Electronics Production (week04)
Group Assignment
- Characterize the design rules for your PCB production process
Tool - Endmill
I used following Endmills for this week.
- Shank diameter: 1/8 Inches(3.175mm)
- 0.0100” DIA 220M .010 (0.254 mm) > Shared
- 0.0156” DIA 2FL SE AlTiN 1/64 Inches(0.396875 mm) > MyBit
- 0.0312” DIA 2FL SE AlTiN 1/32 Inches(0.79375 mm) > Shared
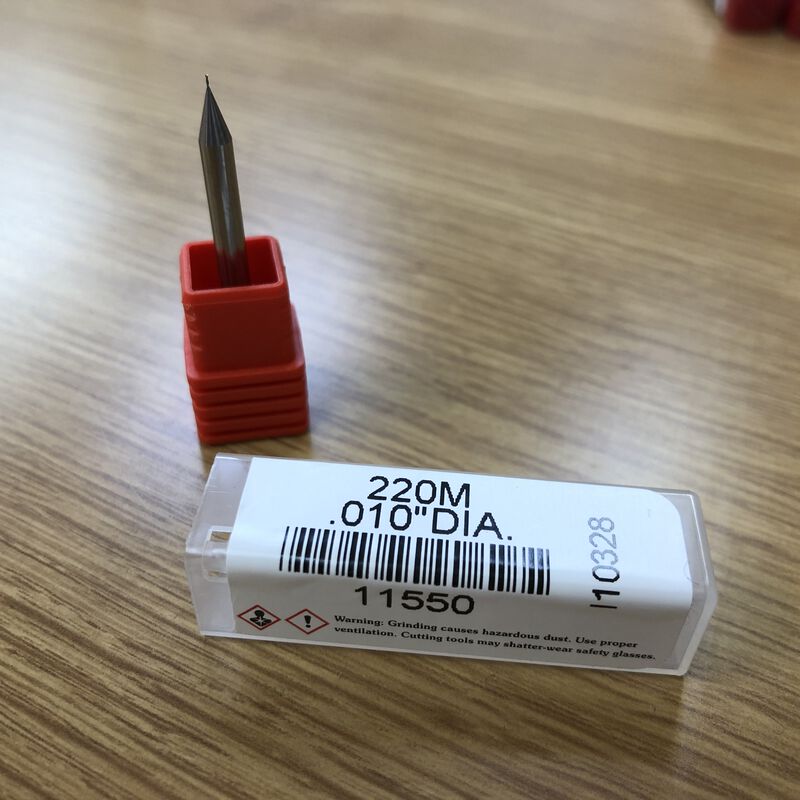
Square End, 0.01 Inch
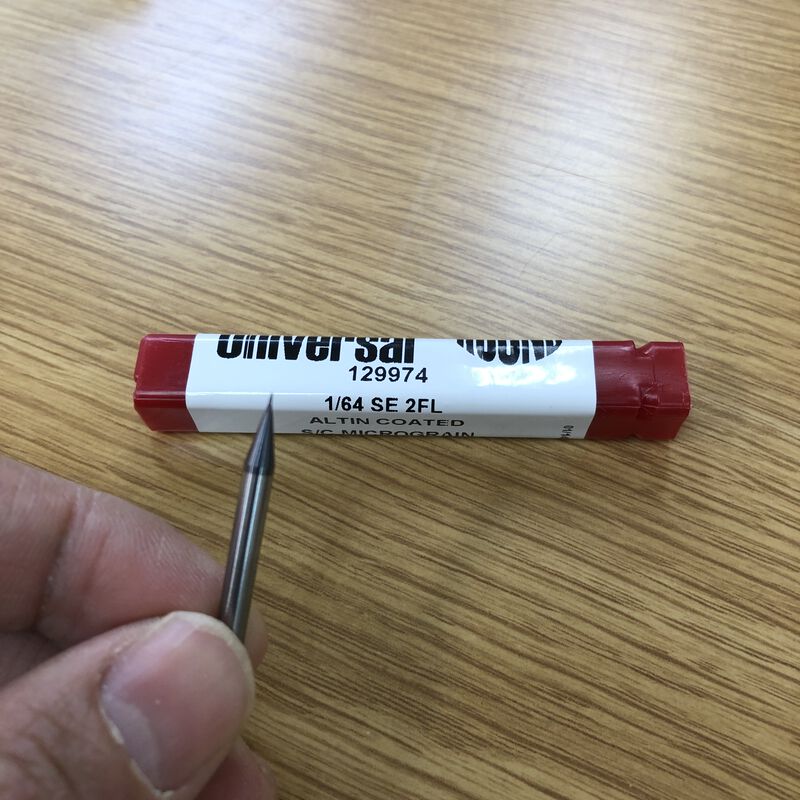
Square End, 1/64 Inch
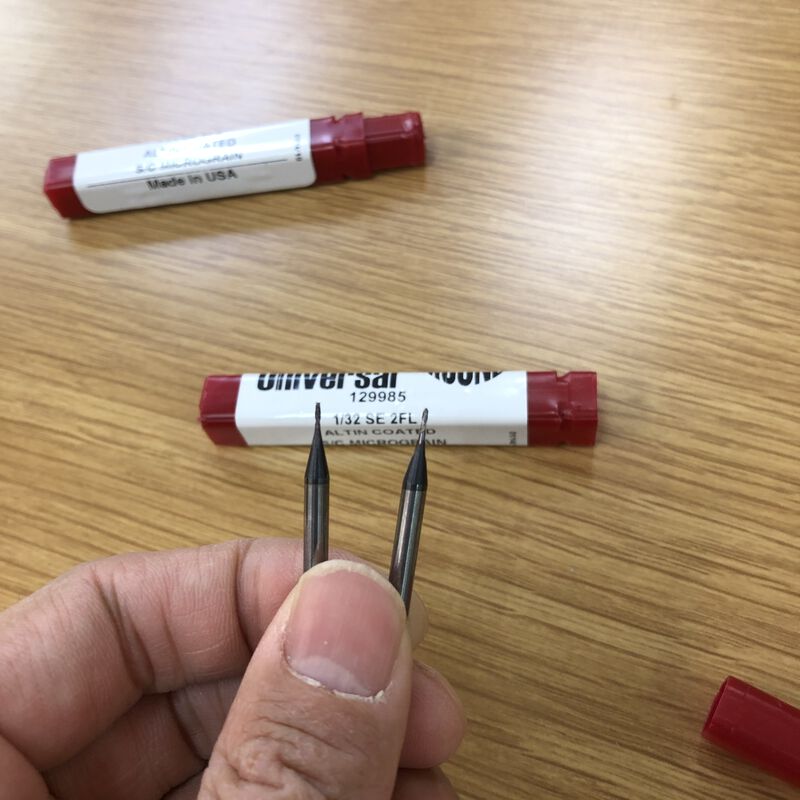
Left: Square End / Right: Ball Nose, 1/32 Inch
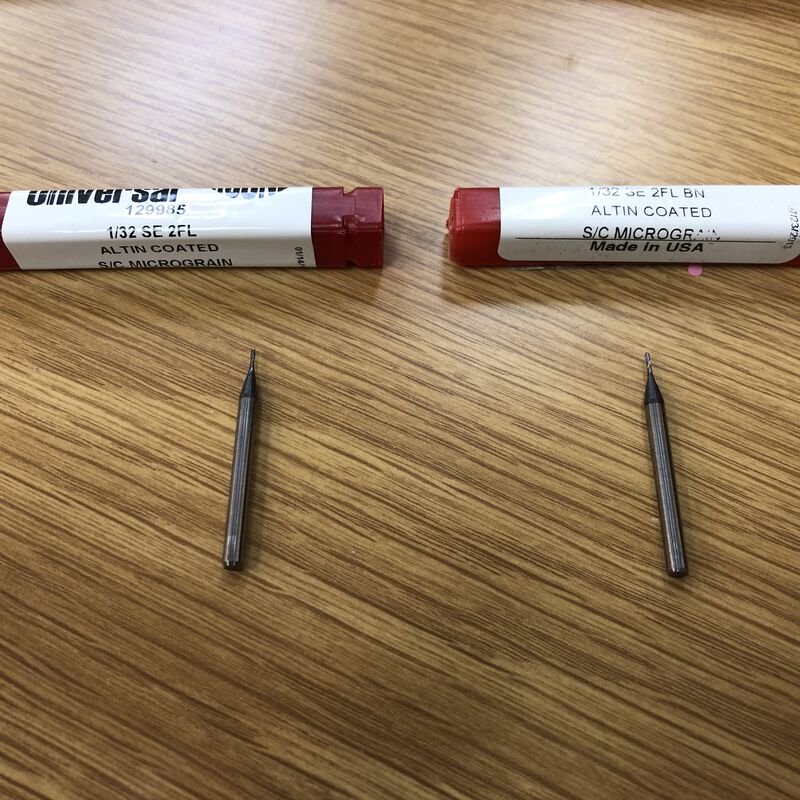
Left: Square End / Right: Ball Nose, 1/32 Inch
Material - PCB
As a PCB Material, I used a FR1(phenolic paper).
Machine - CNC
CNC at Fablab Kannai is Roland MDX15
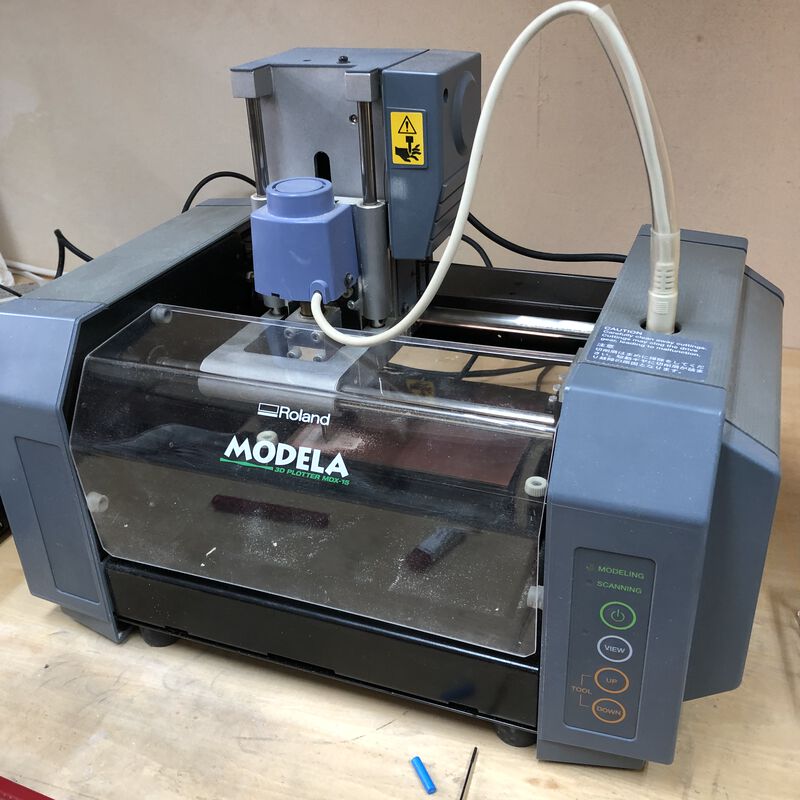
Product | MDX-15 |
Operating range | 152.4mm(X)×101.6mm(Y)×60.5mm(Z) |
Table size | 170mm(X)×110mm(Y) |
Interface | Serial(RS-232C) |
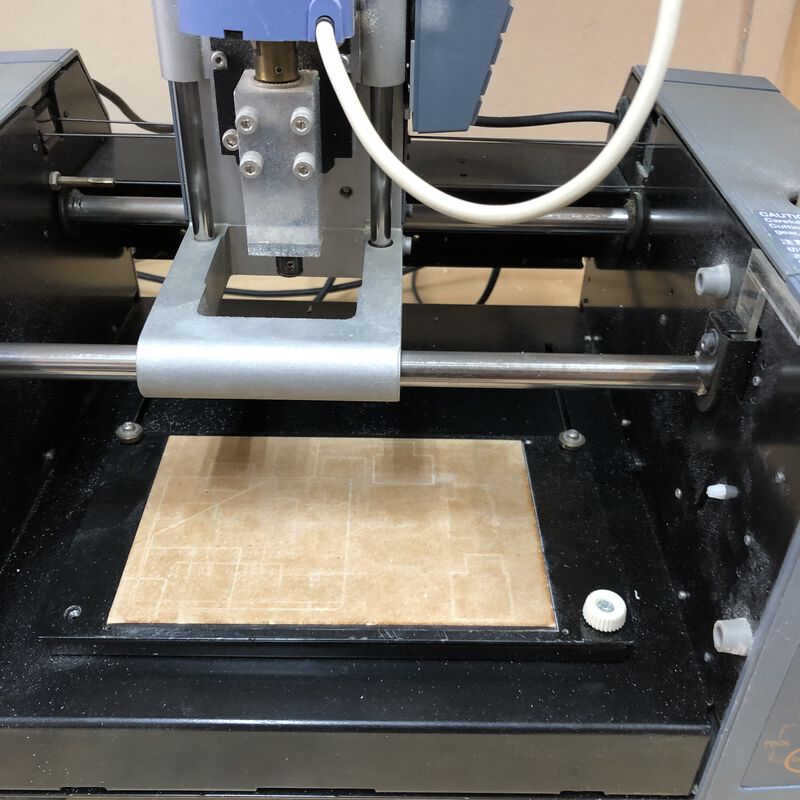
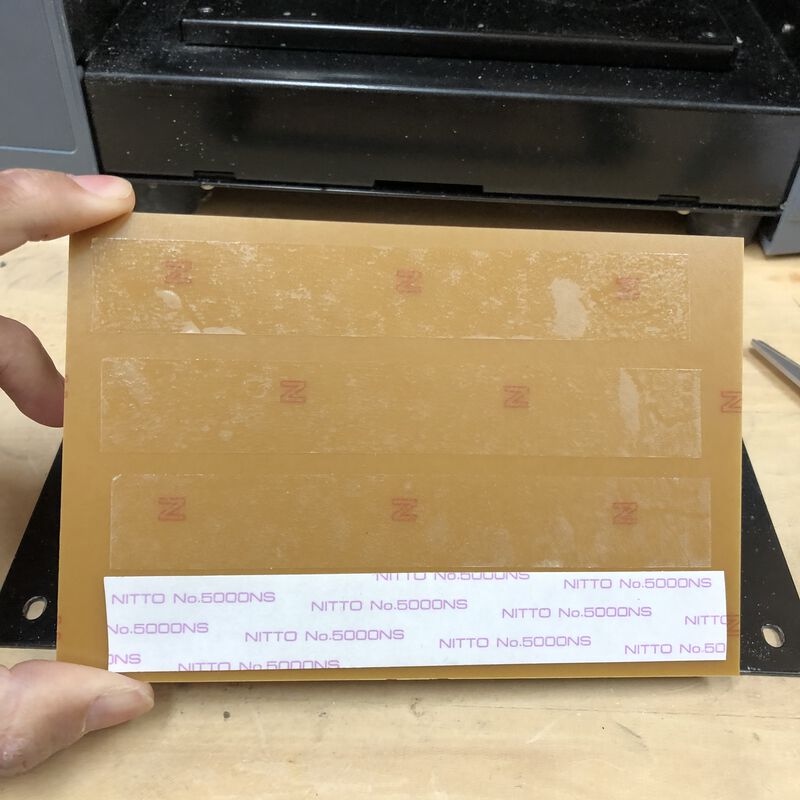
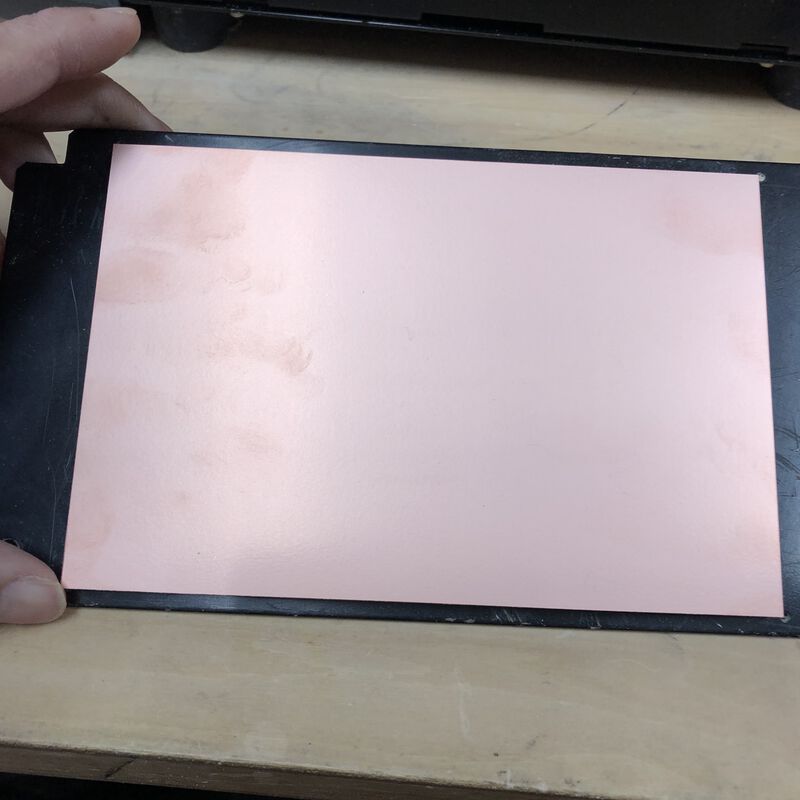
It's important that wasted board on the table to be leveled(flatting)
Fix the PCB sheet on the top of the table with double-side tape
Testcut Data
I checked how MDX-15 can be controlled by the instruction of "tarce width" test file, high resolution png files that is provided by FabAcademy.
Machine client - PC, Mods, FabModule
There are two client PC for MDX-15 at Fablab Kannai.
In Feb 2020, lab is setting up an additional client PC. It's because the USB - serial cables depend on softwares on the PC and we want to avoid to re-plug the cables for the time we want to switch the software.
■The original PC(with Raspbery Pi mark)
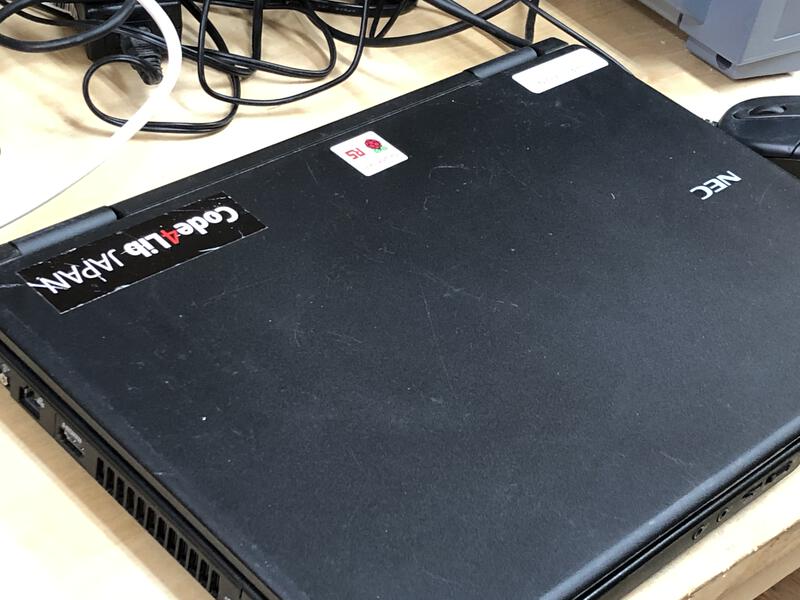
PC with RasPi Mark
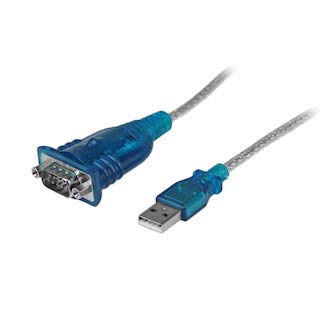
StarTech ICUSB232V2, flow control: RTSCTS
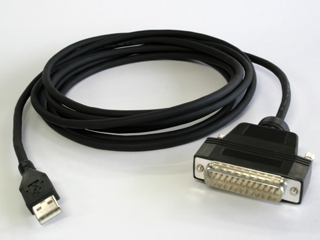
ME-US3, flow control: DSRDTR
After setting up the additional PC, it will not be necessary to use this cable for this PC
- OS: Ubuntu
- PCB milling
- software: Fabmodules
- StarTech ICUSB232V2, flow control: RTSCTS
- OS: Windows
- 2.5D cutting(molding & casting, leveling
- software: Modela Player4
- software: Virtual Modeler
- usb serial cable: ME-US3, flow control: DSRDTR
■Additional PC(with CNC mark)
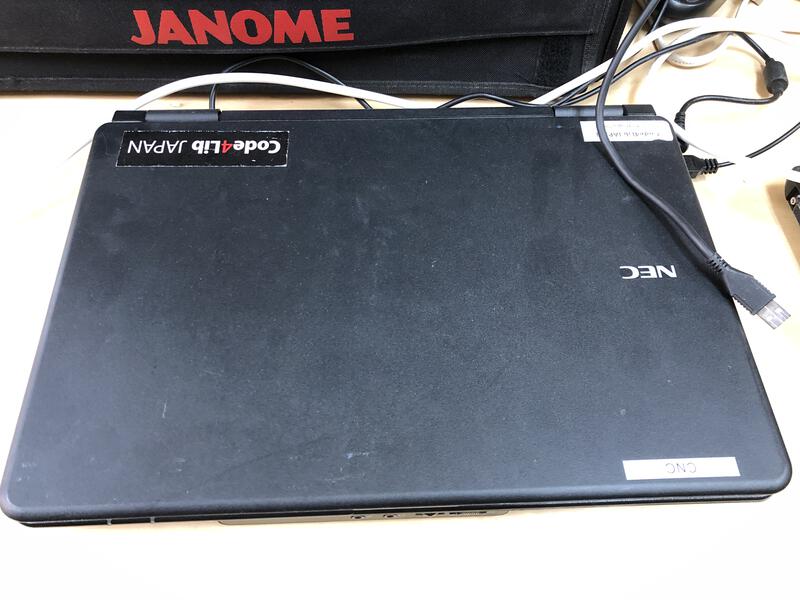
PC with CNC mark
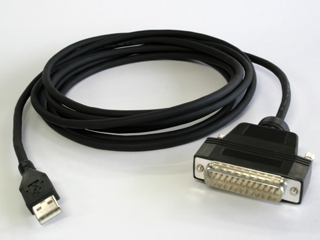
ME-US3, flow control: DSRDTR
- OS: Xubuntu
- PCB milling
- software: mods
- usb serial cable: ME-US3, flow control: DSRDTR
- OS: Windows
- 2.5D cutting(molding & casting, leveling
- software: Modela Player4 (TBD)
- software: Virtual Modeer (TBD)
- usb serial cable: ME-US3, flow control: DSRDTR
■Setup with mods
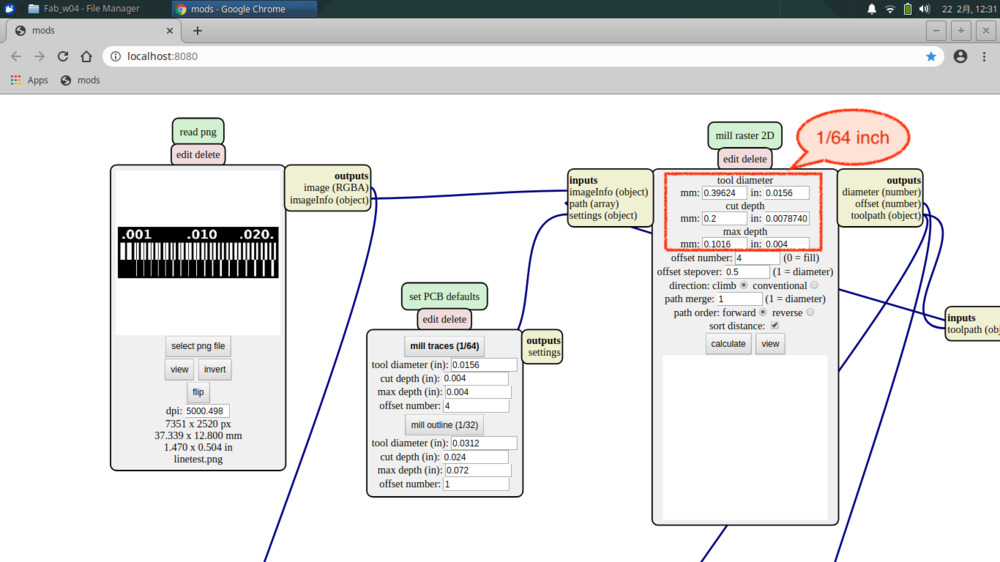
1. read png - select png file
2. set PCB defaults
- "mill traces(1/64"),
- "mill outline(1/32)"
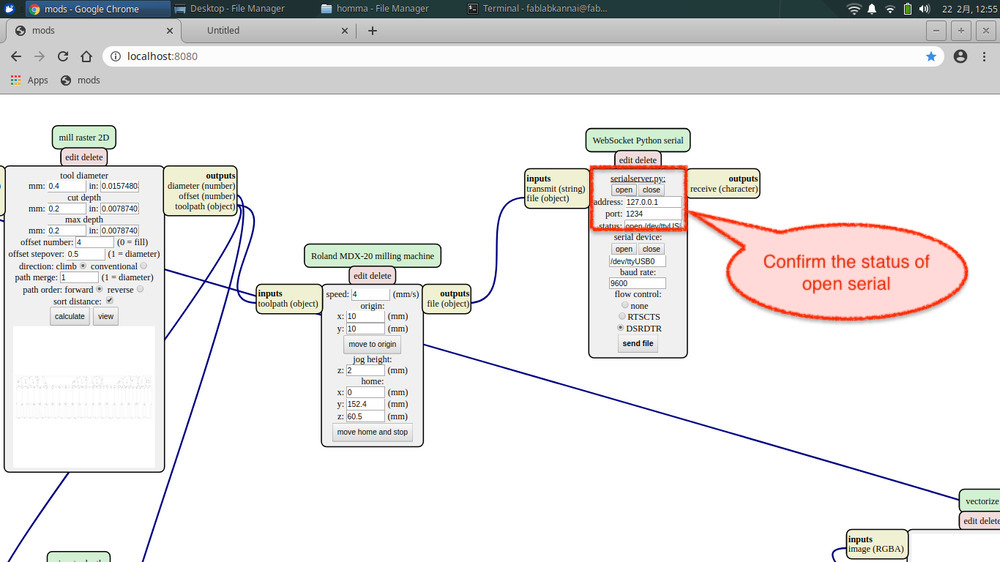
3. Roland MDX-20 milling machine
-x, y position(x:10mm, y:30mm etc.)
-jog height (z:2mm)
4. Raise z axis and set mil
5. mill raster 2D: “calculate”. It looks to be good to click “calculate” AFTER set
origin at Roland MDX-20 milling machine. Otherwise, the parameters of "origin" at the Roland MDX-20
Milling Machine is not applied to the CNC and end mill starts from x:0, y:0.
6. Roland MDX-20 - milling machine ("move to origin”)
<- just in case tool unexpectedly work from the other place
7. WebSocket Python Serial Check the status of serialserver.py (open)
8. WebSocket Python Serial - #Send file"
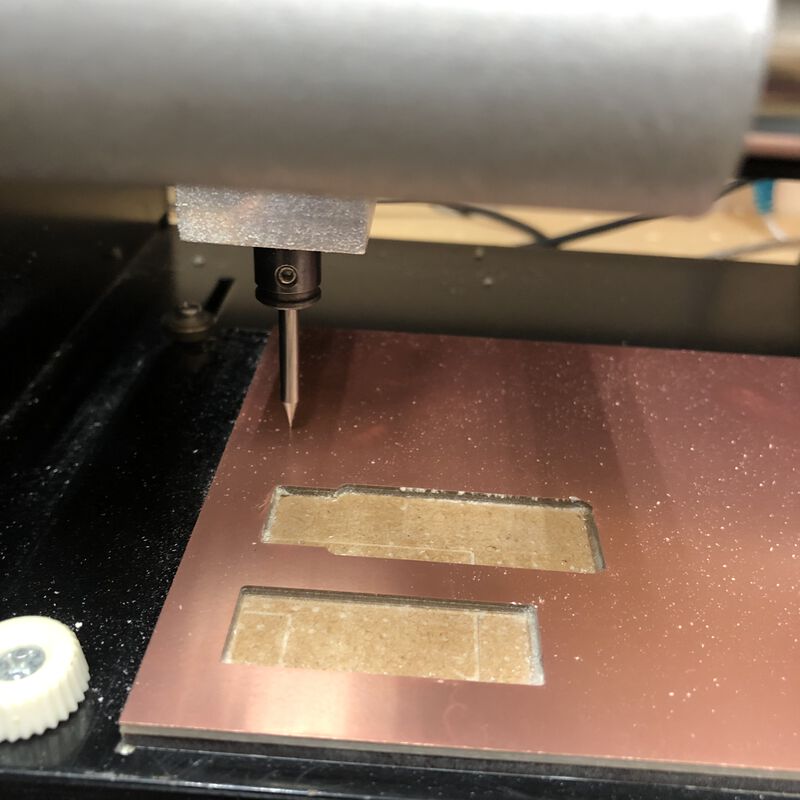
Raise z axis and set mil
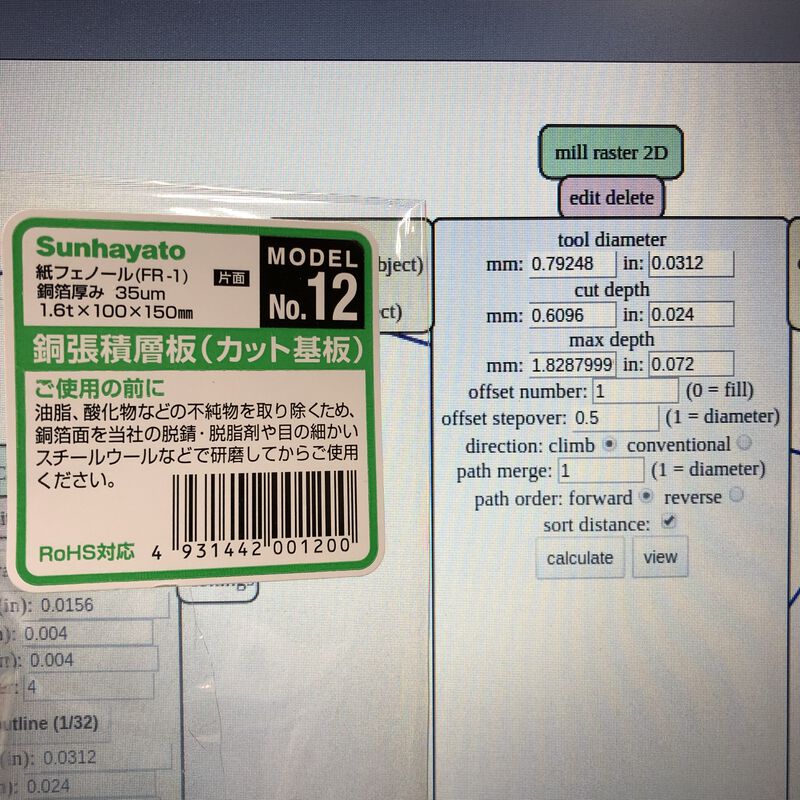
When cutting outline with 1/32 inch end mill,
-set PCB defaults: "mill outline(1/32)"
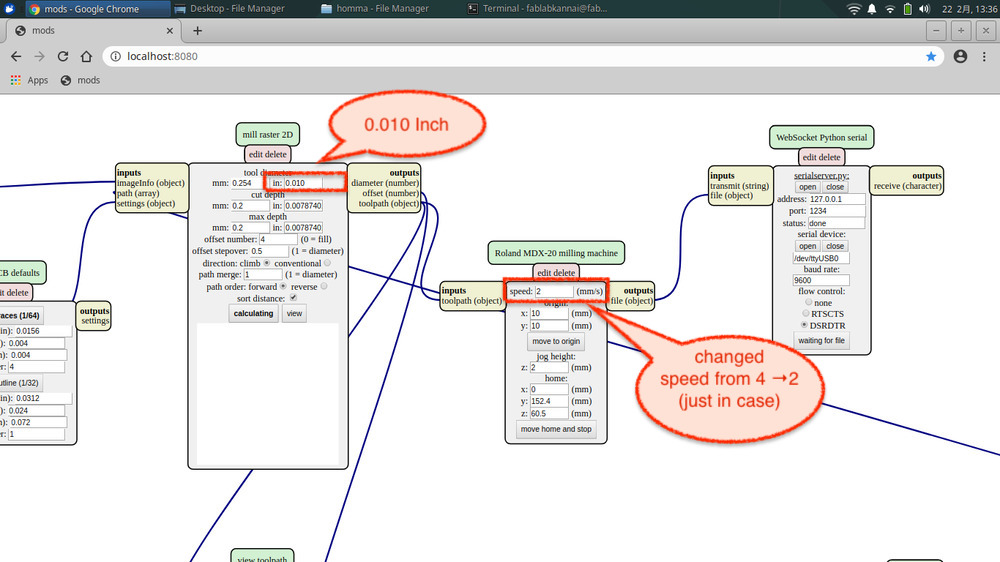
When cutting traces with 0.010 inch end mil,
-mill raster 2D: set tool diameter
Important rule: Cutting depth for 1 time needs to be less than tool diameter.
-Roland MDX-20 milling machine: change speed just in case
-After checking "origin", "calculate
# Check the serial communication process
$ ps -ef | grep -i serial
fablabk+ 754 1 1 12:37 ? 00:01:01 /usr/bin/python3 serialserver.py 127.0.0.1 1234
fablabk+ 2015 1721 0 13:49 pts/0 00:00:00 grep --color=auto -i serial
# kill the serial communication process
$ kill -9 754
$ ps -ef | grep -i serial
fablabk+ 2018 1721 0 13:49 pts/0 00:00:00 grep --color=auto -i serial
# when USB of MDX-15 connected after Linux boot and the error is "permission denied"
$ sudo chmod 777 /dev/ttyUSB0
# Restart the serial communication process
$ cd ~/mods/py
$ python3 serialserver.py 127.0.0.1 1234
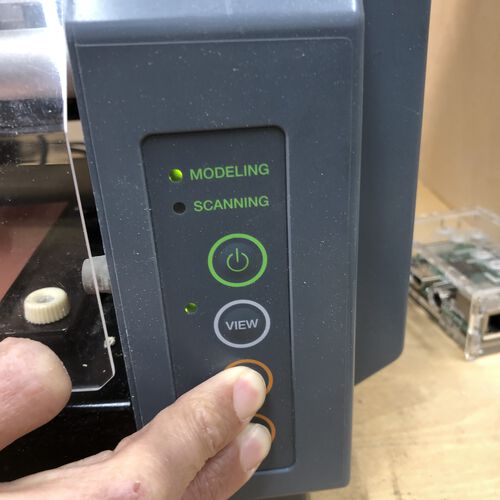
■Trace and Cut
Before cut, close the cover of MDX-15.
After tracing the internal area with 1/64 inch mill, cut the outline with 1/34 inch mill.
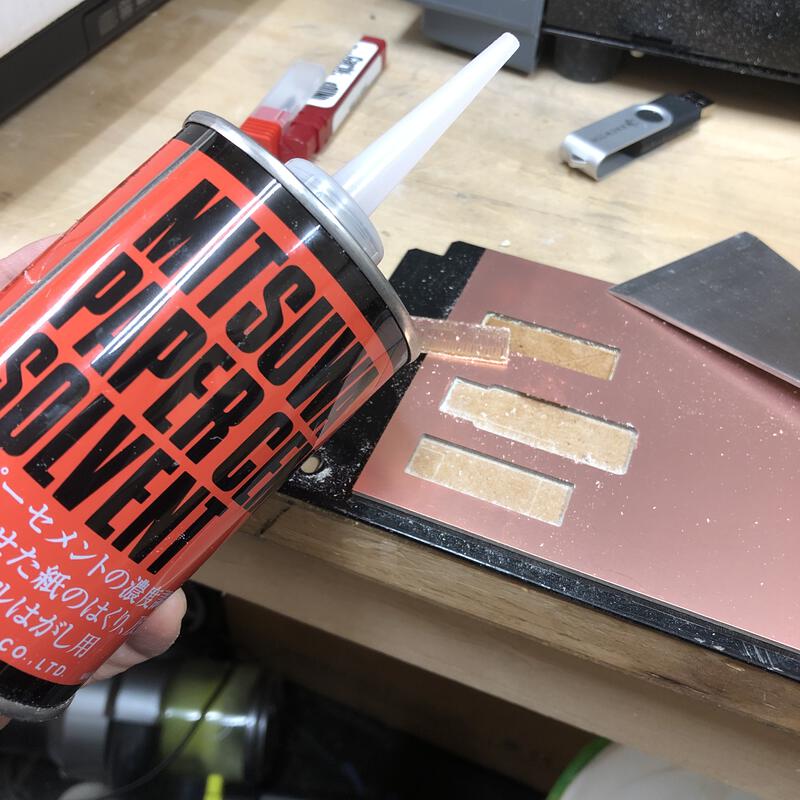
Solvent is a great tool to peal off the cut material
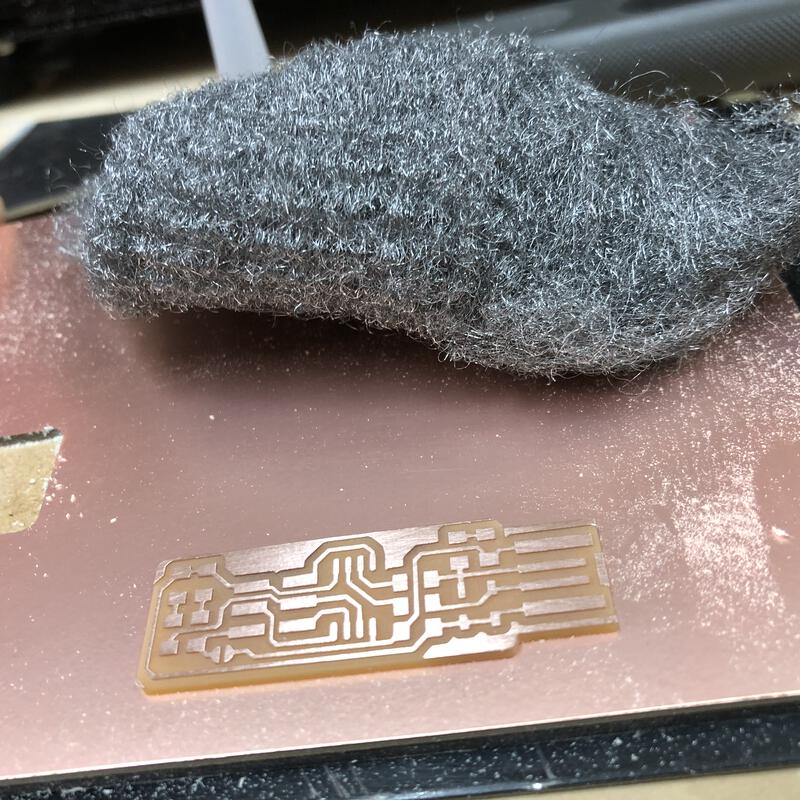
Clean up the surface by steel wool and dish washing detergent.
Evaluation to Test Cut
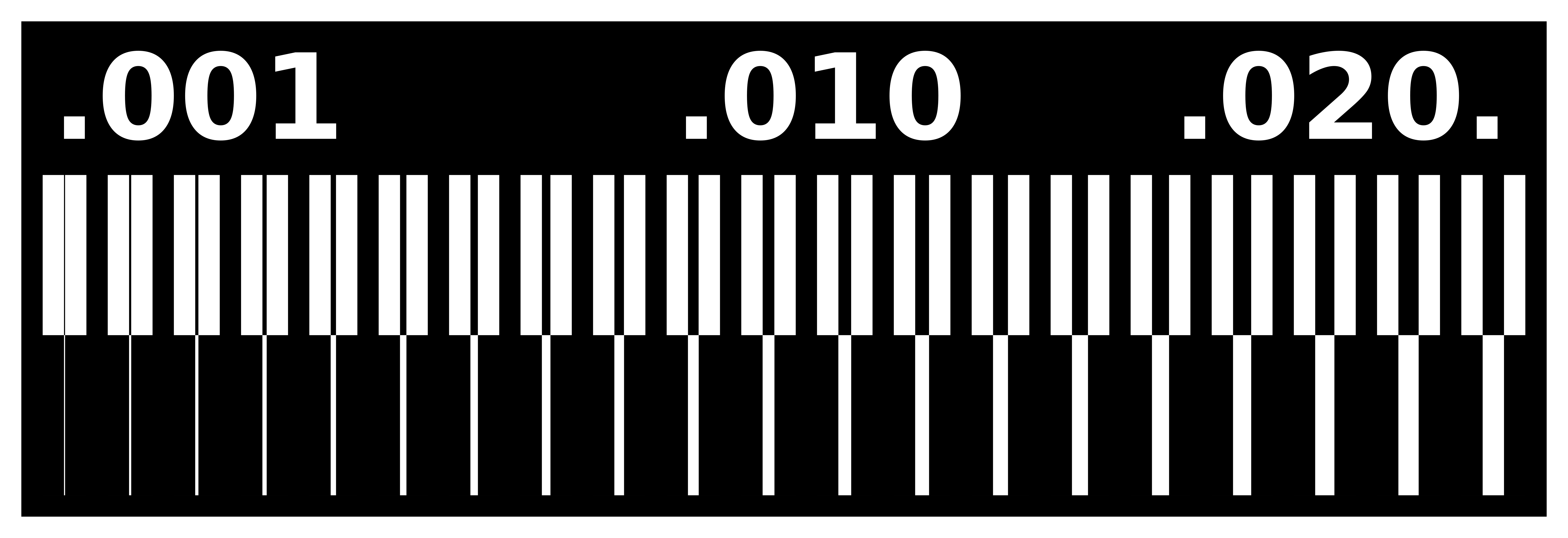
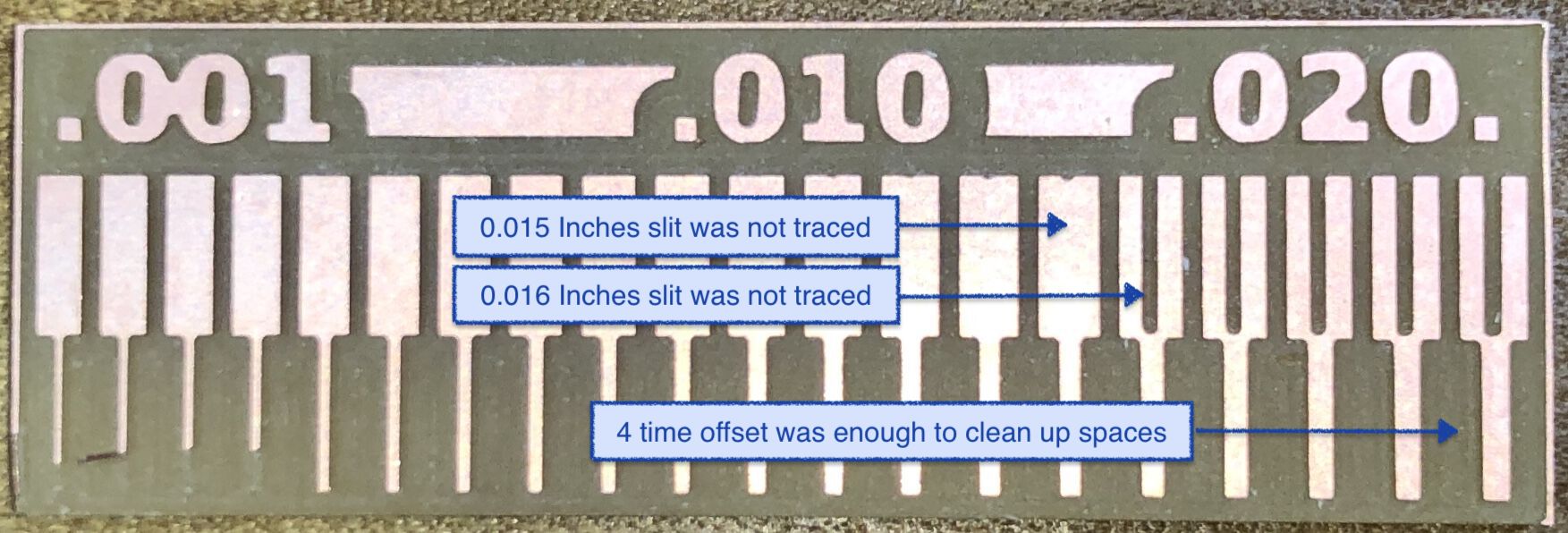
Using 1/64(0.0156) inches endmill, a slit of 0.016 inches slit was traced but 0.015 inches was not.
4 times offset by 1/64 inches endmill was enough to clean up spaces.
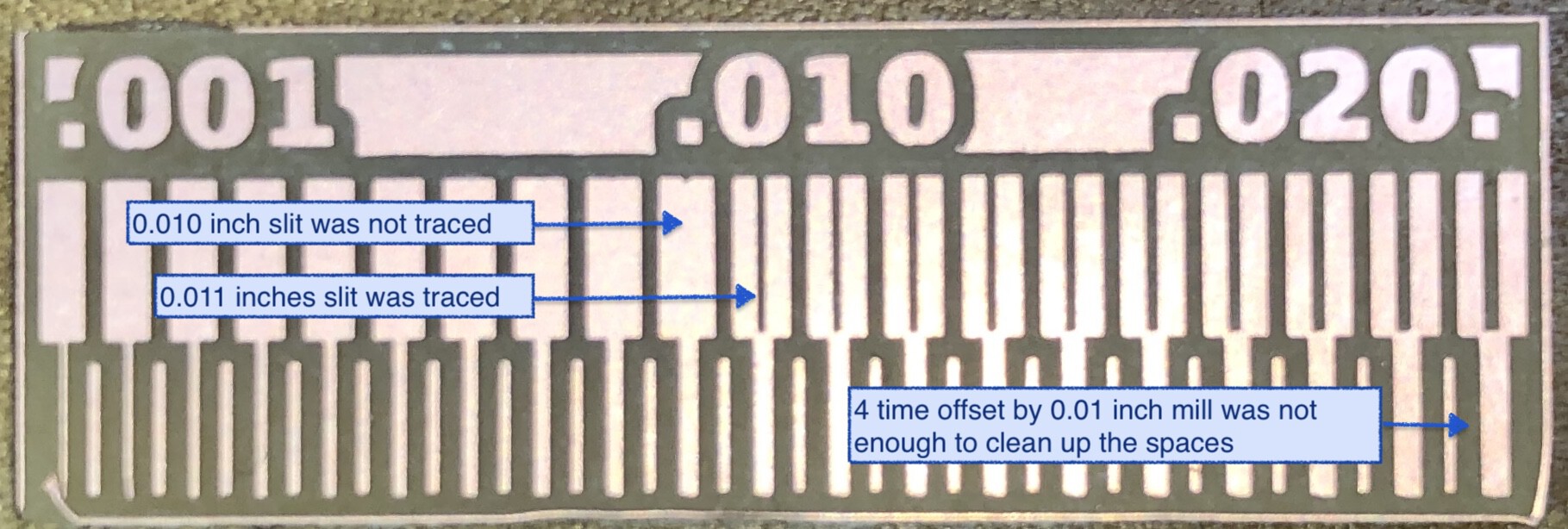
Using 0.01 inches endmill, a slit of 0.011 inches slit was traced but 0.010 inches was not.
4 times offset by 0.010 inches endmill was not enough to clean up spaces.