FabLab Academy 2012
Manchester Lab
David Forgham-Bailey
Comments:
Software:
Hardware: Roland Modela
Weekly Assignment:
I decided to make an eyeball unit for my final project. We were
restricted to milling a wax block, then using this to form a silicone
mould, from which the final 3D shape will be cast.
I designed a two part mould which will produce a silicone mould
(2 part - with registration lugs and pouring/filling spout -
Narrative:
having
produced
the .stl file the milling path is made my Modela
Player. The wax block is first cut to make the top face flat and tool
zeroed. Next path is the roughing out - leave enough work for a final
cut with a round nose tool. Finishing cut is final path - this will
determine the quality of the finished item.
.
Materials:
Machine Settings:
Photos:
<>
Files:
Drawings:
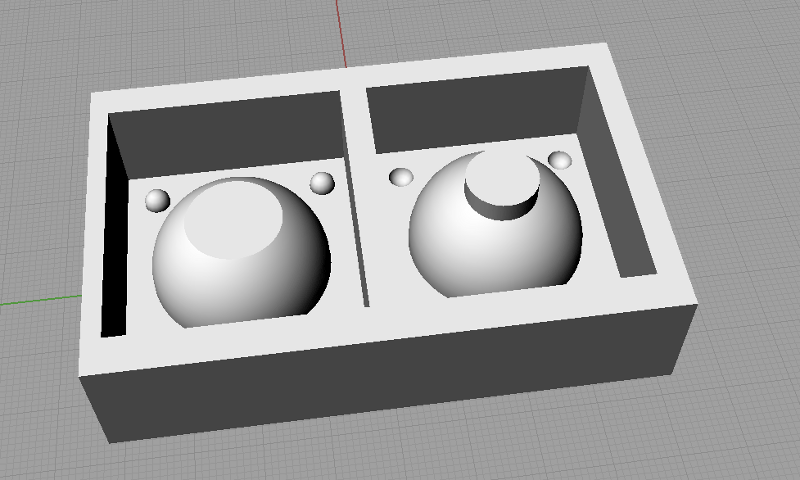
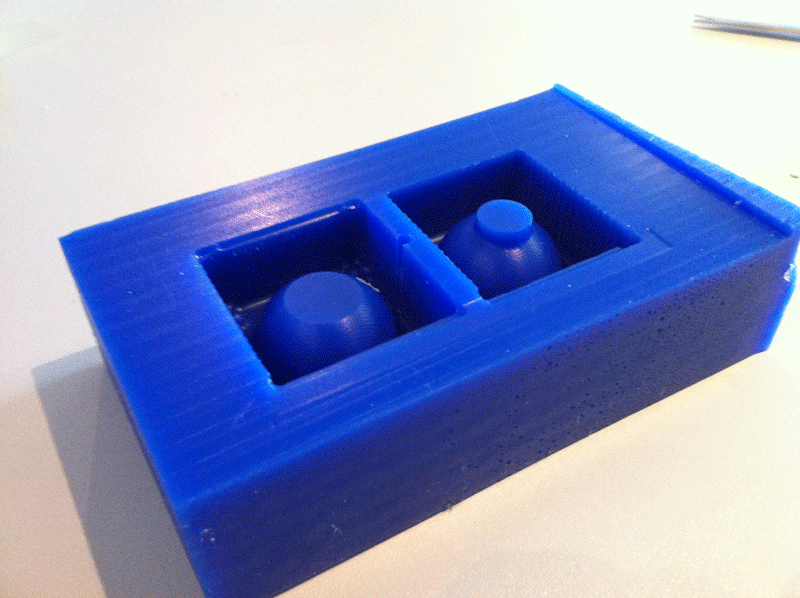
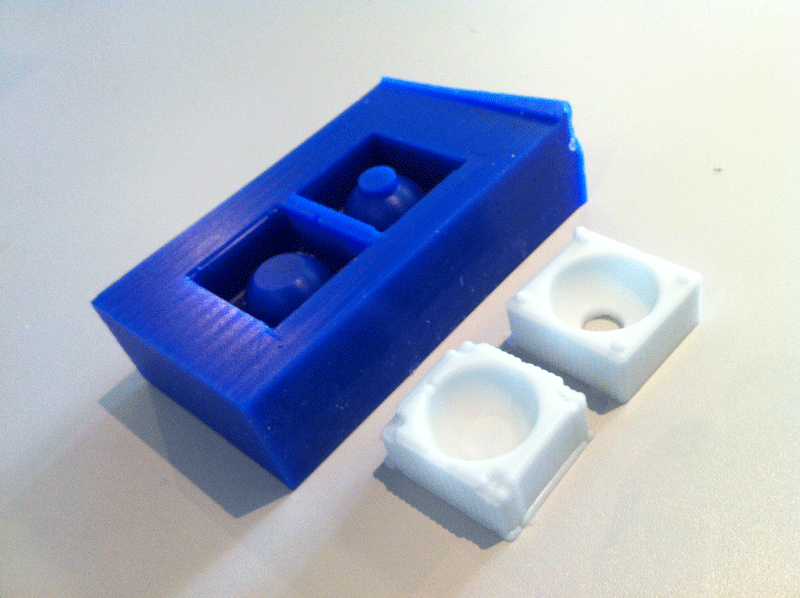
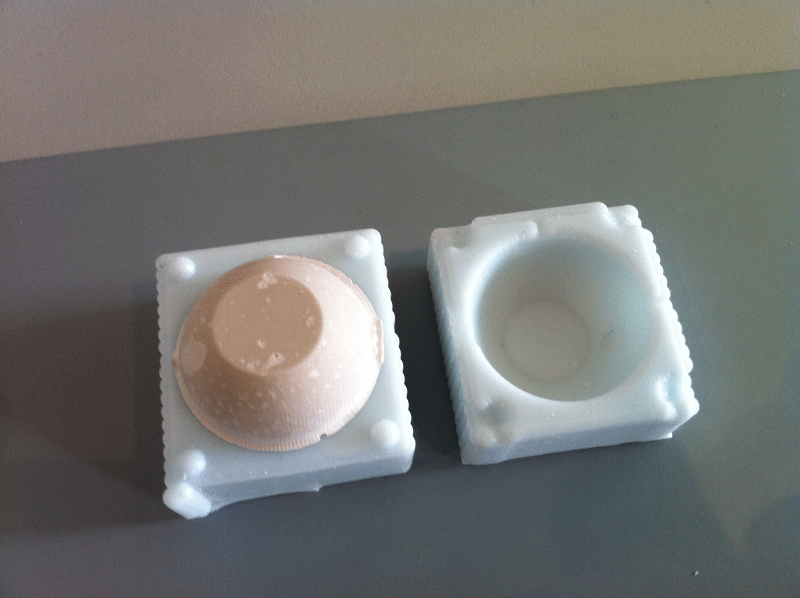
External Links:
Course Notes:
Similar to 3D printing but better finish and quicker - Good for short
production run - not good for parts within parts -
Injection - sprue/runner/gate/vent/partition line/flashing
insert casting - place object in mould before casting
vacuum - blow - inflate - bottles - flexible - start with rigid
material then use flexible - need mould release - make part and bend
mould to demould
machinable wax - high temp wax - remelt and reuse - melt shavings from
machining - remelt and reuse - Good Surface finish
low temp wax - good for transferring - make mould from other objects
rigid foam - building material - use on ShopBot - glue sheets together
for deeper mould - not good finish due to granular foam use Gesso to
seal then sand.
alginate gel - non toxic - one shot use - good for body casts
urethane rubber - plastic - stick to each other - v stretchy -
silicone - not as stretchy - completely inert - will not stick
PDMS - Latex - avoid - cures by drying - takes many coats - take long
time
thermoplastic - fluid when heated - thermoset - needs heat to cure
Drystone - fancy plaster - adds polymer matrix to strengthen - quick dry
Hydro Stone - mix of portland cement and plaster takes a little longer
- cheap $30 - 50lb - waste is just rock - good starting point low
viscosity -
metal powder - ceramic powder - low temp alloys - glass can
be moulded - food -
additives - fibres - add strength - -fillers - add other
characteristics - glass spheres for bulk - other s for
conductivity/density/flexibility/colour/etc
Beware - if water is added to eurothane plastic it will foam -
mixing - mix well
deairing - removes bubles - avoid getting bubbles in first place -
vacuum chamber - residue
when stirring use shear - you have 10-15 mins to work and have bubbles
removed - filling pour slowly - tilt mould so vent on top design mould
for vent to work correctly
curing 150 degC - silicone use desk lamp to elevate temp - exothermic -
gets hot when curing
demould - taper - release agent - washing up liquid - shelf life 6-12
mths will not cur if too old - Keep container ring clean - will not
open if cures in place
safety - materil safety data sheet - disposable gloves - ventilation -
protection - can make you sensitive to the material
weekly project use - silicone rubber - hydrostone - drystone - 3D
toolpath - depth of cut must be possible with selected tool - what is
the cut depth of the tool?
Rough cut in layers to remove material - finish cut follows surface of
the part - tool overlap -
flat end mill for flat surfaces - ball end for round surfaces -
Composites - strong compression - not good in tension - composite makes
tension good - epoxy/carbon fibre - toxic - concrete/rebar - -adobe -
friendly composites - fabris with matrix - epoxy eurothane - needs
ventilation - oat building uses all materials - processes - compaction
infusion - 50/50 volume fraction
open mould - 1 side - *.png good at preserving dimensions