Moulding and Casting
Week 15
Machines and Materials
Softwares
Files
Group Assignments
During this week we are going to design a 3D mould around the stock and tooling that you'll be using, mill it (rough cut + (at least) three-axis finish cut), and use it to cast parts.
Individual Assigment
Design a 3D mold around the stock and tooling that you'll be using, mill it, and use it to cast parts.
In this week,we will learn how to manufacture a 3D model using Roland MDX50 to mill a mold of two complementary parts of the 3D model. Then to attach the two parts of the 3D model together and to pour or inject a liquid material like silicon rubber or plastic. The first method is called “Molding” or “Moulding”, which is a process used of manufacturing by shaping liquid or pliable raw material using a rigid frame called a mold or matrix. This itself may have been made using a pattern or model of the final 3D object. The second process is called “Casting” which is a manufacturing process in which a liquid material is usually poured into a mold. The mold should contain a hollow cavity to fit the desired object, and then allowed to solidify. The solidified part is also known as a casting, which is ejected or broken out of the mold to complete the process.
The following diagram represents the molding and casting process.
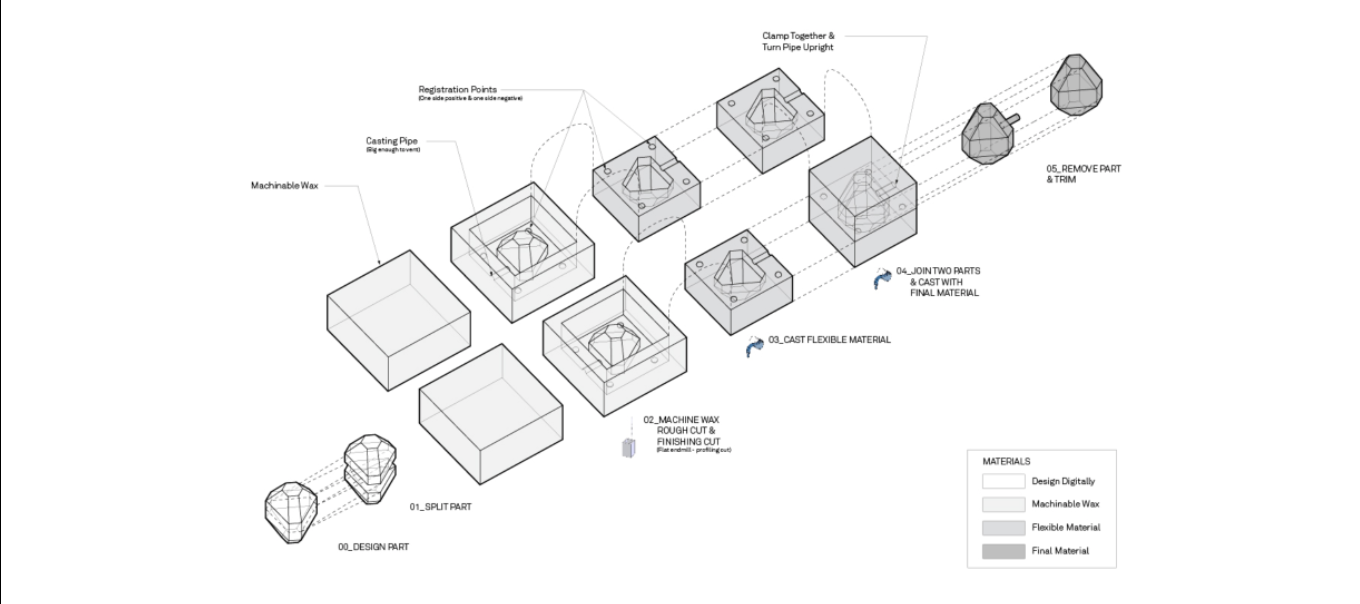
I used Qatar's National Museum as inspiration
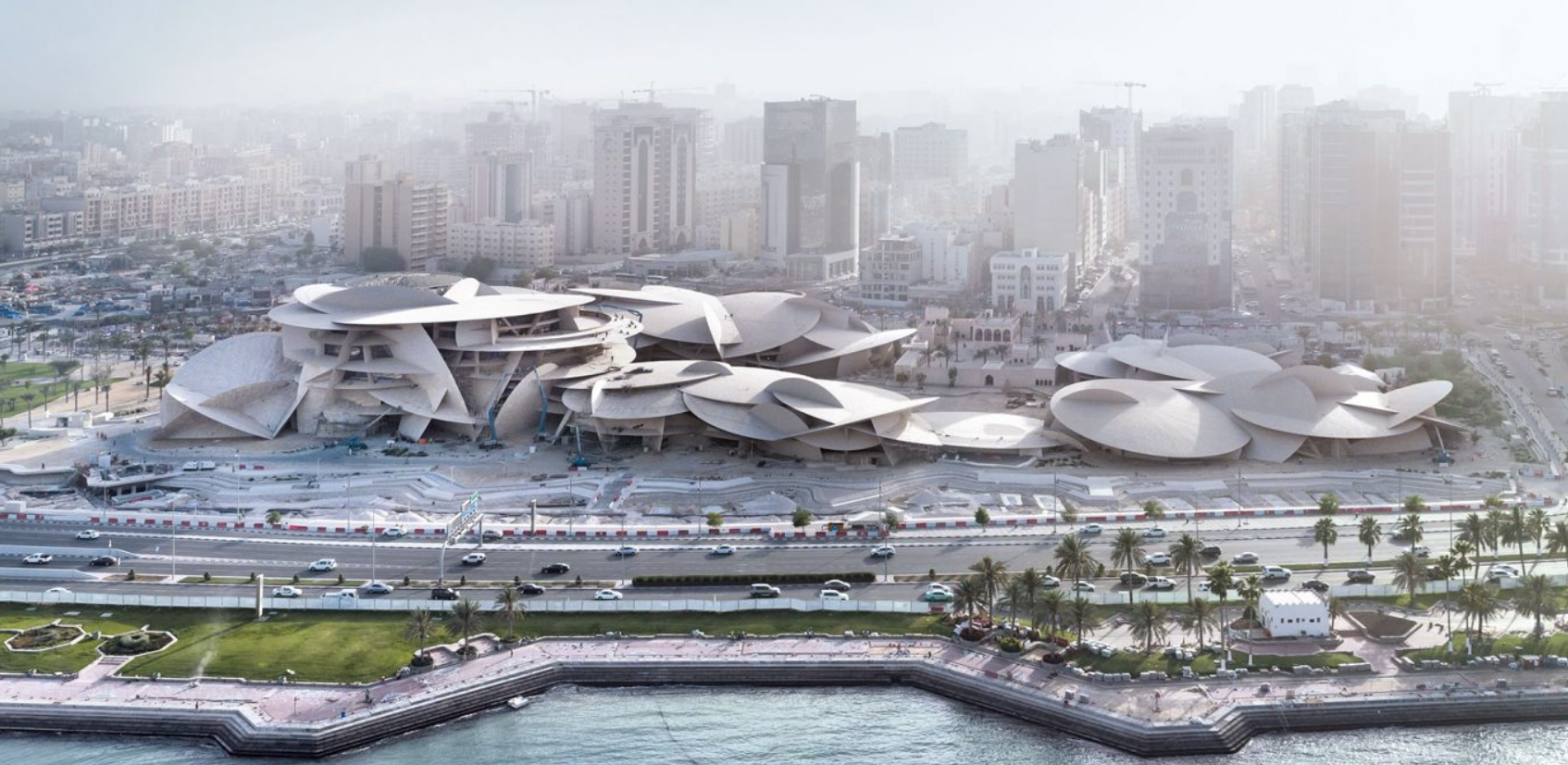
Which blooms like a desert rose
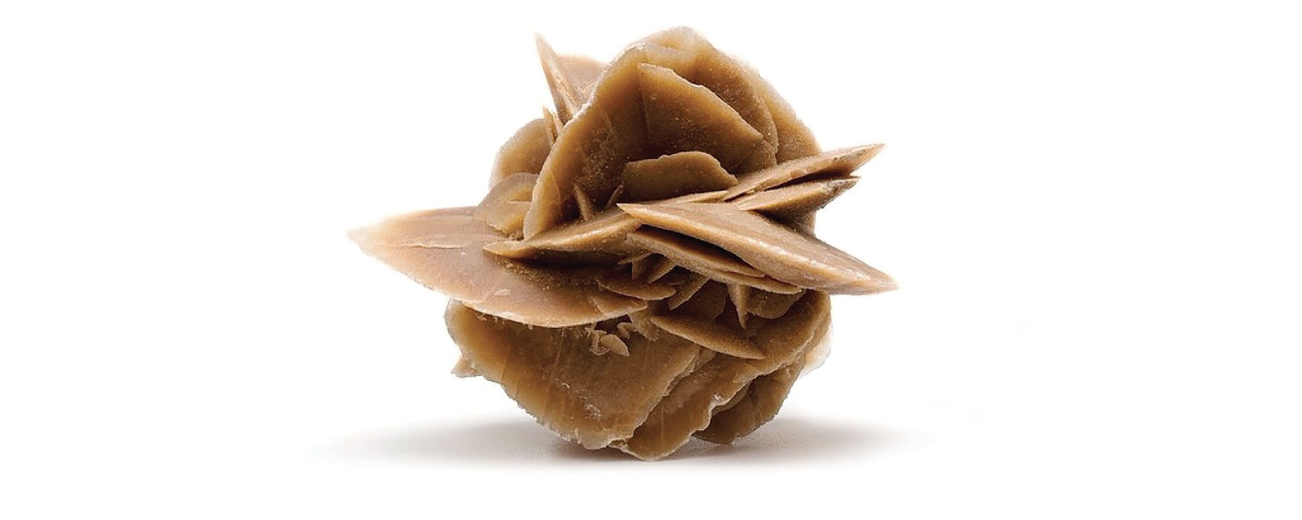
I started the porcess by modeling the pieces in Rhino
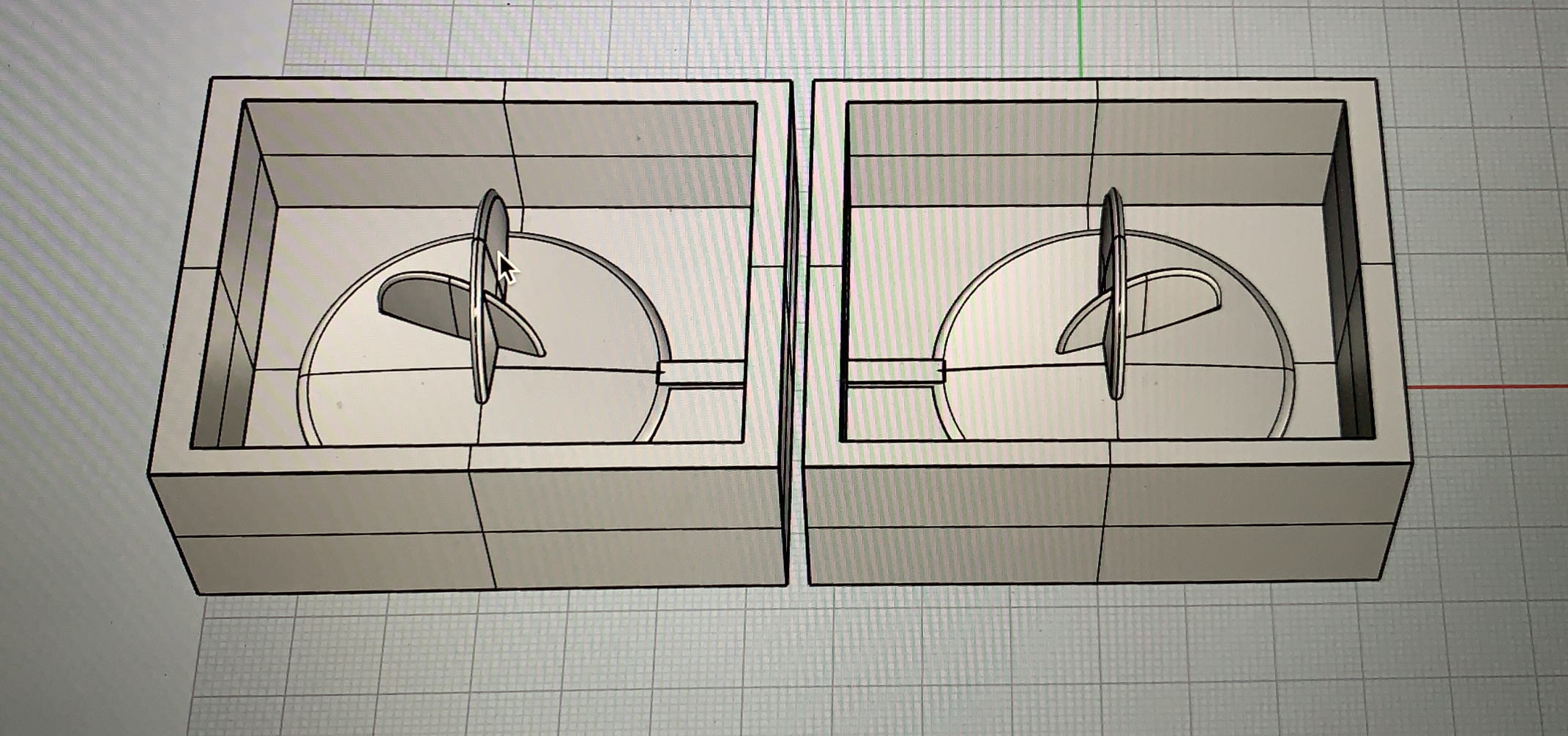
And made render to preview the final piece, decorative cookies or cholates for the Museum's Cafe.
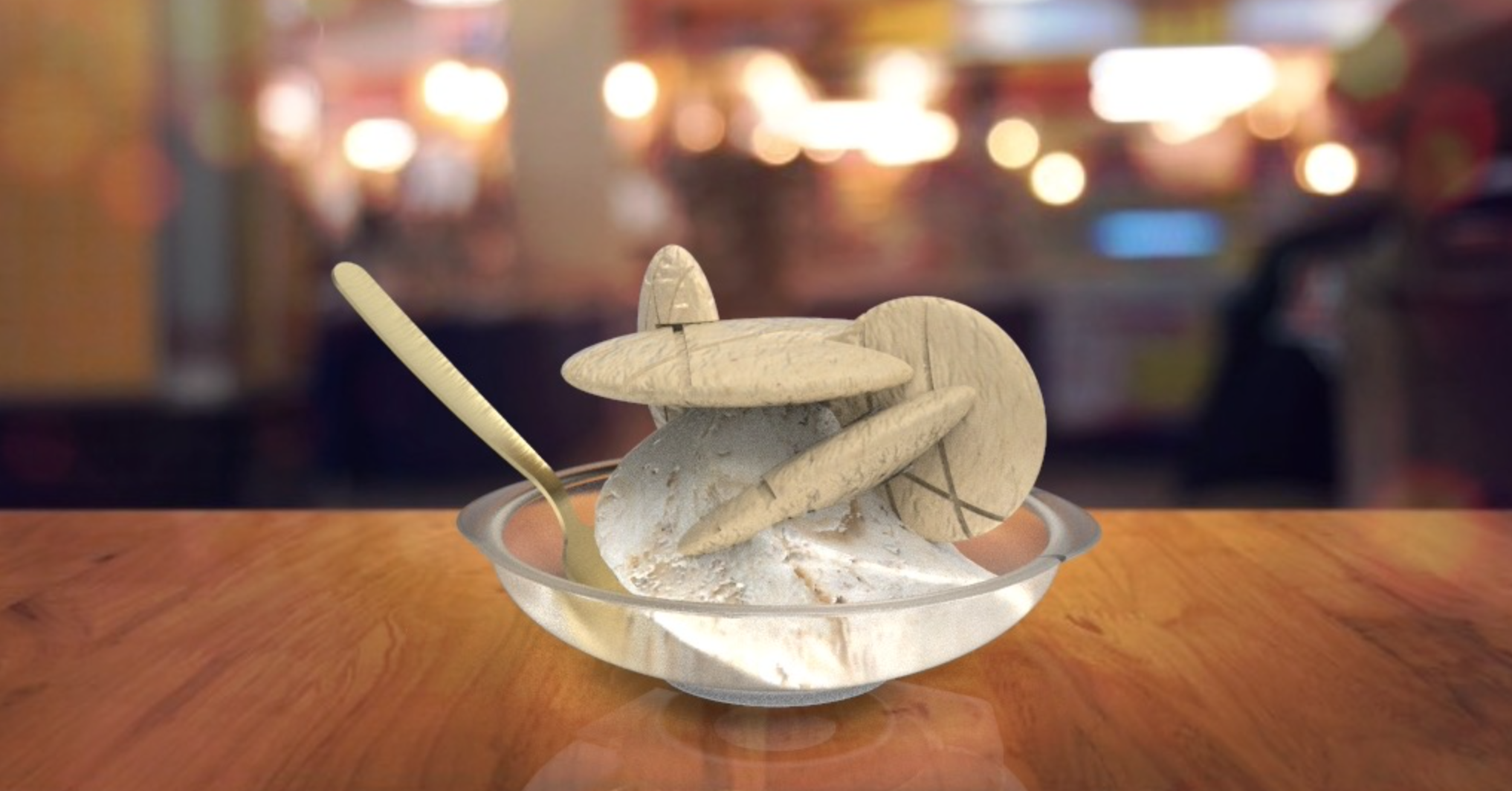
After having the mold ready, we export it to STL file and open it in SRP player, were we set it up and proceed with the milling process. Following the next steps:
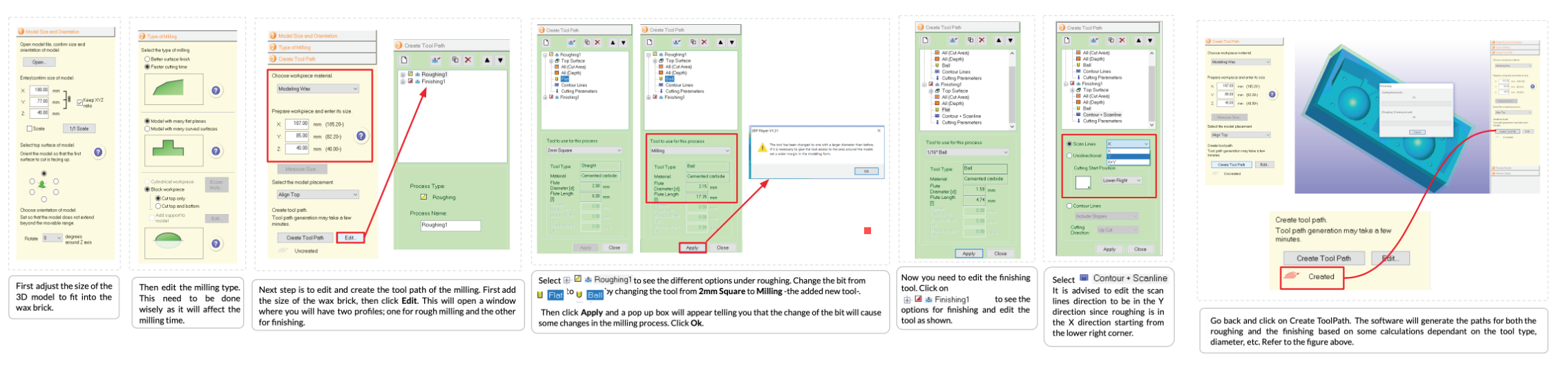
And after Z sensing, marking 0 in the middle of the machinable wax we start cutting the pieces
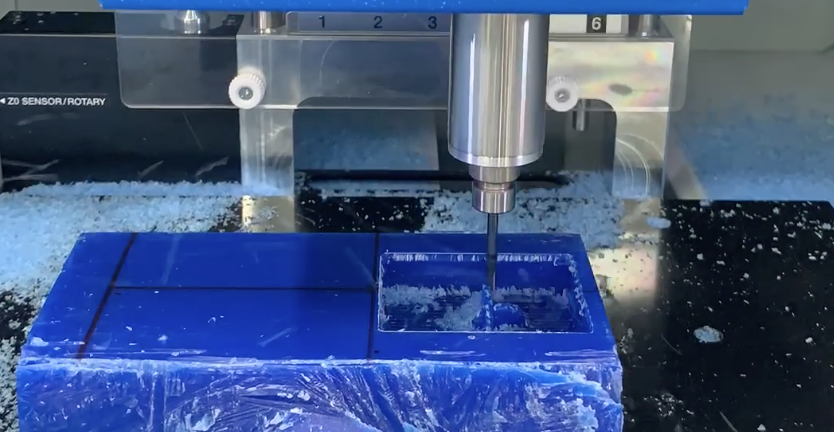
Milling result!
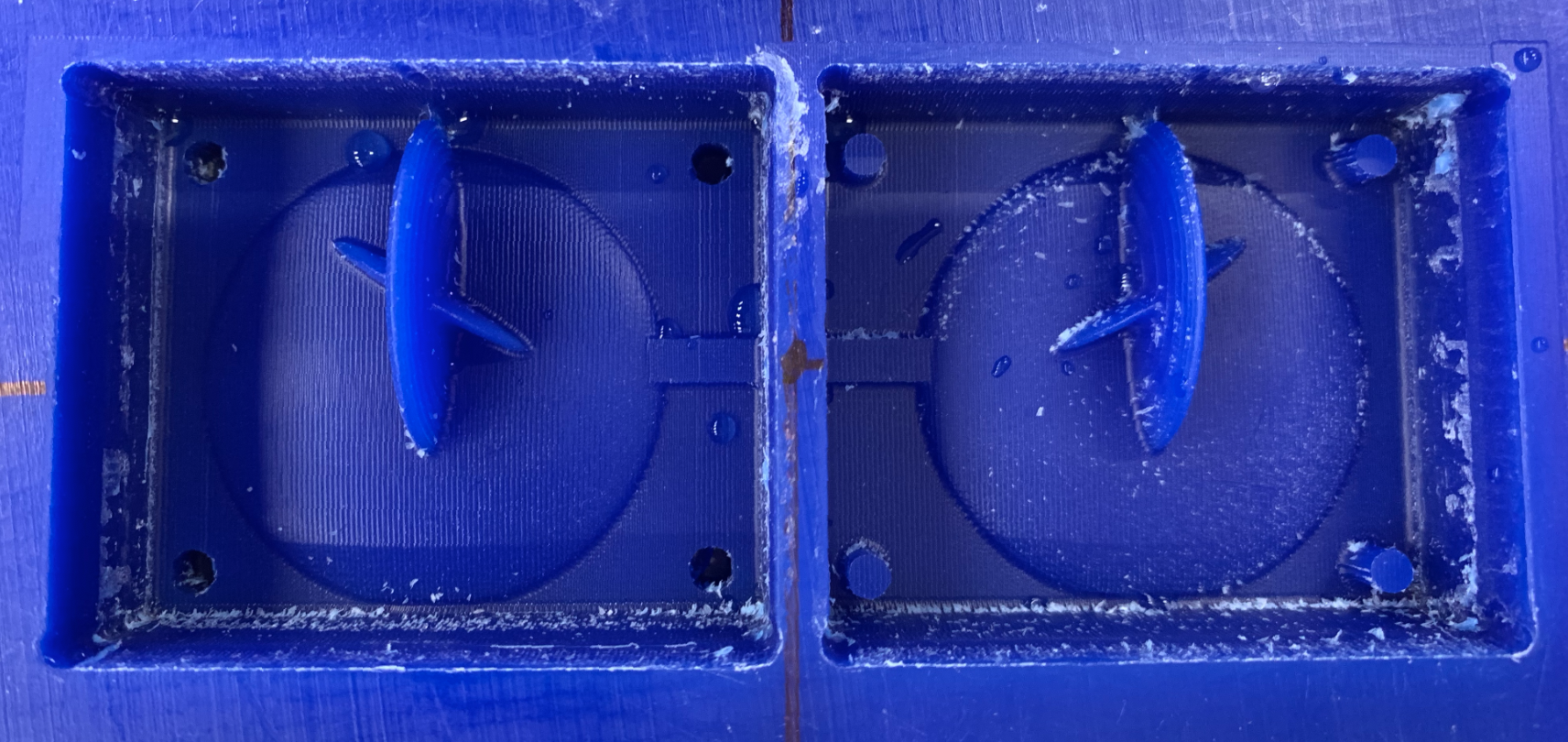
For mold I will be using Smooth-Sil® 940, suitable for making baking molds and trays, ice trays, casting butter, chocolate and other applications used to produce foods.
You can see the date sheet here
Also, below, you will have a glance of the techincal specifications.

1- Smooth-Sil 940 is a 100:10 by weight mix ratio material. Part A of the silicone is weighed. Then part B of the Smooth-Sil is weighed out as well. The material is mixed thoroughly. Once an even mix is achieved, the material can be vacuumed.
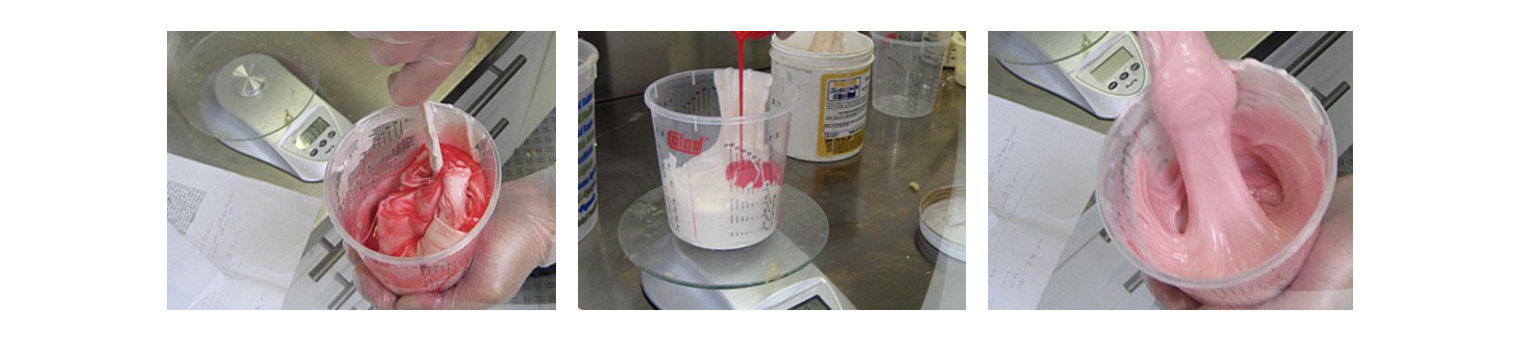
2- The material is poured in a thin stream into the mold box until the silicone flows up and over the model. Smooth-Sil 940 is fully cured in 24 hours.
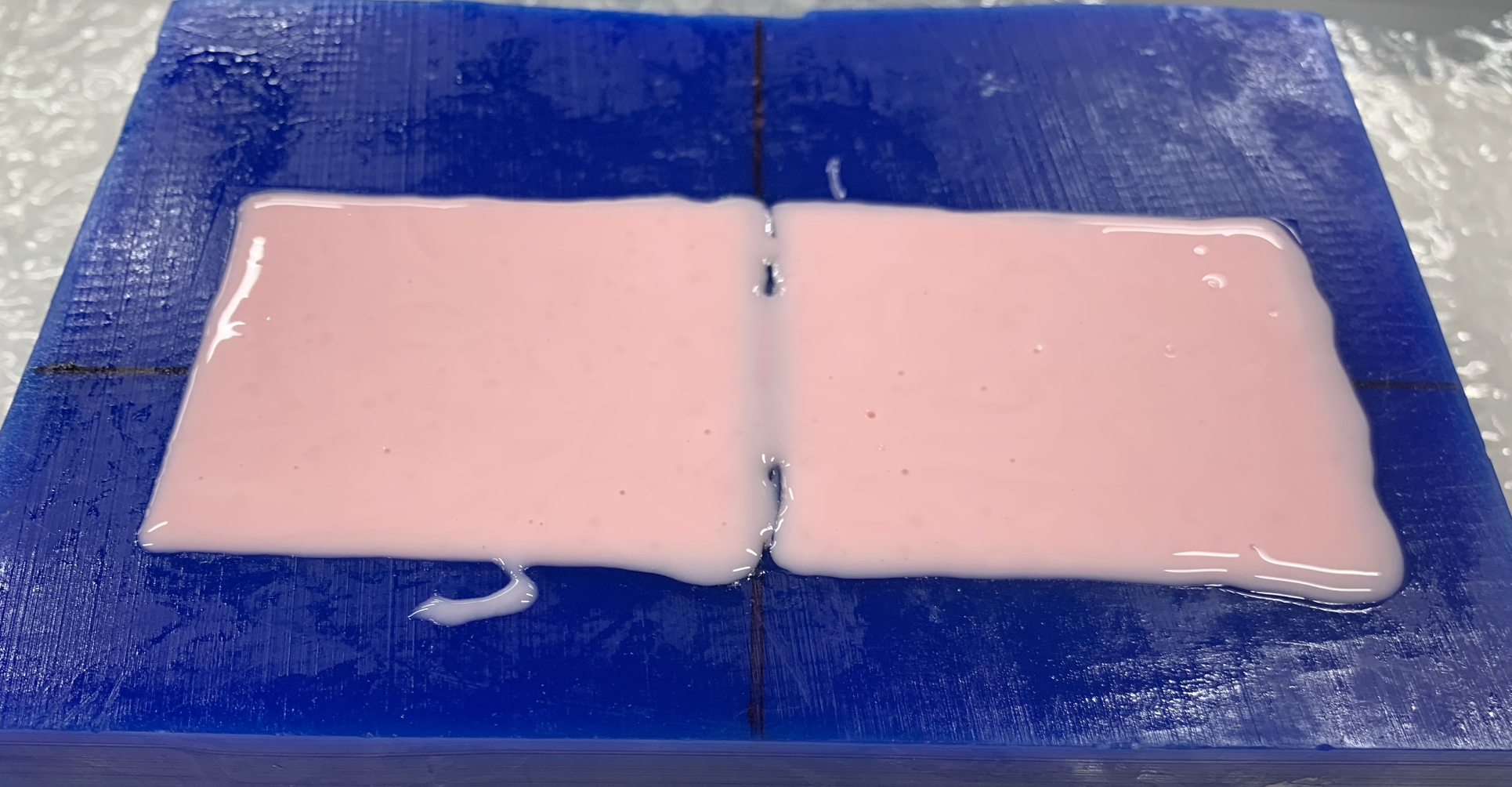
Time to clear the mold and cast some chocolate!
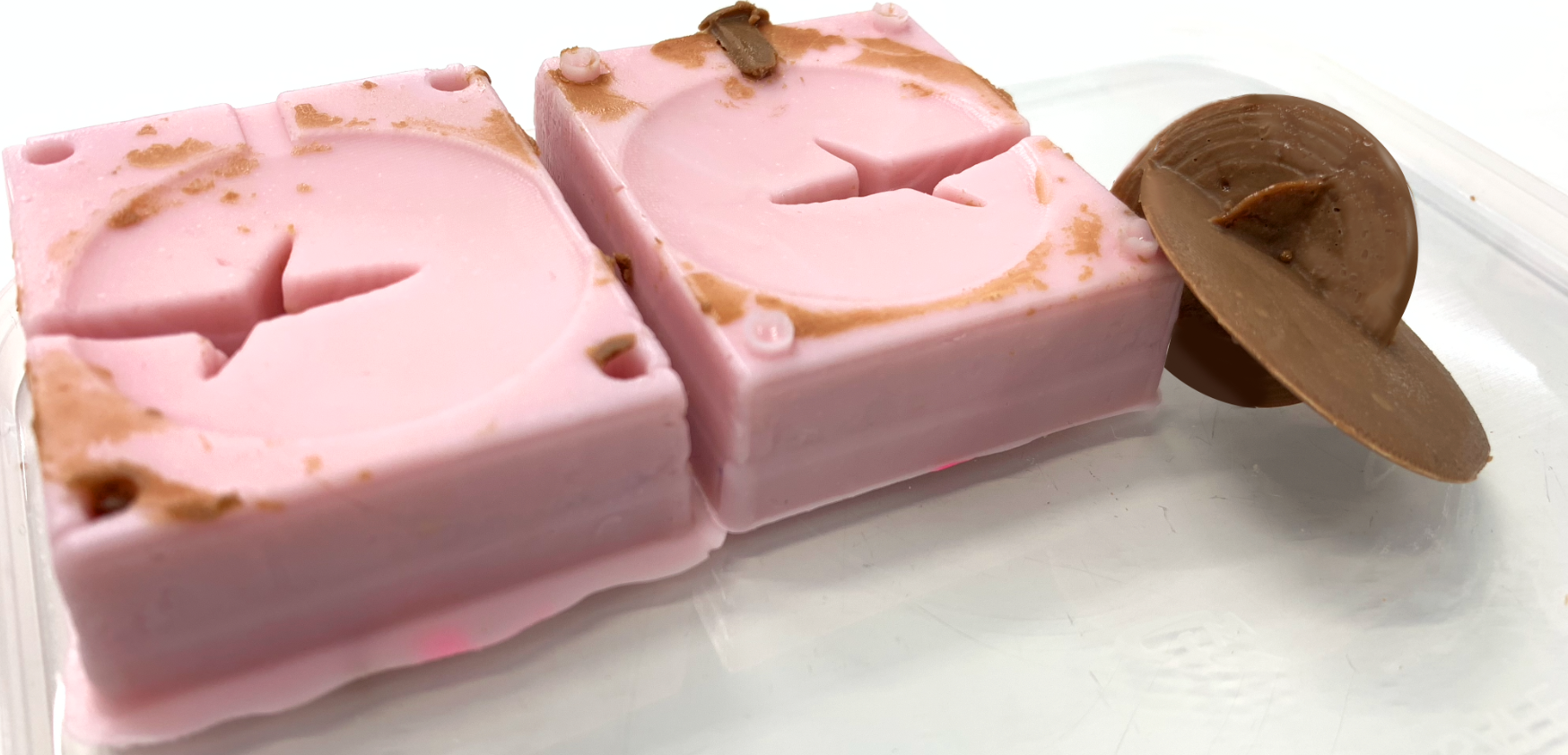
Problems:
The disk in the mold was in the edge, making the mold imposible to close. I decided to repeat the process and refine the form, give a bit more space between the model and the walls and here is the final contra mold:
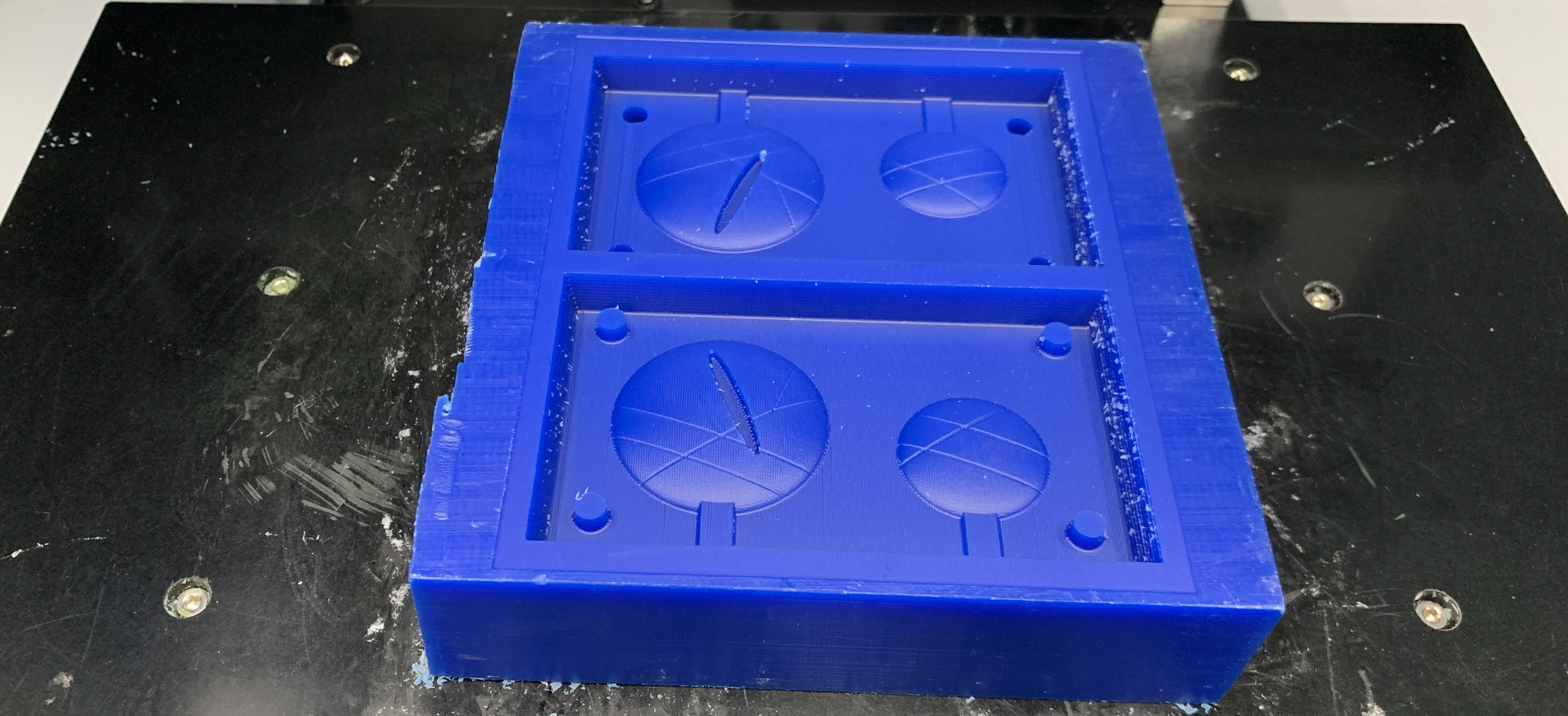
Final mold!
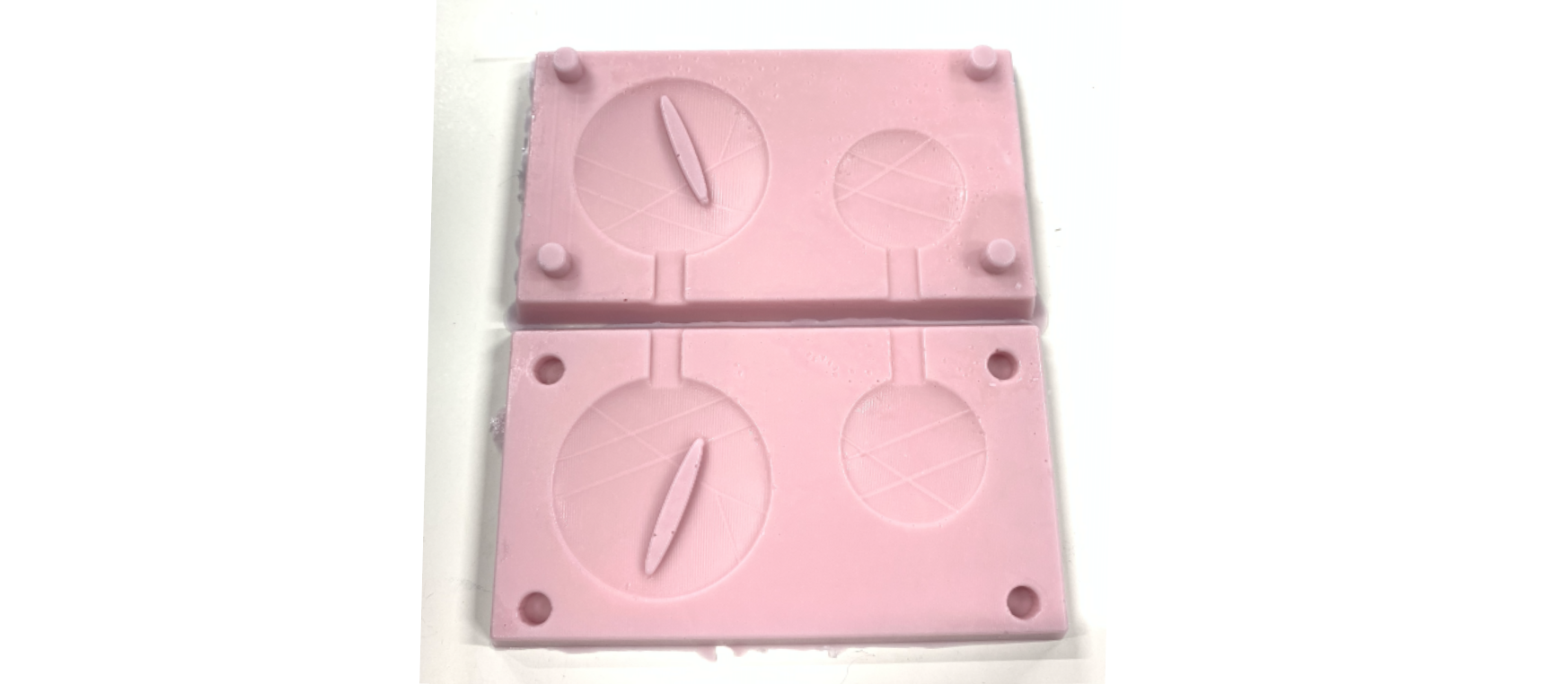
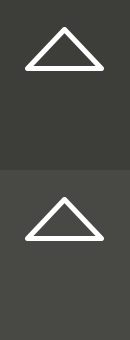