Objectives of the week
- review the safety data sheets for each of your molding and casting materials, then make and compare test casts with each of them
- design a mold around the stock and tooling that you'll be using, mill it (rough cut + (at least) three-axis finish cut), and use it to cast parts
- Understanding of molding and casting process.
- Study of different material like silicon rubber,hydrostone,epoxy resin,instamold.
- Molding process using SRM-20 machine.
1. Group assignment
2. Individual assignment
Learning outcome:
In group assignment task is to read material safety datasheet.In Vigyan Ashram we have different material like Hydrostone,Instamold,Epoxy,machine wax,Moldsil for molding and casting.So we decided to study all materials in group and everyone will share their study material with other.Its not possible to study all material by one person.I got instamold for study.
On Thursday morning, our week mentor give us brief idea about this week.During this discussion she actually introduce us about different material ,What is molding and casting,Desig,installation procedure and the process as well.After this brainstrorming she asked to do our group assignment work for that i need to read the datasheet of silicone rubber and thentry to explain others mates as well.So i start reading the things about silicone rubber which i mentioned below.
What is silicone rubber?: Silicon rubber is a thrmoset process that actually combine two compound together and later you need to heat cured in the mould using different catalyst options which i mentioned below.After doing all this exersize it will result into liquid silicone rubber.Now to undestand in detaled about the silicone rubber i finally go through the data sheet Moldsil-15 PLUS i.e.High Performance Silicone Rubber for Long Lasting Flexible Molds )
Moldsil-15 PLUS(High Performance Silicone Rubber for Long Lasting Flexible Molds )
Introduction:Moldsil-15 PLUS is a premium grade condensation curing type Silicone RTV, recommended for mold making applications. This is a flowable grade, having high mechanical strength and cures with various catalyst options (depending on the application requirements) at room temperature to a flexible elastomer, well suited for detailed and exact reproduction of artifacts, figures, architectural items and similar objects. Moldsil-15 PLUS will reproduce the finest detail of the master and is suitable for a variety of art related and industrial applications such as mold making for reproducing prototypes, furniture, architectural items and sculptures.
Features:
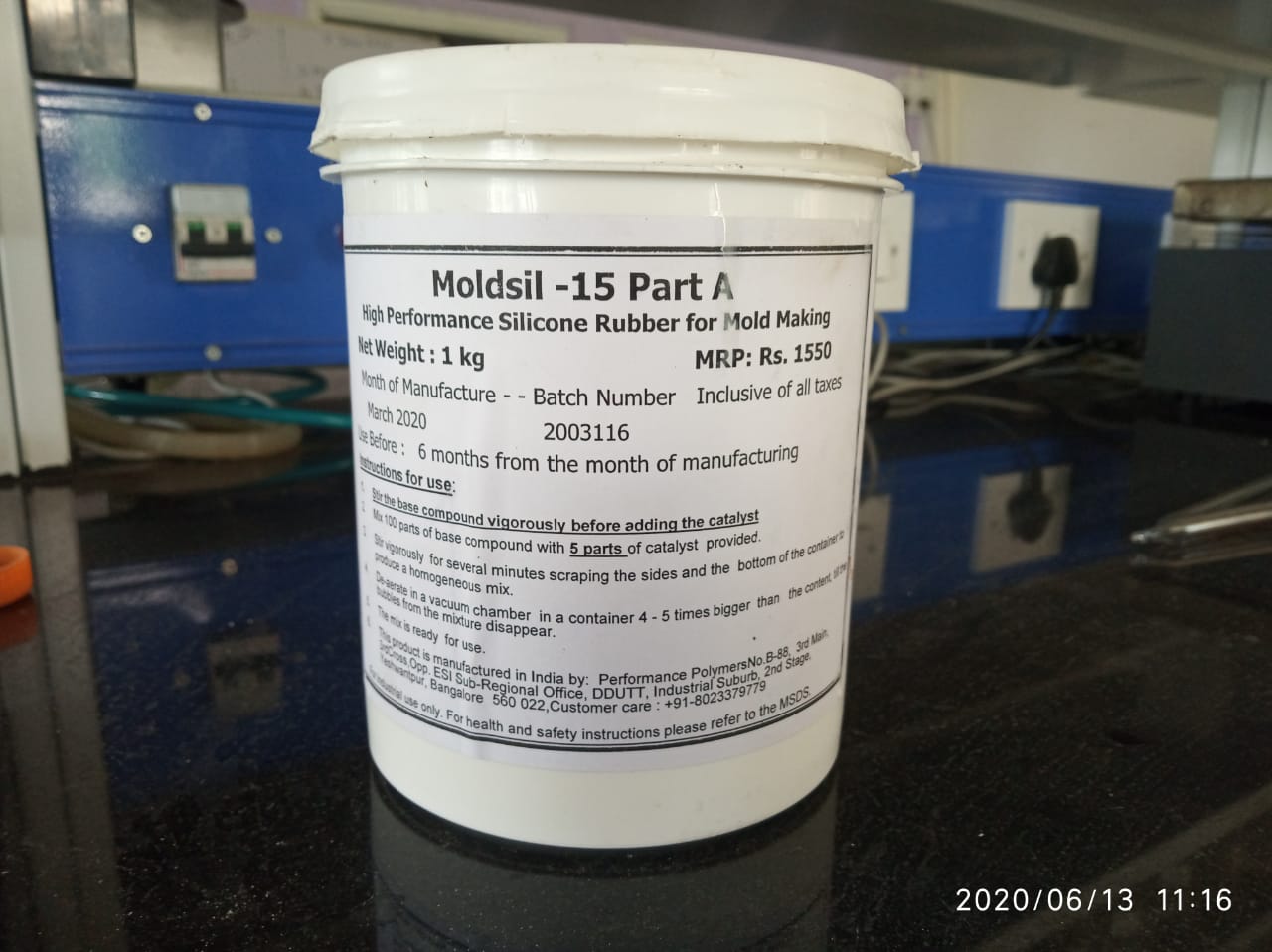
CATALYST OPTIONS:There are three types of catalyst options.
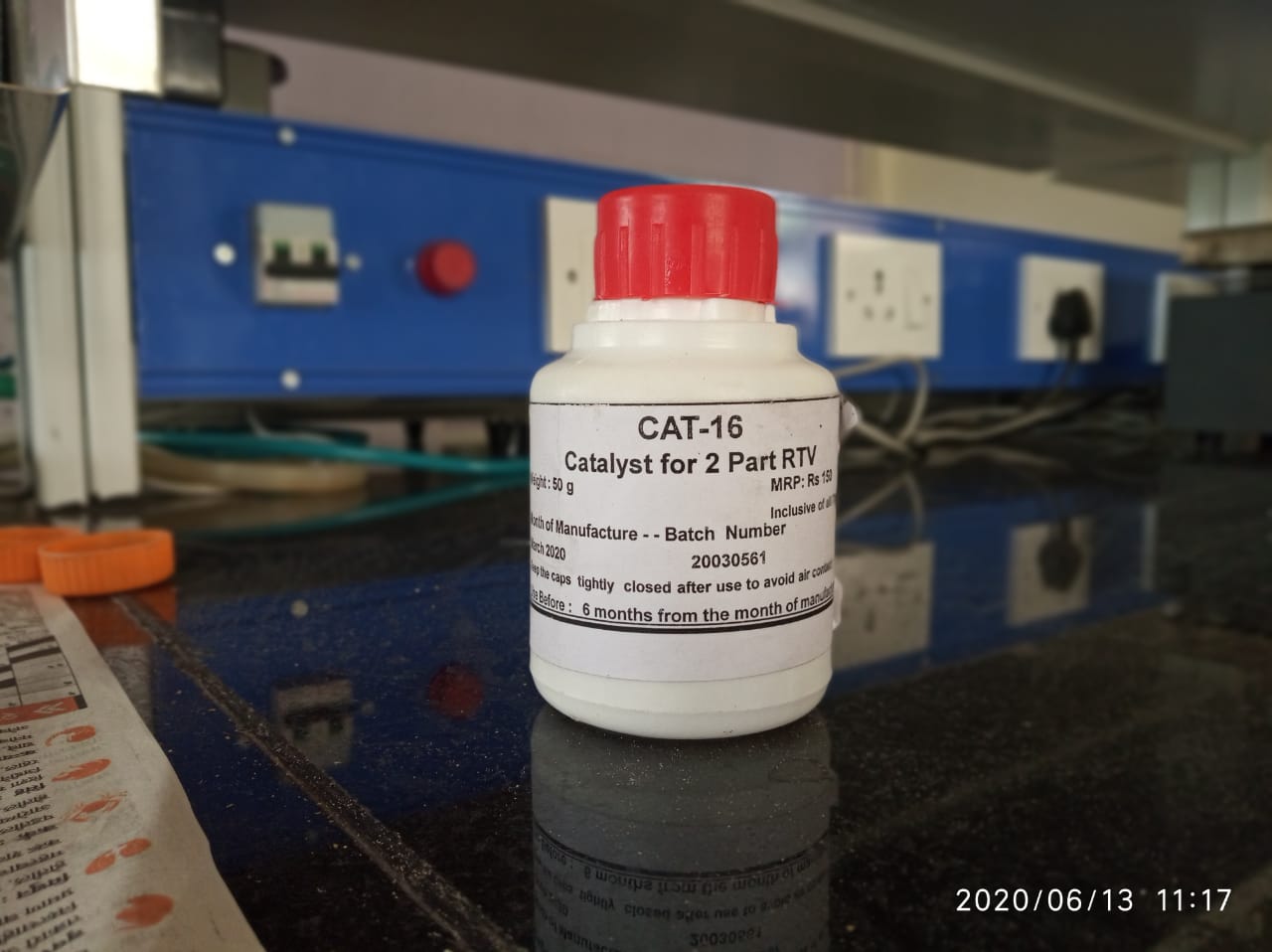
METHOD OF USE
How to mix silicone rubber?
HANDLING PRECAUTIONS AND SAFETY:Moldsil-15 PLUS contains constituents that have been found to be safe. Hence special handing precautions except general industrial hygiene need to be followed. Catalysts (CAT-24, CAT-16 and CAT-04) contain organo-tin compounds and are flammable and might cause irritation upon contact with eyes and skin. Adequate protective measures are recommended. Refer to Material Safety Data Sheet (MSDS) for safe use of the product
Procedure to used Moldsil and catalyst
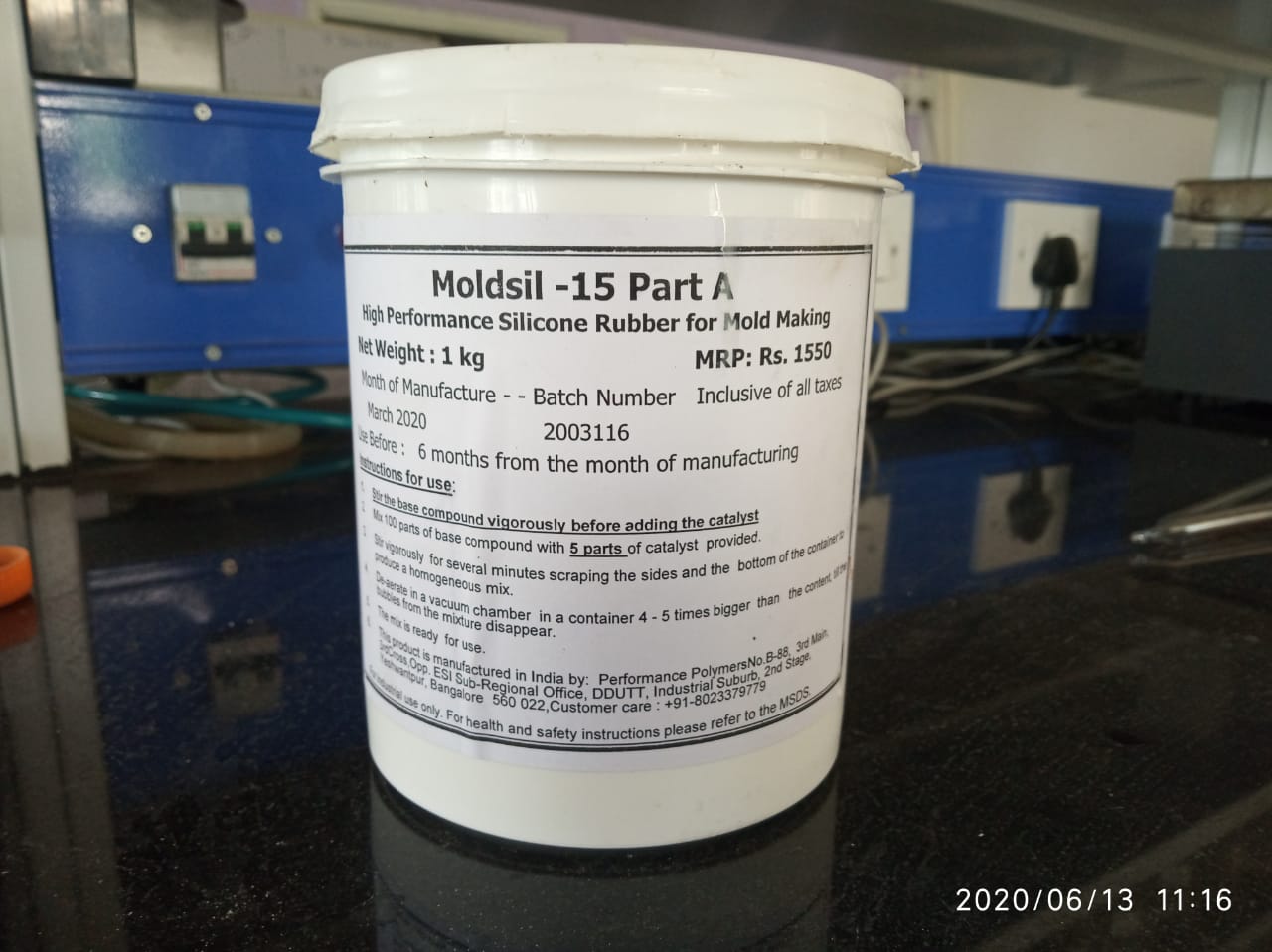
Here is Moldsil 15 part A which i am going to used.
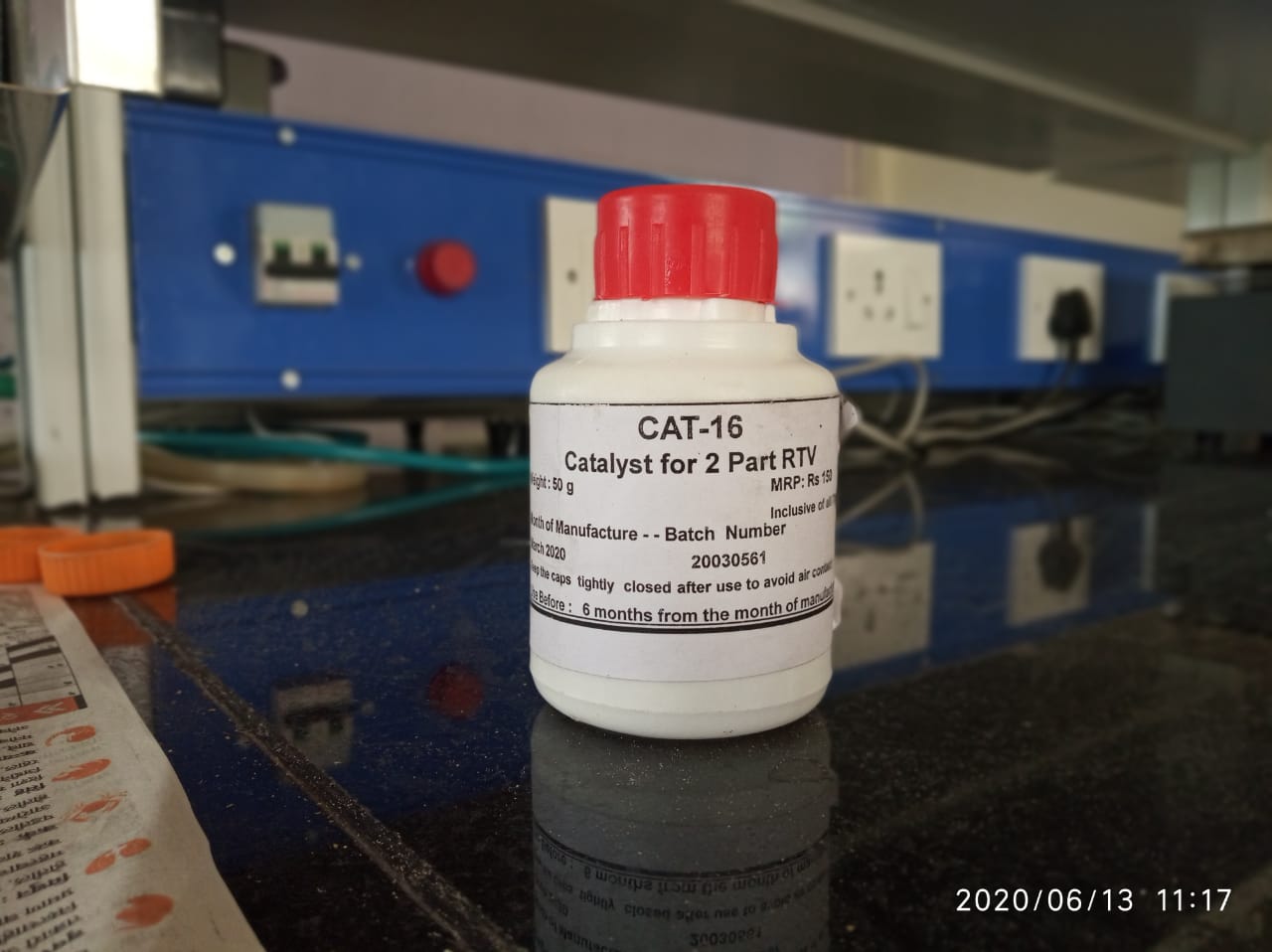
This is Catalyst 16 part B which is being used as hardner.
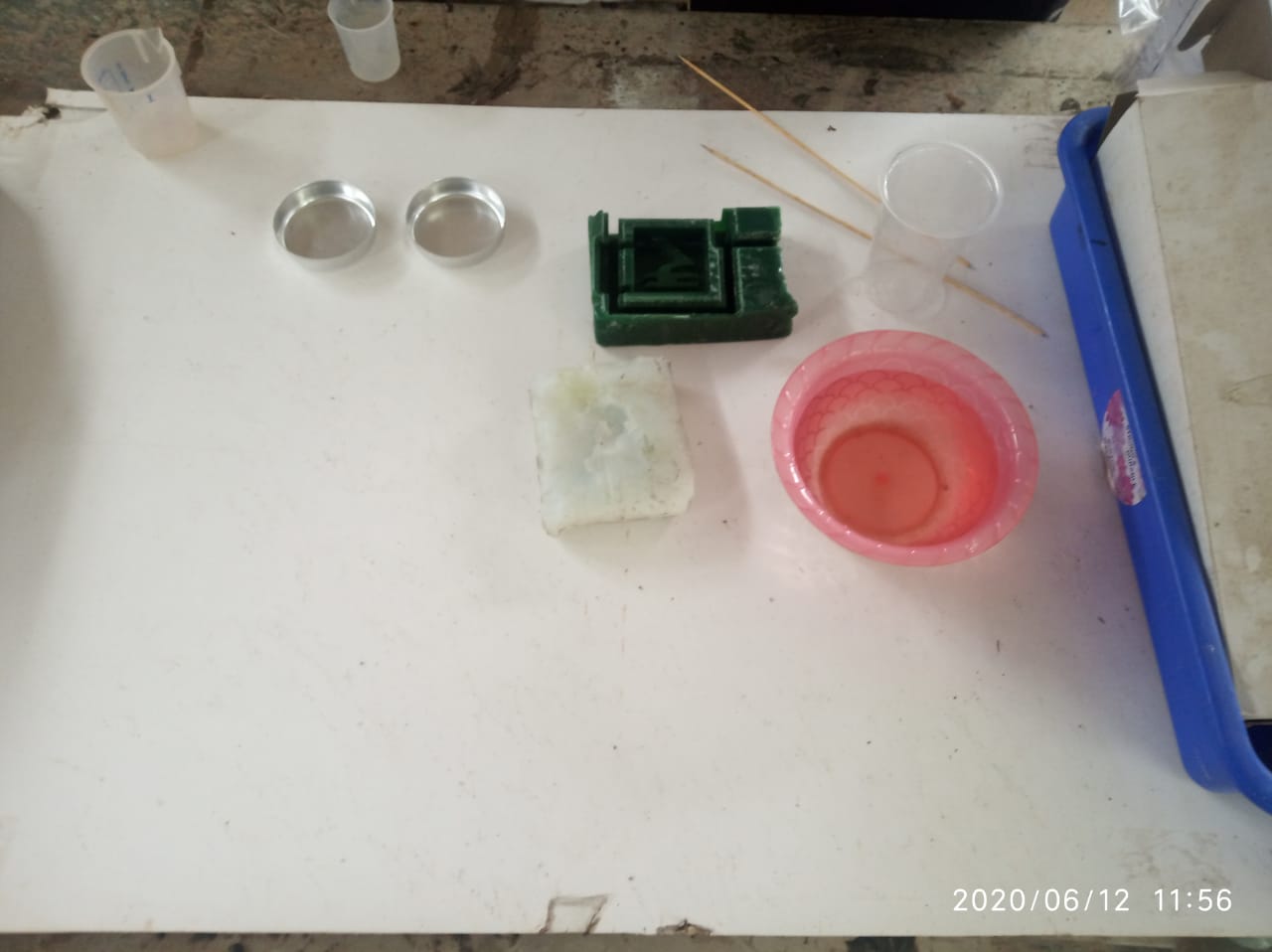
Then i put all necessary things on one platform like mold,silicon rubber,hardner,cups,water,pot etc.
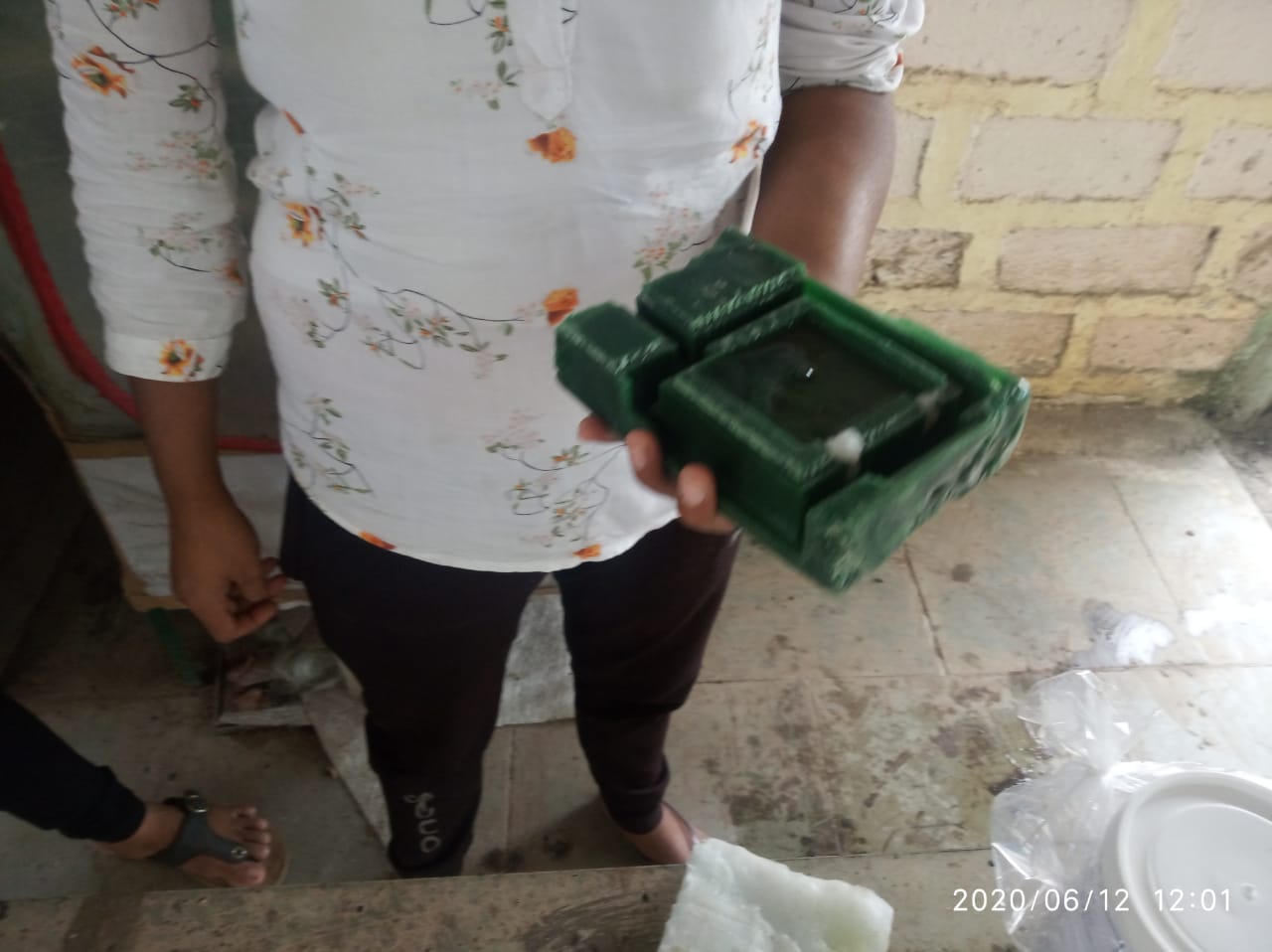
So first i put water into the mold and measure it as well which is 50gm(100%)
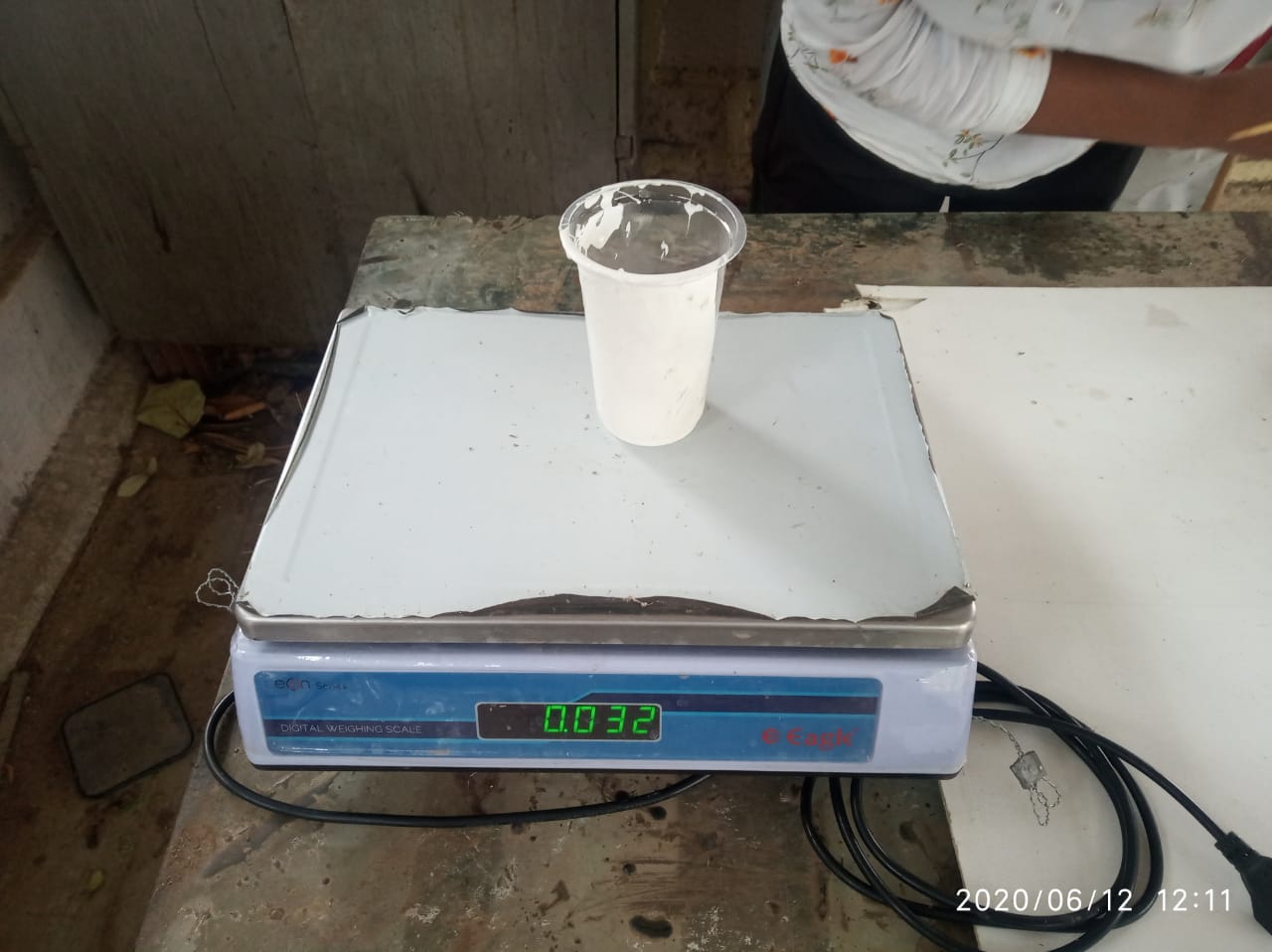
Then take 60% of 50gm moldsil first into the glass.
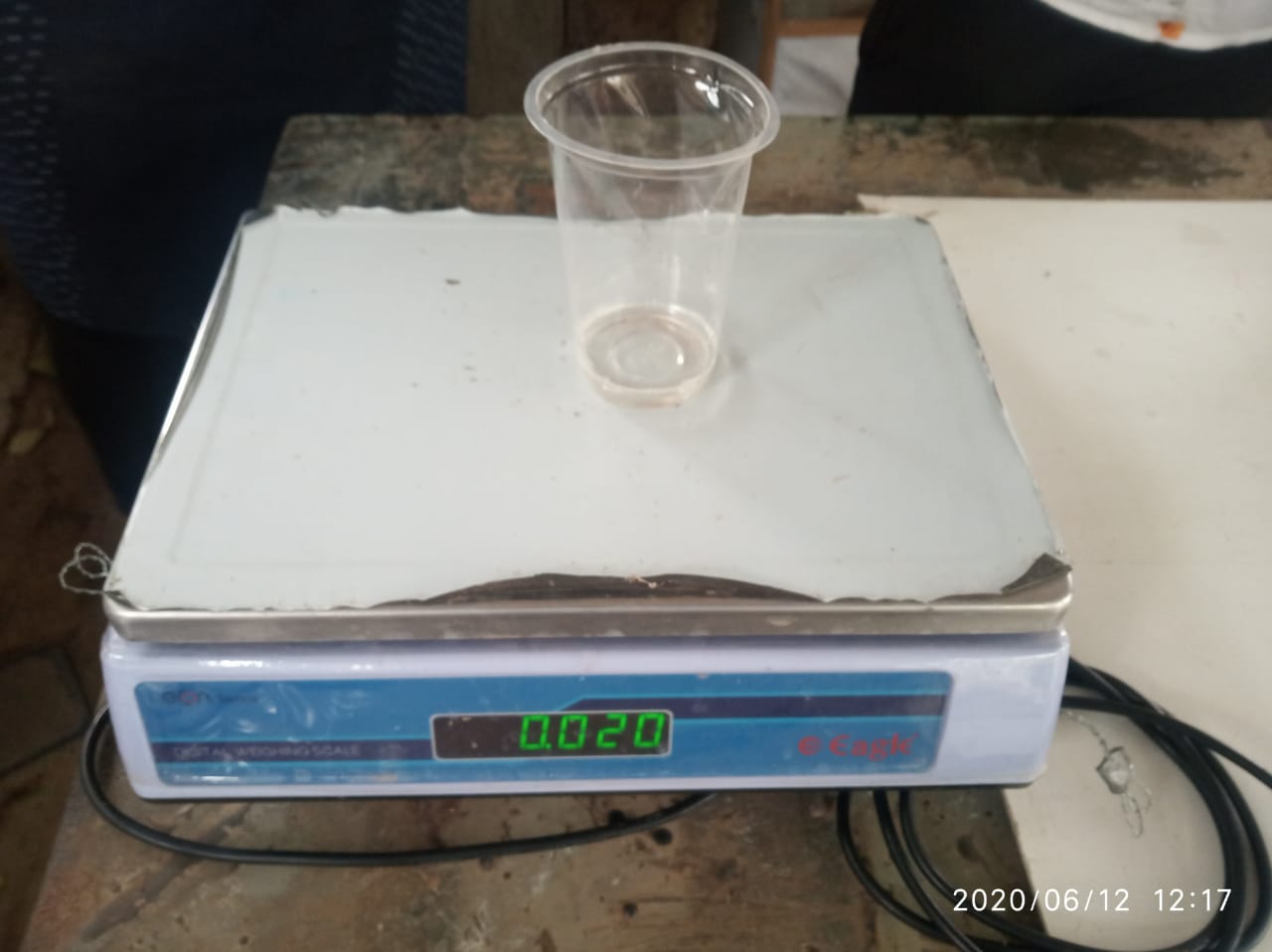
Immegiately take 40 % of 50 gm catalyst as herdner and put them into moldsil and sturred it fast.
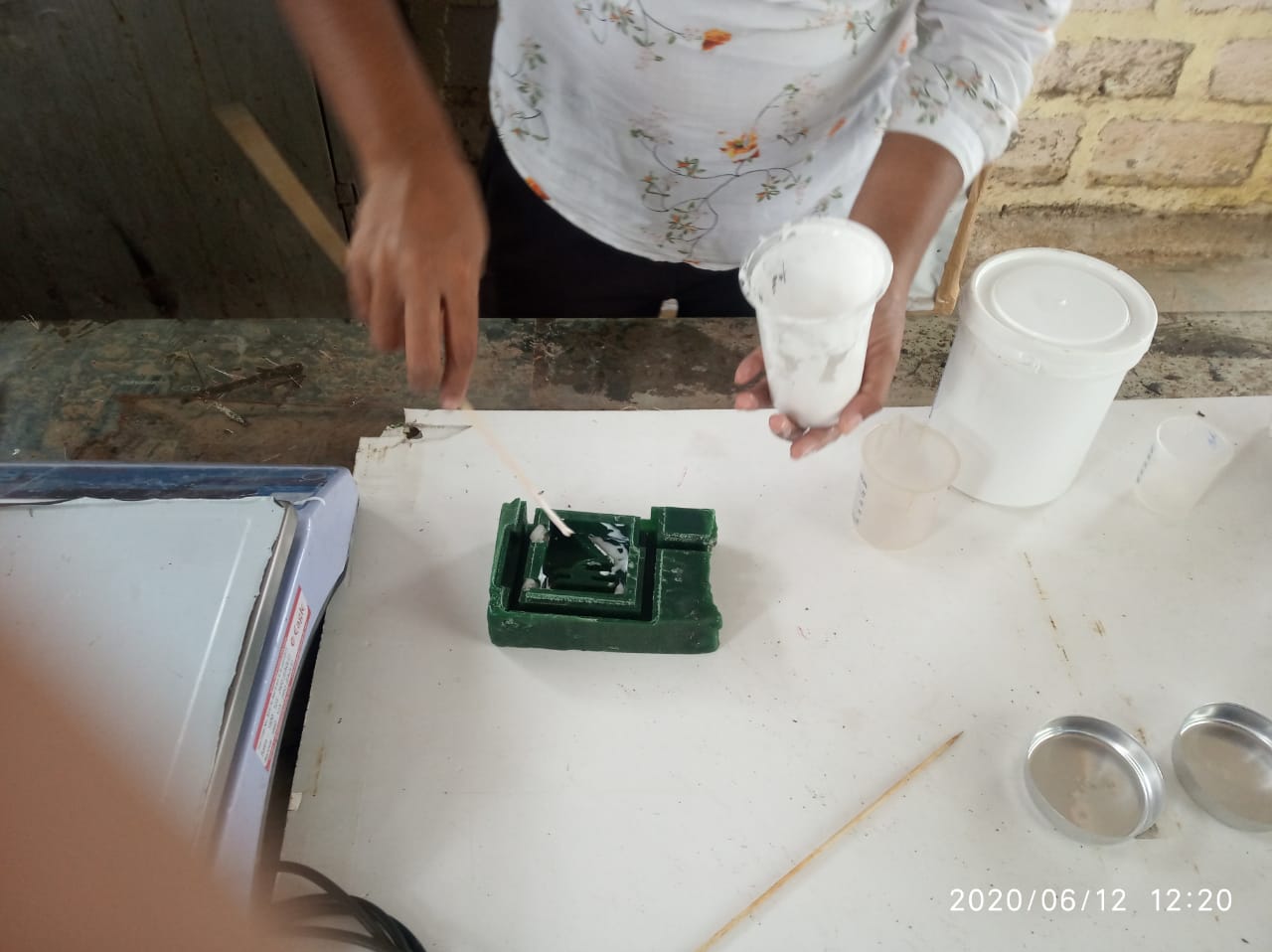
Apply the mixture first into corners
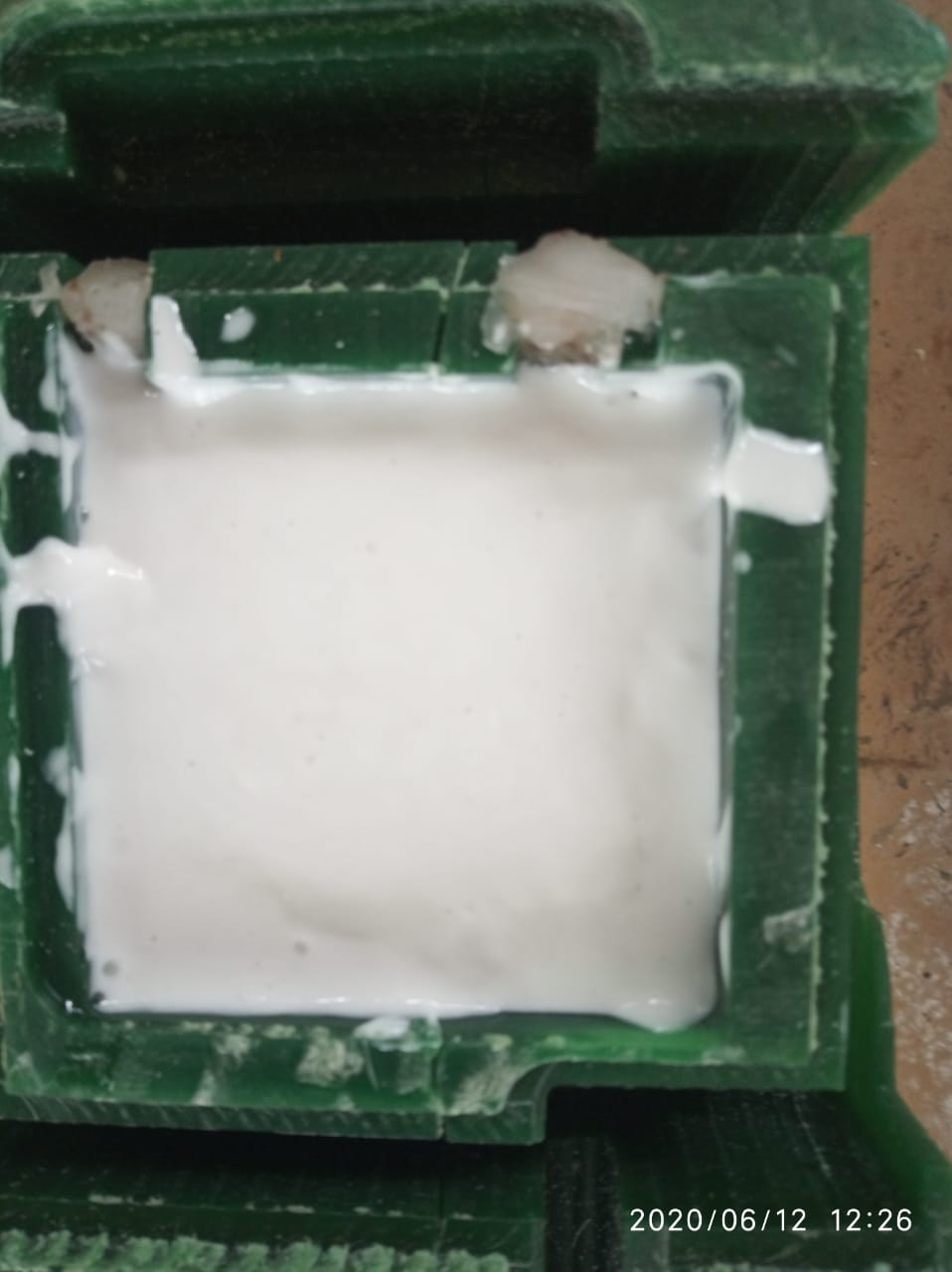
And finally put all into required area of mold.
Removing few bubbles using sterrer.
Instamold:
It is a Casting Compound,Non-Toxic & Safe to use it can be use for Craft or fine art.It can be used for Preserving,Body Casting,Historical Reproductions,Antique Molding,Repair Hobby Castings,Jewelry Making,Ice Sculptures
InstaMold allows for the most perfect reproductions of all 3 dimensional objects and shapes in a matter of minutes. The clever temporary mold making compound is activated by water. Flexible InstaMold makes an exact replica including the finest of detail. InstaMold is completely harmless to use for body casting and the material will not adhere to the originals you are casting. Once you have your completed your mold you can then make numerous copies using Art Plaster, Permastone, resin, wax or other casting compounds.
Thick Strong Mix:
Mixing Proportions: 1 part InstaMold : 2 Parts Water
Characteristics: Greater Volume of Mix Slow Setting Average Retention of shape & size Withstands average handling retains fine detail
Setting time at 70F: 4 - 6 Minutes
Medium Average Strong Mix:
Mixing Proportions: 1 part InstaMold : 3 Parts Water
Characteristics:Greatest Volume of Mix Slowest Setting Less accurate retention of shape Should be handled more carefully retains fine detail.
Setting time at 70F:8 -12 Minutes
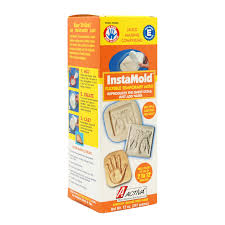
♦ Hydro-stone
Hydro stone is an excellent product for manufacturing solid cast architectural, art novelty and statuary products it is extremely hard, has high compressive strength. It has high water absorption resistance while giving extremely fine detail duplication.
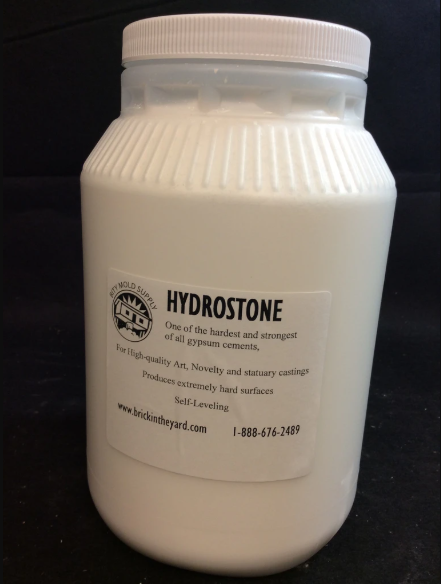
PHYSICAL PROPERTIES
1) Normal Consistency - 32 lbs. water/100 lbs. product (15 kg water/45 kg product)
2) Hand Mix Vicat Set, Target - 19 - 25 minutes
3) Compressive Strength, One Hour After Set - 4000 psi (27.6 MPa)
4) Compressive Strength, Dry - 10,000 psi (68.9 MPa)
5) Density, Wet - 119 lbs./cu. ft. (1906 kg/m3)
6) Density, Dry - 108 lbs./cu. ft. (1730 kg/m3)
7) % Maximum Expansion - 0.24%
MIXING INSTRUCTIONS
MIX PREPARATION :- Use potable water at temperatures between 70 °F (21 °C) and 100 °F (38 °C). Because variations in slurry ( Hydro-Stone Gypsum Cement and water mixture) temperature produce variations in set time, it is important to keep both the Hydro-Stone Gypsum Cement and water in a stable temperature environment prior to use. The higher the temperature of the slurry, the shorter the set time. Conversely, the lower the temperature of the slurry, the longer the set time. Weigh both the Hydro-Stone Gypsum Cement and the water prior to use for each mix. The water-to-Hydro-Stone Gypsum Cement ratio is critical because it governs the strength and the density of the final cast.
SOAKING :- Sift or strew USG Hydro-Stone Gypsum Cement into the water slowly and evenly. Do not drop large amounts of Hydro-Stone Gypsum Cement directly into the water as proper soaking of the Hydro-Stone Gypsum Cement may not occur. USG Hydro-Stone Gypsum Cement should be fully dispersed in the water prior to mixing. Small batches require less soaking time than large batches. See USG IG503 Plaster Mixing Procedures for specific soaking instructions.
MIXING :- Mixing Hydro-Stone Gypsum Cement slurry is one of the most important steps in producing USG Hydro-Stone Gypsum Cement casts with maximum strength, absorption, hardness and other important properties. Mechanically mixed slurries develop uniform casts with optimal strengths. USG Hydro-Stone Gypsum Cement can be mechanically mixed through both batch and continuous processes. Proper blade and bucket dimensions are important for obtaining the best batch mix (see USG IG503 Plaster Mixing Procedures for details). Longer mixing times result in higher mold strength and shorter set times.
POURING
To prevent air entrainment and provide a uniform, smooth surface, careful pouring of USG Hydro- Stone Gypsum Cement slurry is necessary. Agitation/vibration of the filled mold is a further step used to prevent air at or near the mold surface. Whenever possible, USG Hydro-Stone Gypsum Cement slurry should be poured carefully in the deepest area so that the slurry flows evenly across the surface of the case mold. Pouring a large amount of slurry directly on the face of the case mold may result in slight densification of the USG Hydro-Stone Gypsum Cement mold at the point where it strikes the surface of the case. This produces a hard spot, giving uneven absorption.
DRYING
All casts should be dried as quickly as is safely possible after manufacture so that maximum physical properties can develop. Dry to a constant weight. The best drying rooms or ovens provide 1) uniform and rapid circulation (minimum of 15-30 fps (4.6-9.1 mps)) of air with no “dead spots” having little or no air movement, 2) equal temperatures throughout the entire area, and 3) provisions for exhausting a portion of the air while replacing it with fresh air. High humidity surrounding the drying room or oven inhibits drying efficiency because the air pulled into the room is incapable of picking up much moisture from the molds. The maximum temperature at which Hydro-Stone Gypsum Cement molds are safe from calcination is 120 °F (49 °C). With substantial free water in the mold, a higher drying temperature can be used without difficulty. As drying progresses, the temperature must be reduced to prevent calcination. Before removing molds from the dryer, the temperature should approach that of the area around the dryer to prevent thermal shock. See IG502 Drying Plaster Casts for additional information.
Safty precautions
When properly used, Hydro-Stone Gypsum Cement is easy to work with and complies with the federal Labeling of Hazardous Art Materials Act, 12 U.S.C. Section 1277 and ASTM D4236. Keep indoors at temperatures between 65 °F - 75 °F (18 °C - 24 °C) and 45% - 55% RH. Do not stack more than two pallets high. Keep from drafts. Rotate stock. USG Hydro-Stone Gypsum Cement should be used within 6 months of the manufacturing date located on the package. Always follow handling and use directions and safety warnings on the package.
This is final casted part of our group assignment:
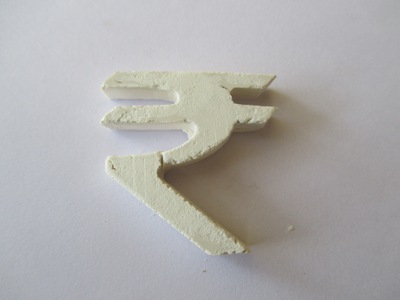