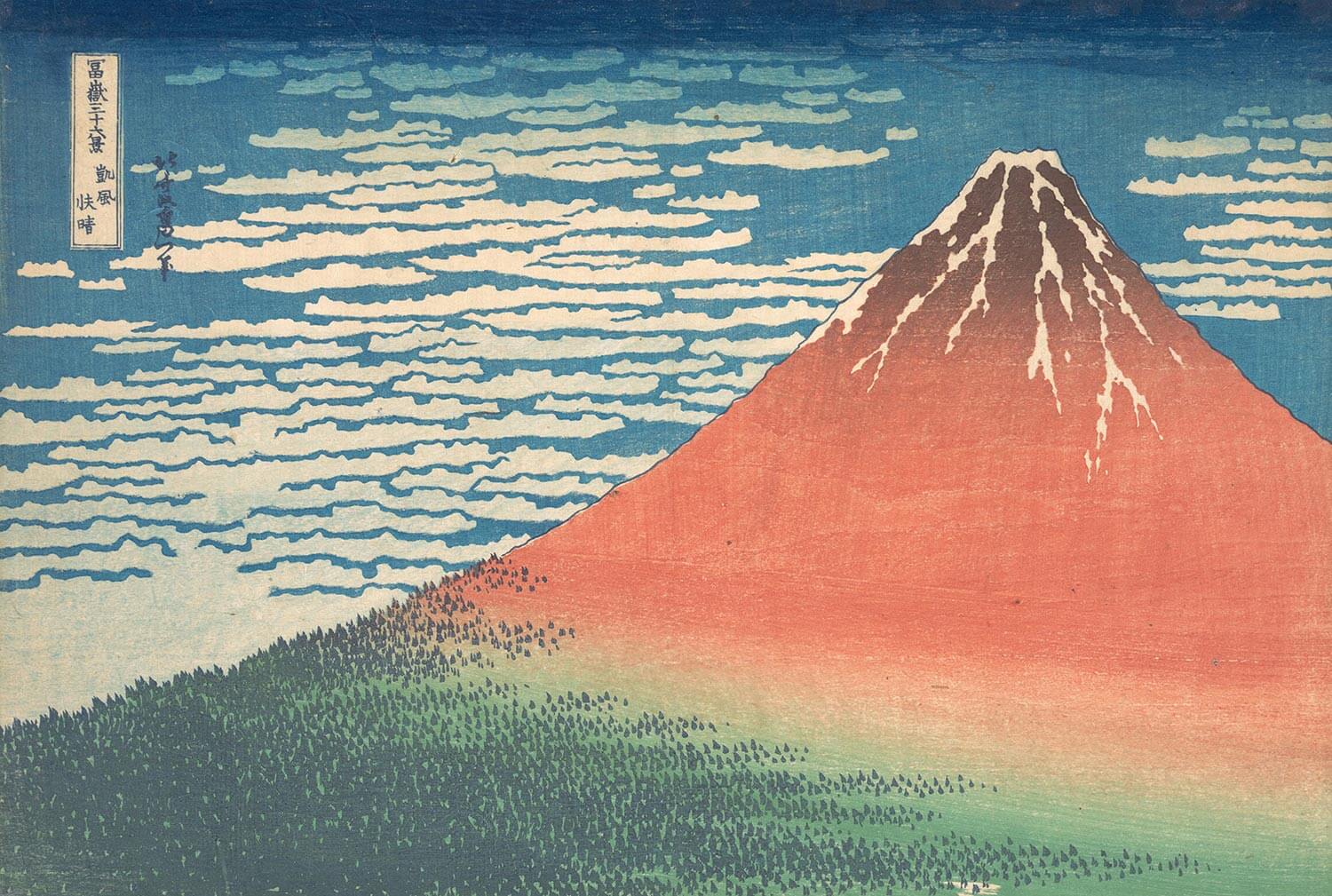
Week 19 - Project Development
Complete yourfinal project, tracking your progress:
what tasks have been completed, and what tasks remain?
what's working? what's not?
what questions need to be resolved?
what will happen when?
what have you learned?
I'm answering these questions after completing my final project. Its the final day of Fab Academy and I'm at a point of reflection rather than planning my next week.
What tasks have been completed, and what tasks remain?
The project is complete and fully functional. There are some small non-essential tweaks I'd like to make after Fab Academy:
- I will test some different types of varnish and identify the finish that minimises noise caused by the magnet dragging on the surface.
- I will add an On/Off switch and a reset button at the back, hidden from view.
- I will modify the PCB so that everything can be powered by the single 12v power supply. Currently I need to plug in the usb cable aswell.
- I will add proper USB and 5mm jack sockets at the back.
What worked?
The design - This worked well and I'm really proud of what I've made. I've never finished a project before (6 started!) and I really didn't feel confident in making it look good. My tutor Andrew helped me a lot with this. We looked at a Macbook together and he helped me de-construct a little what they had done. I'd never before noticed the chamfer at the bottom, the 4 little feet, the subtle line between lid and base when closed, the shape of the cut-outs or any other details like that. Andrew recommended to use wood filler on the 3d prints so that I could sand, prime and paint them and the whole model would have a single aesthetic. This proved to be a really good move and it came out looking awesome.
The skateboard tricks - I think you'd maybe need to be a skater to fully appreciate how accurately the skateboarder moves on some sections of the model. For example, he will turn 90 degree before sliding on a rail and the speed will reduce by about half during the slide, which is exactly what would happen in real life. On the ramps, he will slow down slightly as he goes up, then slide along a little bit and then there is small delay before coming back down. This is just what its like when you're skating a ramp. I think the motion is fun and accurate but probably a little nuanced to be appreciated unless you're really into skateboarding.
The electronics and the programming - I need to include this because I overcame so many problems. I've blown several motor drivers, 2 motors, 5 arduino nano clones, 1 esp32 chip, 1 potentiometer and probably some others components I forget. I've had a 4 month conveyer belt of confusing and stressful problems to overcome but I got there in the end. Everything is working with a reliable movement and I'm yet to start a fire. I'm happy with that!
Minimising the height of the model - My prototype was more than double the height of my final project. At this height, I really don't think it would have looked so good. I took the following measure to reduce height:
1 - Swapped 18mm MDF for 6mm Plywood - saved 12mm
2 - Added cut-outs for the stepper motors to slide up and down - saved 6mm
3 - Made a custom gantry plate so i could mount the stepper at a low height to the side of the moving gantry, as opposed to on top where they normally go - saved 30mm
4 - Modified the magnet holder so it would mount lower on the stepper motor. This meant I could use a hacksaw to cut half of the motor axle off - saved 14mm
5 - Replaced the 3mm plywood main surface with 1.5mm plywood. I gave it added strength with a hidden frame made from 6mm plywood - saved 1.5mm
6 - Used a bevelled edge to create the effect of a frame around the model. This was instead of a raised frame using 18mm plywood - saved 18mm
7 - Connected the aluminium rails to the gantry plates using epoxy glue. When I had previously used bolts, they were rubbing on the motor and so everything had to be raised 3mm to avoid the collision - saved 3mm
Total saving - 84.5 mm
Prototype height - 149.5 mm
Final build height - 65 mm
What didn't work?
The aluminium assembly - The aluminium rails were bolted inside and I had not expected I would need to remove the assembly from the base at any point. In fact I needed to remove it many times and it was a long and fiddly job. If I did this again, I would change the design so that it can be easily removed, adjusted and then put back into place.
The tension adjusters - These parts can be adjusted with an allen key but I can not access the bolt after the model is put together. It means I can not increase tension on the belt without taking everything apart. Even if I did take it apart and make an adjustment to the tension, I can not test the functionality without putting it all together again. I could add holes in the main casing and this would give me allen key access. I chose not to do this because I didn't want to ruin the clean aesthetic. If I made this again, I would use a different type of tensioner, that can be adjusted from beneath, rather than at the end. Then I would add holes in the base that would be out of view.
Noise - This was not a failure because I did make some big improvements to the noise, as listed above. It wasn't a big problem but I did notice that the noise became worse during the day that I had presented. I think maybe some varnish was rubbing off the surface but I can't be sure. I think I can spend some time on this and do some experiments where I would have several skateboarders, with each one having magnets treated differently. Some with a little varnish, some with a lot, some with none, some with a thin layer of felt or some other thin, slippery materials.
Documentation - This is not directly related to my project but I should write this somewhere. I find it really hard to remember to take photos, videos and make notes as I work. My problem is that I enjoy making things and solving problems so much, that I am completely absorbed and lose track of time. At times that I do stop and take notes, it breaks my concentration/flow and then I'm struggling to get back in the zone. I try and keep it in my mind to be documenting as I go but even just trying to remember to do that becomes a multi-tasking exercise which takes the fun and productivity out of it. This is not meant to be an excuse, just an explanation and I'd welcome any advise from others who've overcome this challenge. I want to get better at this because I'd love to give back to the maker communities that have helped me so much.
What questions need to be resolved?
How will I stop the grinding sound of the skateboard moving across the surface? I solved this problem but after an hour of use, a new noise started. I think it is because the varnish on the surface was being removed by the skateboard. I will do some experiments with different types of varnish/finish.
What will happen when?
After completing all Fab Academy assignments, I will do my experiments with varnish and attempt to complete the 4 tasks listed above.
What have you learned?
My goodness, where do i start!? I began to list all of the skills I had learned and then realised I was just creating a list of the Fab Academy syllabus. I'm sure you don't need me to put that list here, but its amazing to look back through the syllabus and remember just how much you have learnt in these past 5 months.
The most important thing I have learned is that I'm capable of completing a project and creating something beautiful that functions exactly as intended. I've learned that completing a project is a special moment and I should always try my best to finish something, even if it doesn't complete exactly as I had hoped. There will be a satisfaction and some additional lessons learned by completing those final steps. I've learned that no matter how many times things fail, if you are determined, you will find the solution to every problem eventually.
Back to homepage:
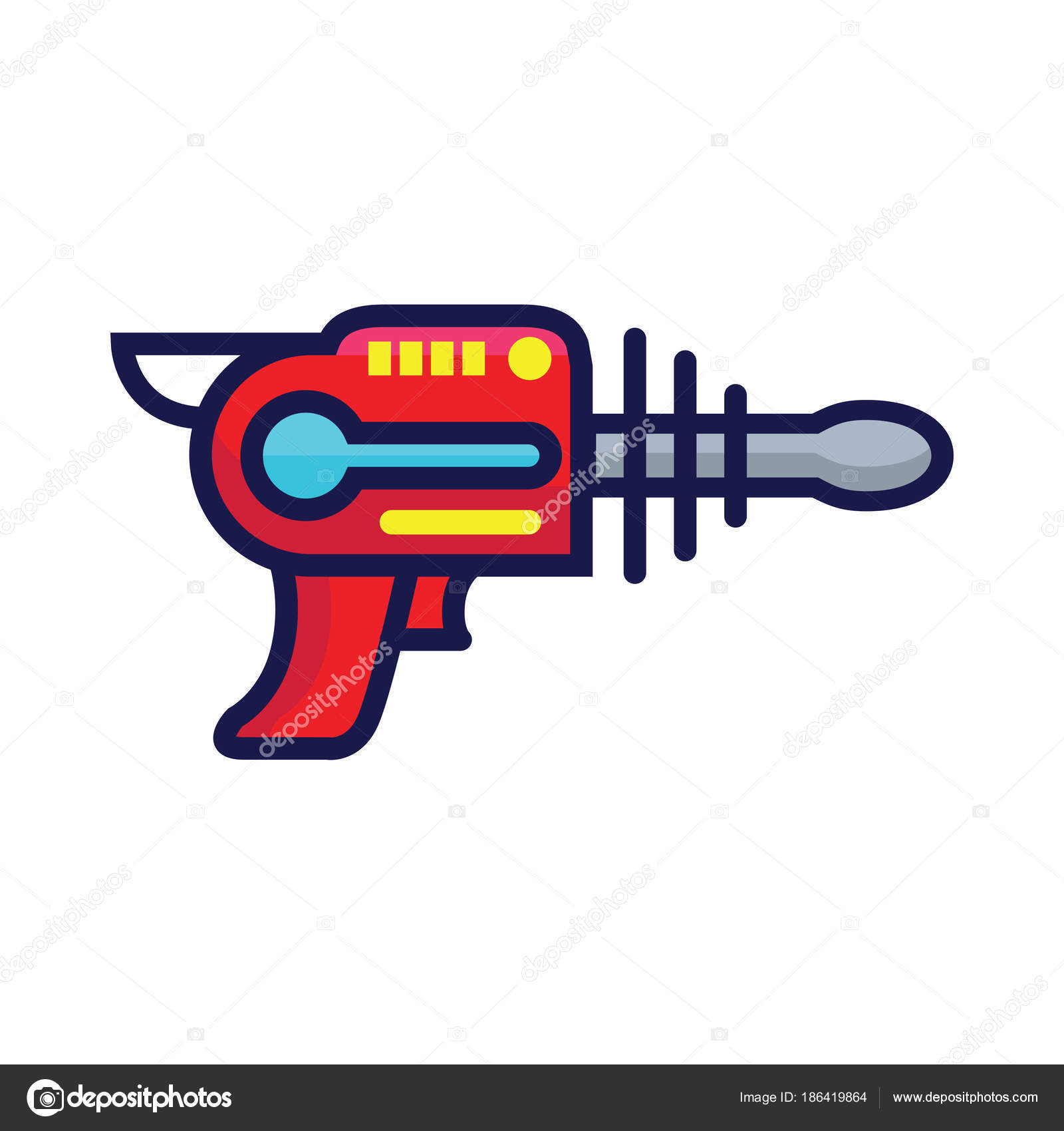