Mechanical design
The team of Fablab Iceland students: Gísli Snær Guðmundsson, Þórður Hjálmarsson, Magnús St. Magnusson and Aida González Vicente.
This week we met in Fablab Akureyri to work together on our projects and on the machine design and build.
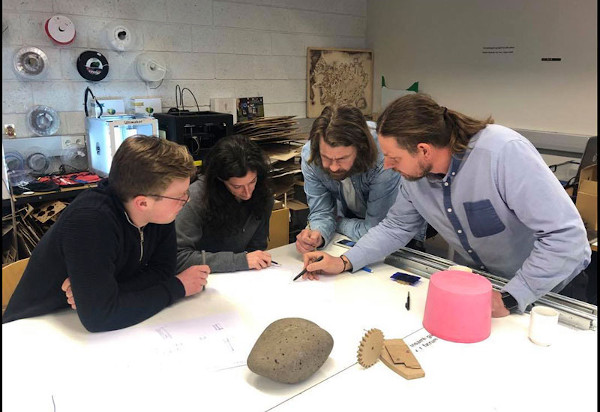
After a brainstorming, we decided to keep simple as possible but try to do something that might be useful for our final projects, either the build or the programming. In the preview sketc below you can see the stucture we came up with. The structure is able to move up and down with a hook that is able to move right and left.
With the basic plan we divided the work between the four members of the groups. We split up two teams of two. Magnús and Gísli started researching on how to use The TinyG, the step motors, the power and the programing. Me and Aida And went on to design the frame and the gears. We decided to use fusion 360 to be able to see the design in 3D.
The TinyG project is a many-axis motion control system. It is designed for small CNC applications and other applications that require highly controllable motion control. After Programming the TinyG we used a hardware fiddle called Chillipepr to communicate with the TinyG.
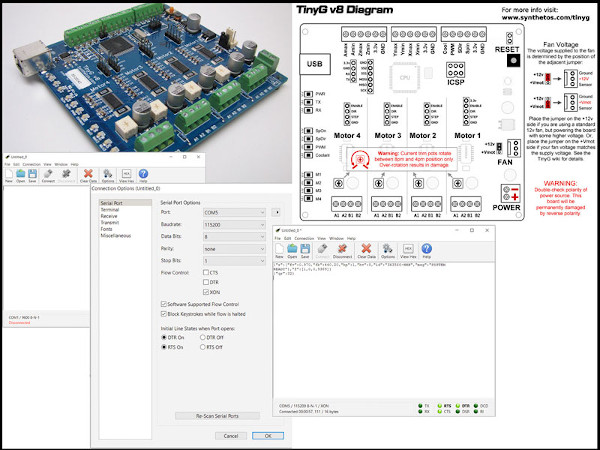
Chillipepr is a full-blown Gcode sender for your TinyG. The workspace connects to your TinyG via the serial port over the ChiliPeppr Serial Port JSON Server. It lets you view your Gcode in 3D, view the XYZA positions, perform jogging, and see advanced real-time details from the TinyG.
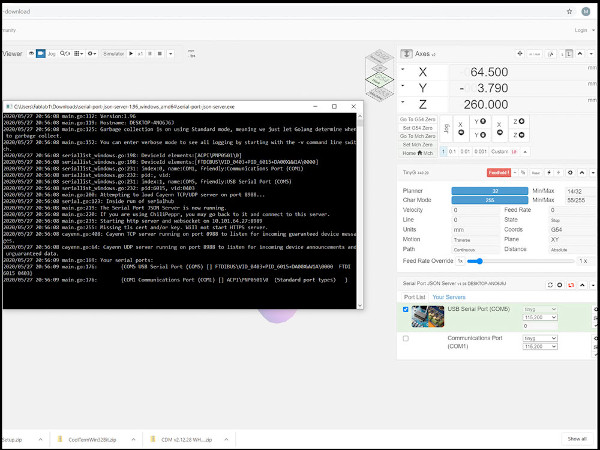
We designed the structure and gears in Fusion and were able to cut out most of the mechanical parts with a laser cutter but for the wood we went old school and used a table saw.
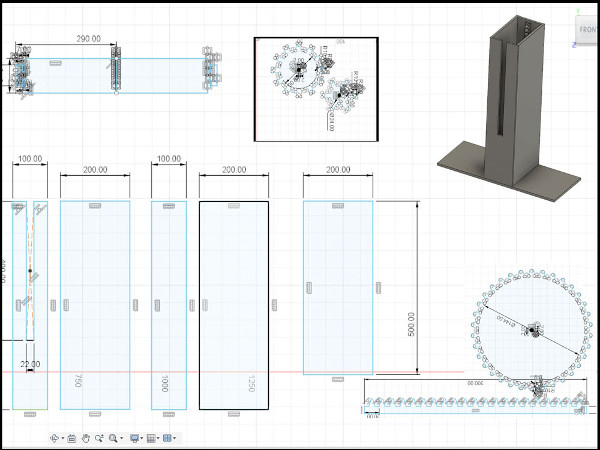
We tried two types of material for the gears. Milling gears out of POM (polyoxymethyline) using the Shopbot and lasercutting gears out of acrylic. We ended up making the gears out of acrylic because thera was less friction and it was much faster to do it that way.
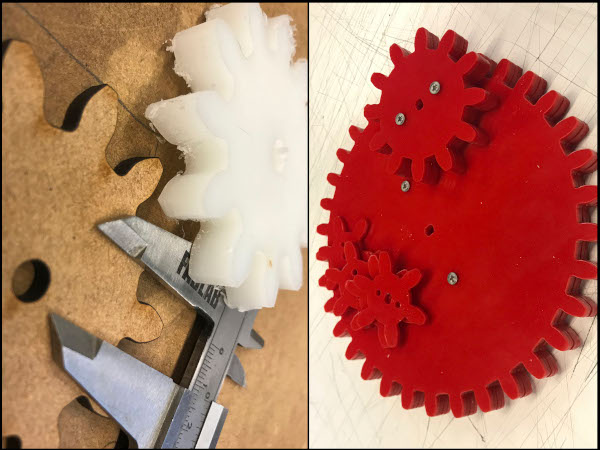
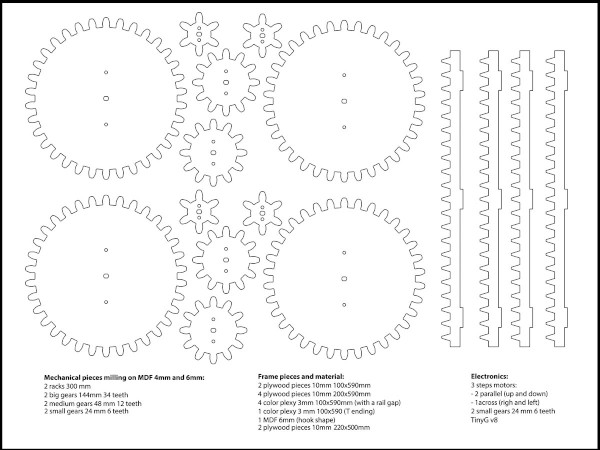
On the video we can see how we can control the machine. The mask video shows how the gears and rack work to go up and down. However the frame was too heavy for the motors to lift properly and there was also an issue with friction in the gears, but the design worked up to a point and with a little manual help the ramp moved up and down
Mechanical design Video HERE.