INTRODUCING
DEVISED
AND BUILT AT
FAB LAB
MANCHESTER
2015
Phílip
Hemstead,
Dåvid Mason, Käsper
Andersan,
Sâlly WIlliams
Group Assignment:
•
Make a
machine,
including the
end effector
• build the
passive parts
and operate it
manually
• document the
group project
and your
individual
contribution
Brainstorming
Over
the course of
a few days, we
all brought
to the table
different
ideas that
might suit the
challenge of Mechanical
and Machine Design.
These included
a 3D
scanning
bed; golf
putting
exerciser;
robotic arm;
hot wire
cutter; roulette-style
random
page
selector (for
Neil).
The
one that had
the overall
approval
by the group,
was an idea by
Philip Hemstead
- a digitally
controlled ball-tilting
maze game.
This would
usefully
utilise the
the capability
of the stepper
motors to
provide
control over
the level of
the game-bed
plane to move
the ball
through an
obstacle
course.
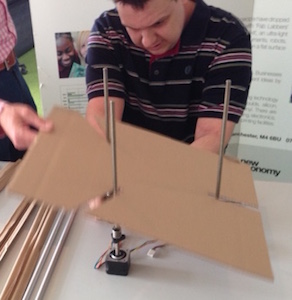
FABNET :
The
'Fabnet'
network would
provide the
communications
system for
the
machine using
muliple
nodes whilst
sharing a
single set of
communication
wires -
described
below:
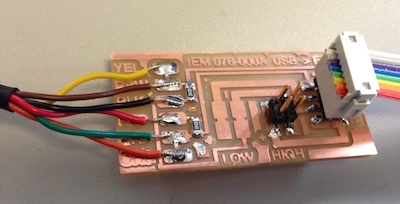
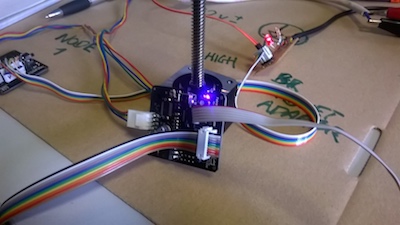
Connecting the
Fabnet Adaptor
to a
single node:
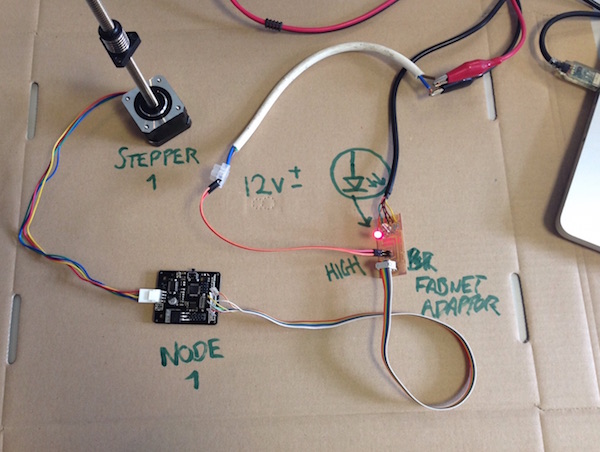
Assembling
cardboard
stages
We made two
linear stages.
The cardboard
cut files were
downloaded and
Pacon 80%
recycled
spotlight
single-walled
tri-fold
presentation
board cut on
the Epilog
laser cutter.
The Epilog
2'x1' bed
meant the
frame parts
were cut in 3
parts with box
joints and
glued together
using Gorilla
glue, this did
not work as
there was no
cardboard in
the box cut to
glue, so the
joints were
gaffer taped
together.
In Nadya's
<a
href=“http://monograph.io/james/m-mtm”
target="_blank">
instructions
</a> she
recommends
gluing all
cardboard
laminate parts
to achieve
maximum
stiffness. In
haste we
omitted this
step causing
issues with
robustness of
the
stages.</p>
There was a
problem
assembling the
frame, stage,
shafts and
stepper
motor/leadscrew
parts together
- they did not
fit! As a work
around we
removed the
inner
lengthways
flaps from the
frame to get
the stage to
fit with the
aluminium
shafts. Also
the stage
internal
dividers
interfered
with the
exterior
cardboard so
were trimmed
to get the
stage to fit
together.


The second
stage was
assembled
ready for the
the maze
assembly and
fixing.
Building
the housing
for
the stepper
motor:
Cardboard
was cut on the
lasercutter
using the
templates
provided:
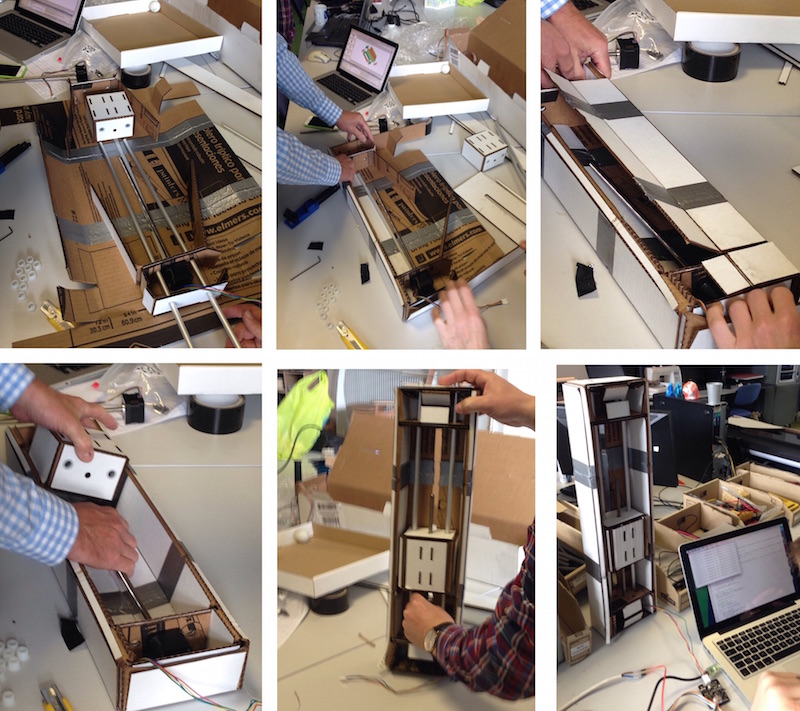
Calibration
The
python
code defined
that 1 x
revolution of
the leadscrew
would travel 6.096mm.
This did not
reflect
the distance
for the
leadscrew
supplied in
the kit.
This was
estimated to
be 8.0mm, and
this was
changed in the
code. With
this calibration,
a
request to
move 10mm
would deliver
10mm.
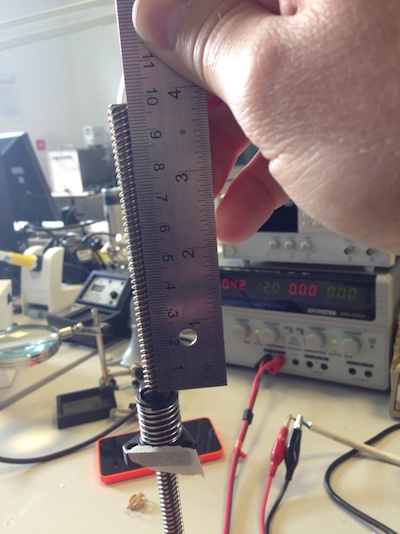
(David
Mason)
Creating the
control
console with
wx python:
wxPython
is a visual
front for
Python
script (which
Gestalt
runs in),
therefore we
aimed to
create a
visual control
for the
stepper motors.
We began by
looking what
was required
for a button
to be pressed
on the
interface.
Once we had a
button
interface, we
then made it
adjust a value
+-10mm.
This was
achieved with
the assistance
of James
Fletcher
(alumna of Fab
Academy) who
helped to take
snippets of wx
code that
would help to
build up our
code. Below is
snippets of
the code and
how they
operate;operateopsnippets
uilhelp
thelped to ;
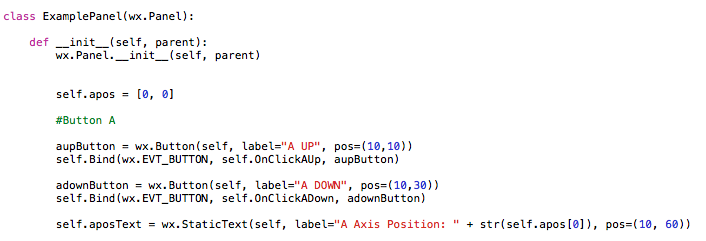
In
the
example above,
we declare an
object which
will be the
location and
identification
of the button.
The
button has a
label and a
position plus
the position.
This
is a relative
position and
will be
updated when
the stepper
motor moves.
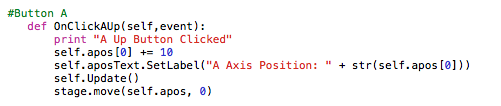
In
this example,
the button (AUp)
is linked with
the axis
position and
the stepper
motor (in this
instance, this
is the X axis
as the
self.apos is
0).
stage.move
self.Update()
then update
the axis.e
t()te selfpos

In this
snippet, the y
and x axis
stepper
movements
are defined as
well as the
direction.
This is
important
because the
final section
determines the
direction, I
ended up
having to
change the
direction in
self.apos[0]
instead
of choosing
TRUE
or FALSE.ded

Finally
we add the
section which
produces the
frame on the
screen
'frame.Show(True)'
which allows
the user
to control the
stepper motors
with the
visual
display. The
supercoords
were used in
the previous
application of
this Python
code, this is
now not
called.
Issues
with wxPython
It
is a great skill
to have a
visual way
of
controllingthe
stepper
motors, but it
soon became
clear that the
application is
not very
responsive to
quick
movements, and
pressing too
many times
could crash
the
application
due to too
much
information.
At this
present time,
we have not
found a clear
way of
alleviating
this situation
therefore the
experimental
code will not
be published.

Creating
the game maze
bed on the
lasercutter:
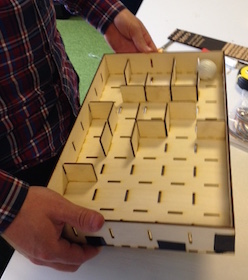
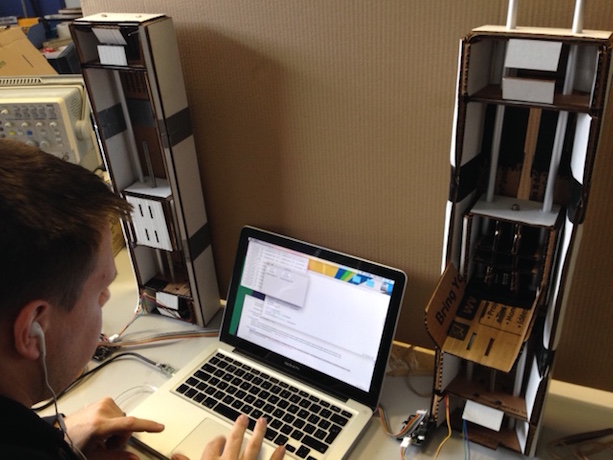
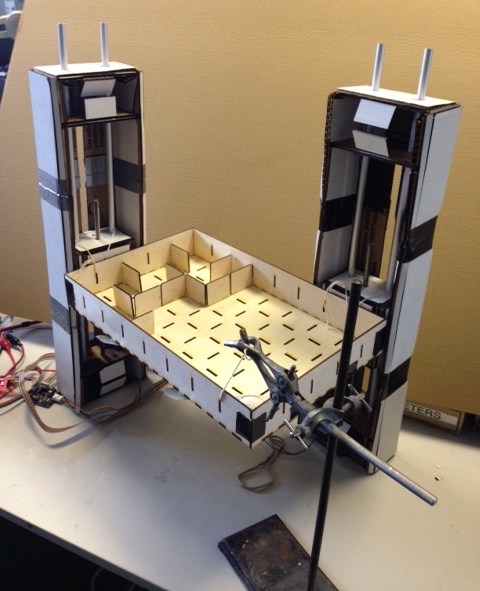
Lasercut
plywood maze
design with
living
hinge to enable
flexibility
during bed-tilting
(Kasper Andersan)
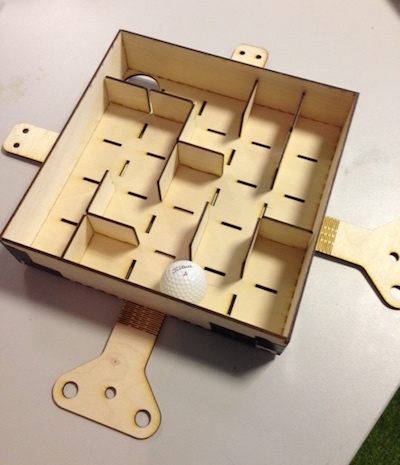
Link to Tutorials:
Fab
in a Box
Tutorial
Explanation
of Fabnet
Download
files:
Fabnet
Board
size