This week’s assignment is to make something "BIG".
The first step is to search what can I make for the FabLab, and I noticed that we did not have a bookcase to put some books or printed objects. In that case I decided to create one (1,60m x 1,60m).
The first was to design and model the bookcase with Inventor using a 15mm thick MDF.
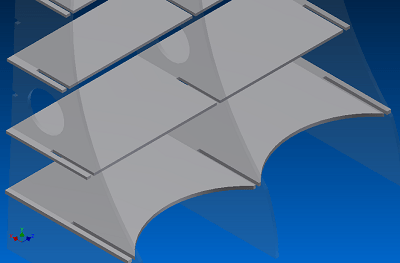
For the fit between the pieces I used only the Press-fit system.
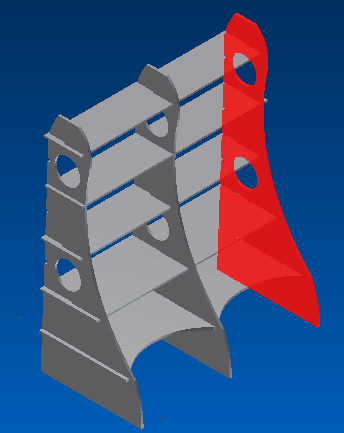
Once I finished the design, I had to make it, in this case I used the ShopBot machine and I used 3 sheets of 15mm thick MDF to give it a greater strength.
The first thing we do is to define the dimensions of the material (1.83 x 1.22 meters) and thickness (15 mm). Then, we import the cut pattern from CAD in .dxf format and now we choose how to cut each line, selecting, indicating the depth of cut, if it cuts outside, inside or over the line and add tabs to hold the parts while cutting and preventing movement or broken tools.
First, with the program you place the object. After that, you create the diferent trajectories of the tool.
To prevent movement of the sheet, it is necesary to set it using screws. The last picture respresents the different parameters of the drill.
We select the tool that we will use to make the cut. In our case it is a End Mill 1/4". It is important to select the right tool because in our design the corners have been done with a 1/4" tool. The Mill expels chips compressing them down and preventing pieces movement.
After the creation of the drill profile, you create the cut profile selecting the object.
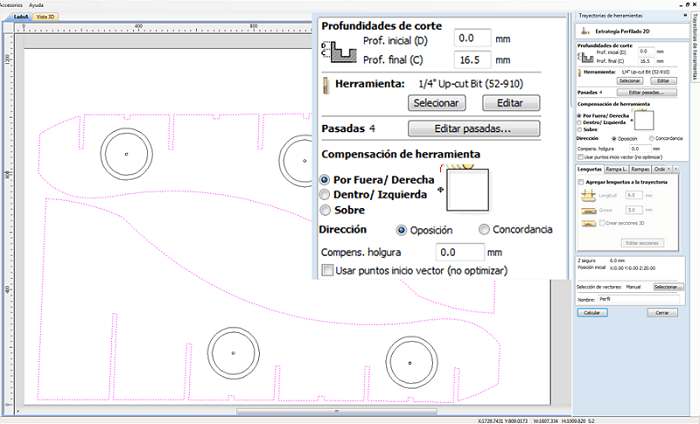
In this step,I needed to program the cuts in 4 passes. The speeds chosen was 170.0 to advance with a depth of 1,25 mm to make the cut.
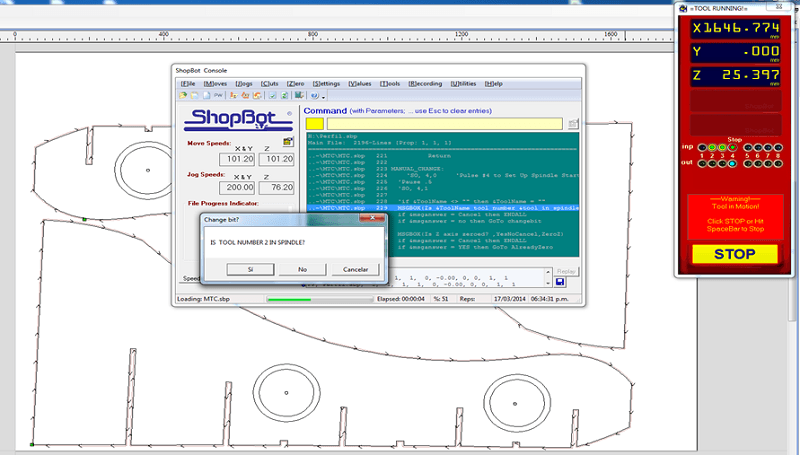
In the picture above we see the cutting path.
When you finished the creation of profiles, you can calibrate the position of the axes x, y, and z.
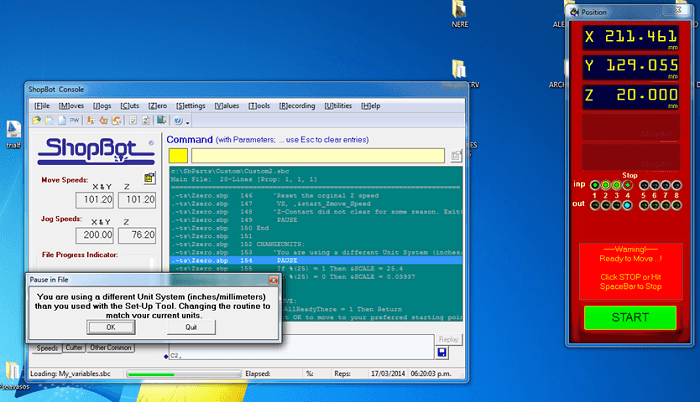
Pictures of Z calibration
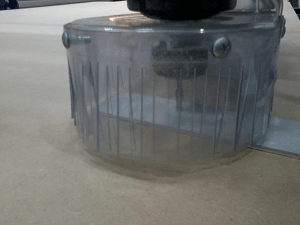
Pictures of X and Y calibration
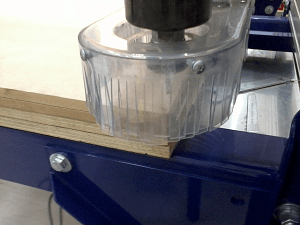
Now, You can begin the cut. first put and fix the sheet.
After cutting, I had problems fitting the pieces. I had planned a 15.2 mm width and the average width was only 14.8 making it not to fit. For that I had to enlarge the socket. So, I took a piece of steel to remove the leftovers.
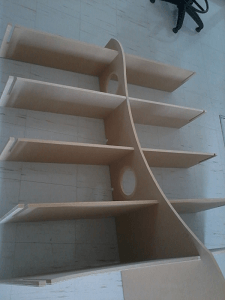
All files are here :
Interesting and stimuling assigment
That's all ....