|
Modeling
-while modeling i came up with more
than one design, most of them were too complex to be
exported as a STL I tried more
than one shape, square, triangle, rectangle and
finally i came up with an idea, to simplify the
connections between the shapes
makes it easier for rhino to recognize

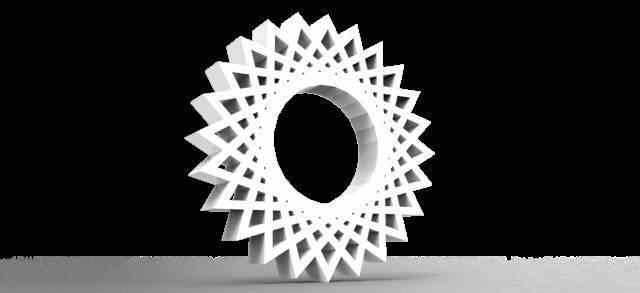
By trimming the meshes it gave me
a more dynamic shape. also i tried to boleen them,
group by group till finally rhino managed to
union them all
This box sounding the design is the Wax mold I'm
milling my design in. Actually after starting to mill
i though that if the outline of the
mold was circular like that of the design, it would've
saved time and material
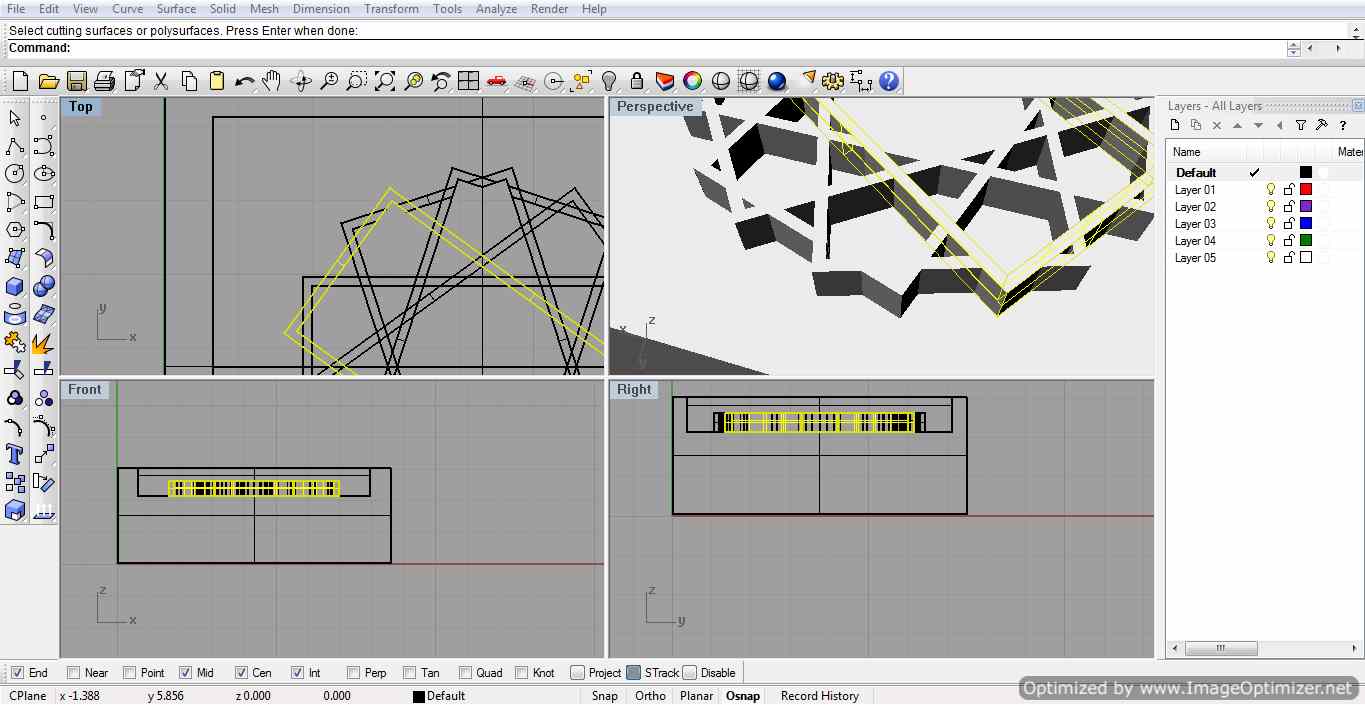
TIP Take your time to modify your
design to save as much as you can, TIME AND MONEY
Milling
I used the IModela to mill the
design in wax. Before exporting your design from rhino
as a STL Make Sure it's LEFT
TOP point is at
the origin
(0,0,0) as the machine starts working from top to
bottom and from left to right and also make
sure its in millimeters other
wise the machine wouldn't
recognize it
The Machine mill STLs on two
stages, ROUGH and FINAL where the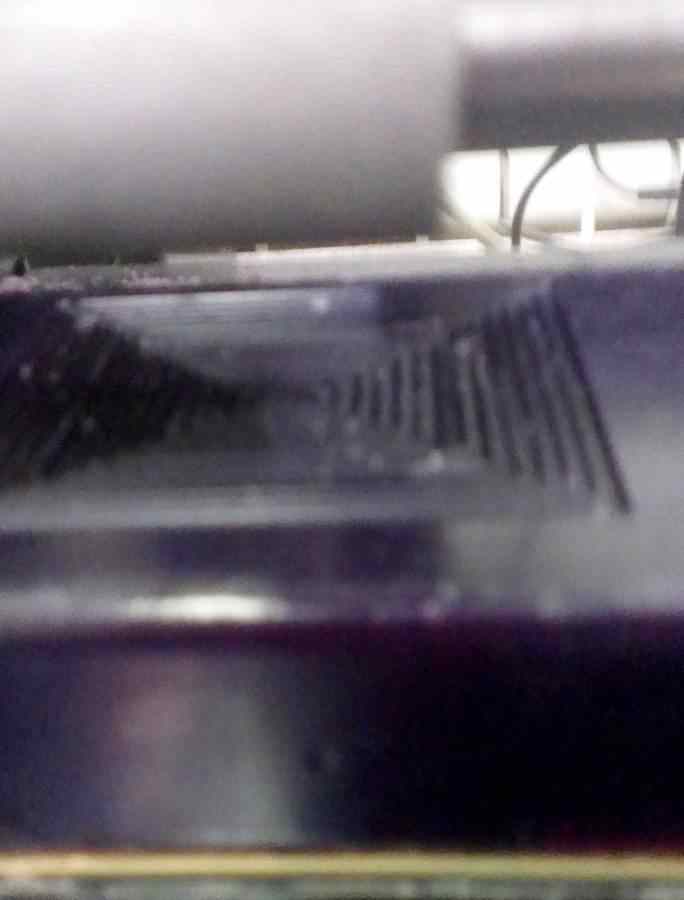
Rough uses the bold pin, and it takes less time than the
final, it also
moves on both axis
(x,y) at the same time. While the FINAL, uses a
finer pin to
smoother the contours of your design, it will take much
more time than the first one, since it mill your design
twice on as
straight lines in the direction, then the second is doing
the same
thing but in the X direction. Both procedures with
variations of the Z
direction according to your design's
surface
t
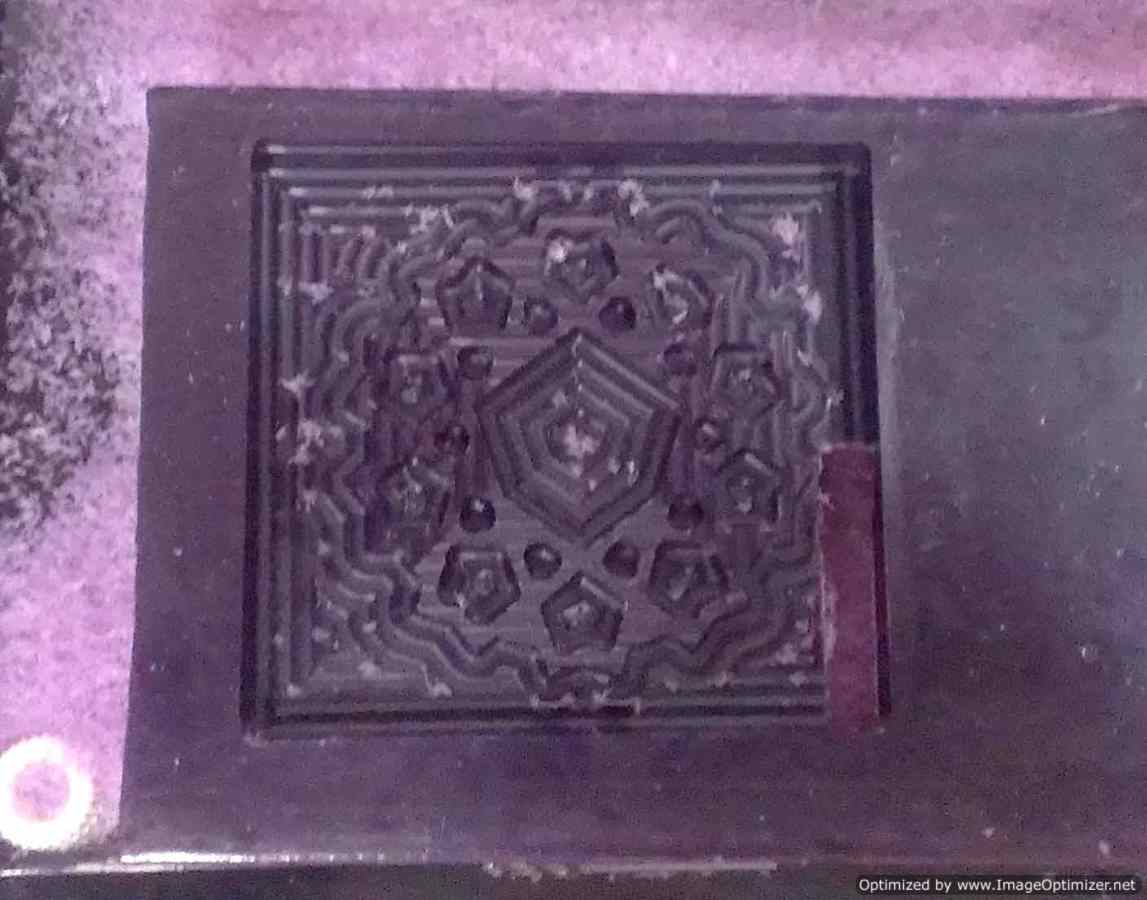
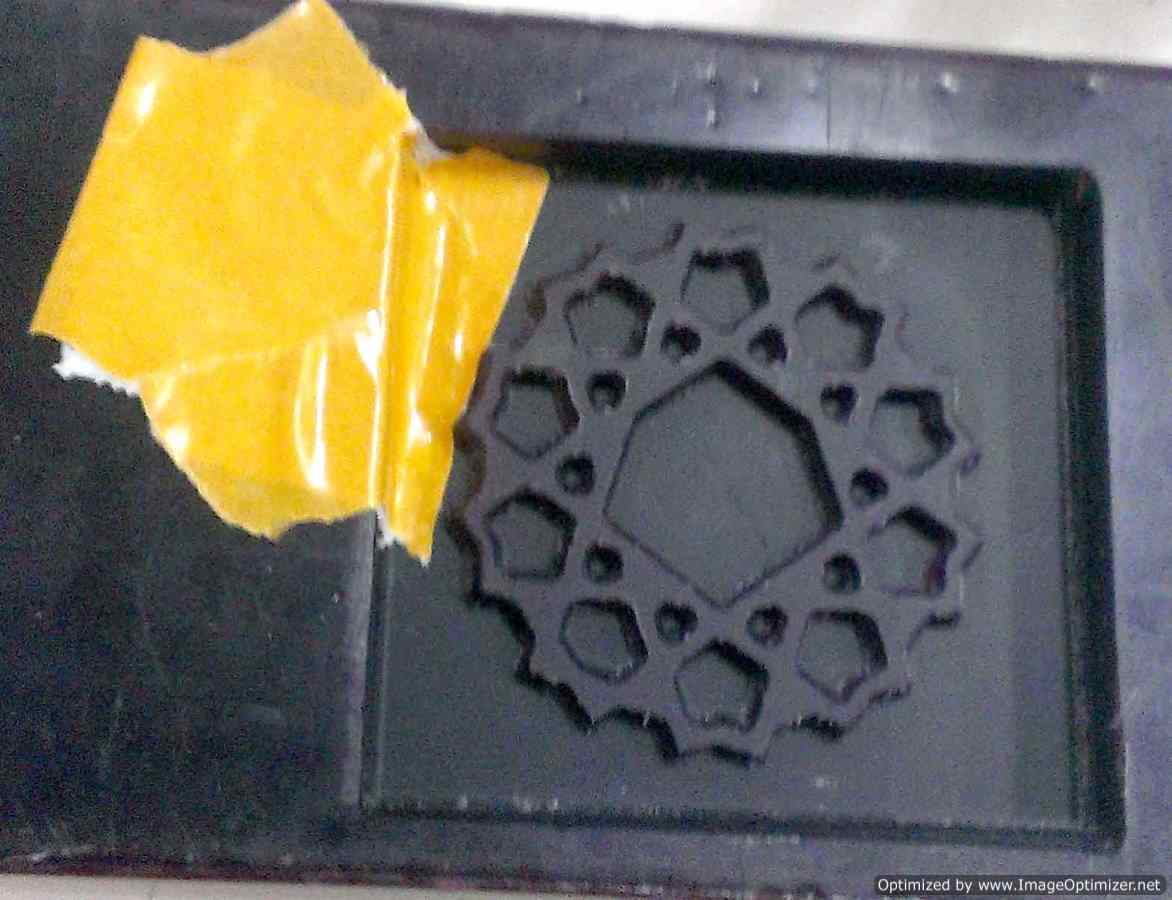
i had an in individual problem with
the mold is that i was using a
used wax bar so the borders of my
design overlapped the old
design milled in the bar. i had
to fill the opening with tape
! let's hope it works
Cooking
Finally i did the mixture
of the rubber mold and
poured it in the wax, it
still has six hours
to go!
IN 20 MINS
After
finishing the mold you take it off the wax, you then
get the negative of your design. Then you mix the
solution for your
final piece. you should use same amount from both jars
and mix them together then pour it to your rubber
mold, but by
changing the ratio between the two solution you can
control how hard or flexible your final piece will be
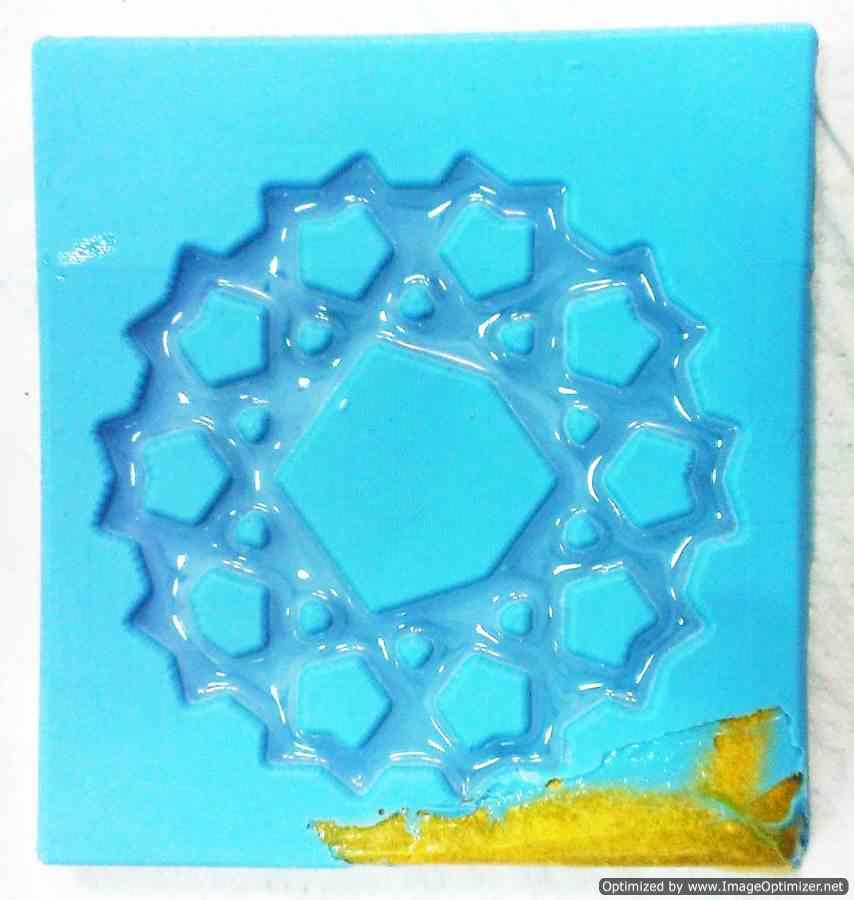 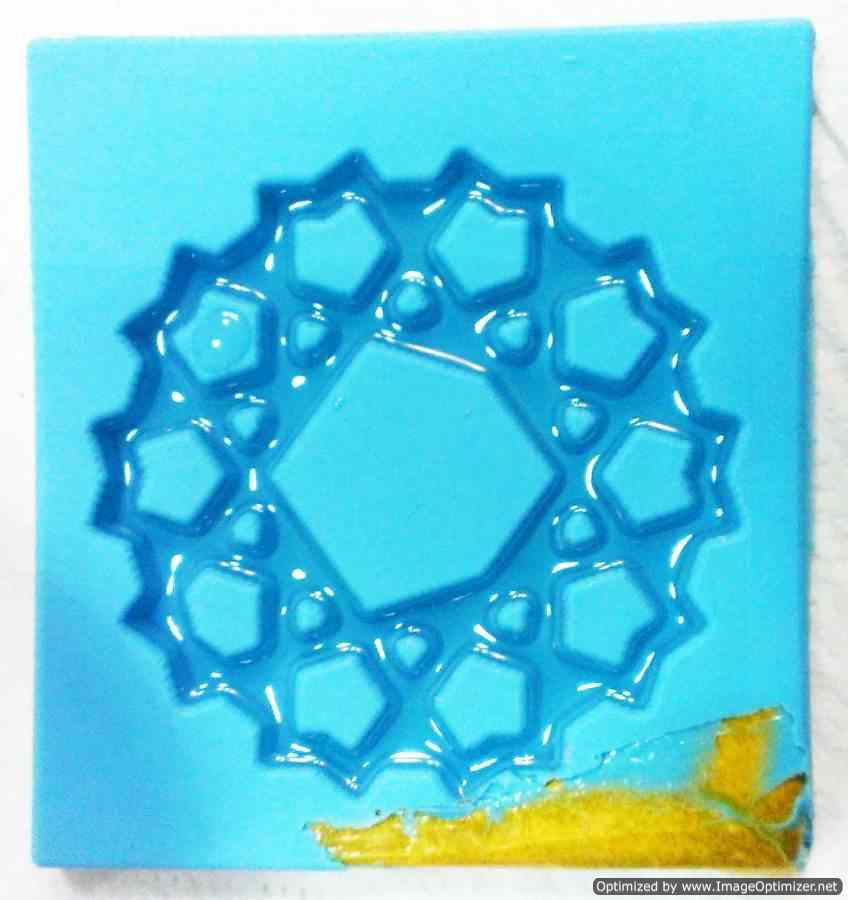
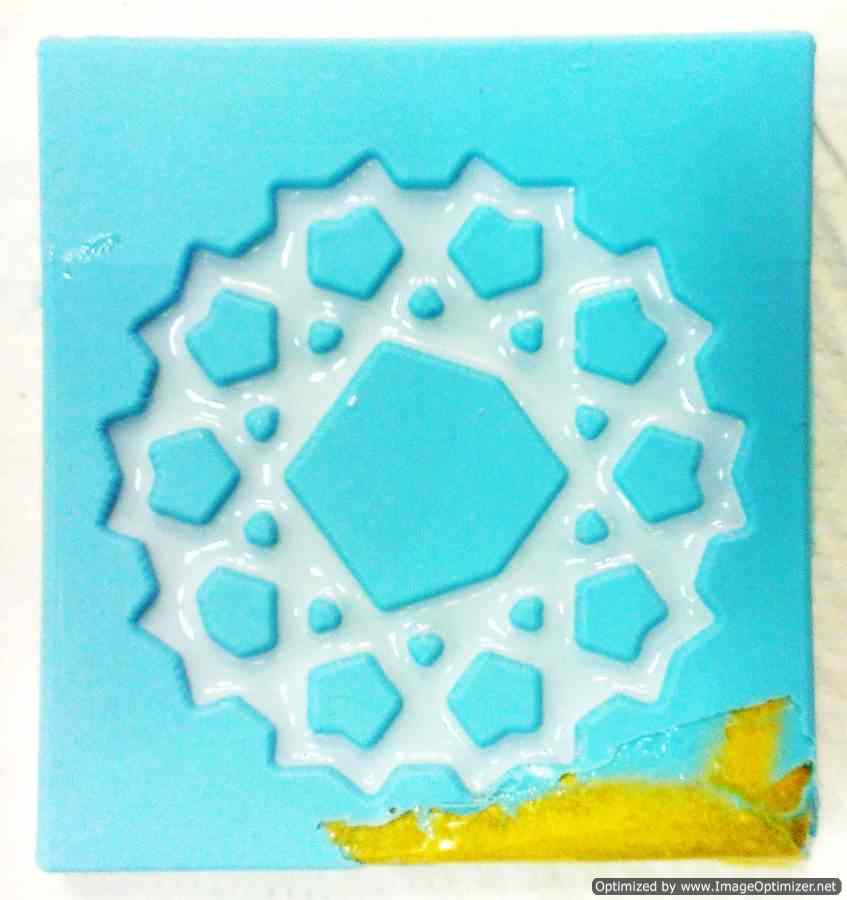 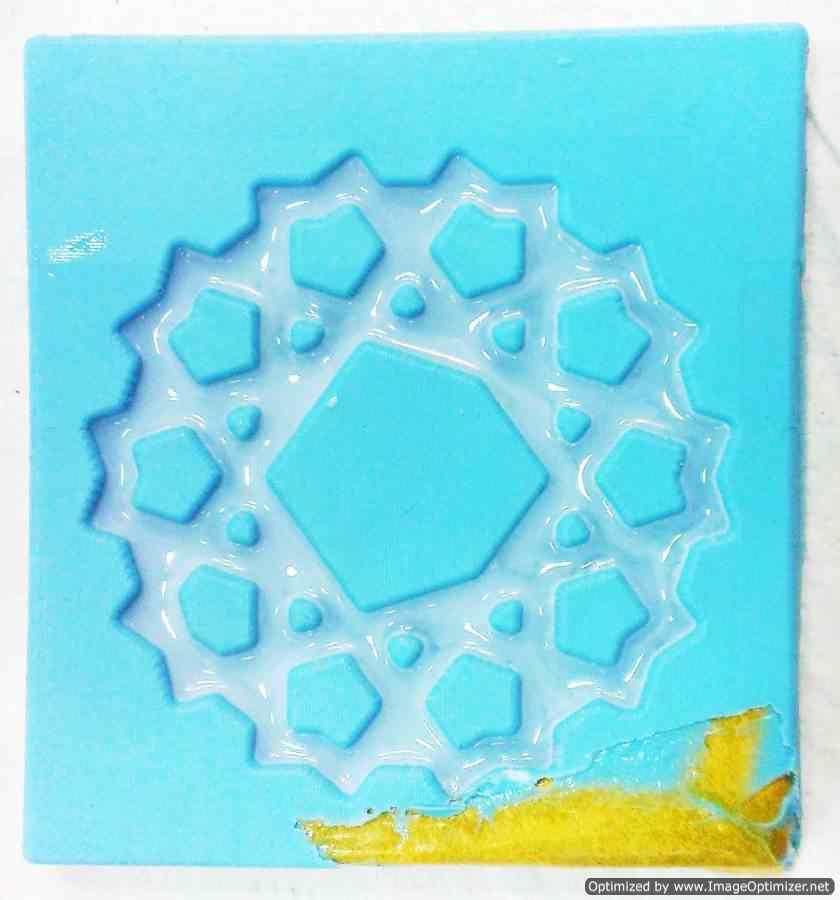

|
>Proposal
>Digital model
>Laser Cutting
>Electronic
production
>3D Scanning
& Printing
>Electronic
Design
>Molding &
Casting
>Embedded programing
>Computer-controlled
machining
>Input devices
>Composites
|