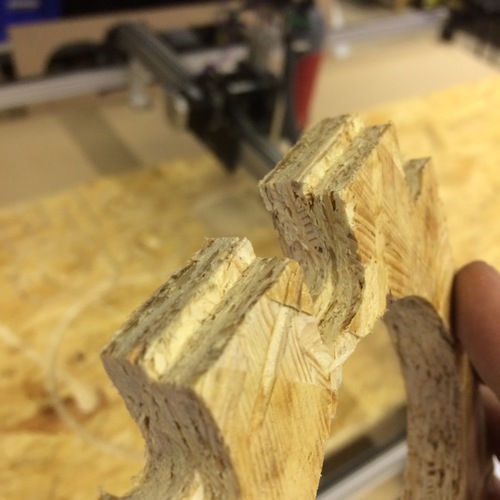
End of day one and I have successfully made only the small pieces.
Round 2
It's been three months. There was no time to finish up until now and finish I will. The Machine needed reworked as the Amperage on the X axis was being strange again. We've spent two hours tuning the machine so we are ready to roll. I double checked everything as this broken bit from my University CNC has me paranoid. It's going slow, but we are moving. We have to stand next to the machine with the vacuum so this is going to be a long day.
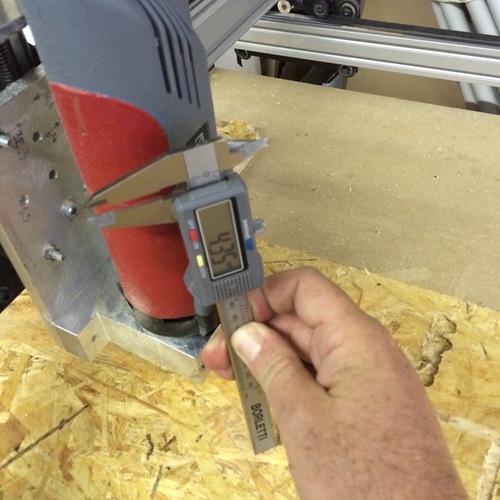
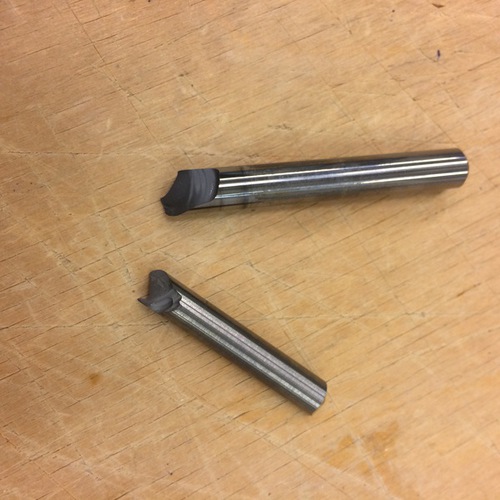
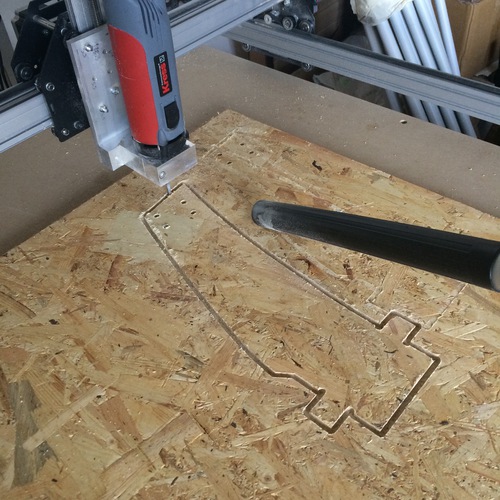
Things are going well, We've kicked up the speed to 220% and the X servo motor is happier (go fig). There are a few spaces where CamBam goes up and down to complete the outline and next time the design will go differently. (There is clearance, but CAMBAM doesn't recognize it. It's been eight strait hours of milling. My lab mates hate me for the noise but I'm going to finish FabAcademy on time.
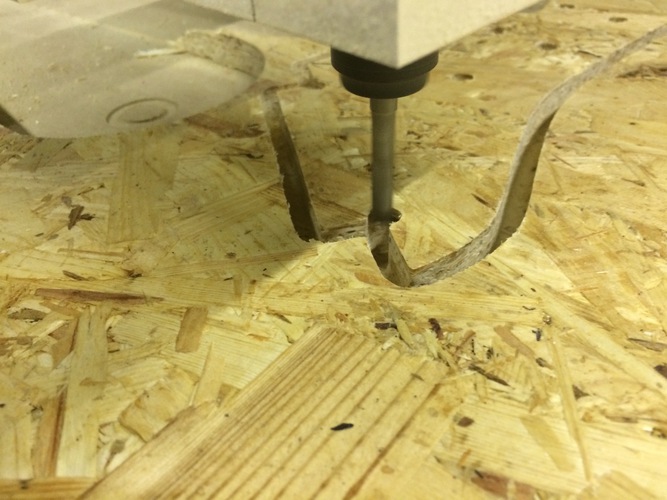
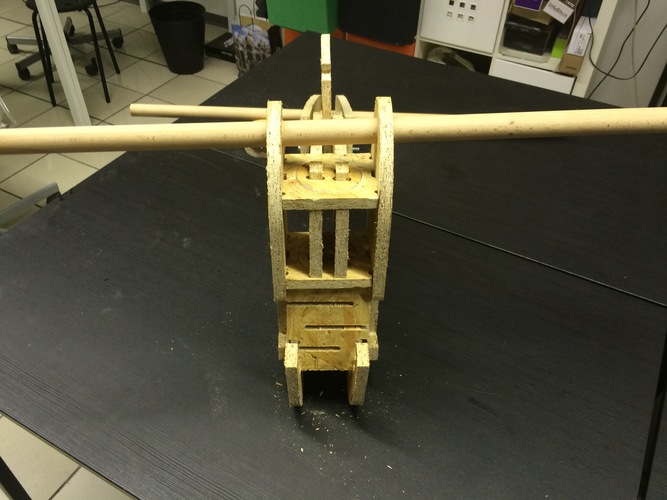
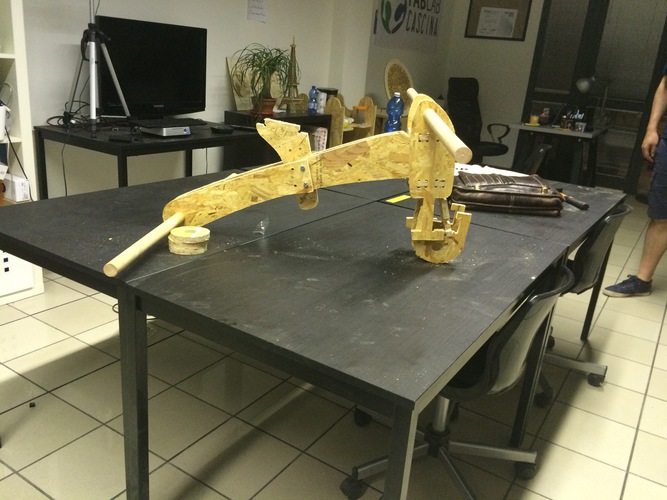
Conclusions
It took a lot more time than expected, The steering collumn works great, the susspension works but next time the flexure will be different. Milling is great when it works, I understand why the shopbot is so exspensive. I hope that someone makes a vacuum adaptor. It's been an intence and satisfying semester. Special thanks to Fiore for staying late to make this happen, not only this night, but all the nights before. (and weekends.)