Week 9 - Moulding & Casting
Brief
The brief for this weeks
assignment was to use a 3 step process to create a cast part.
Step one - mill modelling wax (positive) then cast a flexible
(silicon/rubber) mould in the wax, then finally cast a plaster
reproduction of the wax shape.
Design - Sketchup/Solidworks
Initially I had the idea for creating a door number for my new
house. This being a fairly simple 3d model I chose to use
Sketch-up instead of my more familiar Solidworks. I decided
that I wanted to make a funky shape so I found a font i liked
(magneto) then recessed the number into a half sphere with
attachment lugs to create this.
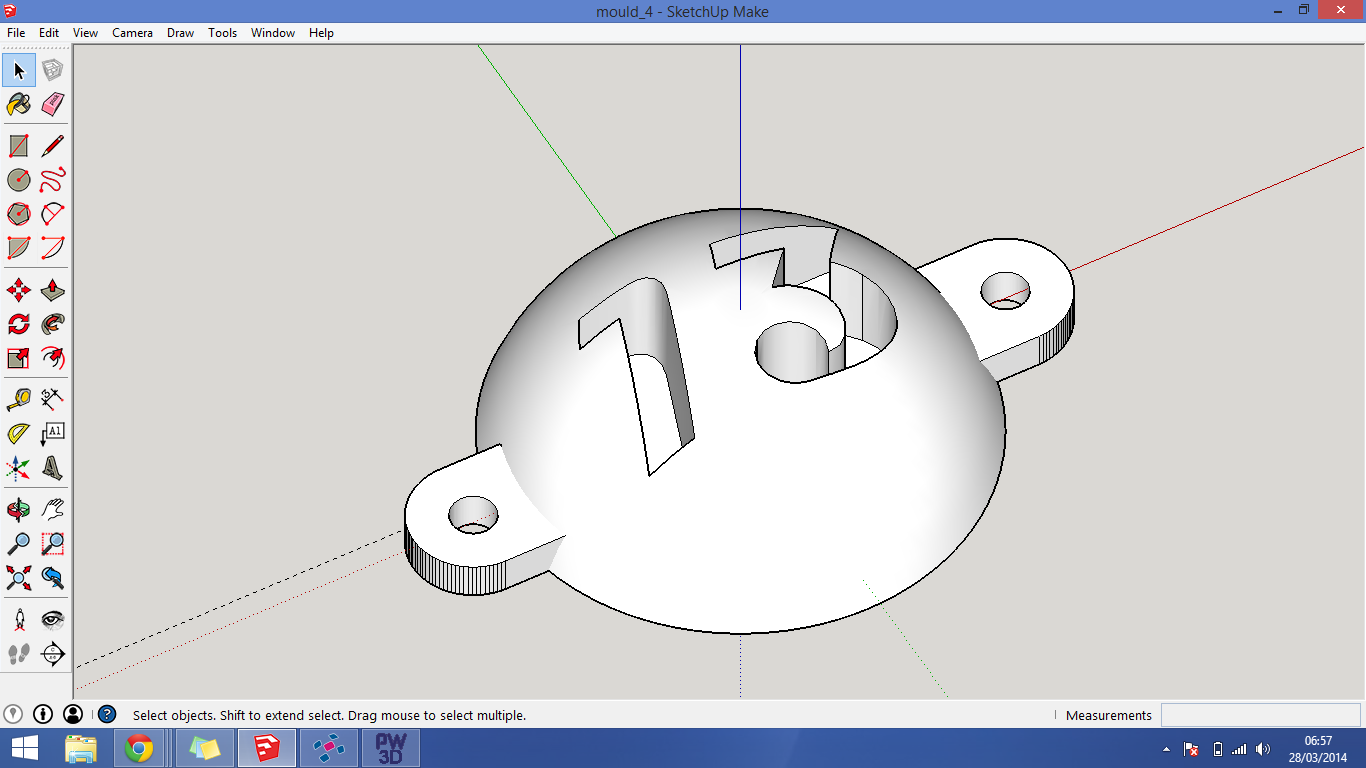
The shape itself was
quite quick to model but with many things in Sketch-up it
did have some errors to correct along the way and although I
have the correct plugin to export to .stl, it is not
possible to control the resolution of the stl export. I then
looked at the .stl in Netfabb studio to check for errors and
found it to have multiple errors, including reversed normals
and holes.
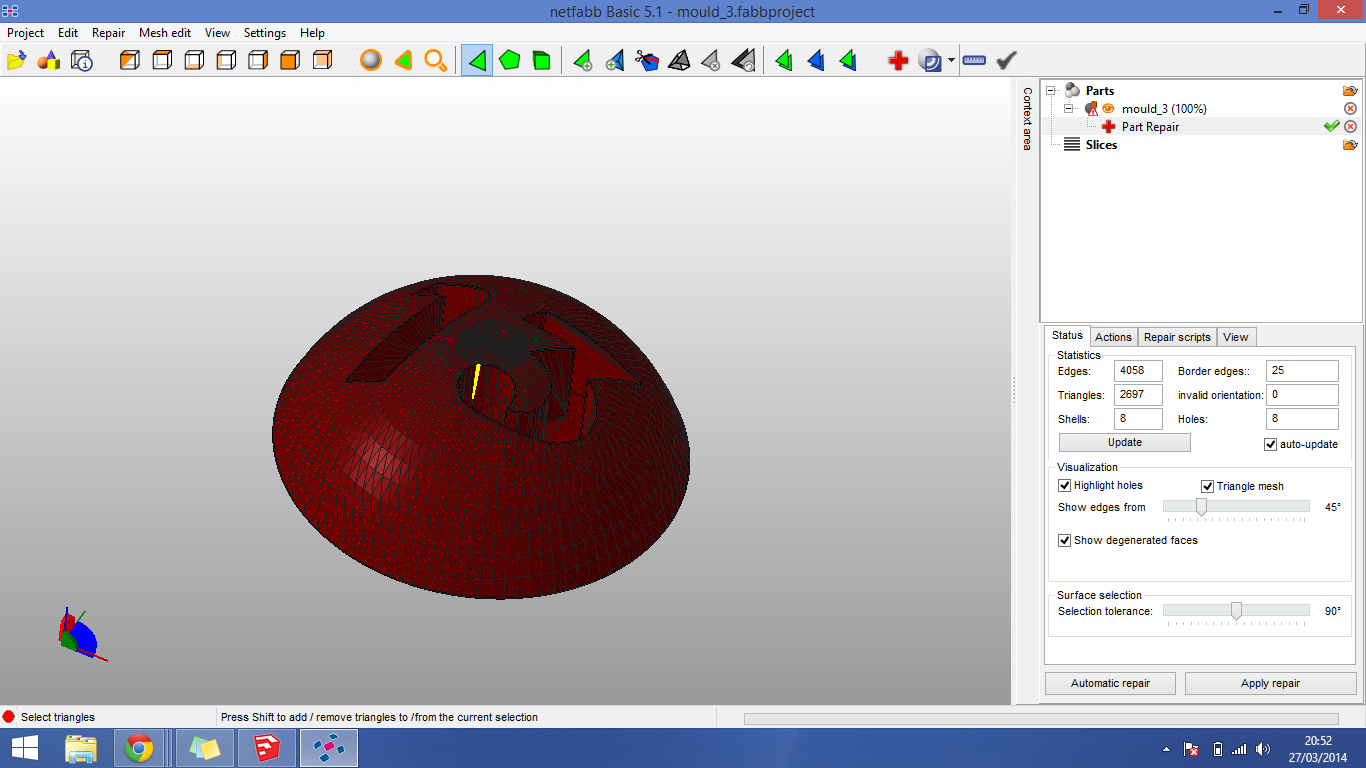
These are easily fixed using the repair
scripts in Netfabb but I felt the stl resolution would
give me a poor cast part with polygon surface detail and
so i decided to re-model the surface in Solidworks and
then be able to control the resolution of the .stl
export.
Toolpath Creation - Partworks 3D
Next I loaded my
.stl into Partworks 3D and configured my
toolpaths. I found Partworks 3D fairly straight
forward to use and the only tricky part was
ensuring my model with walls could fit on my
block of modelling wax.
*TIP* Remember to allow
for wall thickness around the milled shape
(typically 2mm or above) and ensure you mill
at least 2 mm below the wax surface to allow
for a bottom wall thickness of
silicon to form.
I
chose to use a 1/8" down cutter
to mill my roughing toolpath.
The reason I chose this was I
needed 30mm of 1/8" diameter
cutting flute and shaft length
and all other stock bits moved
from a smaller cutting flute to
a larger diameter shank, which
would have caught on the top of
the mould at the lower cutting
areas.
Here is the preview shown below
For finishing I chose to use 1/8 inch
ball nose bit. I used this bit as I have a half sphere shape
which I felt would be better replicated using the ball nose
instead of the flat end mill alternative. I did give this some
thought as it was highlighted in the lecture that flat ends
give you a true flat on recessed features which got me
thinking about which bit is best for 3D milling?
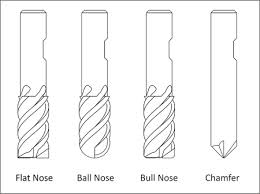
From reading some forum posts I
understand the limitations of using a ball and flat end mill
and that is why it seems the best compromise is to use a bull
cutter. As shown in the diagram above a bull cutter has the
best of both worlds with a mostly flat bottom and a small
radius to do full contoured 3d milling. Having identified the
theoretical correct choice for my milling I still had to
choose from the stock at the lab and that is why I chose the
1/8" ball nose.
The main difference in programming a ball nose for a toolpath
is the stepover value, which takes its toll on the tooling
time. For a flat end-mill a typical value is 50% whereas a
ball nose requires less than 10% for a decent finish and for
this I chose 5% (to get the best resolution without taking all
day). In total my toolpath times lasted approx 1h45 with 40
mins roughing 1:05 finishing. Considering the finishing
toolpath is only getting rid of a very small amount of
material the time is significantly more than the roughing.
Having said that I chose to mill my wax using the Shopbot and
not the Modella as from experience my job would have taken at
least 3 X longer using the smaller machine.
Here is my finishing toolpath preview
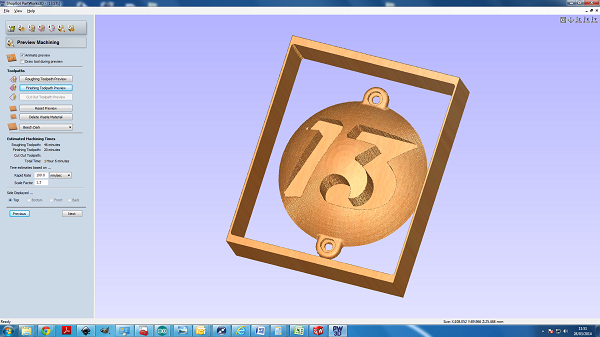
Milling - Shopbot
I set the
machine up in the normal way, the only change to milling wood
was that I took off the protective plastic skirt away and
didn't use the extractor fan. The reason for this was to allow
me to recycle the milled wax swarf and as the wax has an
easily scratchable surface I didn't want the plastic guard to
have the chance to damage my model. The last difference in
set-up was that I needed to make a jig to hold the wax in
place. I think a jig is the best option to restrict movement
without having to to use clamps that extend above the model
surface or counter-sink screws that need to go through the wax
(and may cause cracking). The spindle speed rpm used was 8000.
I read many use slower rpm but as i wanted to machine quickly
and I felt a medium speed rpm would help with that.
Here is my model after the roughing
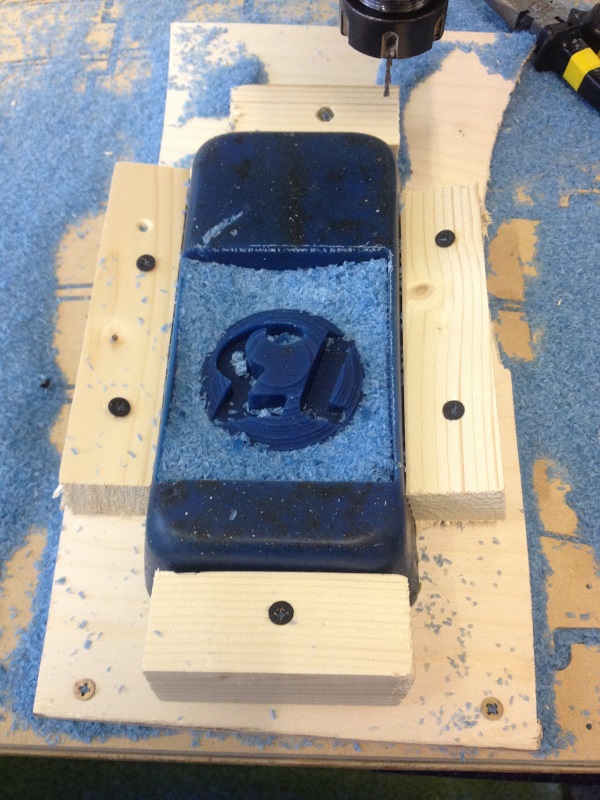
and after finishing......
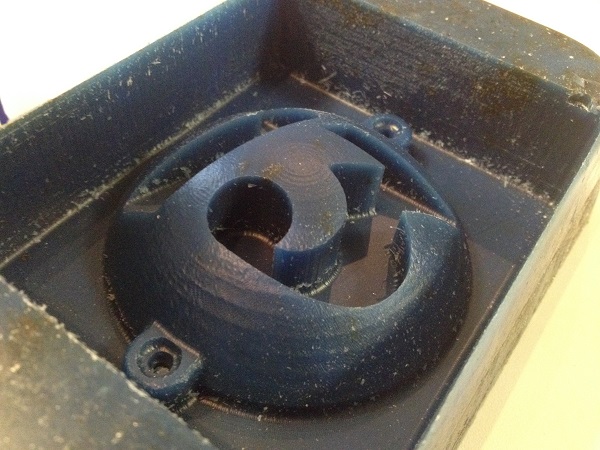
Moulding & Casting
Next I
cleaned up my wax using some cotton buds and then mixed the
smooth-on rubber compound we had in stock. I followed
instructions but as the parts had been opened I didn't expect
them to still be within shelf life, but without any other
material I gave it a try.
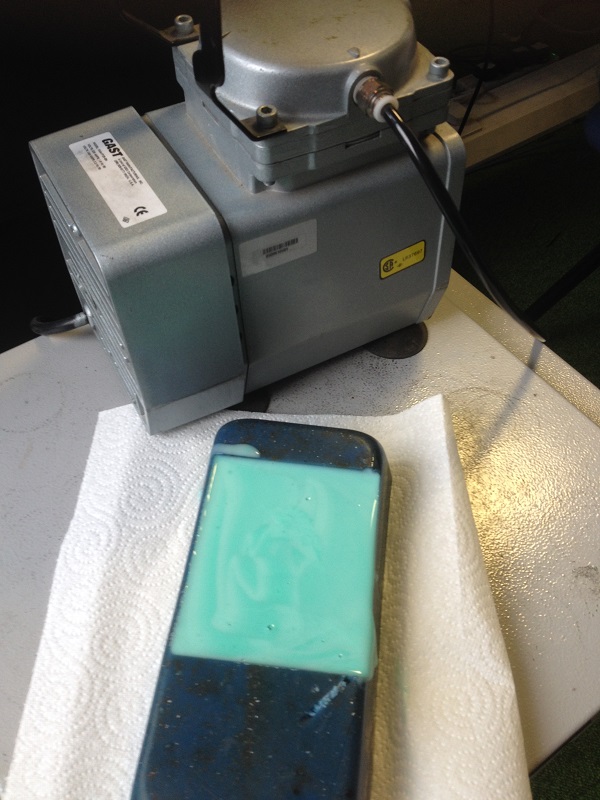
I used the compressor to vibrate the mixture to help release
air bubbles and the Fab Vac-Chamber to suck bubbles from the
mixture.
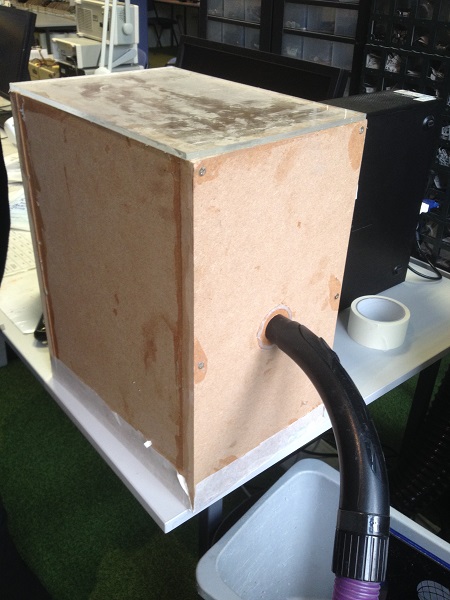
Here is the result.
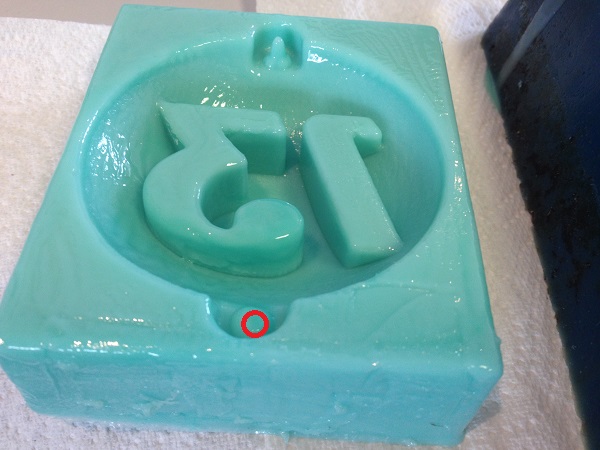
Not bad, but not fully cured (sticky surface) and an error on
the shape of one lugs caused by trapped air in the mixture. To
cure fully I put on a very low oven temp (40C) for an
additional 2 hours. Then I cast a Herculite Stone plaster in
the rubber. We have 3 plasters in stick but they all seem to
have similar properties (from the data sheet) so I chose the
Herculite Stone and mixed to the 100:33 ratio (Plaster:Water)
by weight. The mixture was easy to mix together, just make
sure you add the powder gradually into the water whilst
stirring to stop lumps forming.
Here is the result.
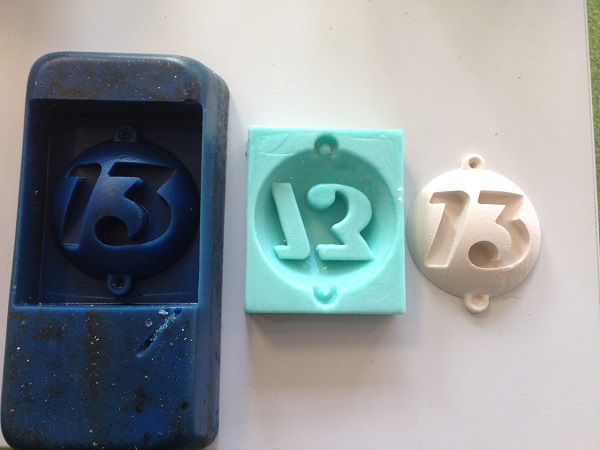
Comparing the three its
it's clear to see the surface finish of the rubber mould has
lost the detail of the cut wax sphere as the material didn't
cure in the mould properly. Not too bad though.
I decided to try a new mould with some RTV 2 silicon to
try and improve the surface finish. I have used this material
in the past on prototyping projects and hoped for a better
result. Instead of equal mix the RTV2 uses a small amount of
catalyst (4%) to mix through the silicon to start the
hardening process. The mixture is more viscous and
significantly harder to mix and pour. The vac-chamber was a
must use when creating a mould with this silicon. I left the
mould in the vac chamber for approx 15 minutes and let it cure
over-night. Here is the result.
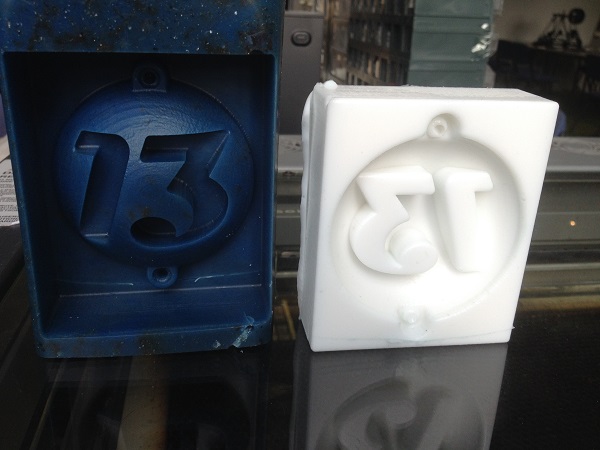
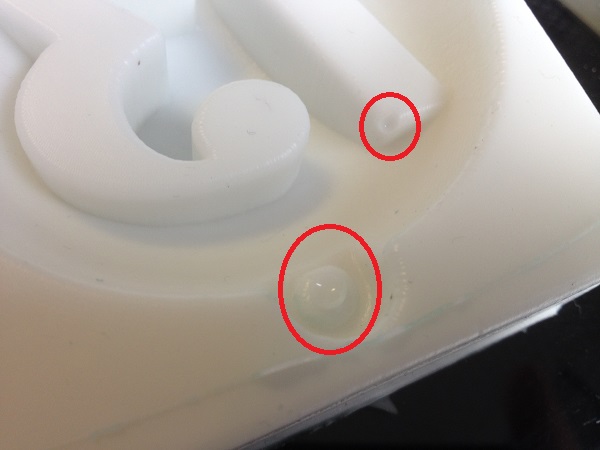
The vac chamber didn't get all the bubbles.....damn.
So I had to patch up the silicon with some bluetack.
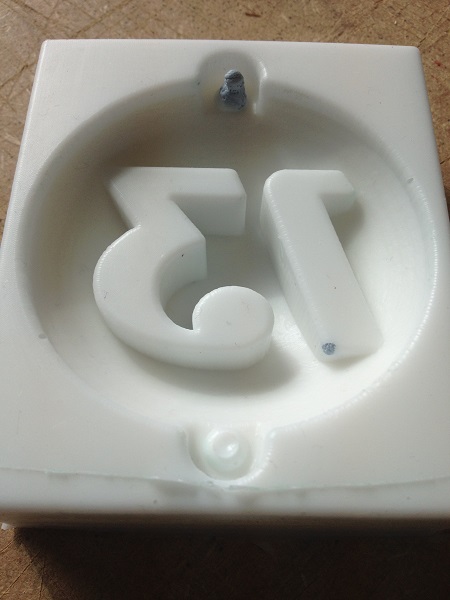
Worked quit nicely actually but there was one area of the
lower lug that I couldn't patch up as the bluetack had nothing
to fit into so instead I set up a rig to suspend the bluetack
into the mould for the plaster-cast.
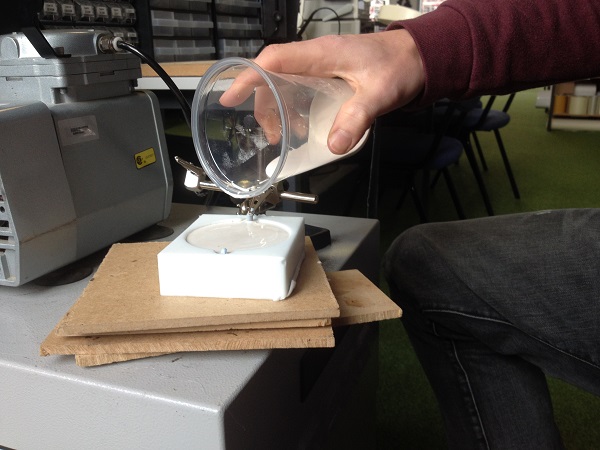
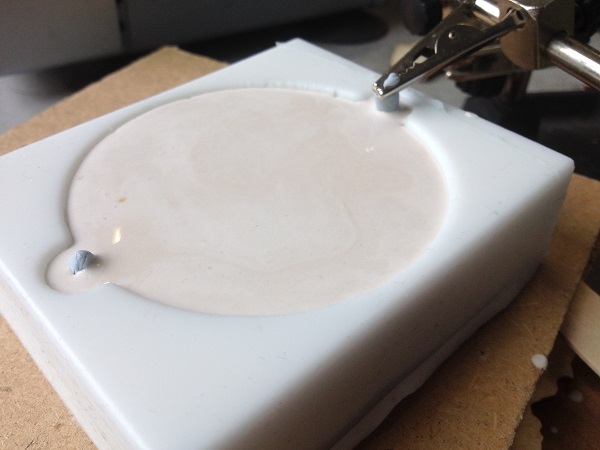
Result
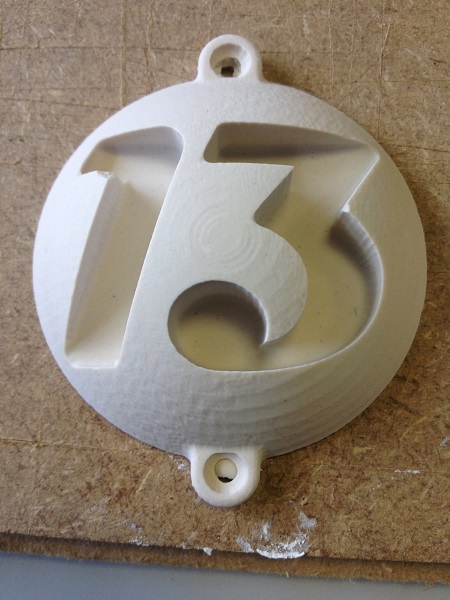
Not perfect. Despite doing a few casts they all had minor
imperfections in similar areas that are thin and therefore
inherently weak. Maybe a design flaw on the thin edges
(radiused edges would have been stronger, and less likely to
break). It took quite a lot of force to de-mould the cast and
with all the force concentrating on the thin edge of the cast
it seems inevitable that some edge damage would occur. I
couldn't work out a way to get round this so decided to do the
best I could to mask the imperfections with paint, (it is
going on my front door after all)
I used acrylic paints and here is the final result.
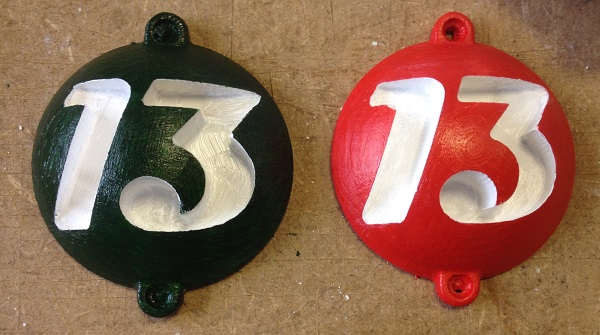
Quite happy with the result, although my colleagues all say it
looks like I live at number 73 when it clearly says 13! Tut
tut some people have no style.
Downloadable
Files
Sketchup 2014
Stl
Partworks 3D
Roughing
toolpath
Finishing
toolpath