composites
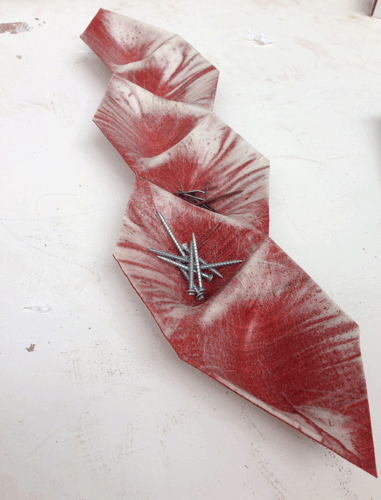
"Runner" bowl
Khadi is the beautiful, raw-spun cotton fabric of India. It was worn by Ghandi, and forms an important part of the soul of India. It has a slight sheen, often excentuated by heavy starching, which turns it into a beautifully striated, paper-like cloth. Ahmedabad, where FabLab CPET is situated, is not only the home of Ghandi's ashram and many of his activities, but is also a historically important mill town producing fabrics of all types.
For a while, I have wanted to "capture" some of these amazing fabrics through a resin-based composite structure. For the Composite assignment, for FabAcademy, I made a long series of connected bowls using khadi impregnated and preserved with liquid plastic.
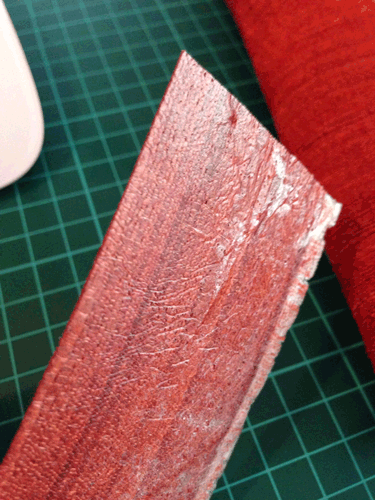
khadi composite test
materials
- XPS (extruded polystyrene)
- khadi (1m by 1.5m)
- Smooth-On 325 (Clear, Urathane plastic)
- plastic sheeting (from trash bags)
- lots of clamps
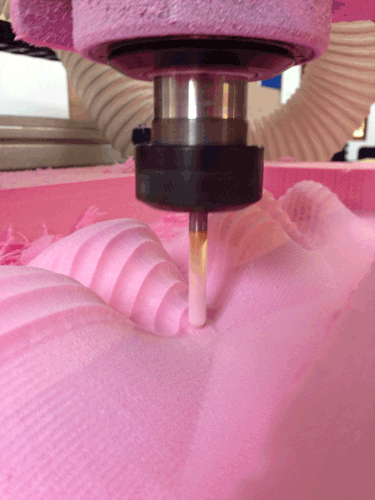
milling (ShopBot)
process
-
Using constuction/insulation foam (XPS), I milled out a two-part mould which would sandwhich the composite as it set. The geometry was a combination of Rhino geometry and some generated Grasshopper computations. I used some mesh softening to smooth the entire surface. (Rhino and Grasshopper files below.)
I milled the positive and negative sections (which were the same geometry (except mirrored) due to the fabric being so thin) as one peice, which I cut from the stock after the milling was complete. I used this guide titled "Router Bit Basics for CNC" and it was a great help.
Cutting Stats
- Spindle Speed: 18000 rpm
- Feed Rate: 2 ips
- Direction: Conventional Cut
- Roughing Bit: .5 in. ball-nose endmill
- Roughing time: about 1 hr.
- Finishing Bit: .25 in. ball-nose endmill
- Finishing time: about 2 hr.
- I was setting up the mould, getting everything ready, when my friend offered some high-tech plastic film that he had recieved as a sample. He suggested that since it was so stretchy and so smooth that it would make a great release film to put between the mould and the composite. So, we stretched the platic out a bit by warming it with a heat gun and then pressing it in the mould.
- I measured out the two-part plastic and dipped in four peices of khadi which I had cut to roughly the size of the mould. Working quickly, I sread each one out and then smooshed the entire setup together. Unfortunetly, it took some time to properly clamp everything down, but that was the least of the problems with this attempt.
- I had laied everything up around 10:00 AM, and when I cam back at around 17:00, I decided to open the mould. When I started to unlock the clamps and pull on the plastic, I found the platic not pealing away from the now-hardened khadi. Then it hit me: my friend had said the plastic film was "PU," poly-Urathane; the liquid plastic was also Urathane-based! Thus the two had chemically bonded to oneanother. :( This was not the only problem. The four layers of fabric made the entire composite too thick.
- Luckily, the mould was still in-tact. I quickly cut two peices of khadi and measured out some plastic quickly laying-up the laminations. Instead of the PU film, I used the plastic from a cheap trash bag. I had used this plastic for my test peice, so I knew it worked. I clamped the mould to itself and left it to sit overnight.
- The next morning, I opened the mould and pealed off the plastic. Decent results. While there were large patches of air boubbles, the shape had been acheaved (even though the whole thing was a little wobblely... more hardener next time). in many of the places, the khadi showed beautifully. I trimmed the exccess khadi from the sides and the peice was done. :)
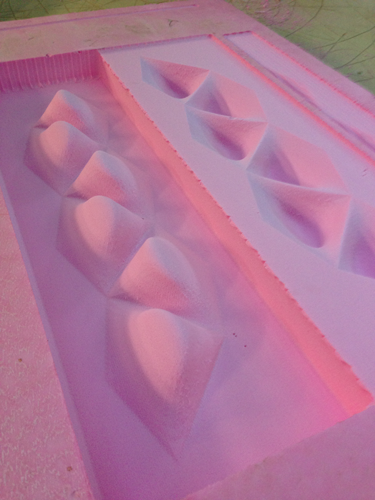
mould before it is cut out of the larger block of XPS
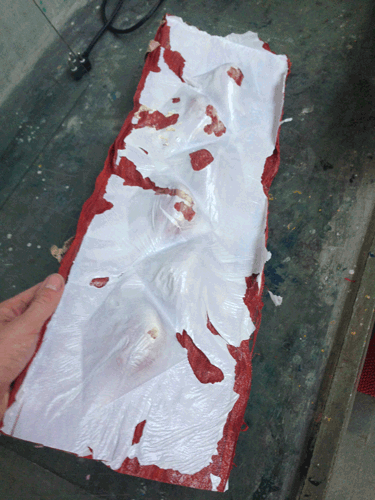
result of the first attempt ... :(
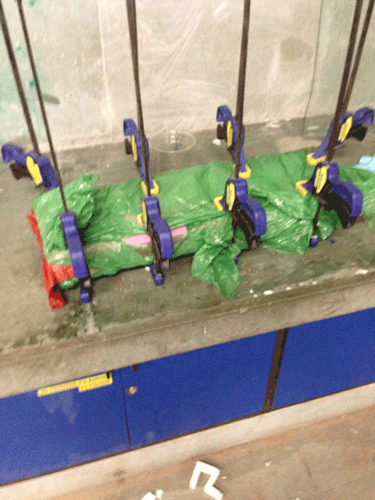
second try!
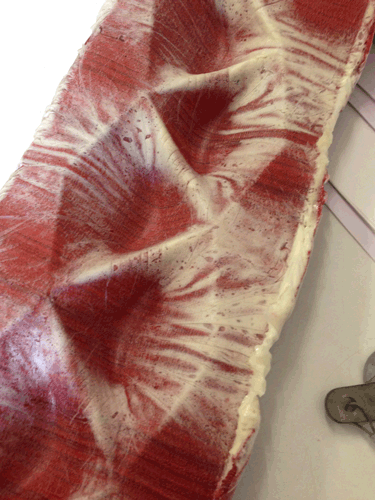
after release from mould
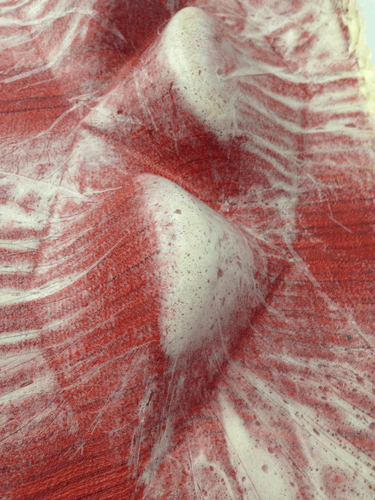
close up of convex surface, bubbles have been trapped
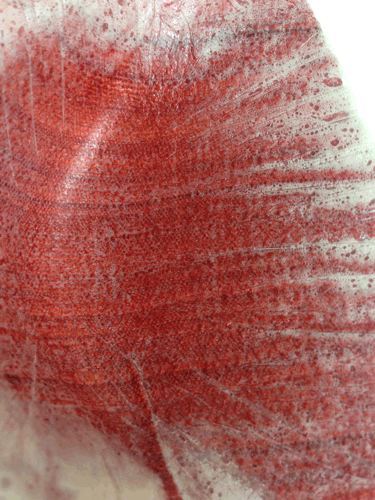
close up of concave (interior) surface, bubbles have, more-or-less, been push out