FabLab Academy 2012
Manchester Lab
David Forgham-Bailey
more than just cutting - upto 7 axis and more - robotic arm etc -
Roland Modela
Shopbot
KUMA
Type of material influences type of tool -
Materials:
Rigid foam insulation - polyeurothane foam - veneer plywood - mdf -
moulds/final parts - MDO - OSB-aluminium - Lexon-polycarbonate glass
Find local suppliers for materials....
TOOL BREAKAGE
Tooling: moves swarf away form cut - ONSRUD- SDS TOOLS - find uk
equiv... - Coatings: - make tool harder - A1TIN - cast iron - hard -
T1C - vioet brown - alloys - Titanium Nitrate - Gold - Gen purpose -
T1DR - specialist
centre cutting/slot cutting - up/down cut - good for finish on both
sides of ply - takes waste away from cut and face of material
mechanical feed - cutting depth - flat/bull end - flat cuts rectangular
slots - rough path leaves steps - bull finishing tool - use smaller
step order -
Diameter of tool / tool holding diam - steps shorter than flute depth -
length of tool - ensure long enough for work - Speed: - rpm of cutter -
feed - speed in lateral plane - Wood - highest rpm is 18000 see tooling
catalogue for speed/feed chart - 1/4 in tool (0.015mm) 18000rpm -
chipload calculator for Shopbot - if tool is hot after cut then feed
rate too slow
Lubricants: dishwasher fluid?
Fixturing: vises/clamps/screws - design positions when designing tool
path - draw hole where not cutting path - double sided carpet tape -
adhesive - encapsulation -
Kerf - diam of tool - offset - thickness of tool - cut on
inside/outside/on line - (changes with tool width)
Rhinocam-file formats -
Safety:
Comments:
Software: - Inkscape/Rhino/
Hardware: ShopBot - sanding equipment -
Weekly Assignment:
Make Something Big
Narrative:
I began this task with the firm idea of making a magic box - I have
had woodworking plans for manufacturing a magic box for a number of
years. But on reflection, the clash between Open Source and The
Magician's Code persuaded me to find something different.
I found an old plan of a 4x8ft sheet of ply which made a workstation
and matching stool and left no waste material - I spent a weekend
rejigging the plan to incorporate snapfit joints and made up a 3D model
to ensure the joints were correctly aligned. - I had reservations
about being able to secure the plywood to the Shopbot bed - but hoped
it might be
possible to use carpet tape. I decided to have a reserve plan if
this was not possible.
My research for ideas brought me to a set of play planks which I had as
a
child in the 1950's - (see images) - these are now called linkerlogs
and an opensource project.
From Mechanics Illustrated Dec 1953:
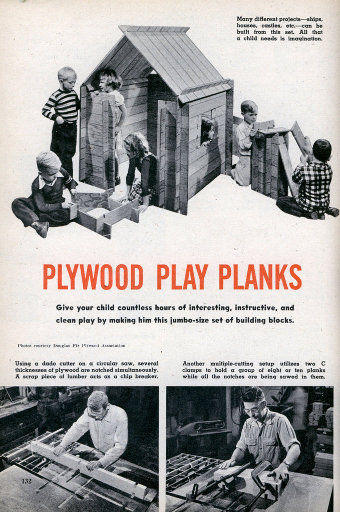
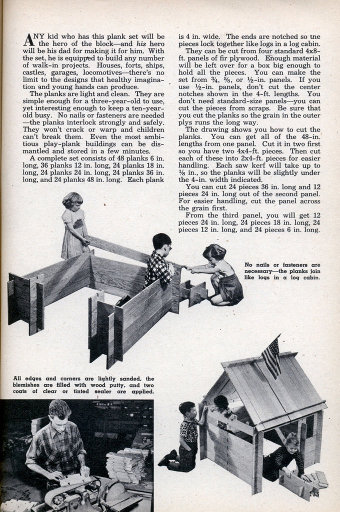
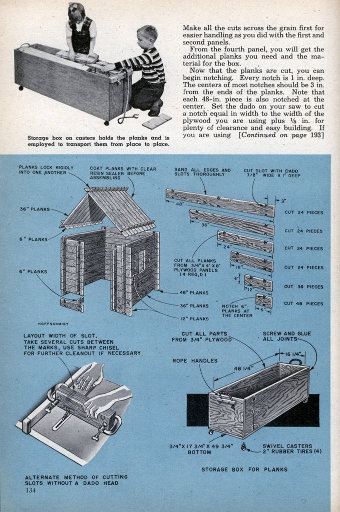
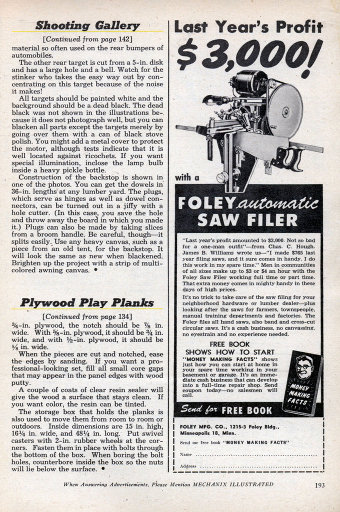
I used
Materials: 1/2inch plywood sheet - 4ft x 8ft
Machine Settings:1/4inch tool(up/down cut) - 18000rpm
Photos:
Toolpath:
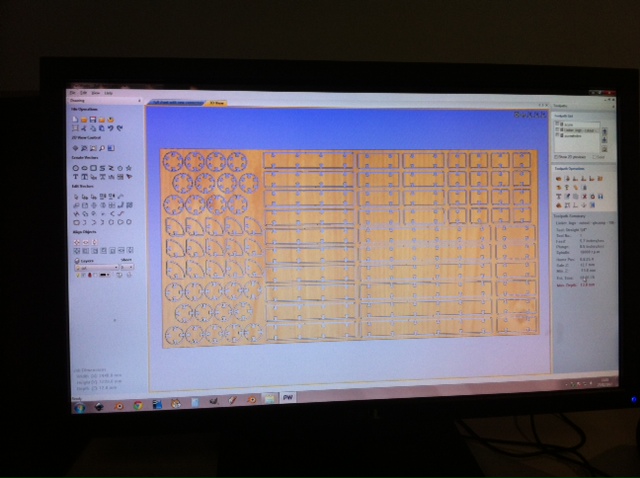
Shopbot bed - in action:
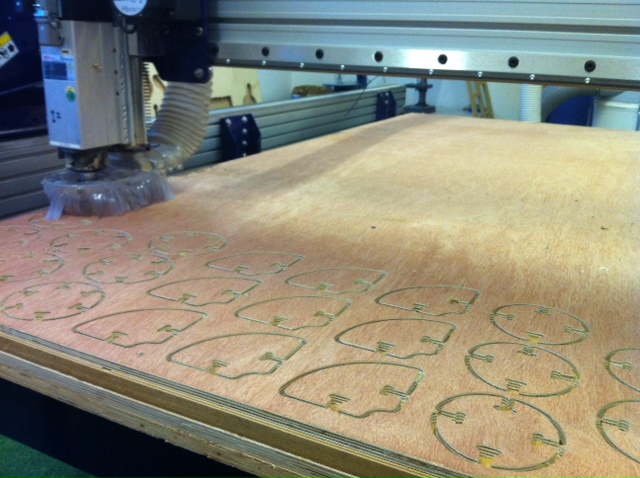
Kit Assembled:
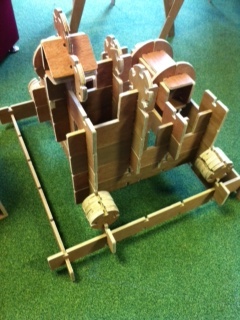
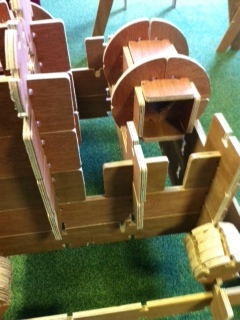
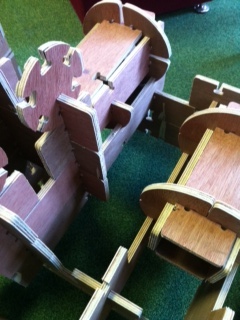
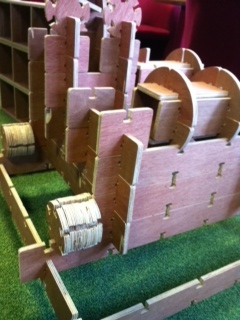
Files:
Drawings:
External Links: