press-fit construction
background
I first found the inspiration for this from a project that happened in one of the MIT masters architecture studios. It involved an "interactive" installation in Lobby 7 of MIT where people could rearrange large, triangular, foam modules that had been milled out on a ShopBot. The modules were simple and produced fairly nice results, so, when I was asked to do a workshop for a bunch of middle-schoolers, I made a box full of smaller, card-board modules based on the same design.
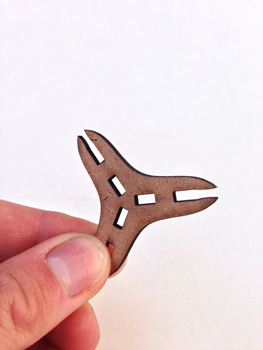
the module
the design
My adaptation to the design addressed the issue of structural integrity when using materials with a lower coefficient of fiction that blue, structural-foam. In my design, I added a notch that a snap flexure could grip onto. In order to make the calibration of the design/geometry with the materials and fabrication technique (laser cutting), I parameterized the design on Grasshopper (See "Files" section).
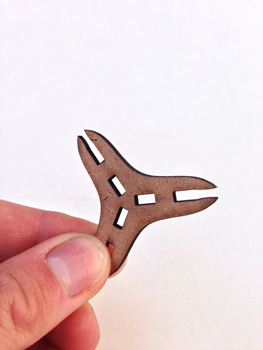
the module
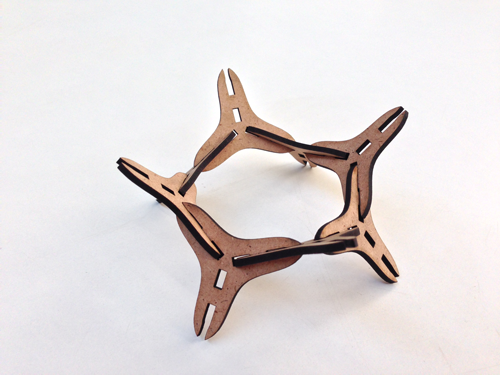
this shouldn't happen...
an interesting note
The interesting thing about this module is that, in perfect geometry, it should not produce the forms that it does. It should not be able to re-attach with itself to form rings. But because of the material (being flexible) and the laser cutting (the cut having a width greater than zero) there is some geometrical "give." I added to this give by making the slots .005" wider than the material. This allowed form more flexible systems. Yet, as the systems get larger and larger, the error reduces, slack disappears, and very ridged forms are created.
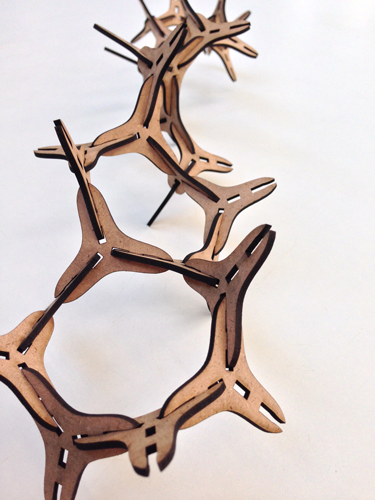
a linear structure
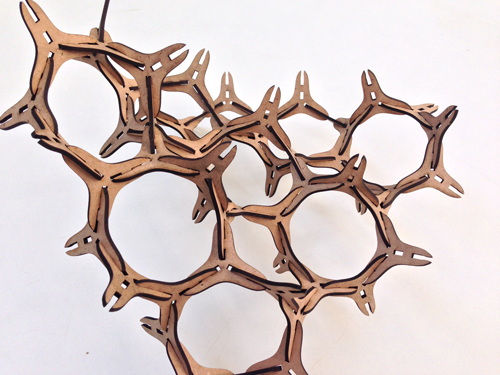
the surface created from the linear structure copied in v direction
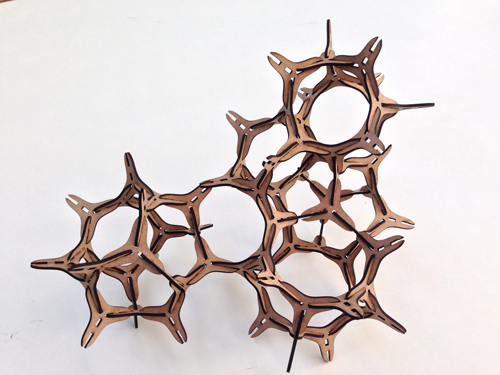
a structure that some of my students made