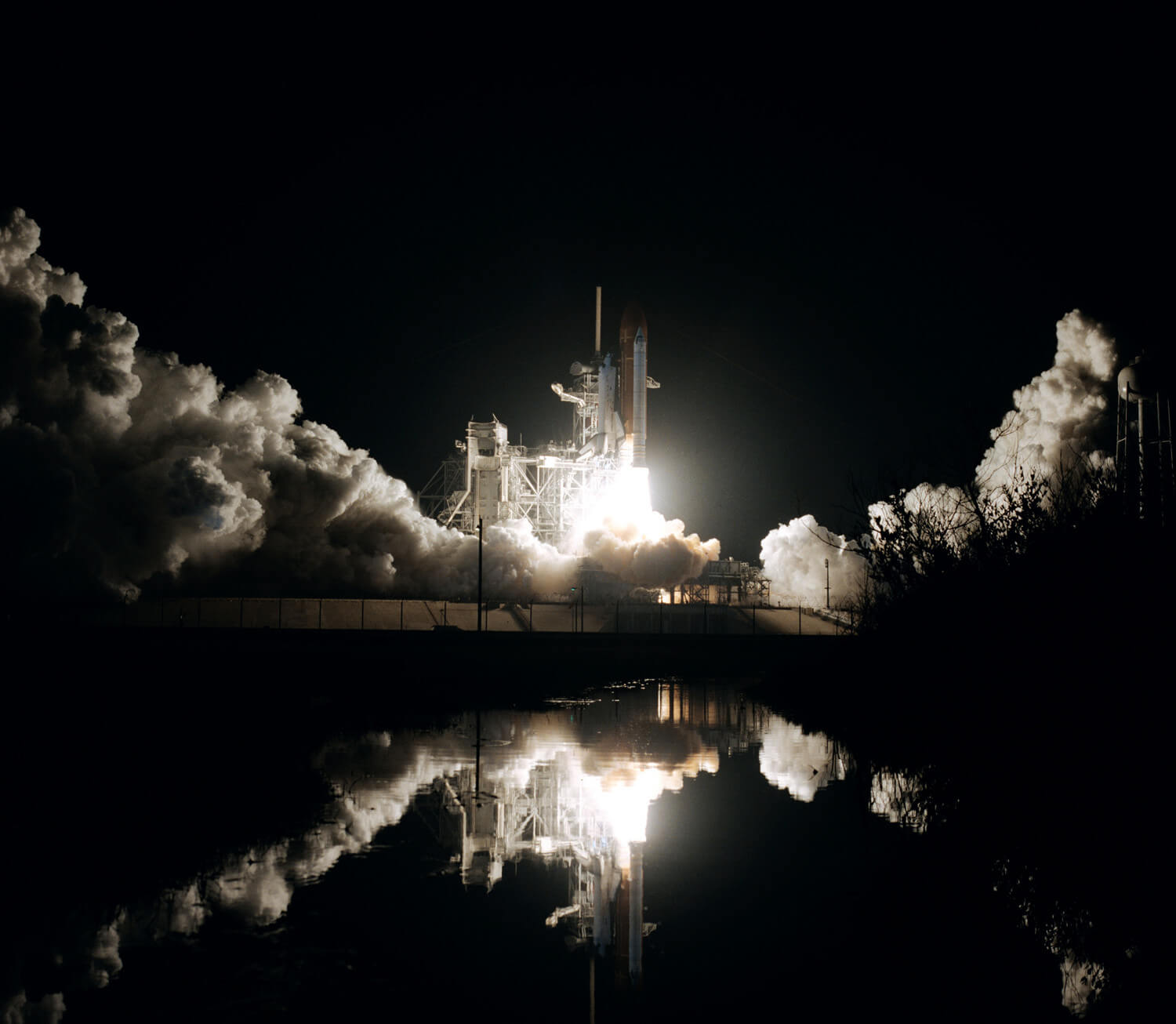
Week 17 - Applications & Implications
What does it do?
I've created an architectural model skatepark that comes to life. There is a 2 axis gantry beneath the model and this allows a set of magnets to be moved around the underneath of the model. An additional motor adds rotation, allowing the skateboard to twist as it executes tricks on the obstacles in the skate park.
Who's done what beforehand?
My dad was an architectural model maker and made many beautiful models. Still today, in spite of digital designs, many architectural models continue to get built.
One of my favourite projects from a previous year from the train model by Adrian Torres. It was simple but beautifully made:
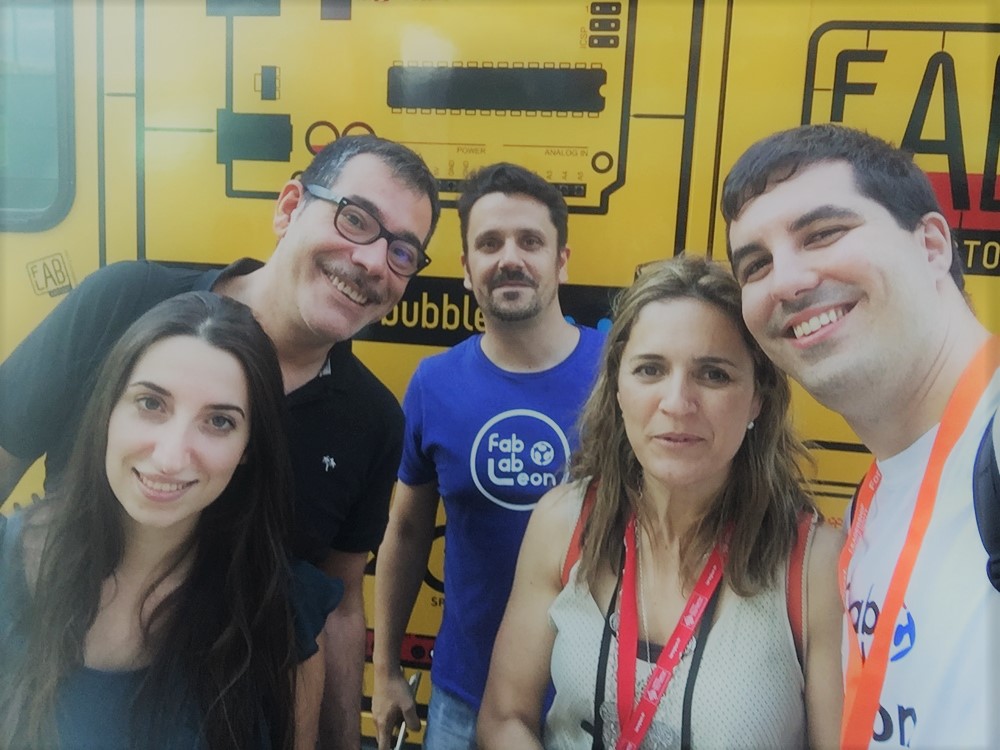
Neil pointed out an incredible project in Germany:
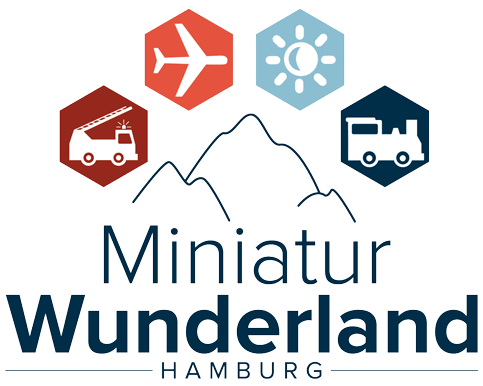
There are plenty of small model skateparks which are popular for use with fingerdecks which are a miniature skateboard toy.
What did you design? What parts and systems were made?
- A 2 axis gantry system, similar to a CNC machine, but in place of the router there is a stepper motor with a set of magnets. Although I'm sure its been done, I've never seen this design.
- My own custom library with a set of functions that allow my skateboard to move in any combination of straight and circular patterns across an X and Y axis. I can adjust speed, use acceleration and control the rotation of the skateboard.
- A plywood casing with an offset frame at the top and chamfer at the bottom. Its mounted on 4 feet and the lid can be easily removed to access the mechanics and electronics inside.
- A plywood base that has cut-outs for the stepper motors, ventilation holes and some fixing holes to attach the aluminium rails. The 2D sketches were made in Fusion 360 and laser cut.
- A set of contours to add some 3-dimensional shape to my model. These were designed in Fusion 360 and laser cut.
- A set of skatepark features and a custom motor plate to attach the main stepper motor to the gantry. These were designed in Fusion 360 and 3D printed.
What materials and components were used?
Material/Component: | Total spent: | Cost in final project: | Notes |
---|---|---|---|
PLA filament | £40 | £5 | Many failed prints while I tested designs for skatepark obstacles |
Plywood in thicknesses of 1.5mm (the main surface), 4mm (the contours), 6mm (main casing) | £70 | £20 | I have lots of plywood remaining for future projects |
Wood filler | £0 | £5 | Provided by lab but I have estimated cost |
Primer | £20 | £20 | |
Aerosol paint | £10 | £10 | |
Varnish | £8 | £1 | |
Glue (epoxy, super, PVA, hot) | £0 | £3 | Provided by lab but I have estimated cost |
Felt | £0 | £2 | Provided by lab but I have estimated cost |
Aluminium extrusion, size 2020 | £10 | £4 | |
Aluminium gantry plate x 3 | £24 | £24 | |
Nema 17 stepper motors 1.5A x 2 | £35 | £14 | Bought pack of 5 and used 2 |
Nema 17 stepper motor 1A | £21 | £7 | Bought pack of 3 and used 1 |
GT2 belt drive and pulley system | £15 | £15 | |
Scale model people/tree set 1:75 | £10 | £2 | |
Endstop switches x 2 | £7 | £2.80 | Bought pack of 5 and used 2 |
Magnets in sizes 5x1mm, 5x2mm, 5x4mm | £10 | £1 | Tried many sizes and shapes but in final project, used just a small qty |
Wires and JST connectors | £10 | £0.50 | Bought a complete set for future projects |
ESP32 chip | £12 | £3 | Bought 4 and used 1 |
Custom fab board | £0 | £3 | Provided by lab but I have estimated cost |
Potentiometer | £0 | £0.50 | Donated by friend but I have estimated cost |
Toggle switch x 2 | £5 | £1 | Used 2 from a pack of 10 |
Stealth chop drivers x 3 | £20 | £15 | Used 3 from a pack of 4 |
Untitled | |||
TOTAL: | £327 | £158.80 |
Where did they come from?
Most consumables were provided by the workshop at Plus X. Aluminium extrusion, gantry and belt drive parts were from Ooznest in the UK. Plywood from a local company called Covers Timber. Everything else from Amazon.
How much did they cost?
I spent £327 in total but this includes a lot of materials and components that will be used for future projects. If I know the parts I need will be useful in the future, and assuming they are not perishable or likely to depreciate, I'm always happier buying a larger quantity to get a better unit price. The actual cost of the parts and materials in my final project was £158.80.
What processes were used?
- 2D and 3D design in Fusion 360
- 3D printing on our Prusa i3 models
- Laser cutting on our Trotec
- PCB milling on our Roland SRM-20
- Surface mount soldering
- Woodworking tools - Band saw, scroll saw, disc sander, rail saw, router
- Finishing - Wood filler, sanding, priming, painting
What questions were answered?
Can you create a natural movement that looks like a skateboarder more than it looks like a machine?
Yes you can. Its not perfect but I think I've created a fun and reasonably natural motion. Key factors that helped this were using acceleration to vary the speed, going faster after leaving a ramp and slowing down as you enter one.
What is the optimal size and shape of magnet?
The magnets should be round. Using rectangular magnets created problems where the magnets were wobbling about, unsure which part of the rectangular magnet it was most attracted to. Using larger magnets gives a stronger connection which is good for sending the skateboard upwards on the Z axis, for example if it goes up a ramp. The downside of the larger magnets is that the skateboard needs to be bigger which in turn forces the entire model larger. It reduces the number of obstacles you can fit into your model without making it prohibitively large. I found 5mm to be the optimal size.
What distance do you require between the skateboard magnets and the magnets underneath the model?
I used 5mm x 5mm round magnets underneath the model and 5mm x 3mm round magnets in the skateboard. (magnets continue to gain strength while you increase their depth up to the point where their depth equals their width. After this point, an increase in depth has an insignificant impact).
With my magnets as above, I could control the movement of the skateboard with rotation with a gap of up to 11mm between skateboard magnets and motor magnets. If I didn't need to use rotation, I could maintain control of the skateboard with a gap of up to 16mm.
What can you do to minimise noise?
Noise was a big problem on this model. So many different parts were making more noise than I had expected. It had the potential to ruin the project but I took the following measures which each made a significant difference:
1 - I swapped my regular motor drivers for stealth chop drivers made by Trinamic. This made a huge difference.
2 - I reduced tension on the timing belt, setting it to the slackest it could be without skipping steps.
3 - I raised the stepper motor pulleys by 0.5mm to ensure they would not rub against the stepper motor during operation.
4 - I used 5mm felt feet to help reduce vibration.
5 - I added a layer of varnish to reduce friction where the magnets drag along the top surface.
6 - I played around with different speeds and found the least noisy speed to be where the motor delay between steps was between 40 and 60 microseconds.
7 - I avoided sudden movements, making sure to decelerate and then accelerate if changing direction
Do I have what it takes to be a successful inventor and maker?
Yes I do :)
What worked?
The design - This worked well and I'm really proud of what I've made. I've never finished a project before (6 started!) and I really didn't feel confident in making it look good. My tutor Andrew helped me a lot with this. We looked at a Macbook together and he helped me de-construct a little what they had done. I'd never before noticed the chamfer at the bottom, the 4 little feet, the subtle line between lid and base when closed, the shape of the cut-outs or any other details like that. Andrew recommended to use wood filler on the 3d prints so that I could sand, prime and paint them and the whole model would have a single aesthetic. This proved to be a really good move and it came out looking awesome.
The skateboard tricks - I think you'd maybe need to be a skater to fully appreciate how accurately the skateboarder moves on some sections of the model. For example, he will turn 90 degree before sliding on a rail and the speed will reduce by about half during the slide, which is exactly what would happen in real life. On the ramps, he will slow down slightly as he goes up, then slide along a little bit and then there is small delay before coming back down. This is just what its like when you're skating a ramp. I think the motion is fun and accurate but probably a little nuanced to be appreciated unless you're really into skateboarding.
The electronics and the programming - I need to include this because I overcame so many problems. I've blown several motor drivers, 2 motors, 5 arduino nano clones, 1 esp32 chip, 1 potentiometer and probably some others components I forget. I've had a 4 month conveyer belt of confusing and stressful problems to overcome but I got there in the end. Everything is working with a reliable movement and I'm yet to start a fire. I'm happy with that!
Minimising the height of the model - My prototype was more than double the height of my final project. At this height, I really don't think it would have looked so good. I took the following measure to reduce height:
1 - Swapped 18mm MDF for 6mm Plywood - saved 12mm
2 - Added cut-outs for the stepper motors to slide up and down - saved 6mm
3 - Made a custom gantry plate so i could mount the stepper at a low height to the side of the moving gantry, as opposed to on top where they normally go - saved 30mm
4 - Modified the magnet holder so it would mount lower on the stepper motor. This meant I could use a hacksaw to cut half of the motor axle off - saved 14mm
5 - Replaced the 3mm plywood main surface with 1.5mm plywood. I gave it added strength with a hidden frame made from 6mm plywood - saved 1.5mm
6 - Used a bevelled edge to create the effect of a frame around the model. This was instead of a raised frame using 18mm plywood - saved 18mm
7 - Connected the aluminium rails to the gantry plates using epoxy glue. When I had previously used bolts, they were rubbing on the motor and so everything had to be raised 3mm to avoid the collision - saved 3mm
Total saving - 84.5 mm
Prototype height - 149.5 mm
Final build height - 65 mm
What didn't work?
The aluminium assembly - The aluminium rails were bolted inside and I had not expected I would need to remove the assembly from the base at any point. In fact I needed to remove it many times and it was a long and fiddly job. If I did this again, I would change the design so that it can be easily removed, adjusted and then put back into place.
The tension adjusters - These parts can be adjusted with an allen key but I can not access the bolt after the model is put together. It means I can not increase tension on the belt without taking everything apart. Even if I did take it apart and make an adjustment to the tension, I can not test the functionality without putting it all together again. I could add holes in the main casing and this would give me allen key access. I chose not to do this because I didn't want to ruin the clean aesthetic. If I made this again, I would use a different type of tensioner, that can be adjusted from beneath, rather than at the end. Then I would add holes in the base that would be out of view.
Noise - This was not a failure because I did make some big improvements to the noise, as listed above. It wasn't a big problem but I did notice that the noise became worse during the day that I had presented. I think maybe some varnish was rubbing off the surface but I can't be sure. I think I can spend some time on this and do some experiments where I would have several skateboarders, with each one having magnets treated differently. Some with a little varnish, some with a lot, some with none, some with a thin layer of felt or some other thin, slippery materials.
Documentation - This is not directly related to my project but I should write this somewhere. I find it really hard to remember to take photos, videos and make notes as I work. My problem is that I enjoy making things and solving problems so much, that I am completely absorbed and lose track of time. At times that I do stop and take notes, it breaks my concentration/flow and then I'm struggling to get back in the zone. I try and keep it in my mind to be documenting as I go but even just trying to remember to do that becomes a multi-tasking exercise which takes the fun and productivity out of it. This is not meant to be an excuse, just an explanation and I'd welcome any advise from others who've overcome this challenge. I want to get better at this because I'd love to give back to the maker communities that have helped me so much.
How was it evaluated?
Neil clapped when he saw it working. I'm pretty sure that's kind of a big deal!
I had 2 clear goals when I started Fab Academy:
- Learn as much as possible
- Complete my first project
With that in mind, I'd say that this project was a roaring success. It was complicated enough that it was motivating and forced me to fail and learn more than I could have imagined. However, it was not so complicated that I didn't finish it. Prior to Fab Academy I had started 6 projects and completed none. Now I have completed something that looks more beautiful than I ever believed I could make. Its been a great experience and has been a big boost to my confidence in what is still a very new field for me. So with that in mind, I consider this project a great success.
Back to homepage:
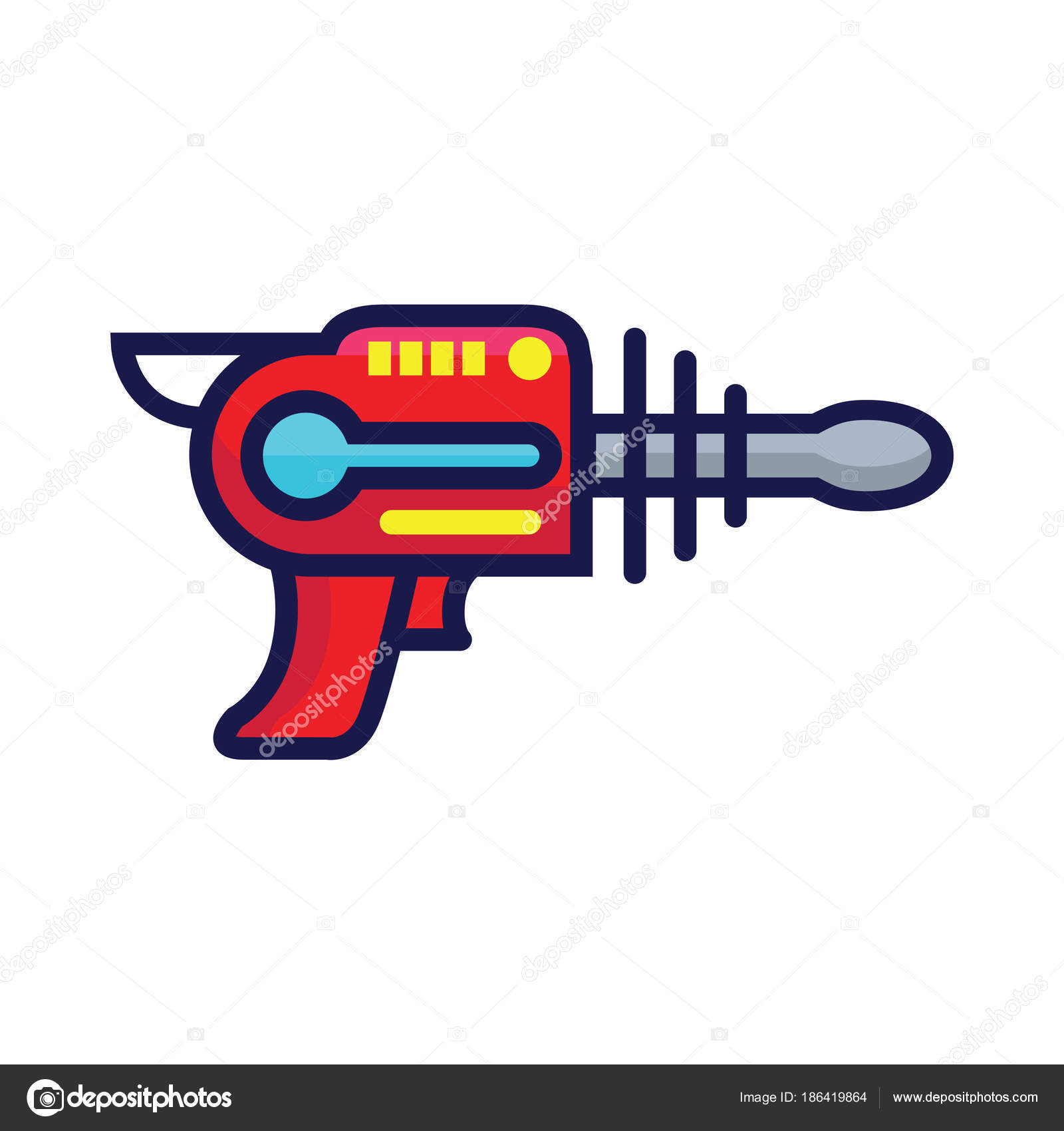