Applications and Implications
Week10
As mentioned on my final project page, I want to work with an irrigation system that is based on clay pot irrigation, an ancient technique that has proven to be extremely water efficient. Working this week's assignment means basically navigating through a set of questions provided in the last global lecture. For orientation, fig.01 presents a sketch of the system I intend to create; further details regarding its design and the progress of work packages will be exposed in my final project page.
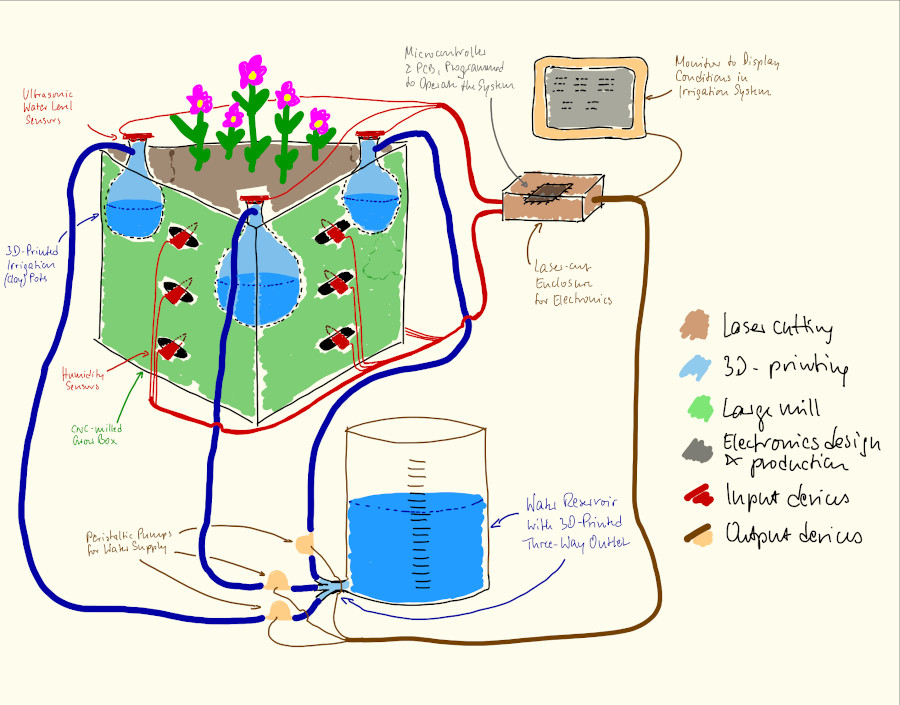
Fig.01: Concept for irrigation monitoring microcosm
What will it do?
The purpose of my final project is to design a lab-scale microcosm for the monitoring and assessment of irrigation devices. It all pivots around a triangular soil microcosm that will be equipped with
- plant material,
- 3x3 soil moisture sensors,
- 3 passively water exuding irrigation objects (vases) with
- water level sensors.
On the periphery, the system includes
- an enclosure with electronic parts, connected to a monitor,
- a 10L water reservoir with a three-way outlet that connects to
- hoses and peristaltic pumps which conduct the water from the tank to the vases.
This system is designed to test the efficiency of different (passive) irrigation objects by monitoring water consumption on one end of the supply chain, and soil humidity and plant growth on the other end. The irrigation devices may be exchanged to test different shapes and materials - or different techniques such as drip irrigation.
Who's done what beforehand?
Within the maker scene and specifically among students of the FabAcademy, irrigation has been a subject of great concern over the years. The search engine on the FabAcademy website brought 120 hits on "irrigation" between 2016 and 2019 alone. Most of those final projects integrate irrigation tools but rather focus on the growth system, e.g. as a controlled greenhouse, the famous Aquapioneers project, our very own Dima's Grow It Yourself greenhouse, a growth system for mushrooms, an installation for balconies, an integrated system for Smart Farming, the ornamental installations of Hanging Gardens and the so-called Aeroponics, and two more variations of integrated aquaponic systems from AKGEC and SZOIL FabLabs. Other related projects make their approaches towards water monitoring, rainwater harvesting, and a watering machine. Particular projects that include specifically interesting elements for my monitoring system include a silicon-sealed outdoor sensor, a template for my electronics casing, a DIY valve and a bell siphon. Finally, regarding the system integration and networking, I find the projects on fog harvest monitoring and IoT for agriculture very helpful and inspiring.
Apart from our Fab community, I consider our Rhine-Waal University's project on smart agriculture and commercial, large scale irrigation monitoring systems as related, such as the SignalFire or the ADCON solutions. Innovation labs on small scale irrigation such as ILSSI focus rather on feasibility and application of irrigation systems for small farms in underprivileged regions of the world.
Clay pot printing, too, has already reached commercial status, companies such as 3D Potter offer not the product, but the printer! Using 3D-printed clay pots for irrigation, though, is still new. Besides our Lima pioneer project, the only reference I found produces irrigation clay pots in the traditional way.
What will you design?
My personal input starts with the irrigation pots. For starters and simplicity, I will use PLA prints with shallow walls to allow a defined amount of water to exude. The subsequent experimental part shall cover the testing of different shapes and the mixing (ratios and techniques) of clay with organic material to reach a reproduceable quality. Another small 3D-printed object will most probably be the three-way dispenser from the water tank to the pots.
As for the casings, I will design the triangluar growth bed to be milled with our large CNC mill and the enclosure for the electronics to be laser-cut from plywood with flexible curved edges. Both designs will be made in Fusion360.
In the field of electronics, I will design a PCB that provides enough pinouts to receive data from at least 9 moisture and 3 water level sensors, plus another PCB to cover the operation of the three peristaltic pumps and the monitor. Operation of the latter may need to be switched to another board, depending on the heat produced by the pump controllers. Programming those boards requires Arduino coding of various input and output devices.
What materials and components will be used?
- In the field of 3D printing, my prototype will be made entirely of PLA; experiments with clay must be postponed to a later moment in time when the time pressure has eased somewhat.
- For the grow bed container I will use ordinary 15mm OSB
- The electronics casing will be made of 3mm MDF
- The moisture sensors are capacitive
- Water levels within the pots are detected with ultrasonic sensors
- The PCB will be milled as a ground board
Where will they come from?
See table below.
How much will they cost?
Component | Price (total) | Supplier |
10 moisture sensors | EUR 21,98 | AZ-Delivery |
3 ultrasonic water level sensors | EUR 6,29 | AZ-Delivery |
3 peristaltic pumps | EUR 35,67 | Yosoo |
5m silicon hose | EUR 10,50 | Technische Ausstattung Fritsch |
approx. 1.5kg of PLA filament 2.85mm | EUR 33,88 | ICE Filaments |
15mm OSB sheet (205cm x 62,5cm) | EUR 8,31 | OBI |
Soil | EUR 8,99 | OBI |
3mm MDF sheet (244cm x 122cm) | EUR 10,50 | Hornbach |
electronics: details tba | EUR 20,00 | Conrad |
power supply: details tba | EUR 20,00 | Conrad |
small parts and consumables (approx.) | EUR 20,00 | Conrad |
total | EUR 196,12 |
What parts and systems will be made?
- Irrigation pots
- Three-way dispenser from water tank
- Grow box
- Electronics casing
- PCB
- Arduino code
What processes will be used?
- 2D and 3D design in Fusion360 and Rhino
- laser cutting on Epilog Fusion
- 3D printing on Ultimaker S5
- milling of press-fit grow box on large format CNC mill
- PCB design in Autodesk Eagle
- PCB milling on Roland mill
- PCB soldering and progamming
- Integration and calibration of sensors, pumps and monitor
What questions need to be answered?
Regarding the project success, my most pressing questions are obviously: how does the system perform in the long run? Is it stable enough, is the soldering flawless to allow for a long-term usage in class?
But apart from those rather general inquiries, some more detailed questions are of concern:
- could the system's monitoring device be expanded into a 3D model for moisture of the entire soil body?
- If so: do the 9 sensors suffice or are more sensors necessary in the center of the microcosm?
- If so: may those sensors be installed without protection or will they require e.g. silicon sealing?
- How much heat will the MOSFETs generate inside the electronics casing? Would the heat require ventilation?
How will it be evaluated?
Naturally, the evaluation of the microcosm will be based upon its functionality. This means that the sensor network should work properly and deliver plausible data to the monitor, the pumps should bring water to the pots once their fillings reaches critical levels, and all the containers, hoses and pumps should be water-tight. In addition, after the initial testing and calibration phase is finished, the subsequent test-runs in the system development will assess whether the data between water level, soil moisture, and plant growth correspond and actually make sense. Eventually, the microcosm shall deliver reliable information on irrigation efficiency, expressed as biomass per volume water.