Assignment
INDIVIDUAL ASSIGNMENT:
Design and produce something with a digital fabrication process not covered in another assignment.
Composite materials
So what is composit ..? A composite is a material made from two or more different materials that, when combined, are stronger than those individual materials by themselves.What I did
- Designed mold for making composite material
- Made composite mobileholder using linen and resin
- Learned uses of composite materials
Composite material
A composite material (also called a composition material or shortened to composite, which is the common name) is a material made from two or more constituent materials with significantly different physical or chemical properties that, when combined, produce a material with characteristics different from the individual components. The individual components remain separate and distinct within the finished structure, differentiating composites from mixtures and solid solutions.
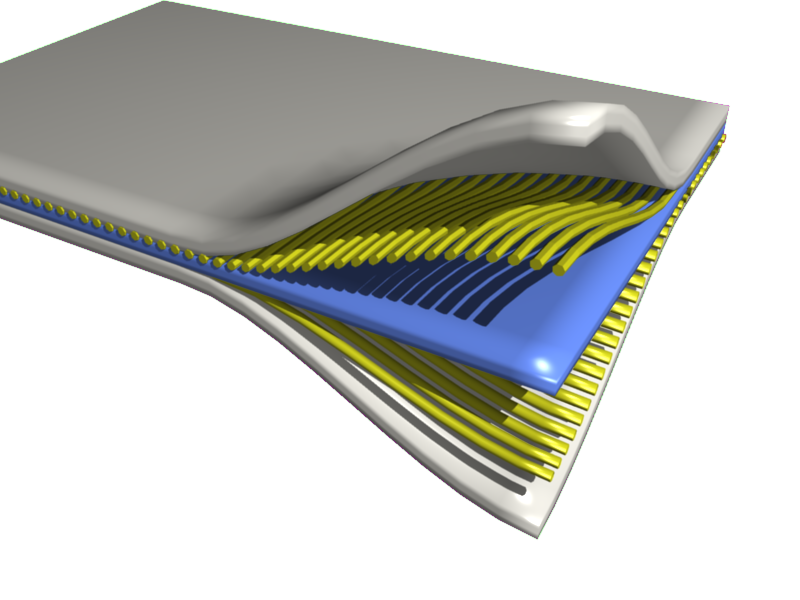
source wiki
Composite material using Resin & Linen
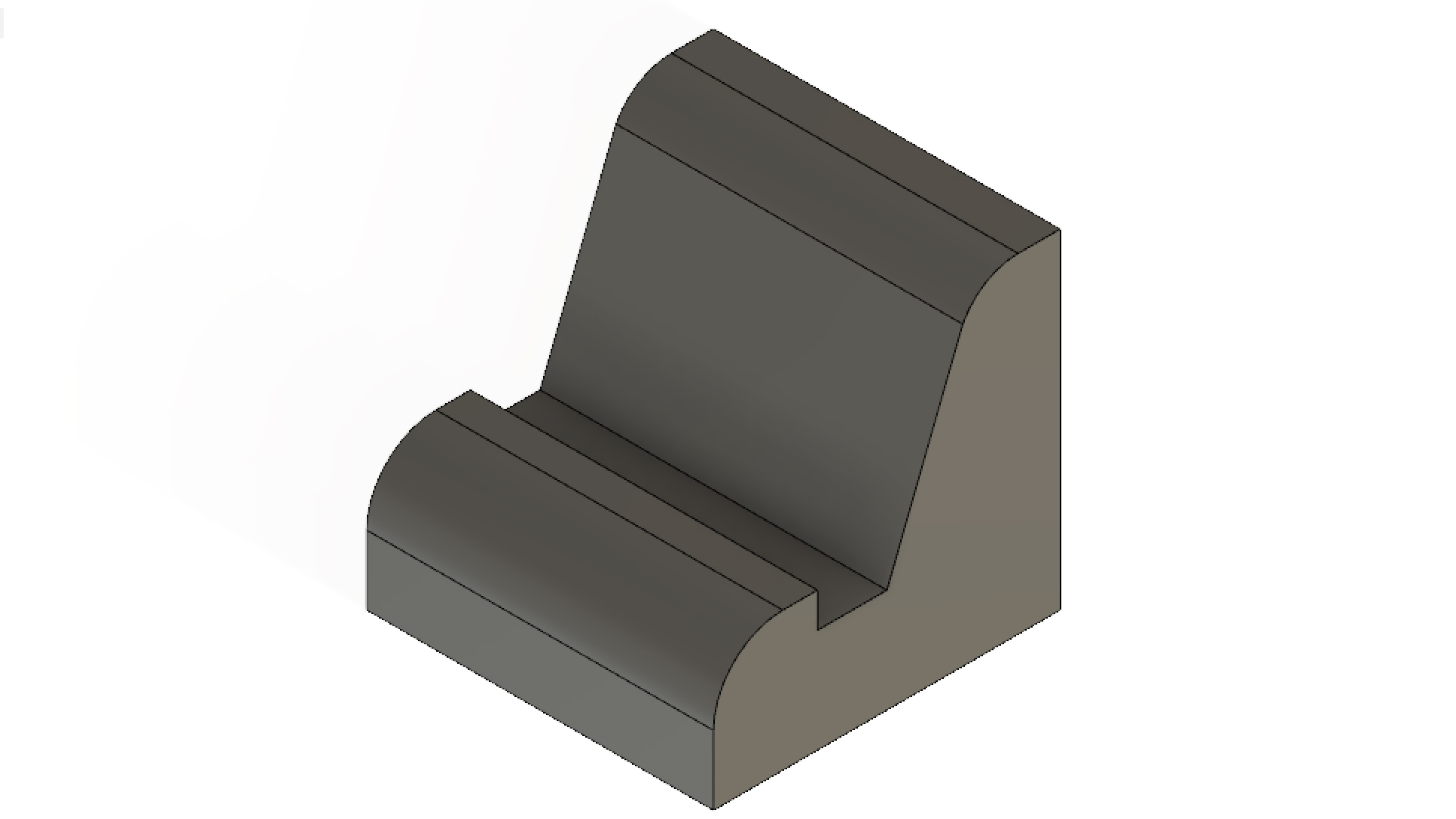
For this week assignment I decided to make a mobile holder using coposite material. I made model using fusion 360
Download the design file
Download f3d file here
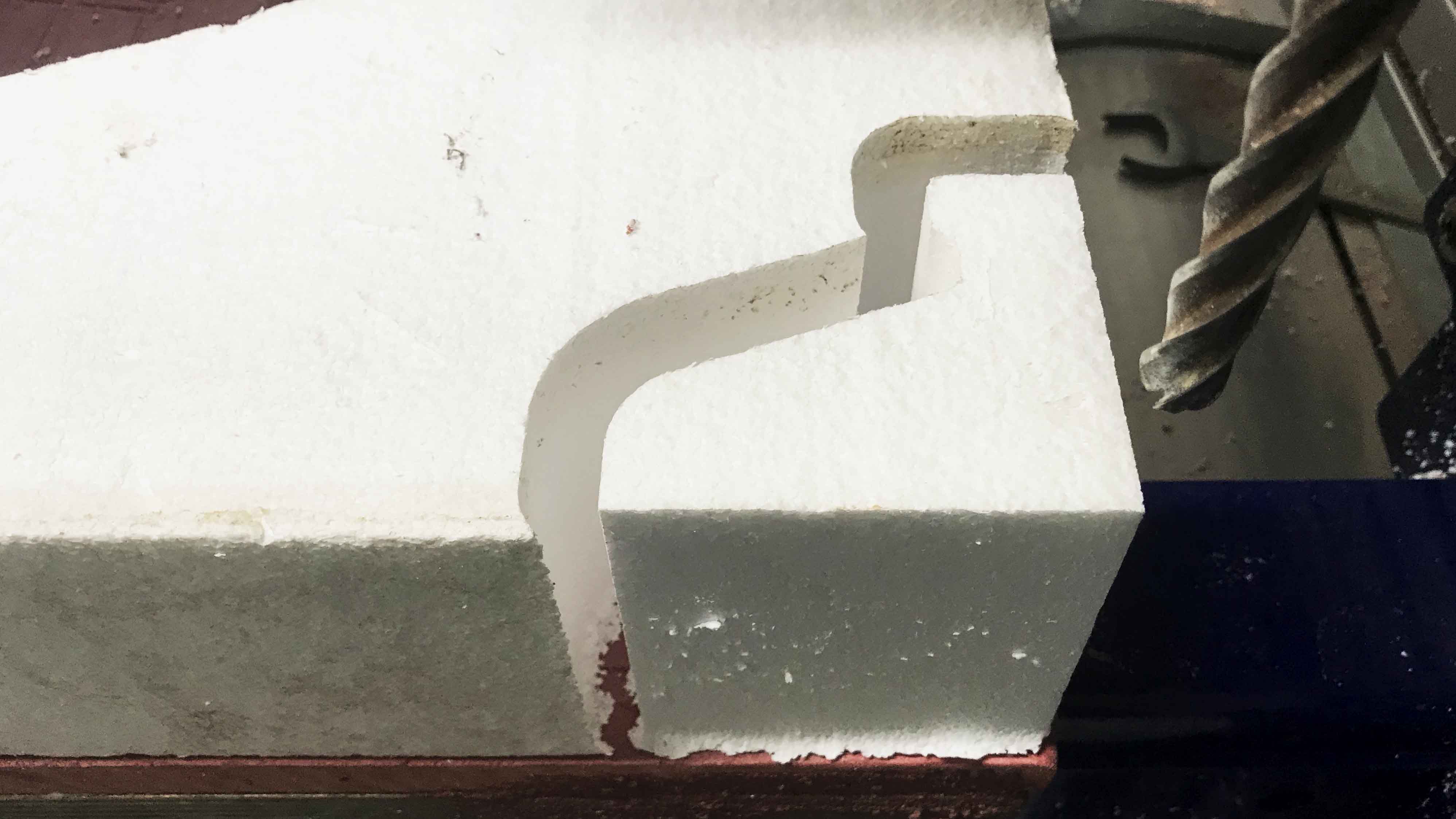
I used thermocol block for making the mold.
Instead of using a STL(3D) format I uesd a DXF(2D) file which reduced the macinig time to less than 10 minutes. Milled 100mm thick thermocol in shop boat.
Since the I used 100m block I checked for the longest bit available in my lab. I found 1/2" ball end
bit. Since I used this large bit, the sharpe edges become round.
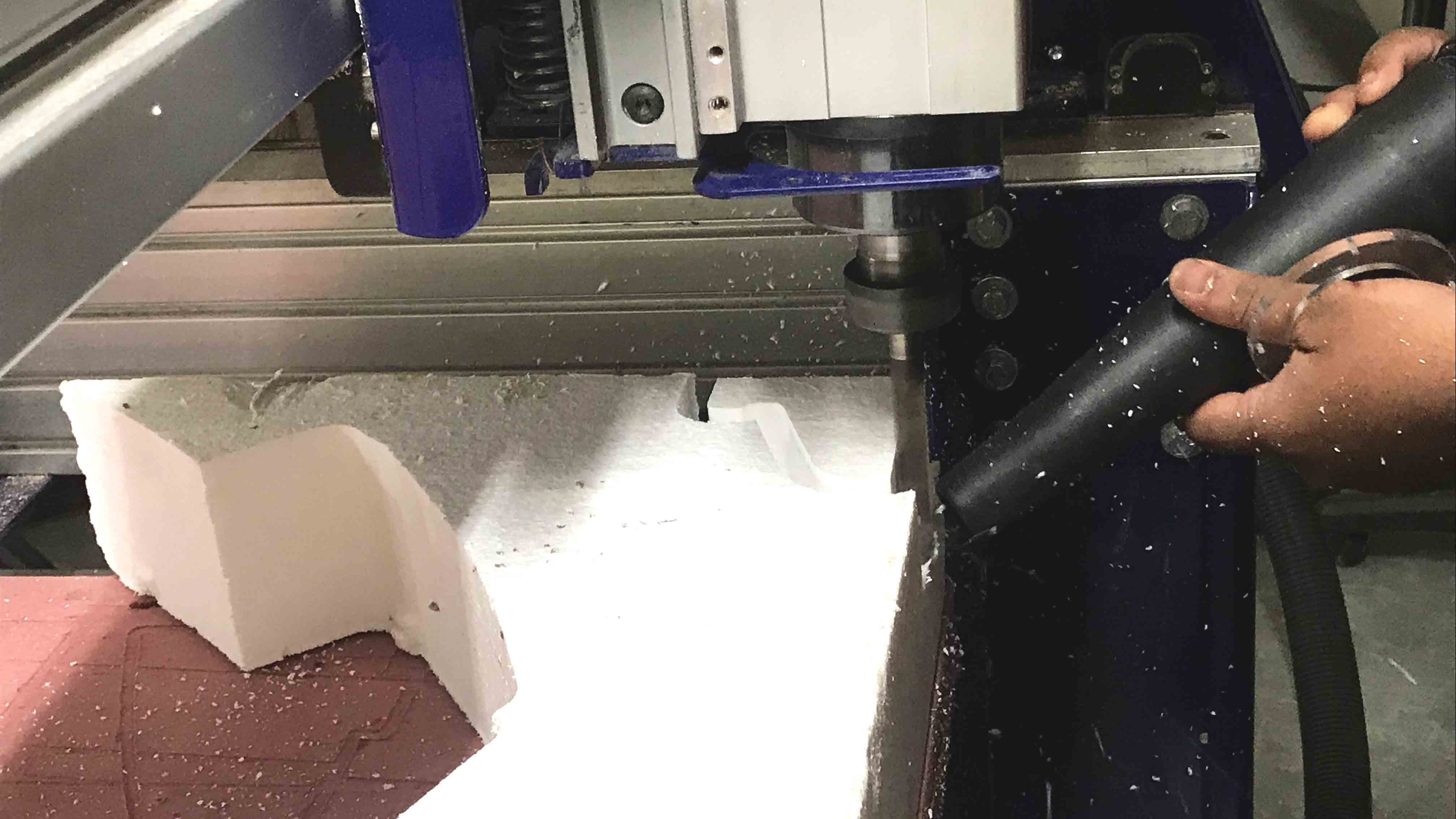
I had to remove the dust skirt so that I can mill 100 mm block. I used vaccum cleaner to remove the flying debris
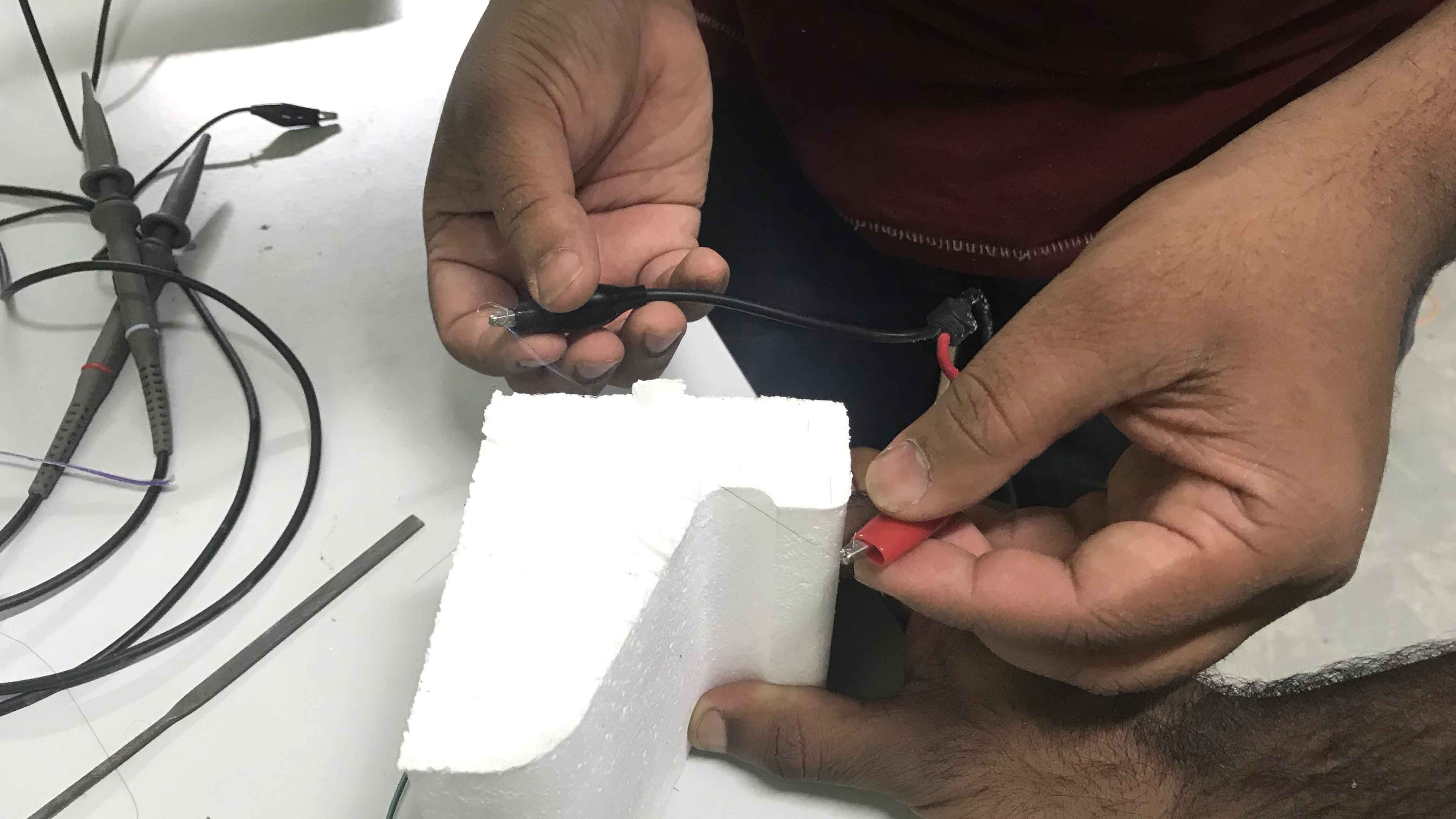
Because of the ball end bit final layer was not removed properly. First I tried to remove that layer using heated wire by connecting it to power supply. The surface finish was very poor.
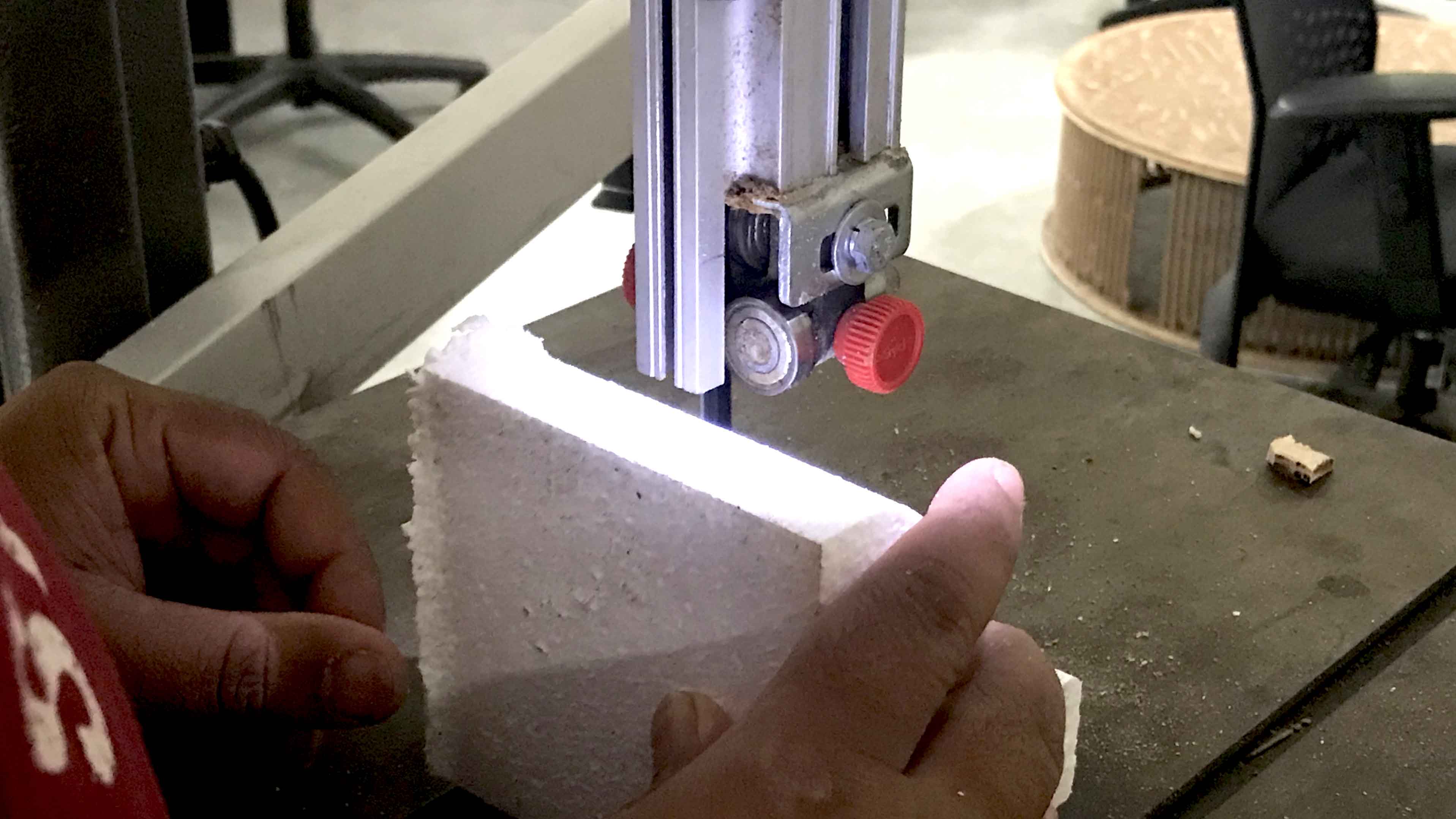
Then I tried to cut the block using band saw. But the size of the block is larger than the band saw
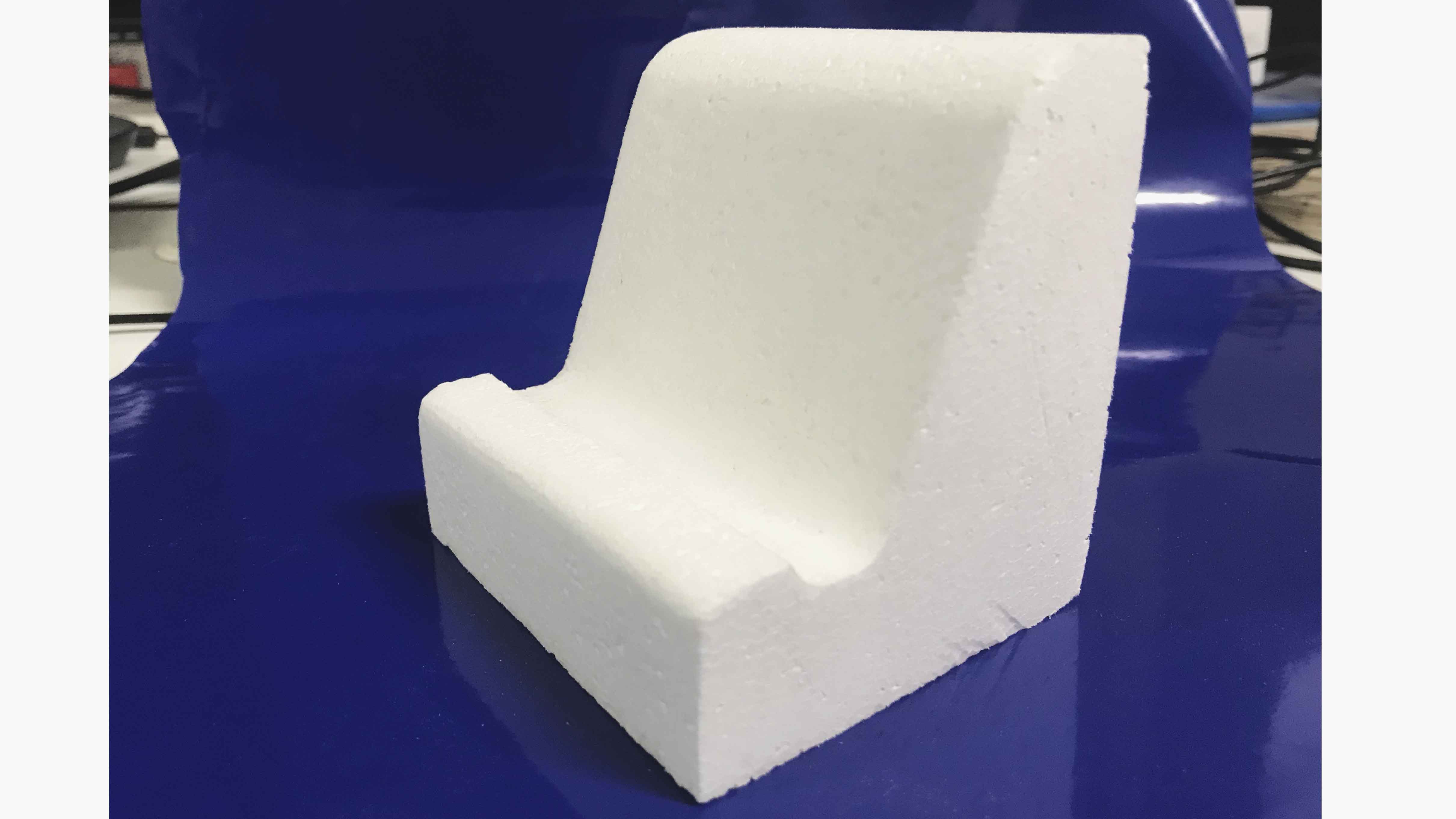
Later I cut the excess material using hacksaw blade and finished the surface using sand paper of 120 grit
Material used
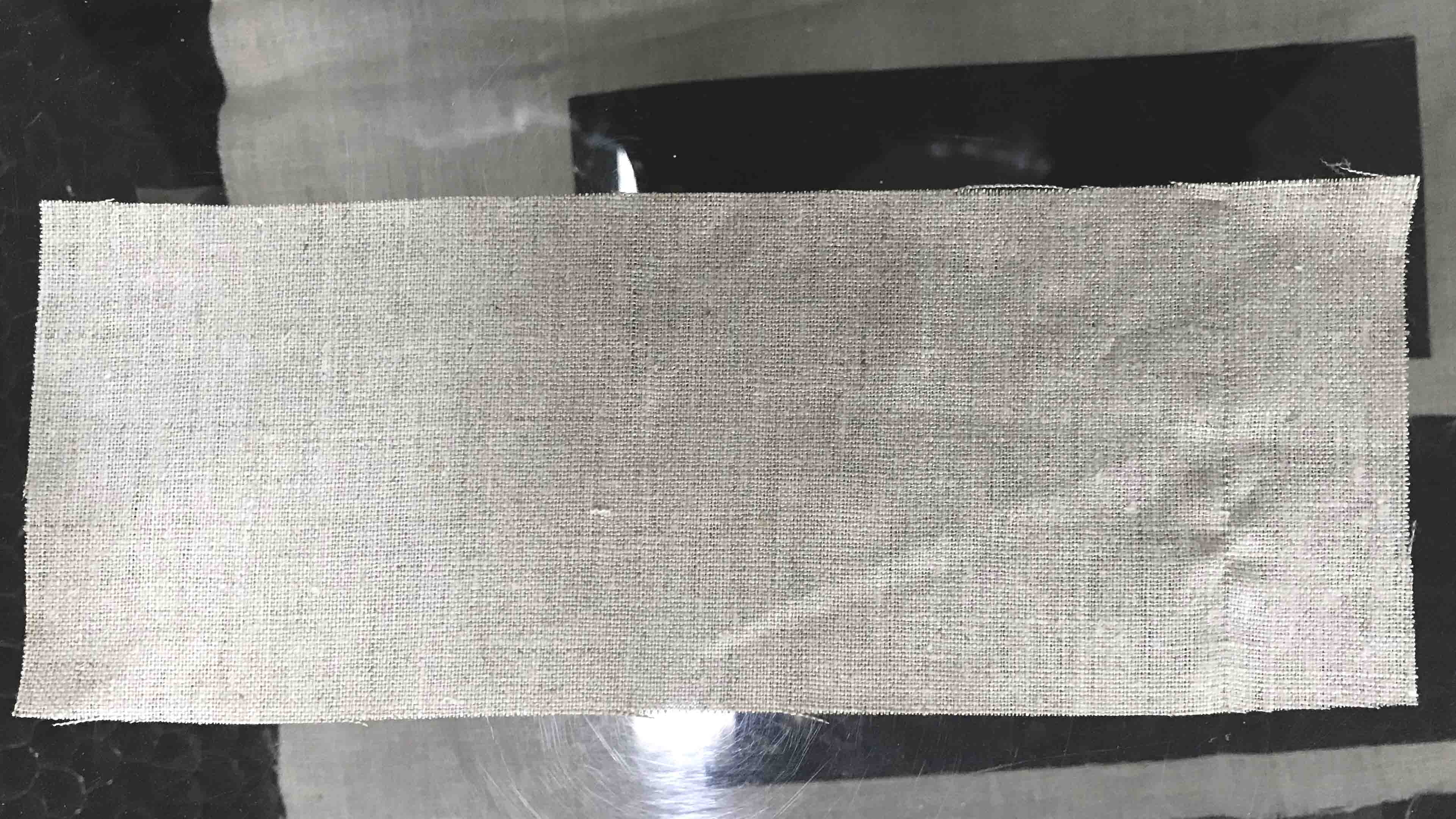
Linen fabric is used as composite
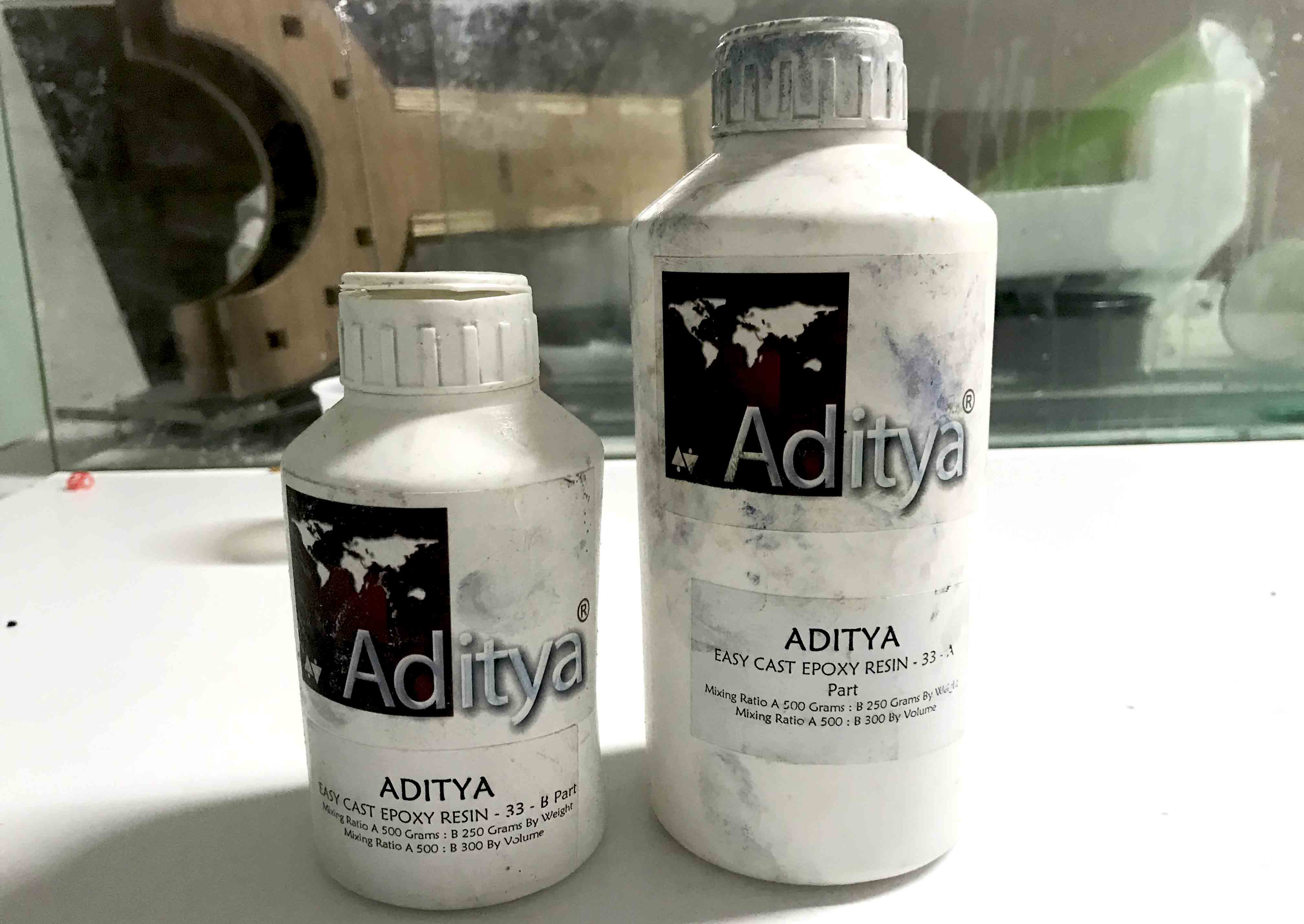
Epoxy resin is used for making the composite . The ratio is 1:2 by weight or 2:3 by volume
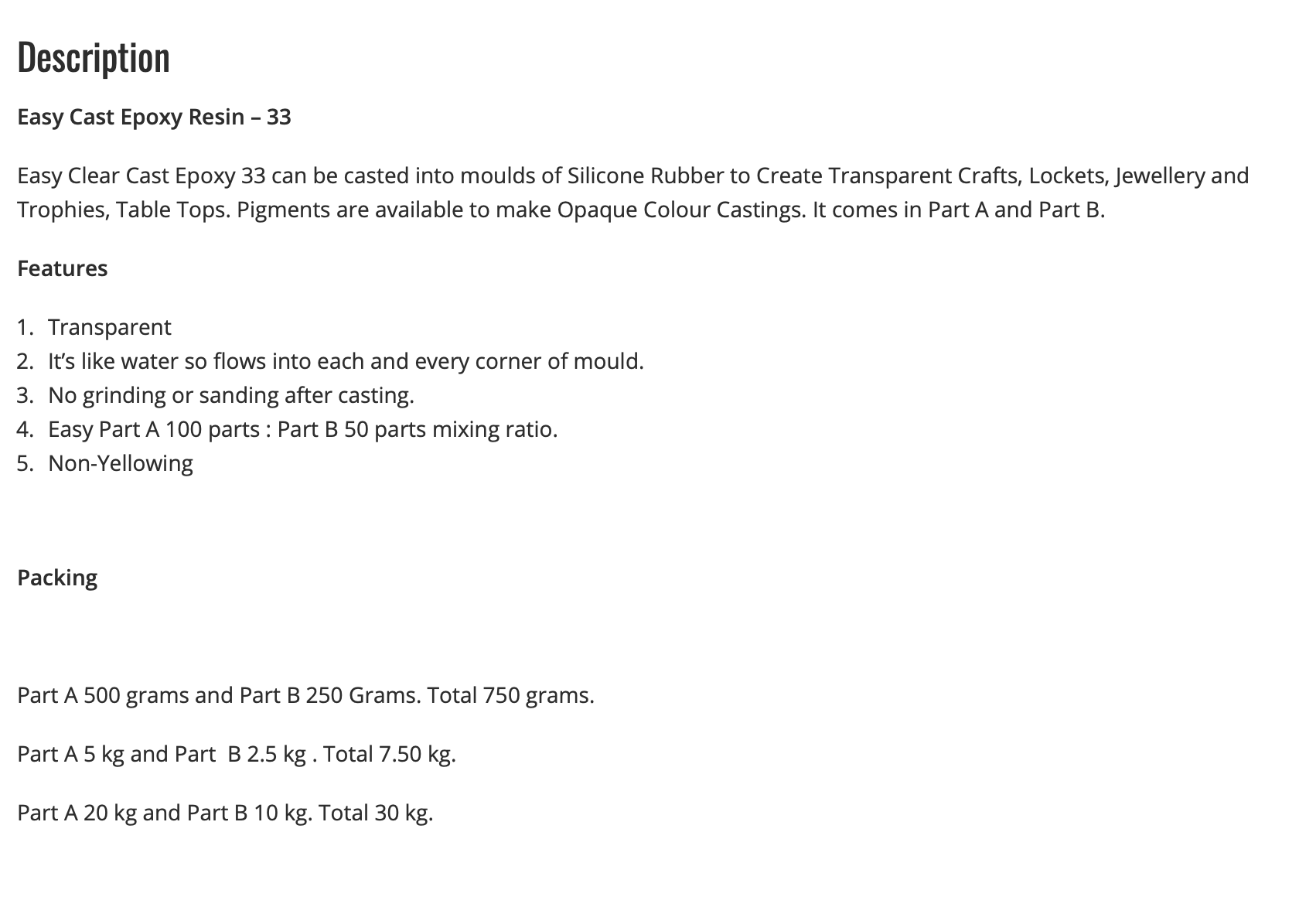
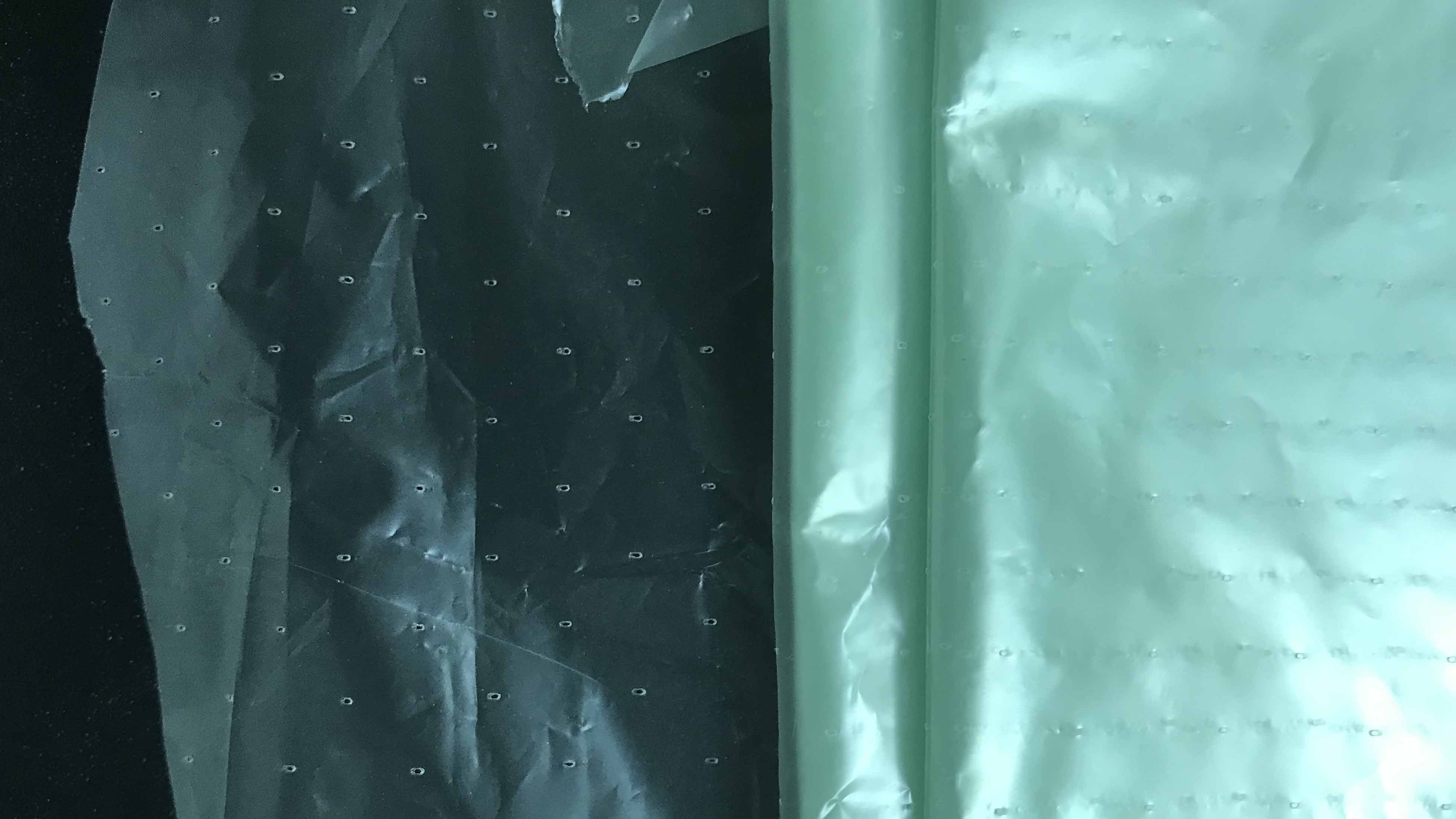
Bleed is used to cover the composite. It is a plastic film with bleed holes when vaccum is applied, the excess resin will flow throgh this bleed holes
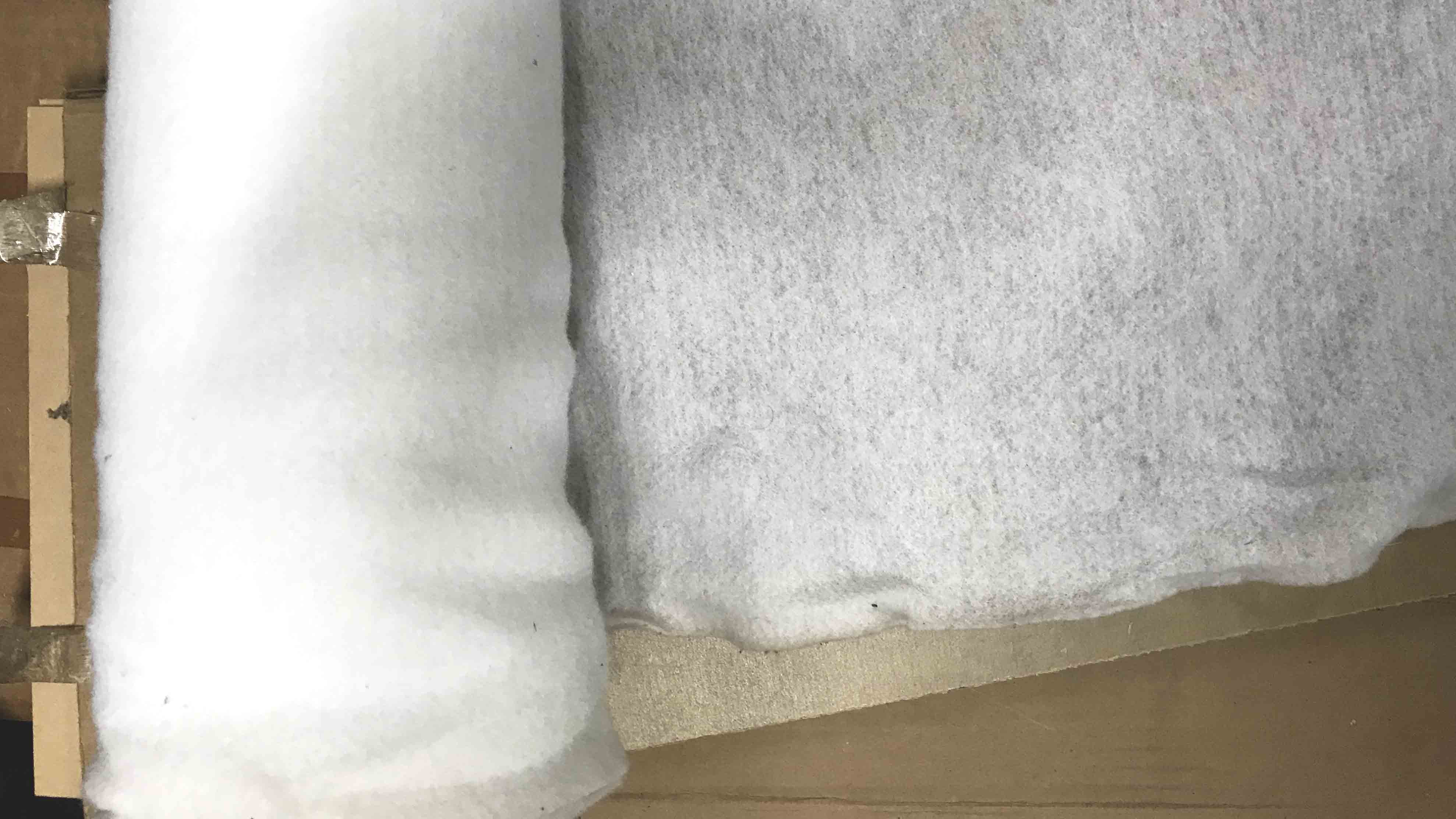
Breather is synthetic fibre used to release the mould
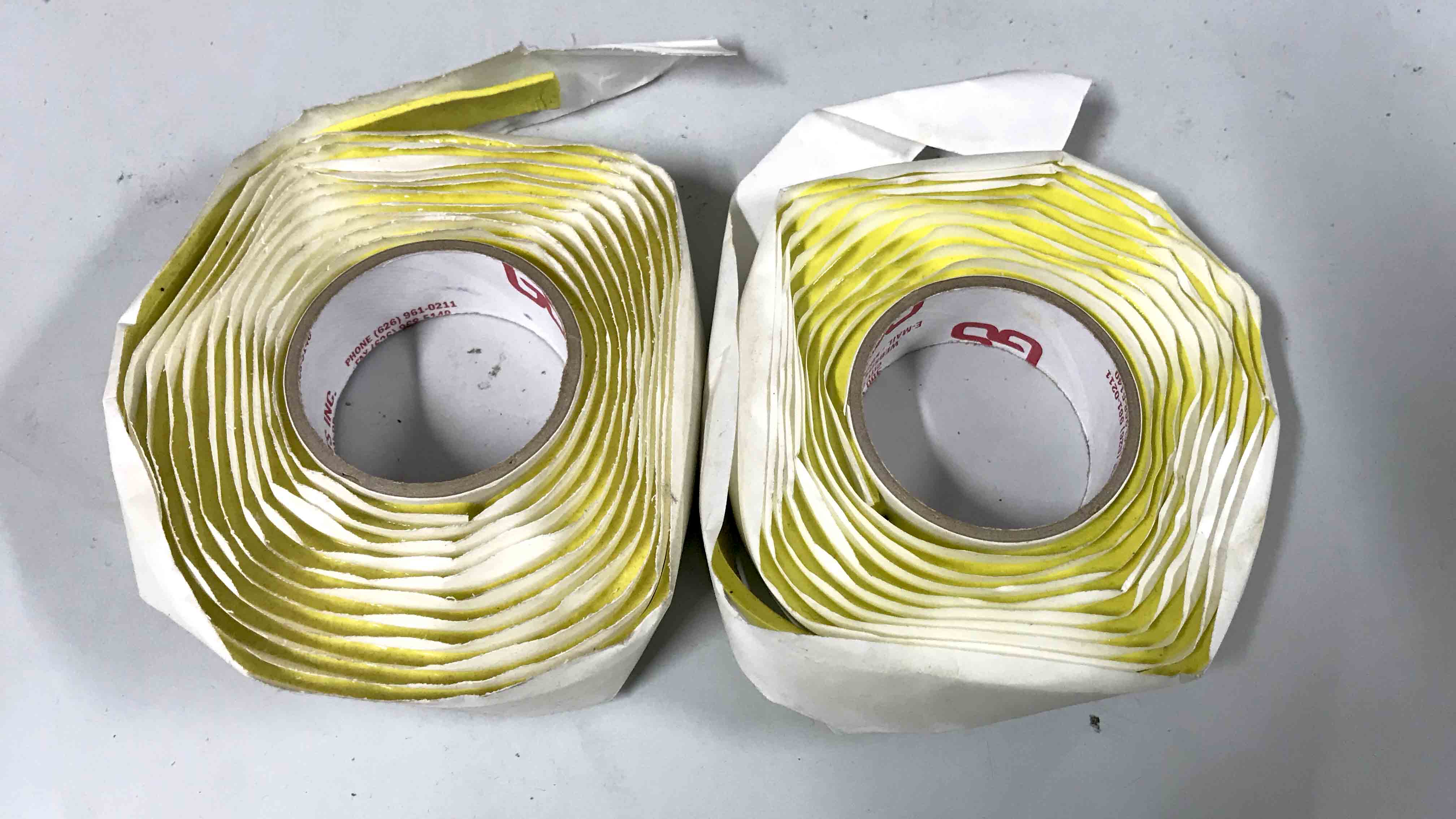
Tacky tape is a butyl-based vacuum bag sealant giving high elasticity and tenacity. It has exceptional sealant properties, eliminating the risk of imperfect seals often found in the initial phases of vacuum bag application, so improving the vacuum efficiency and reducing labour. It is suitable for polyester, vinyl ester and epoxy laminating systems.
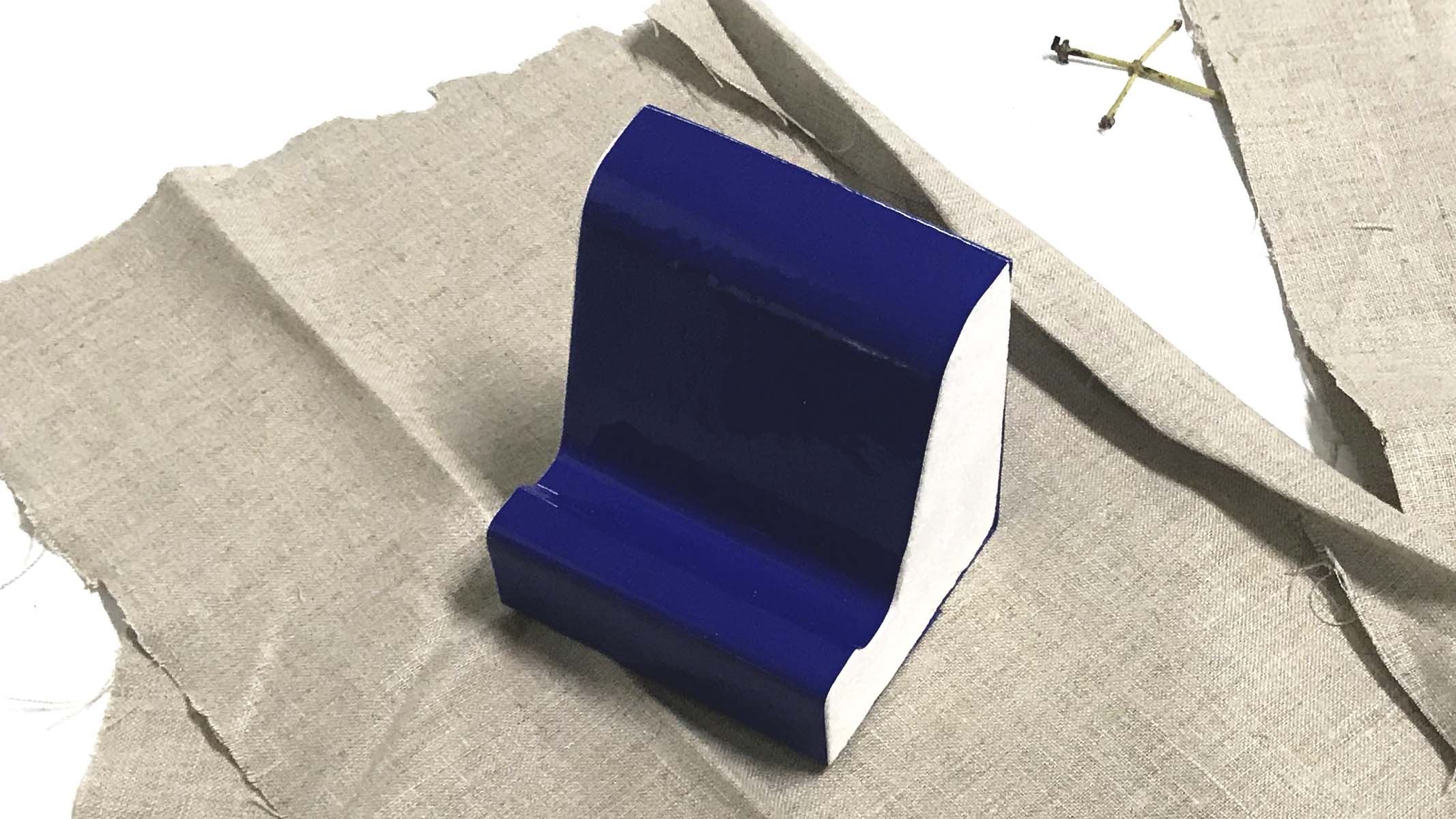
To release the compsite from the mould I used a vinyl sheet. Otherwise the thermocol will absorb the resin and once it is dried, it will be difficult to remove the mold.
both hands and polyethlene sheet to protect your clothes. It is very difficult to remove the resin from clothes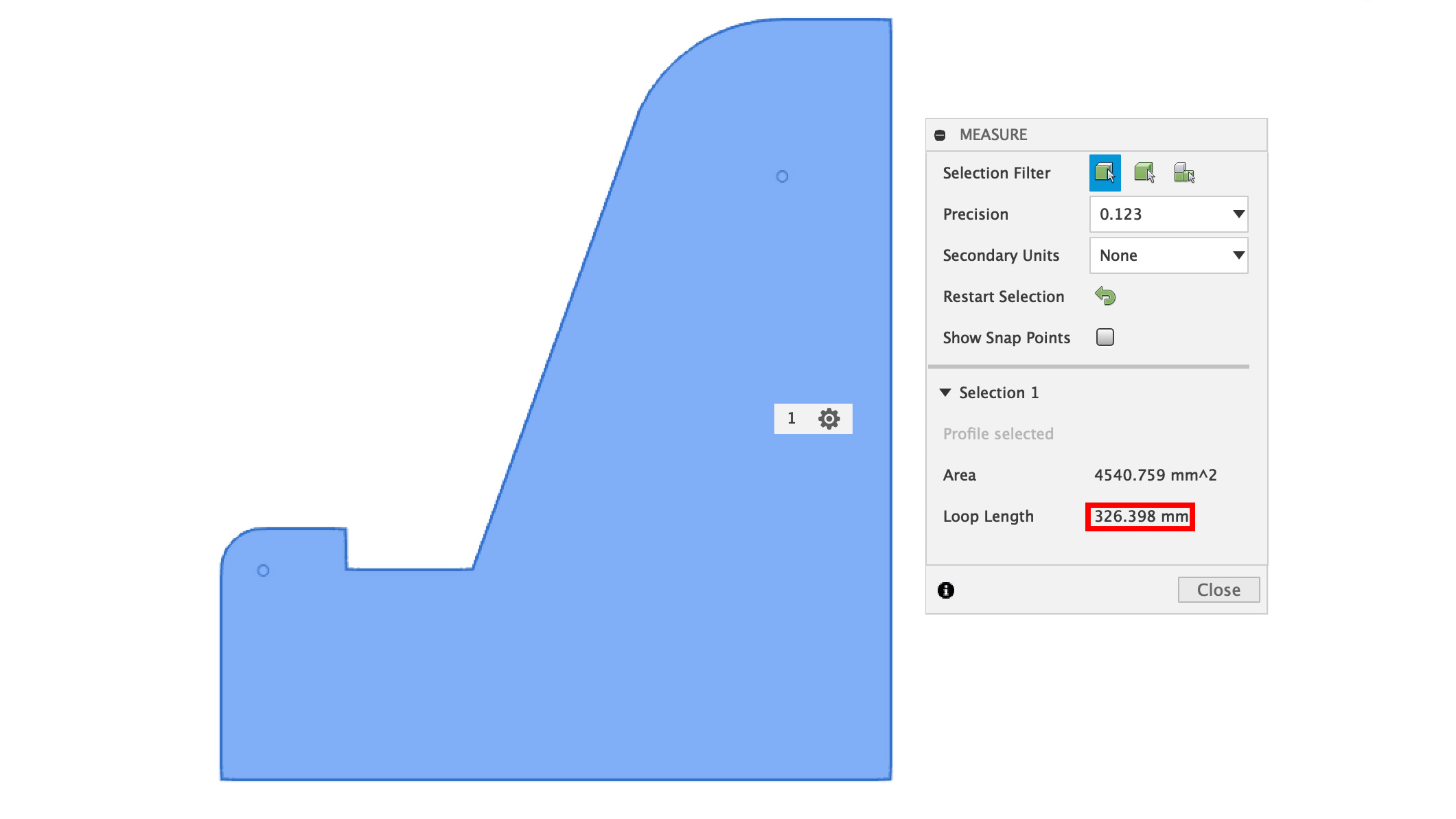
I used the INSERT >> MEASURE option in Fusion 360 to measure the circumfrence of the shape
Laser cutting linen
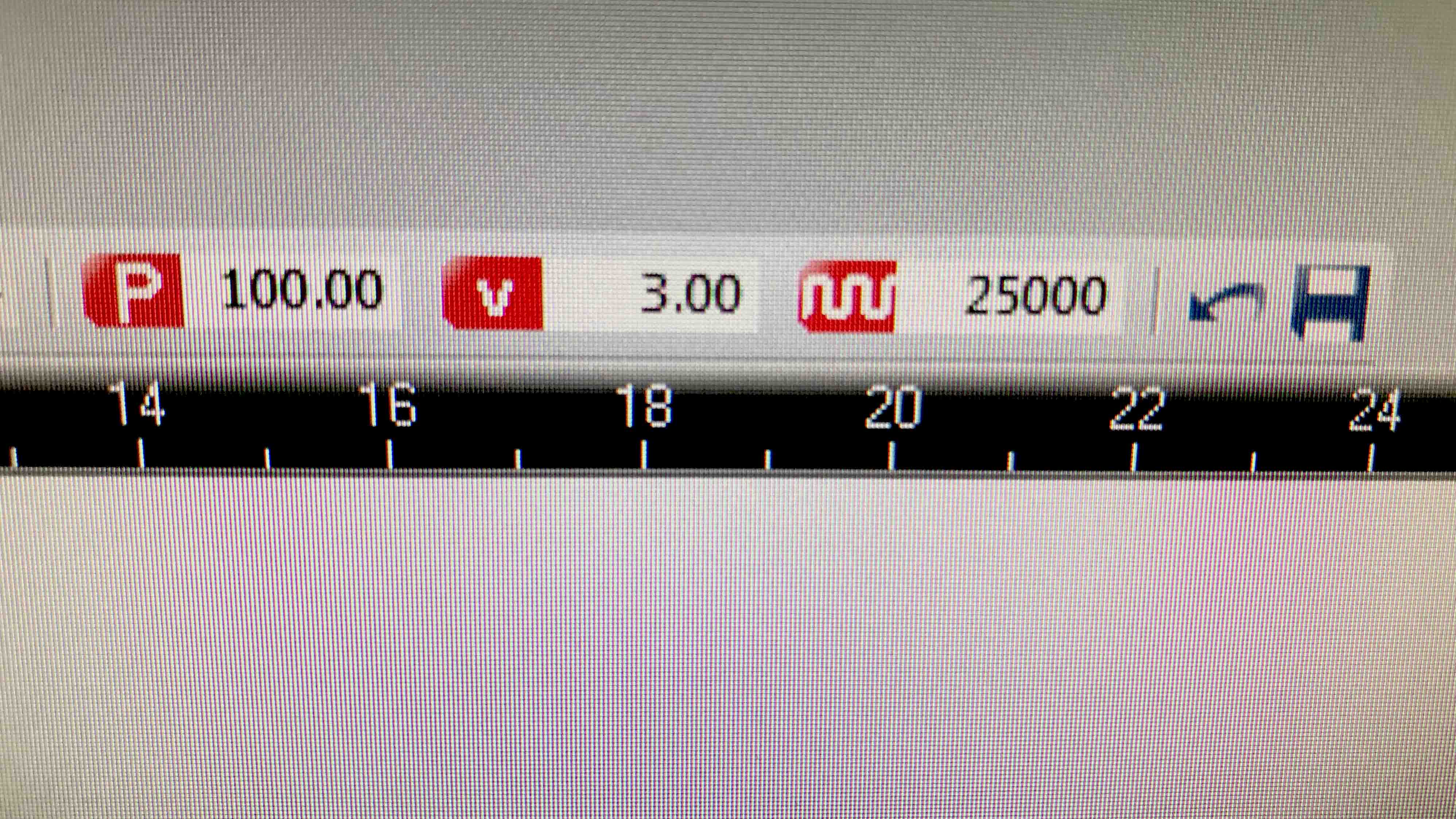
After trial and error for some time I found optimised cutting parameters for the fabric
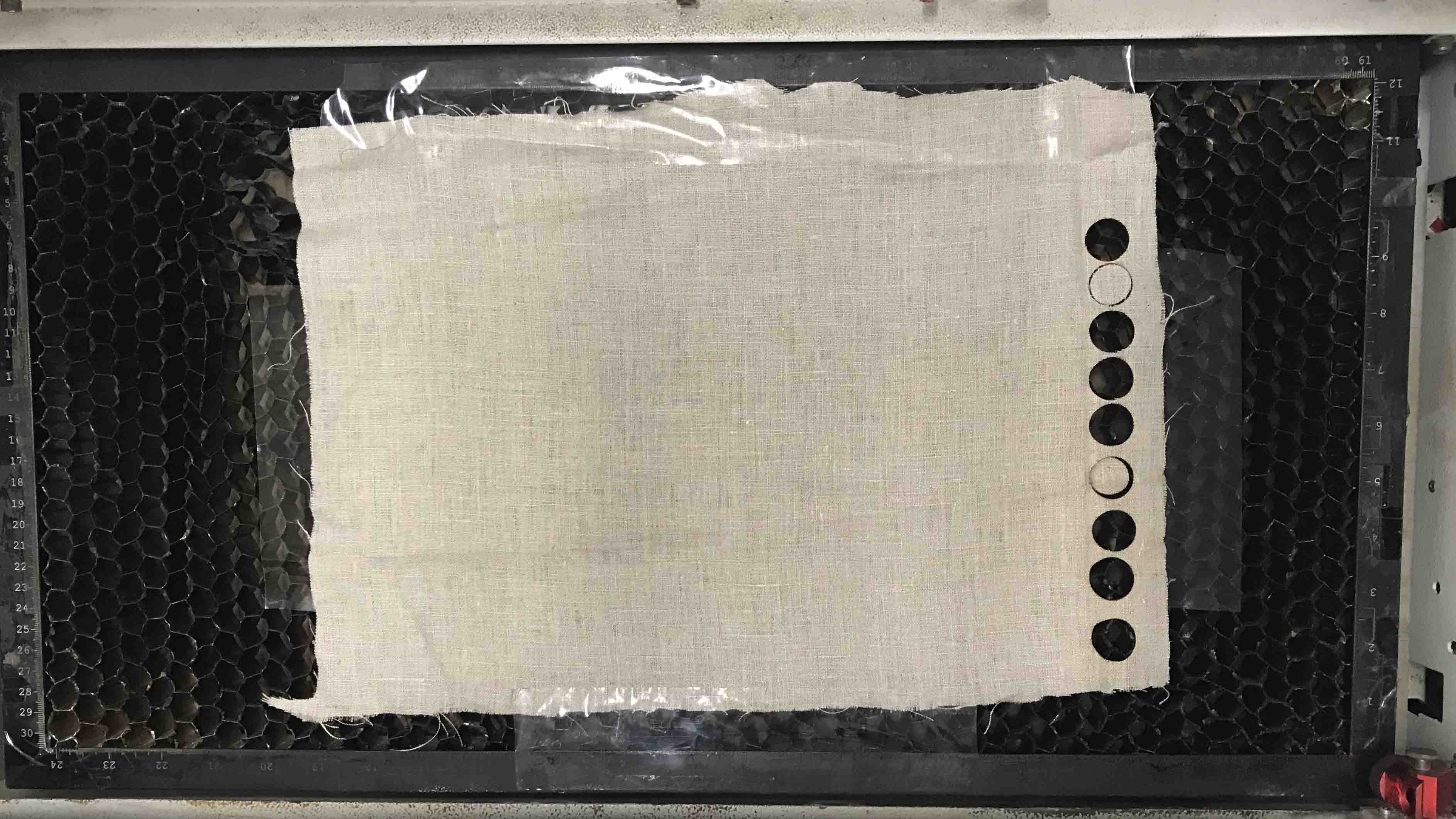
Keeping the fabric on the laser bed was very difficult tast and we nether had an iron box to iron the material. I used cello tape to keep the fabric in position. It is possible to cut over the cellotape.
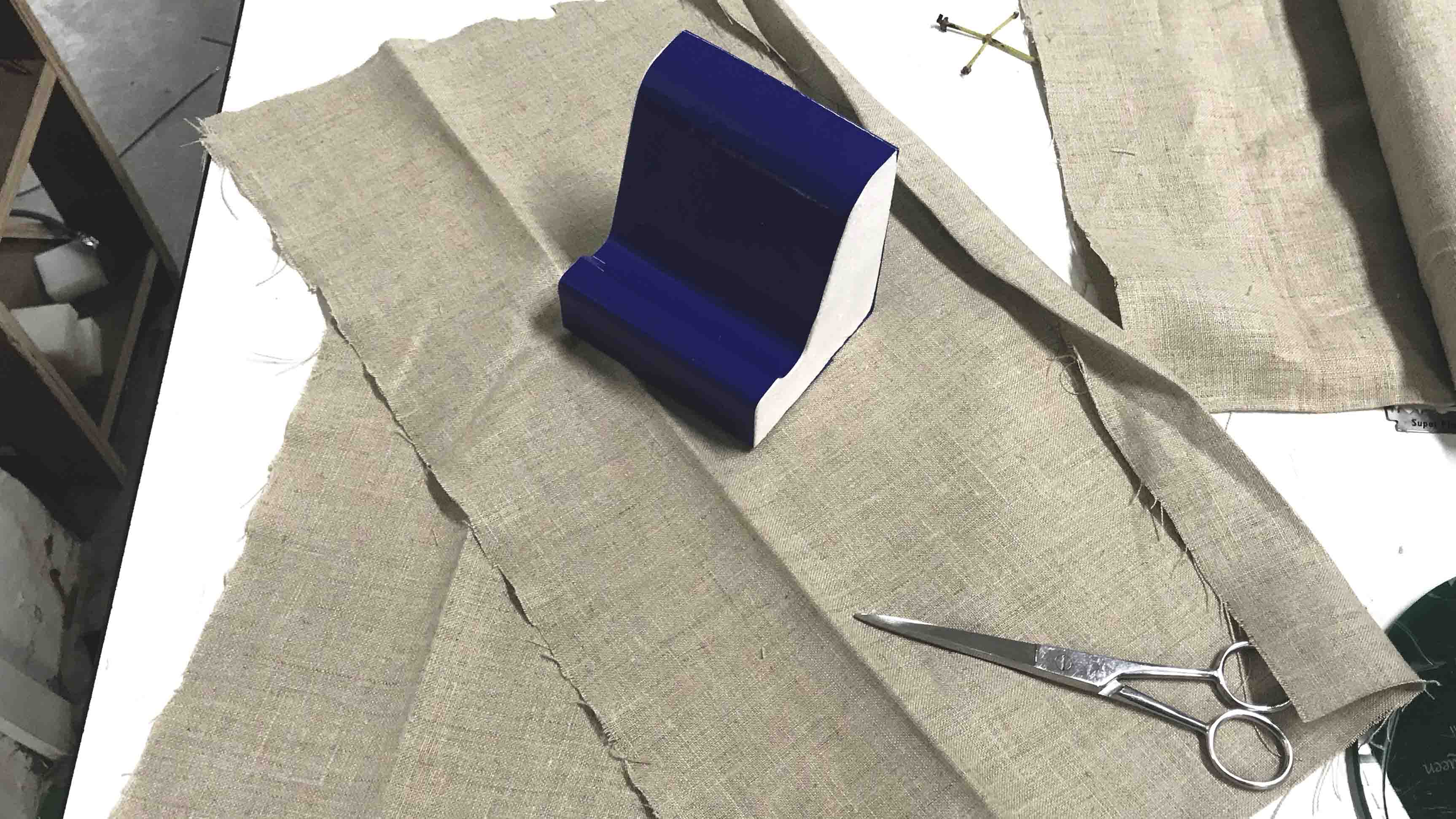
I have prepared the mold for preparing the composite. Decided to use four layers of fabric.
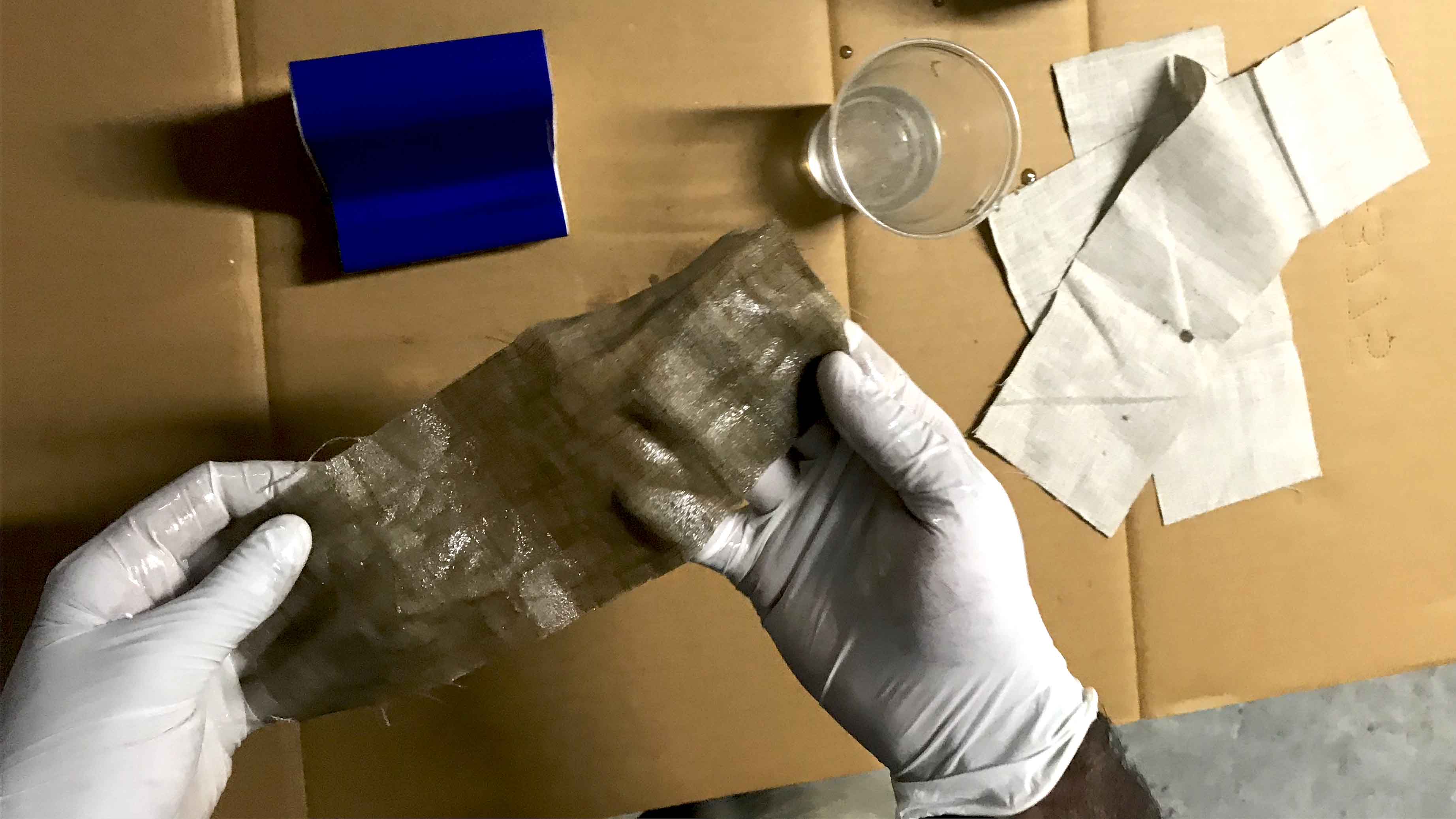
Mixed the resin with the ratio 1:2 by weight. Soaked the linen strips in the resin. Allways use gloves on both hands and use protection for your clothes. It is very difficult to remove the resin from clothes
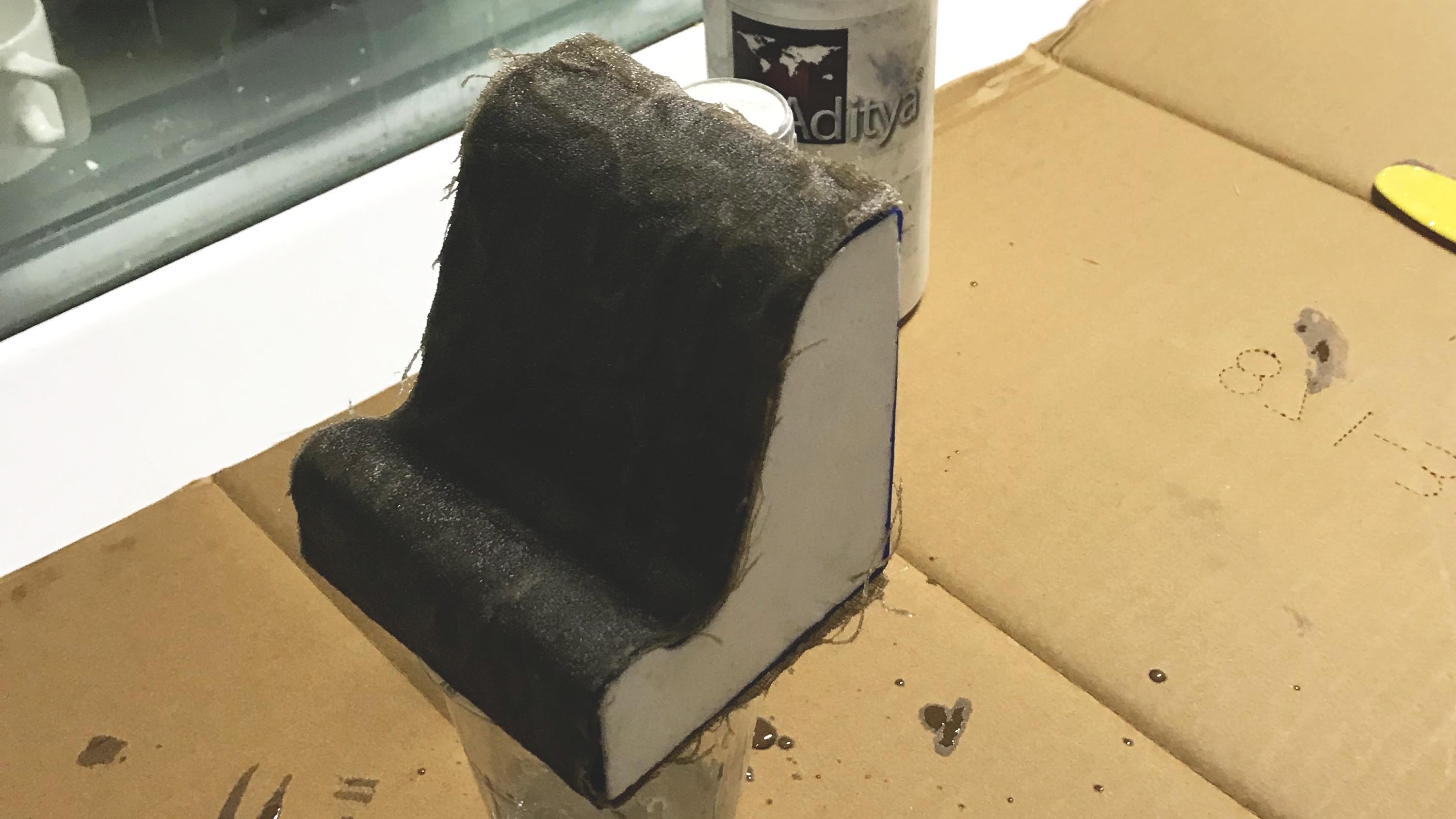
Carefully add each layer to the mold. Always wring the fabric to remove the excess resin.
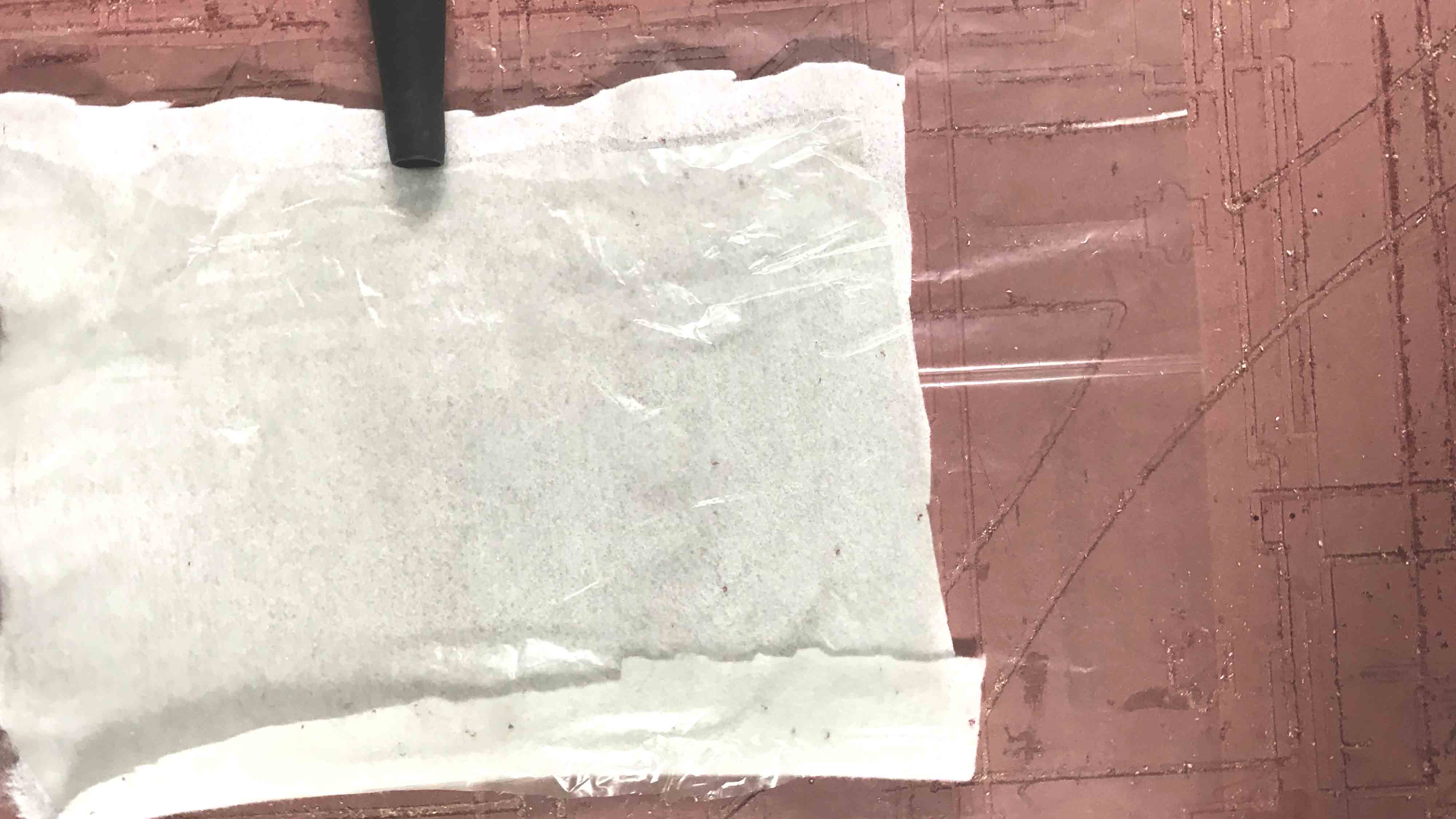
Prepare the vaccum bag. First cut the vaccum bag at desired size, then cut the bleeder and breather which should be smaller than the vaccun bag. Stick the tape on all side and make sure that it is air tight.
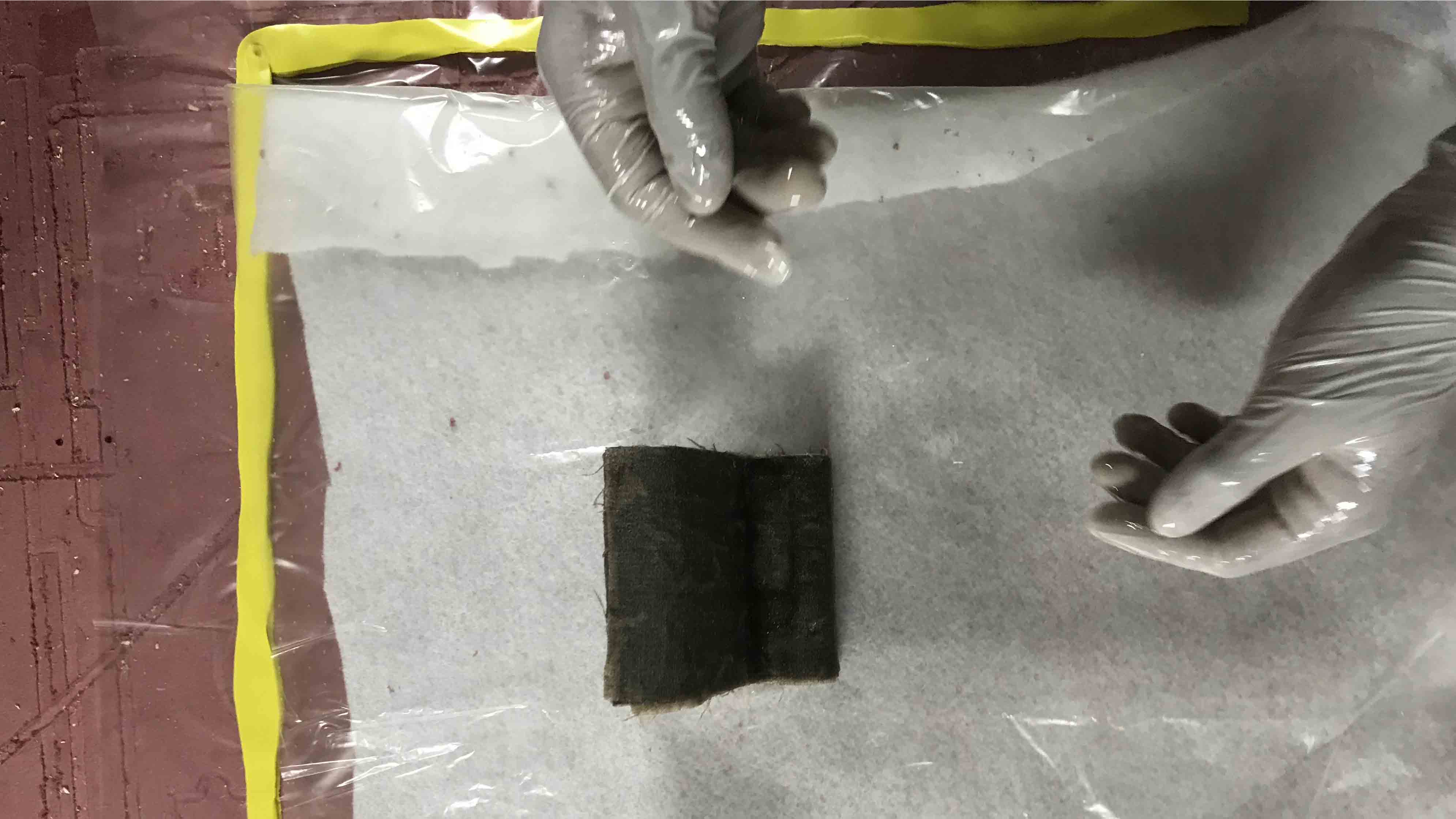
Place the mold on the center
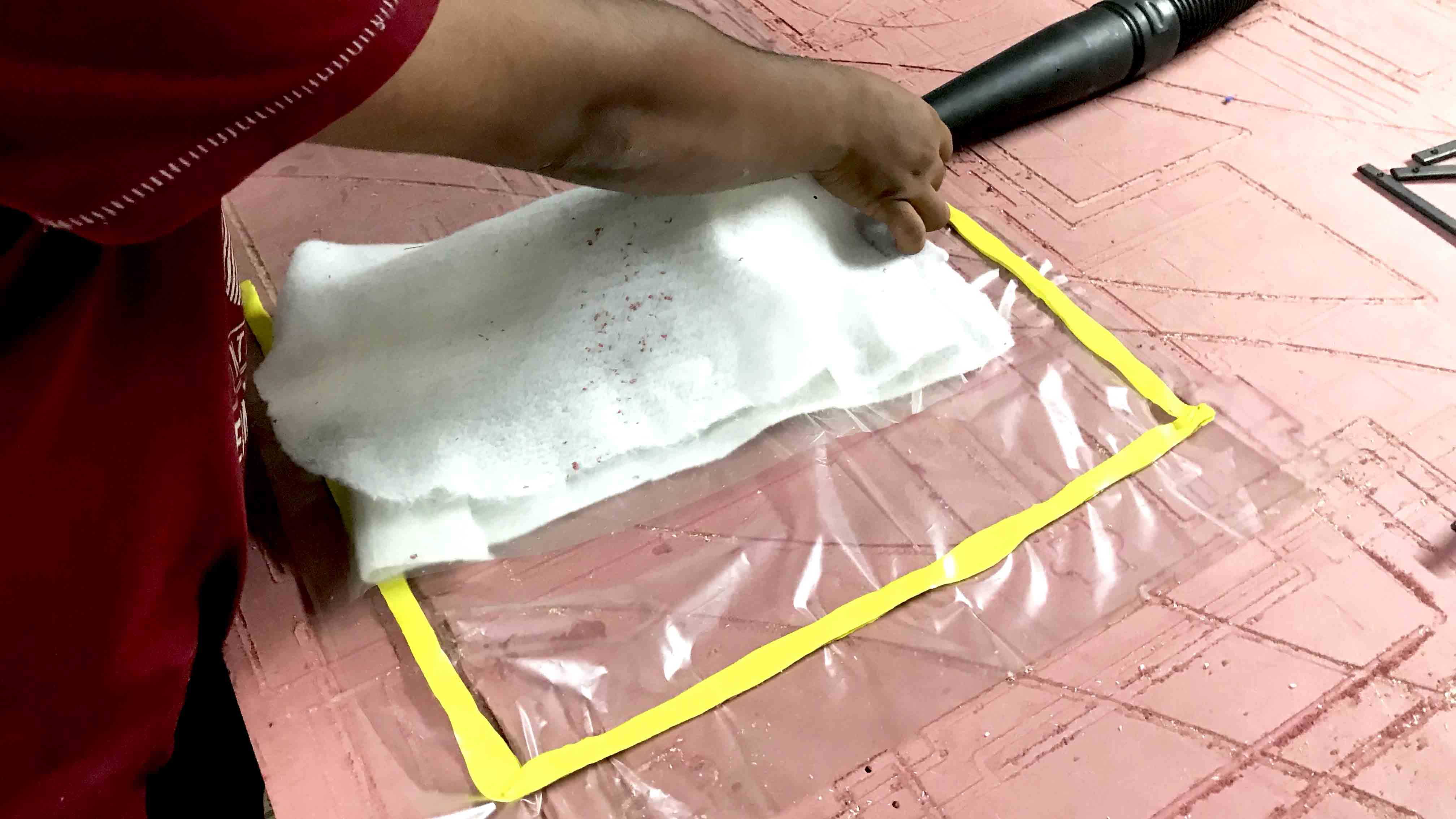
First cover the mold with bleed film and try to avoid air bubbles in between them
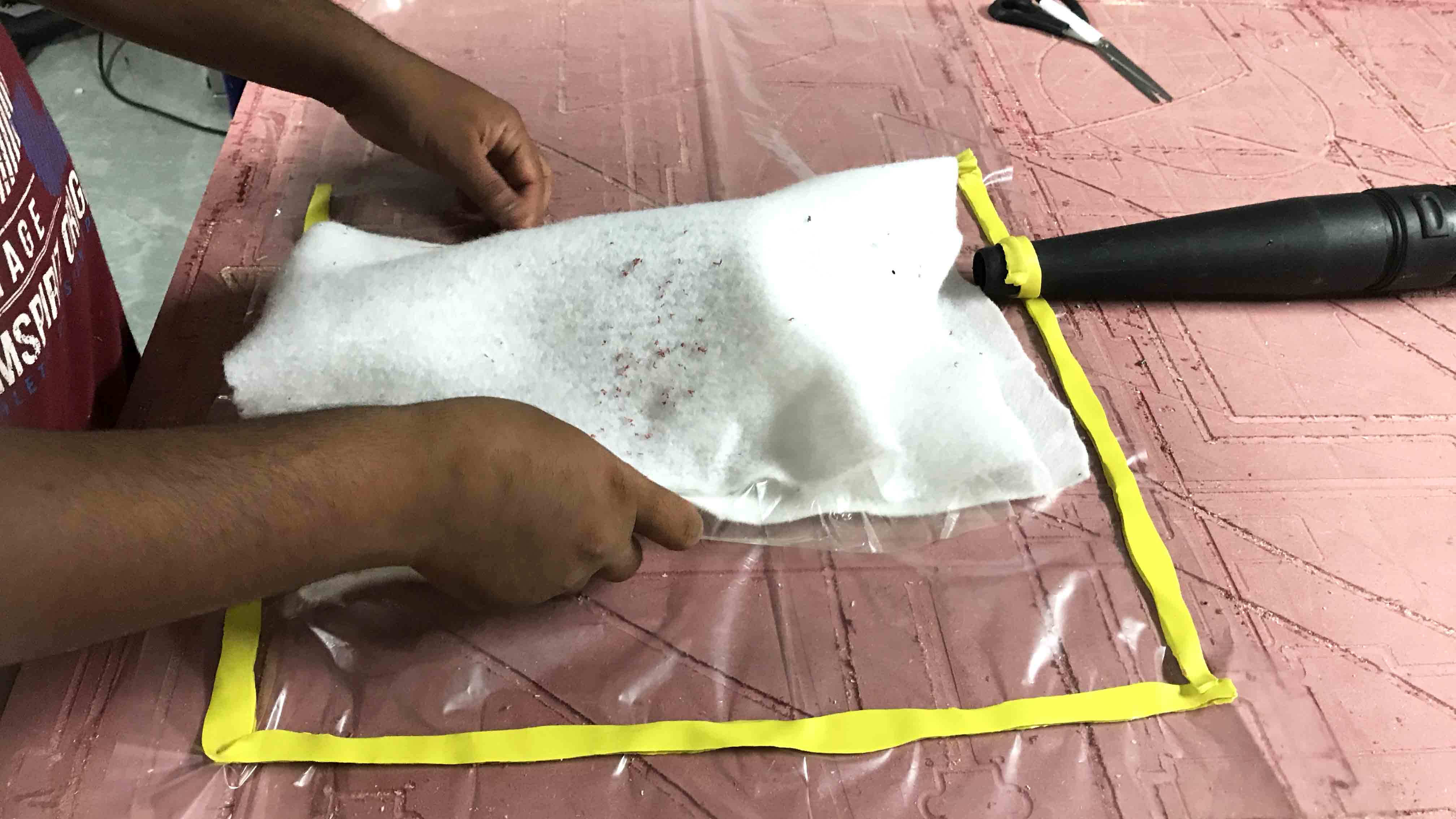
Cover the breather layer. For making the vaccum I used the SHOPVAC vaccum cleaner which can create powerfull vaccum.
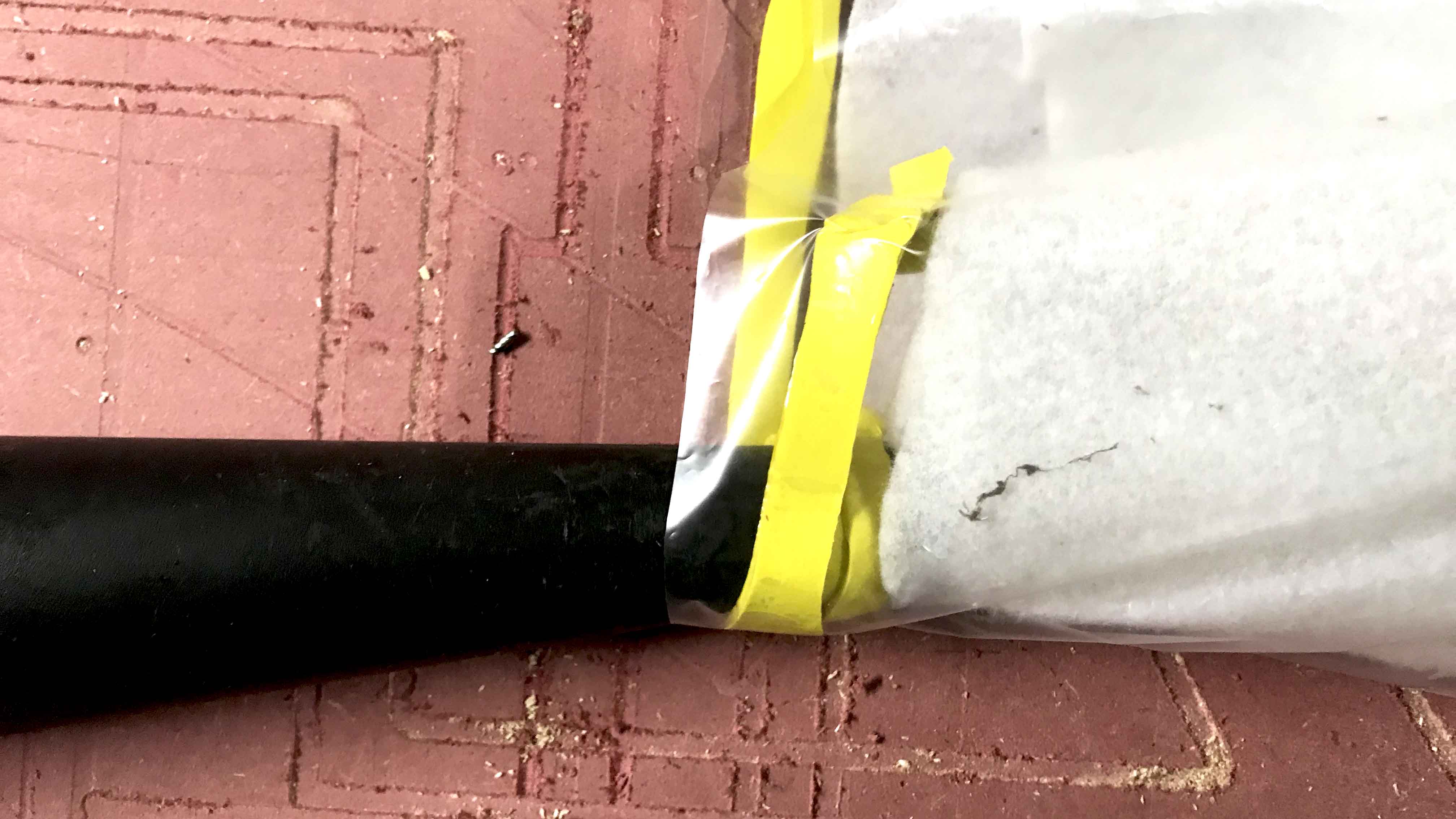
I applied a layer of tape on the mouth of the vaccum to make sure it is air tight.
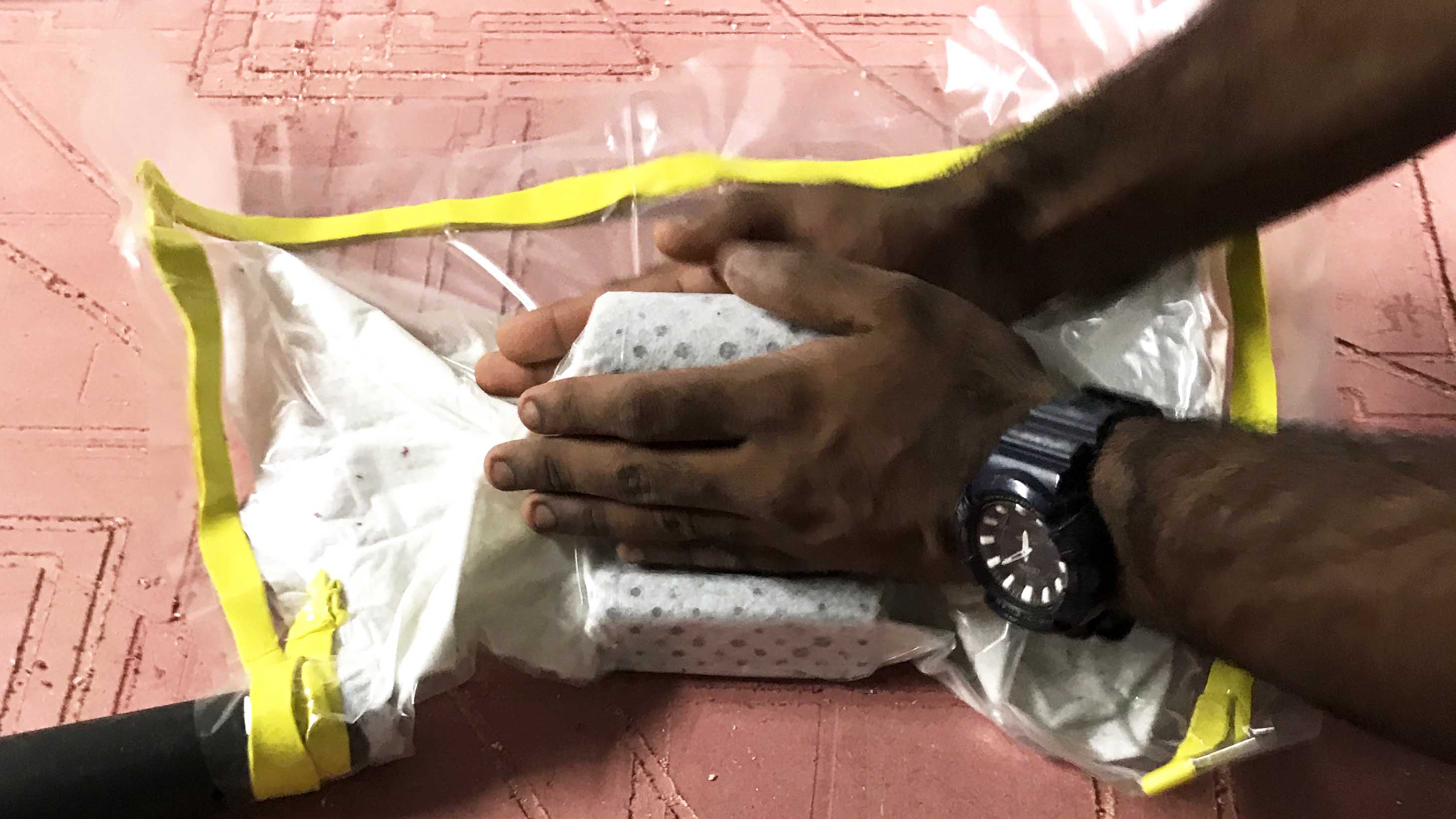
Start the vaccum and make sure it is sealed properly. Press the sides and wall of the mold and squeze out the excess resin.
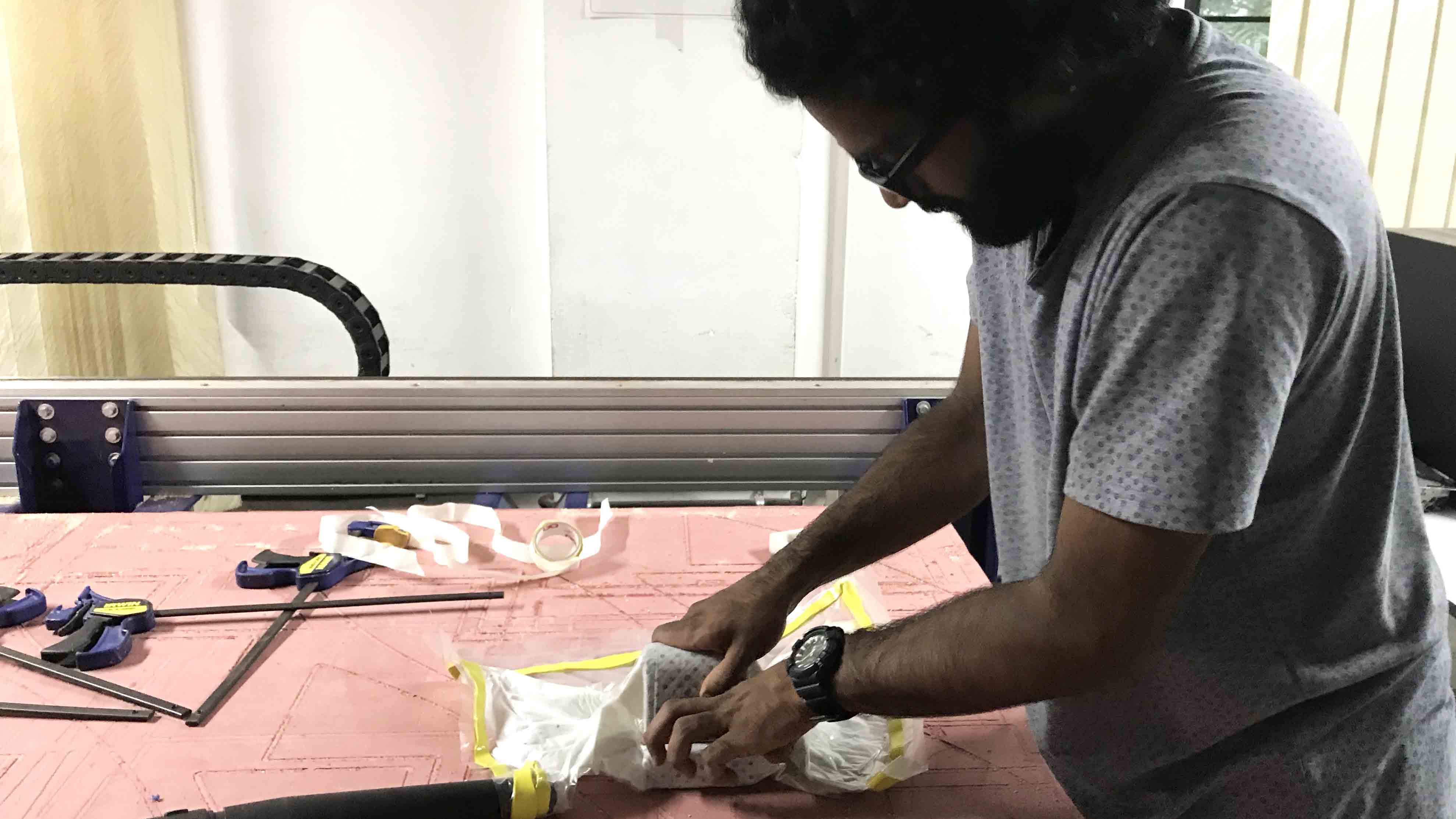
I had to press and shape the mold to maintain the shape of the mold. It seems the mouth of the vaccum cleaner is not properly sealed. I had to remove the tape and fix this problem twice.
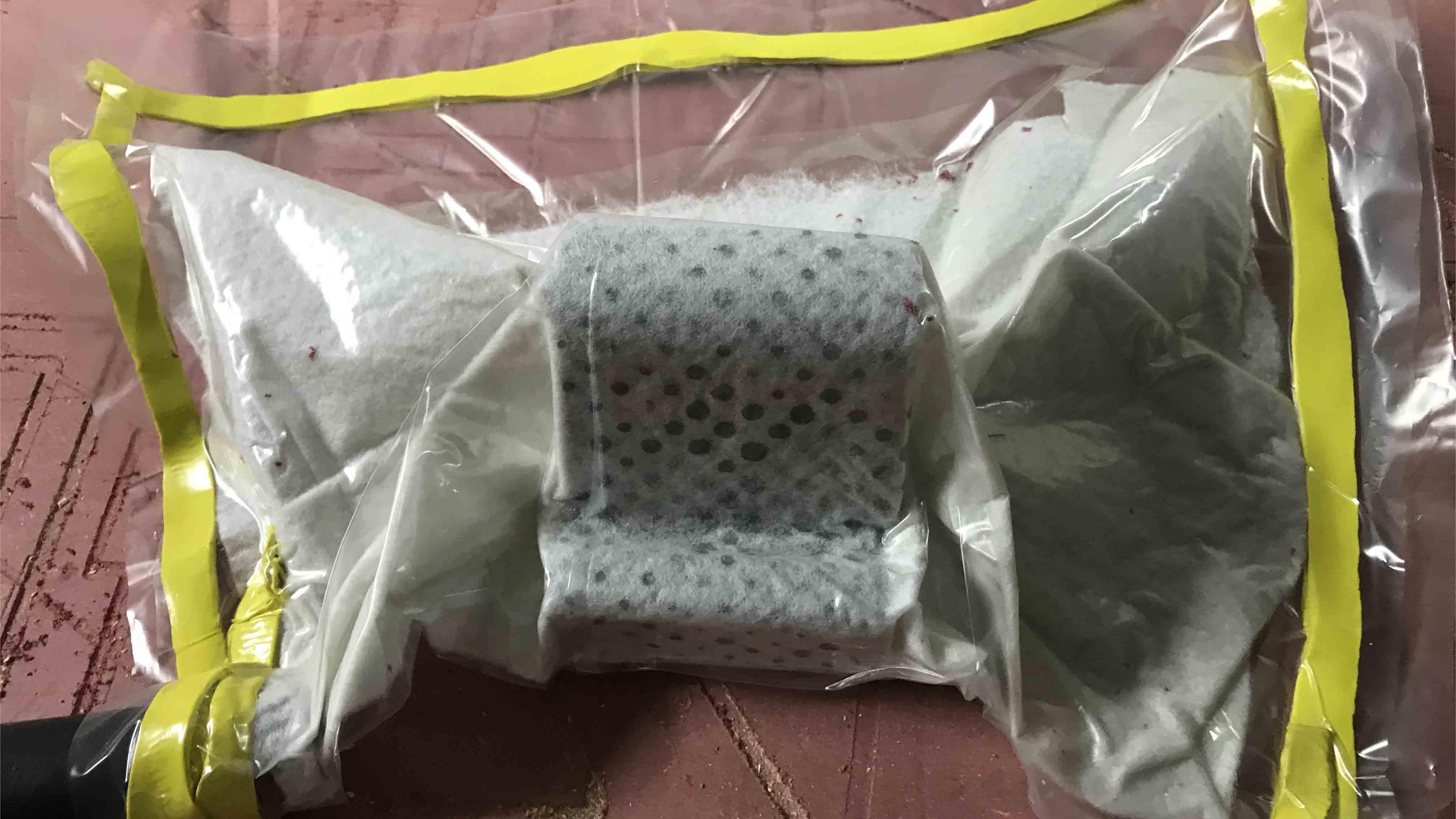
Now it looks like the vaccum is maintained properly. I kept vaccum running another one hour. Switched off the vaccum after one hour and removed the vaccum cleaner pipe from the the vaccum bag. I kept the pack closed over night.
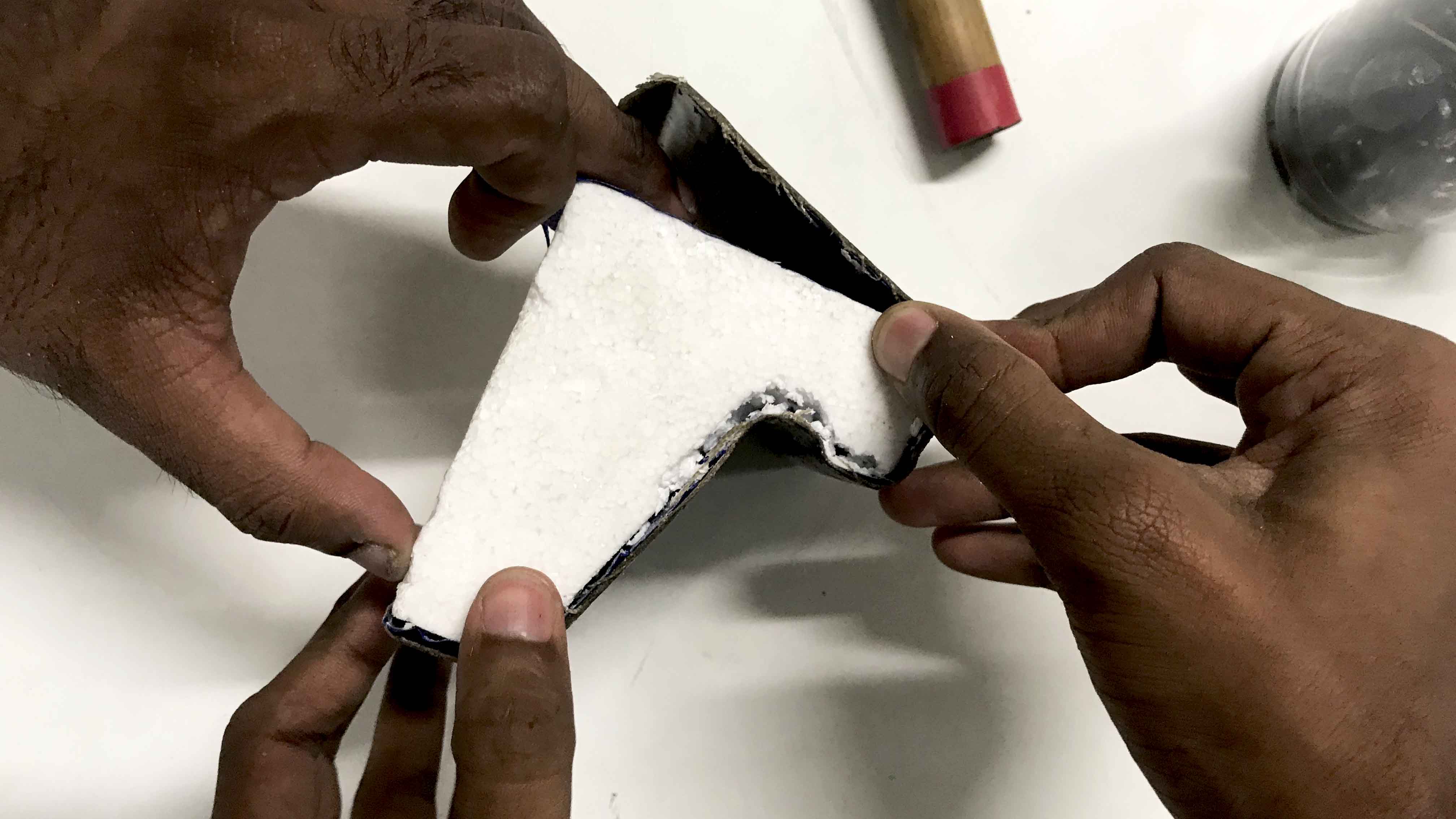
Next day I opened the pack. I found that the the excess resin struck between the thermocol and the vinyl sheet, it was very difficult task to remove the composite from the the mold. I have removed the mold from the composite after few tries, but it destroyed the mold.
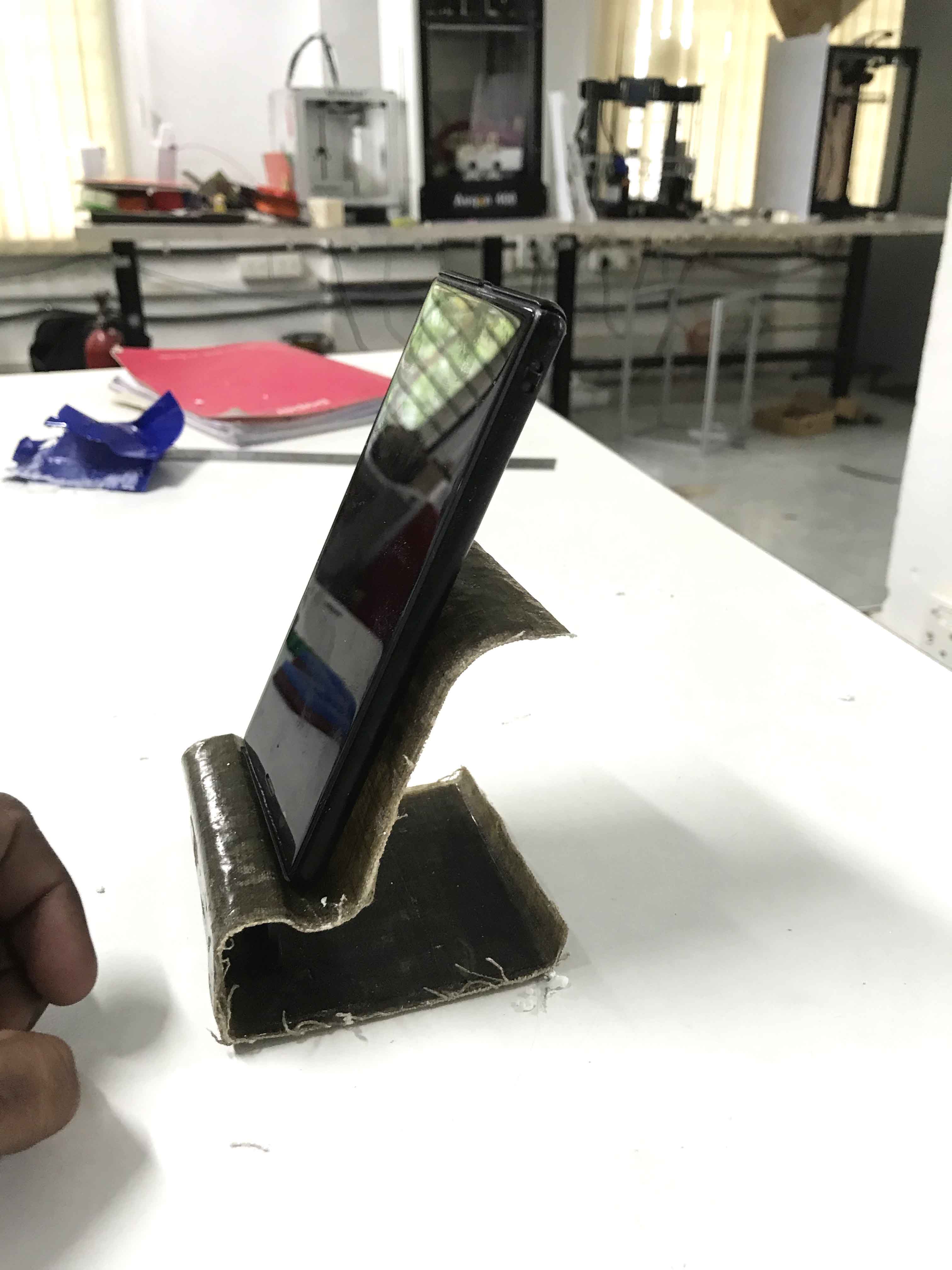
Finally removed the excess parts using band saw. This image is taken before finishing touch.
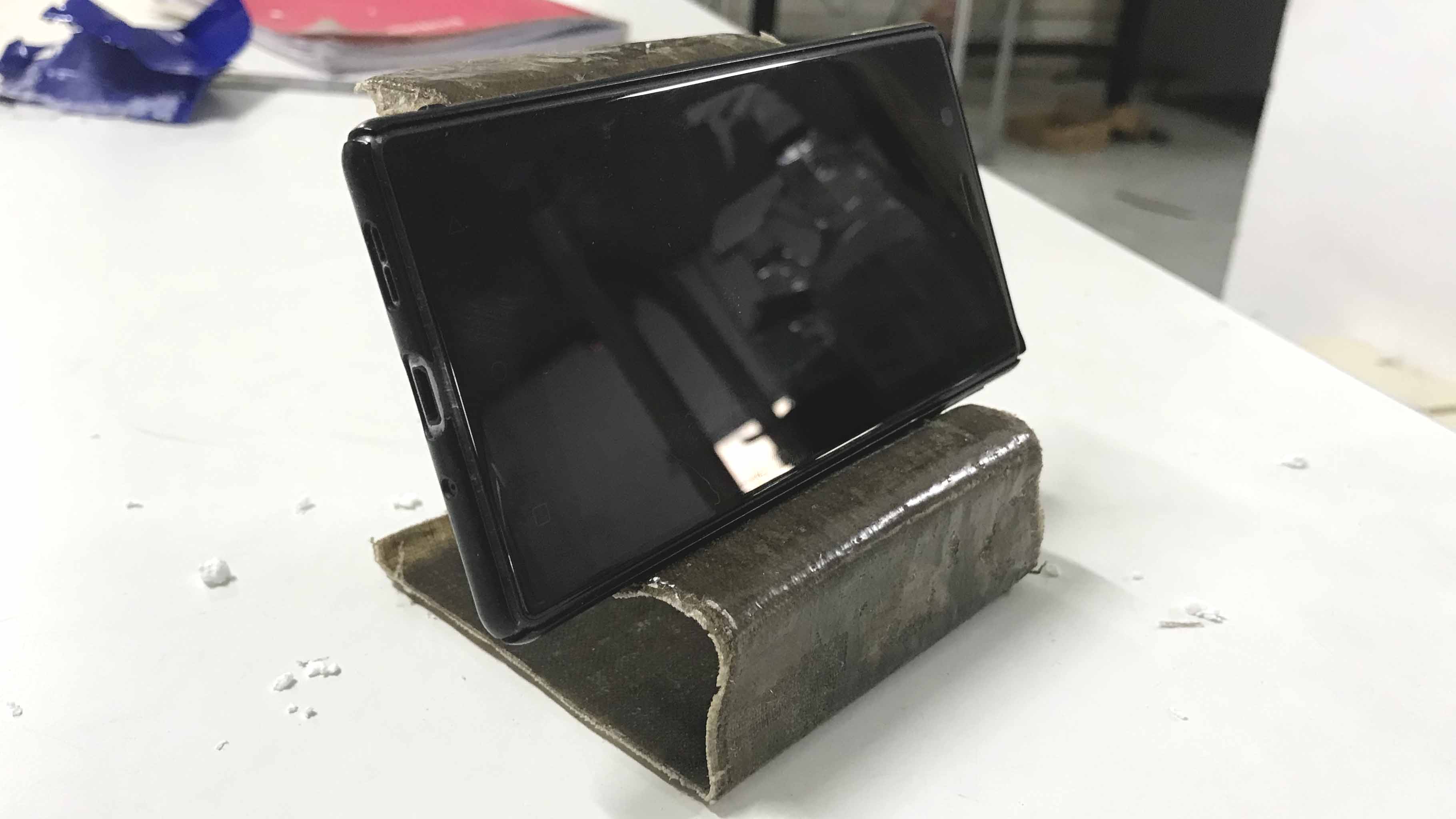
It seems four layer is not enouth for this kind of shape. I should have added few more layers to make the stucture stronger
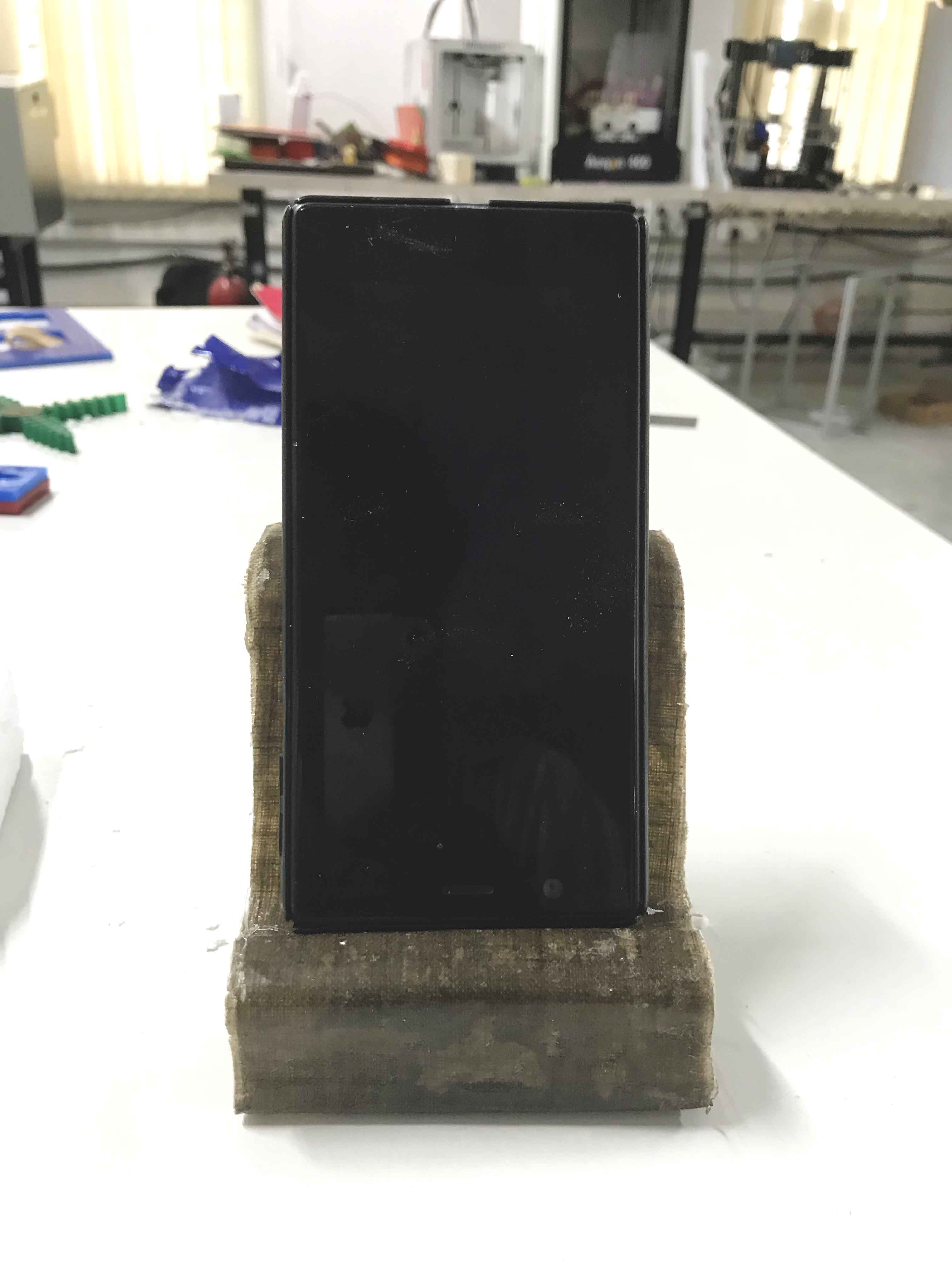
Hero shot
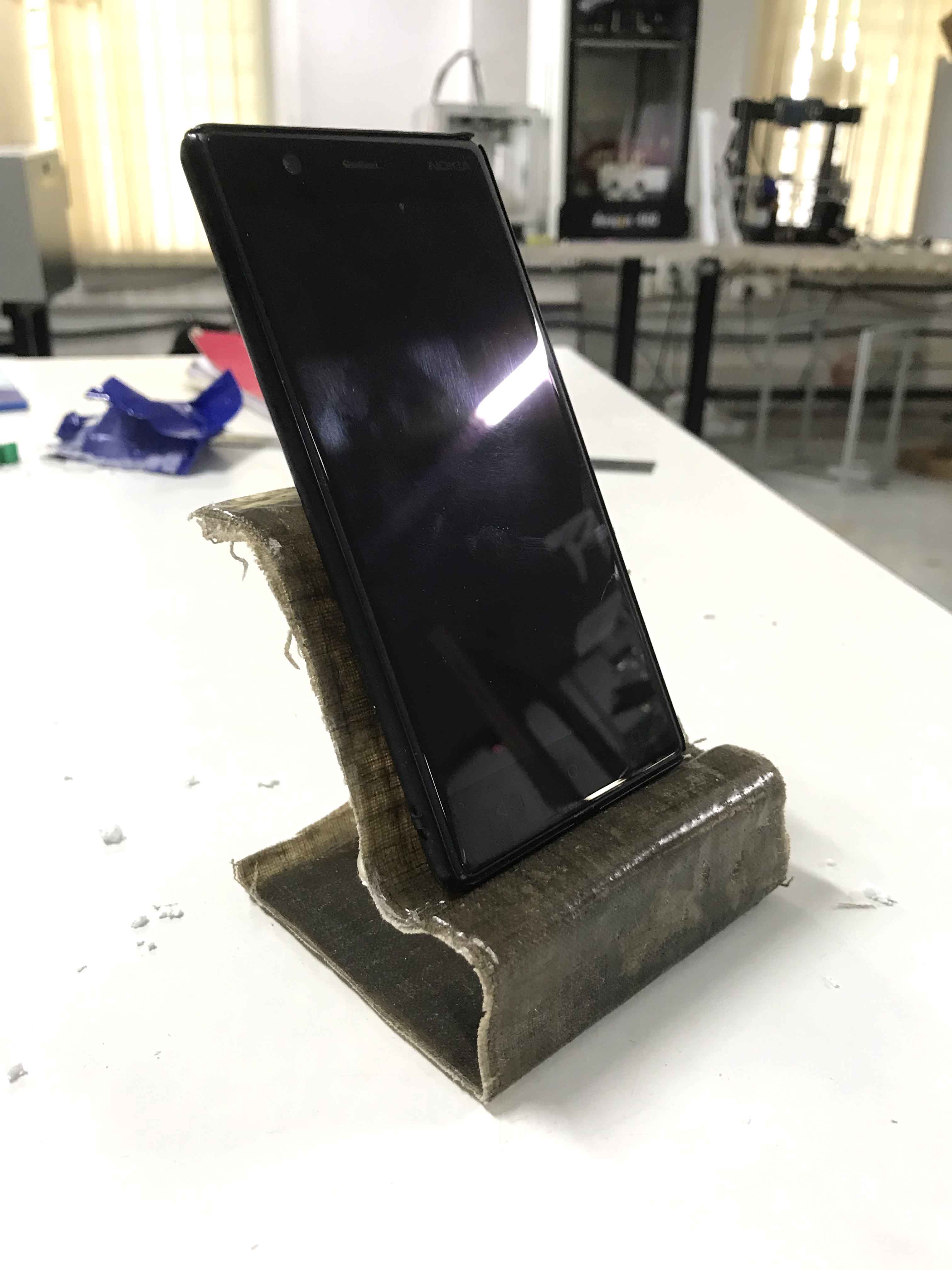