Assignment
GROUP ASSIGNMENT:
Review the safety data sheets for each of your molding and casting materials,
then make and compare test casts with each of them
INDIVIDUAL ASSIGNMENT:
Design a mold around the stock and tooling that you'll be using,
mill it (rough cut + (at least) three-axis finish cut),
and use it to cast parts
What I did
- Designed 3D mould for making Sphericon using fusion 360
- Milled positive mold in Machinable Wax
- Cast using transparent resin
- Added blue pigment and casted
- Casted using bismuth
- Made final surface finish for bismuth using file and sand paper & polished using dremels
Molding and casting
3d printing and cnc machining is good in creating complicated 3d geometries.
It is very inefficient is replicating similar designs .Though there are faster and more precise
machines are developing like SLS(selective laser sintering) and CLIP(Continuous Liquid Interface Production )
still it is consuming more time.
Casting is a manufacturing process in which a liquid material is usually poured into a mold, which contains
a hollow cavity of the desired shape, and then allowed to solidify. The solidified part is also known as a
casting, which is ejected or broken out of the mold to complete the process. Casting materials are usually
metals or various cold setting materials that cure after mixing two or more components together; examples
are epoxy, concrete, plaster and clay.
Design 3D mold
My goal is to design Hexasphericon using fusion 360
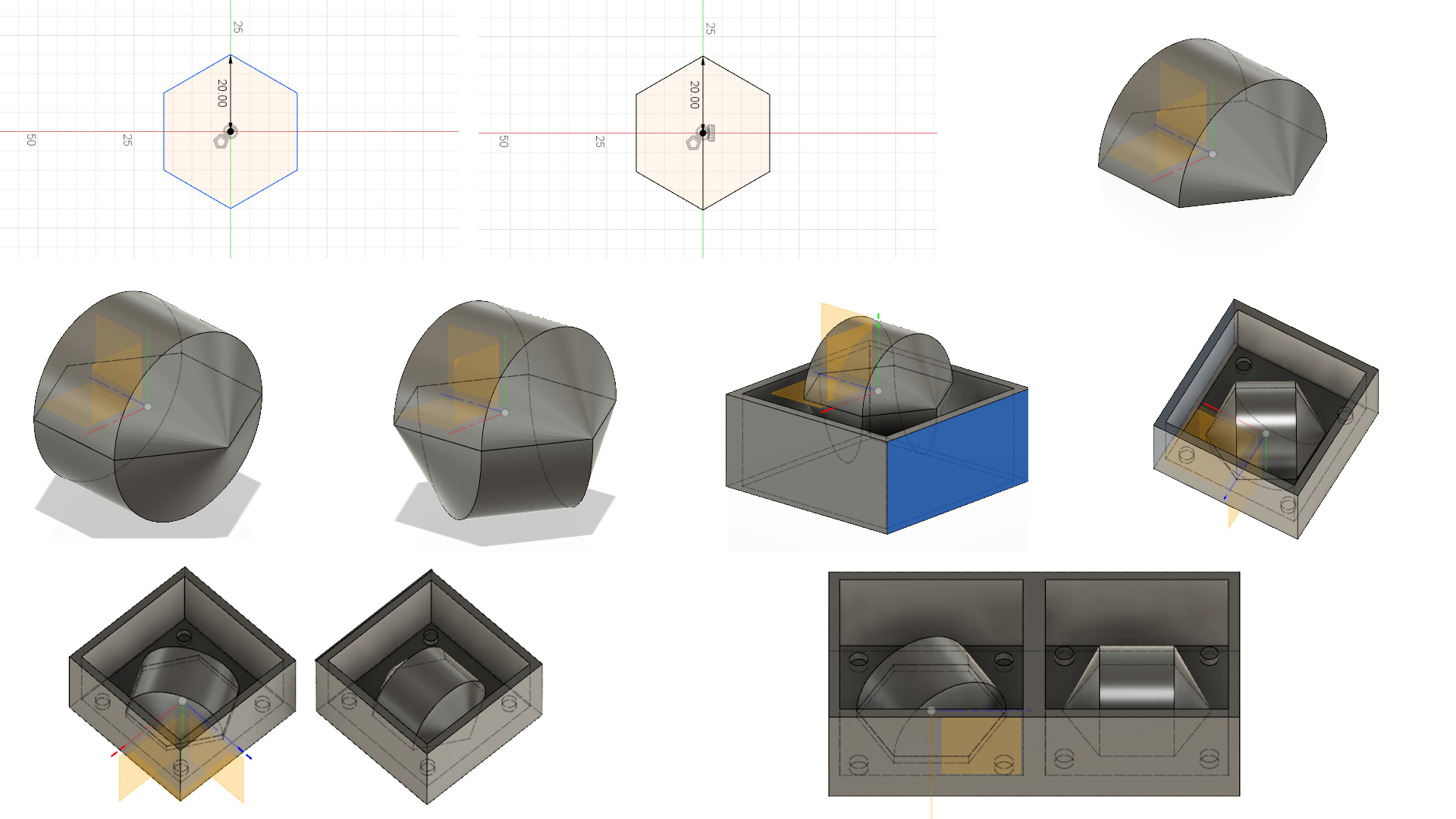
Start drawing using inscribed polygon in the sketch menu
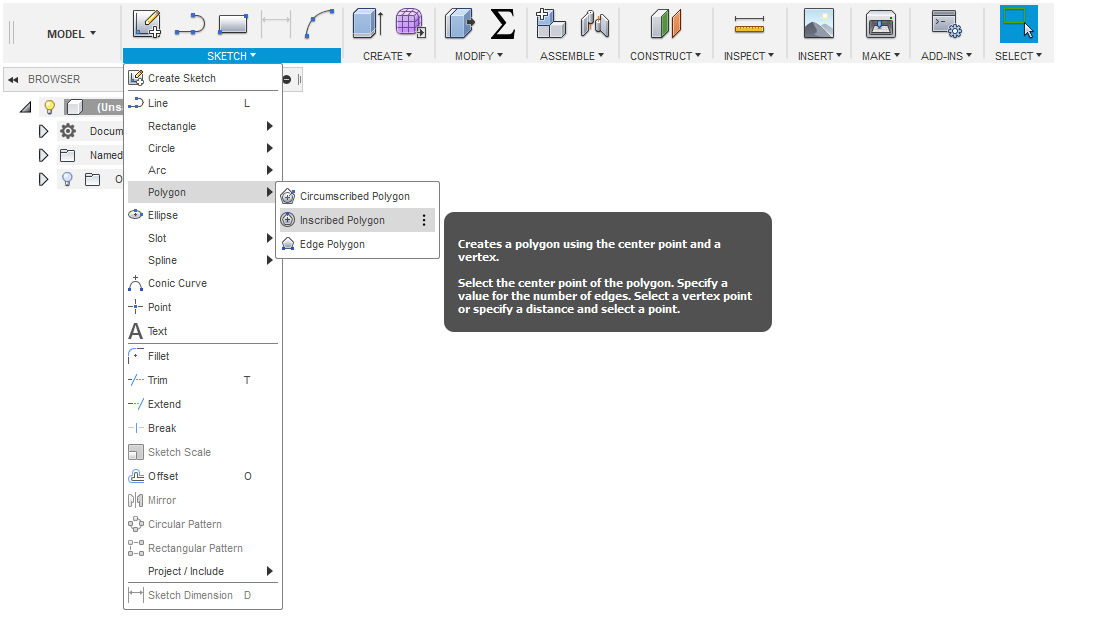
Finished design for final milling
Download f3d file here
SMOOTH-ON OOMOO®30
OOMOO™ 30 is suitable for a variety of art-related and industrial applications including making one and two-piece block for sculpture and prototype reproduction, casting plaster, resins and wax. OOMOO™ silicones are also suitable for electrical potting and encapsulation applications.
- Safety Use in a properly ventilated area (“room size” ventilation). Wear safety glasses, long sleeves and rubber gloves to minimize contamination risk. Wear vinyl gloves only. Latex gloves will inhibit the cure of the rubber. Store and use material at room temperature (73°F/23°C). Storing material at warmer temperatures will also reduce the usable shelf life of unused material. These products have a limited shelf life and should be used as soon as possible. Premix Parts A and B thoroughly before using.
- Cure Inhibition Silicone rubber may be inhibited by certain contaminants in or on the pattern to be molded, resulting in tackiness at the pattern interface or a total lack of cure throughout the mold. If compatibility between the rubber and the surface is a concern, a small-scale test is recommended. Apply a small amount of rubber onto a non-critical area of the pattern. Inhibition has occurred if the rubber is gummy or uncured after the recommended cure time has passed. Materials found to cause cure inhibition include sulfurbased modeling clays and latex rubber. To prevent inhibition apply a sealing agent . . . apply a “barrier coat” of clear acrylic lacquer sprayed onto the clay surface.
- Applying A Release Agent Although not usually necessary, a release agent will make demolding easier when pouring into or over most surfaces. Ease Release™ 200 is a proven release agent for making molds with silicone rubber and for releasing new silicone from cured silicone. Mann Ease Release™ products are available from Smooth-On or your Smooth-On distributor. Because no two applications are quite the same, a small test application to determine suitability for your project is recommended if performance of this material is in question.
- Measuring & Mixing Before you begin, pre-mix Parts A and B thoroughly. After dispensing equal amounts of Parts A and B into mixing container, mix thoroughly for 3 minutes making sure that you scrape the sides and bottom of the mixing container several times. Mixture should have a uniform color with no color streaks. If you observe color streaks, continue mixing until they are eliminated.
- Pouring For best results, pour your mixture in a single spot at the lowest point of the containment field. Let the rubber seek its level up and over the model. A uniform flow will help minimize entrapped air. The liquid rubber should level off at least 1/2” (1.3 cm) over the highest point of the model surface.
- Curing Allow to cure for 6 hours at room temperature (73°F/23°C) before demolding. Post curing the mold an additional 4 hours at 150°F (65°C) will eliminate any residual moisture and alcohol which is a by product of the condensation process and may inhibit some resins. Allow mold to cool to room temperature before using. Do not cure rubber where temperature is less than 65°F/18°C.
- Using The Mold No release agent is necessary when casting wax or gypsum. Applying a release agent (Ease Release™ 200) prior to casting polyurethane, polyester and epoxy resins is recommended to prevent sticking and mold degradation.
- Mold Performance & Storage The physical life of the mold depends on how you use it (materials cast, frequency, etc.). Casting abrasive materials such as concrete will quickly erode mold detail, while casting non-abrasive materials (wax) will not affect mold detail. Before storing, the mold should be cleaned with a soap solution and wiped fully dry. Two part (or more) molds should be assembled. Molds should be stored on a level surface in a cool, dry environment.
Making mold
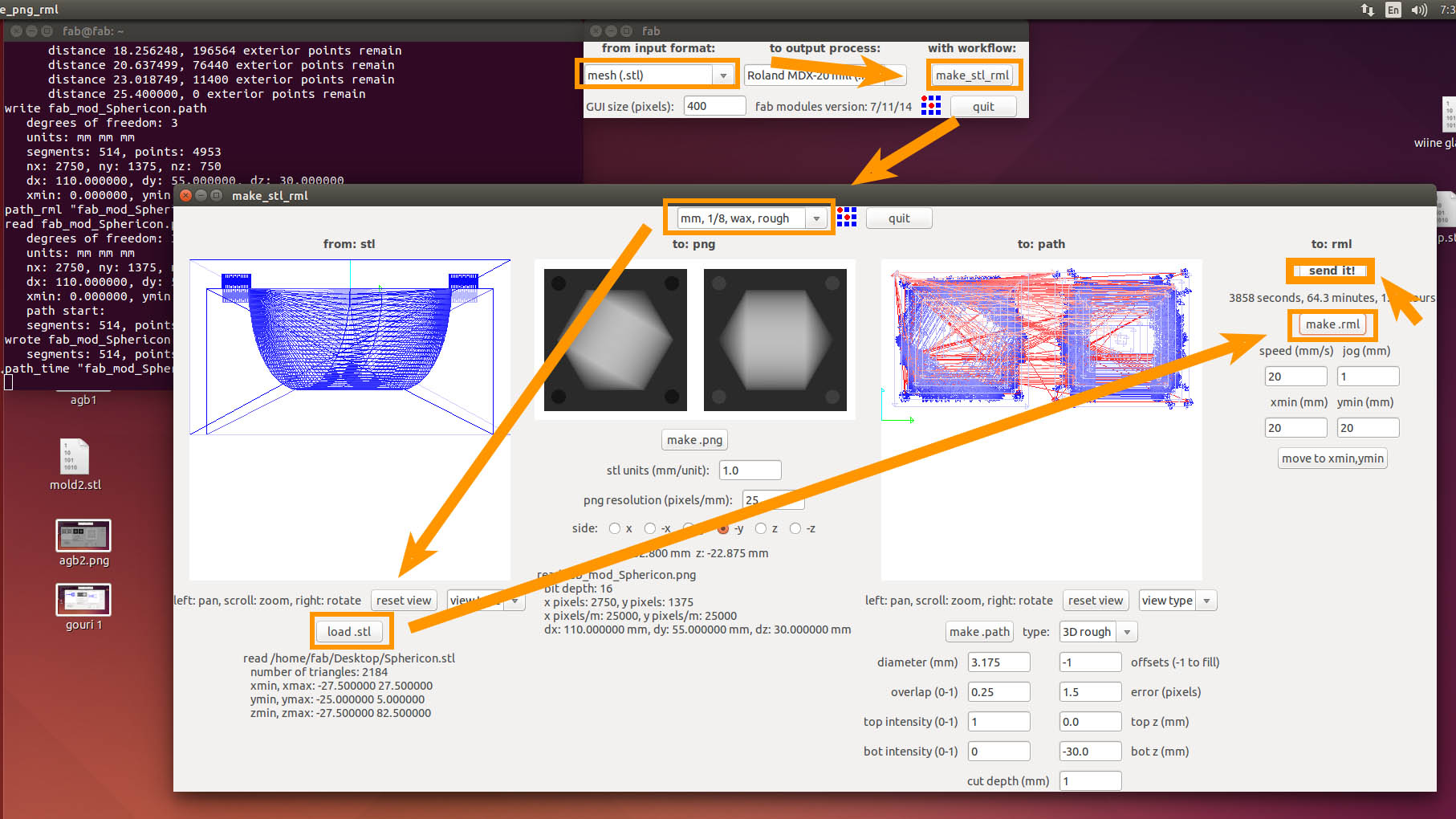
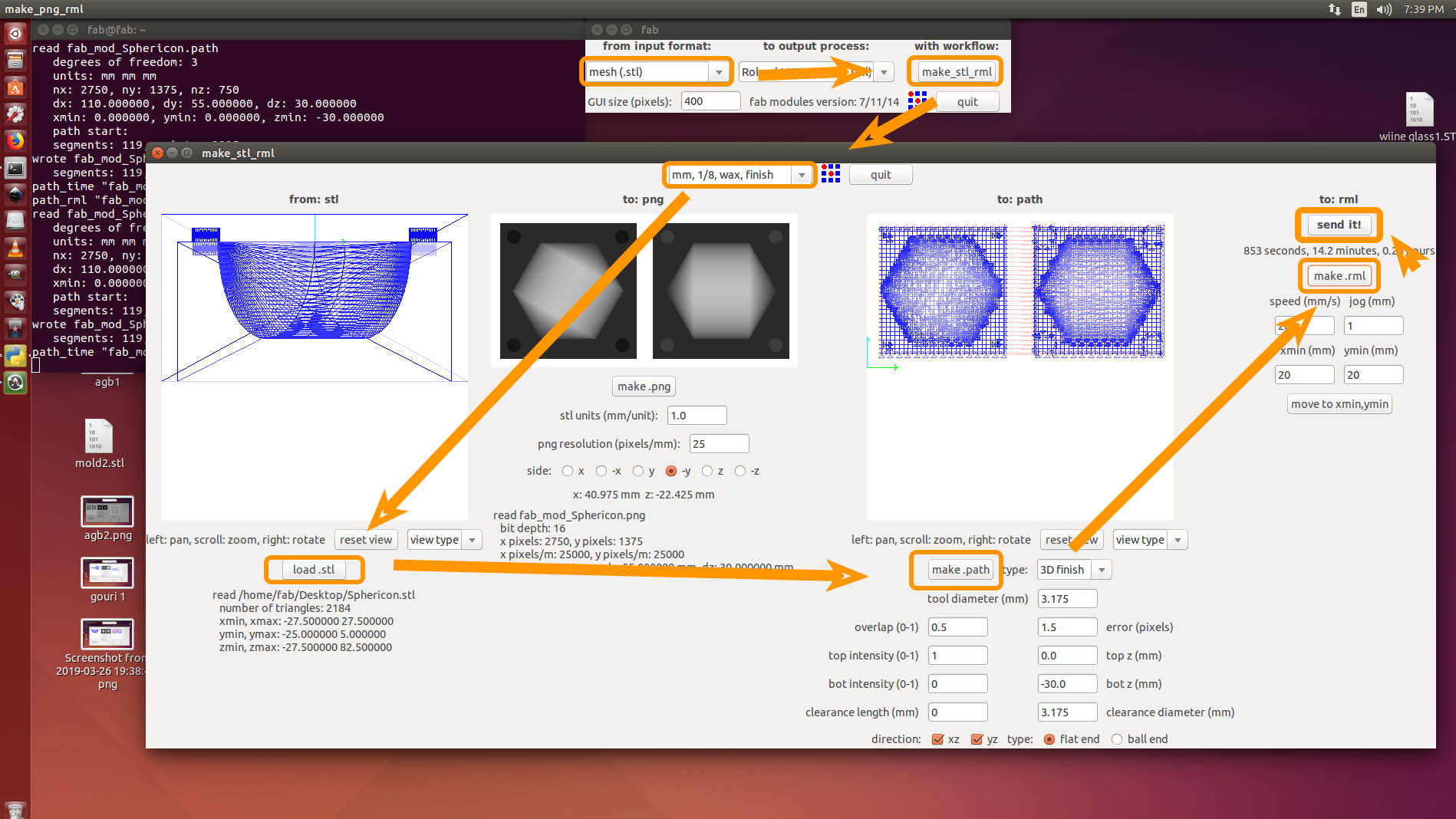
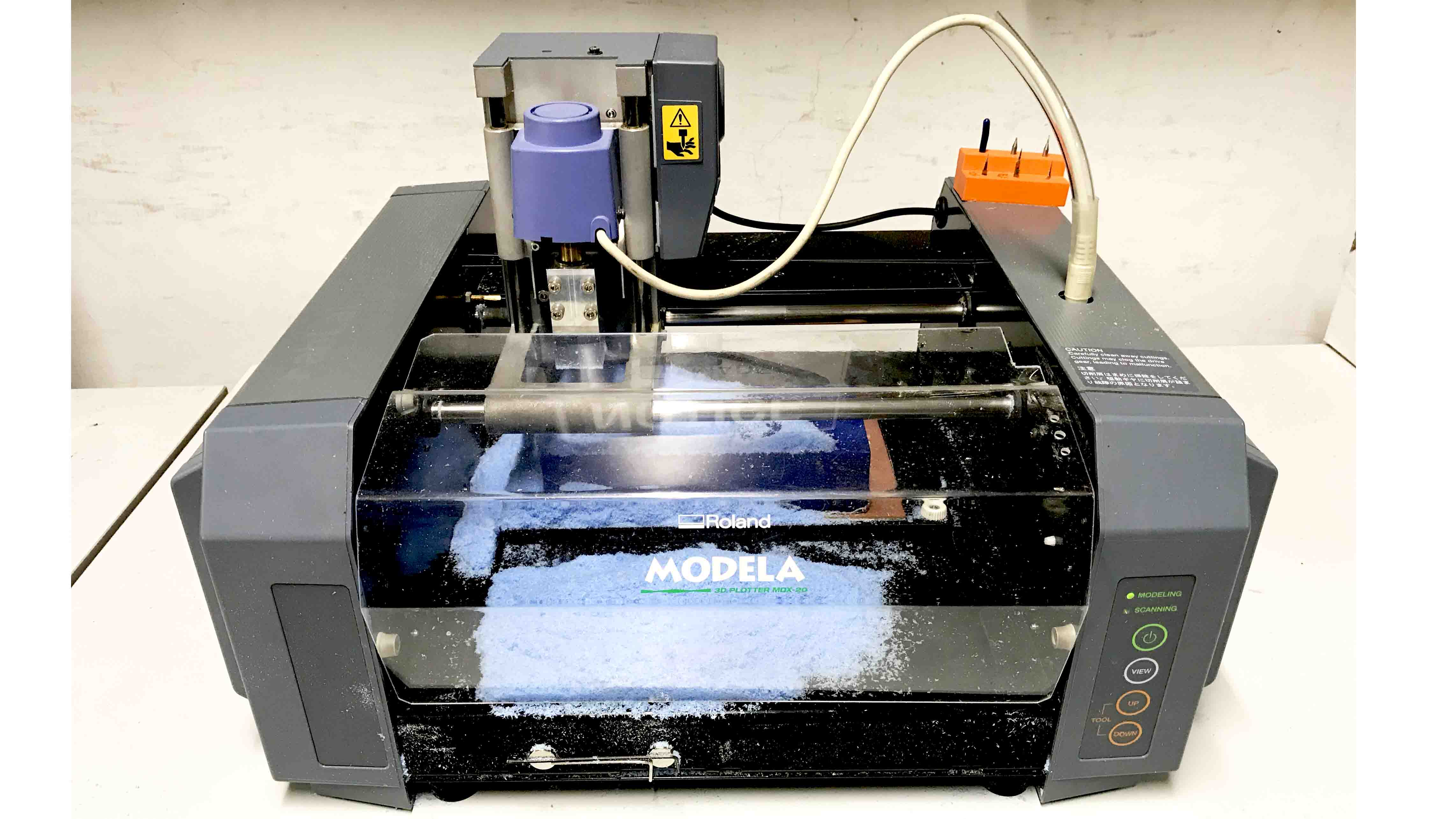
Used modella for milling purpose. It took me 1 hour 20 minits to finish the rough cut. later finished it using ball end bit, which took 15minits
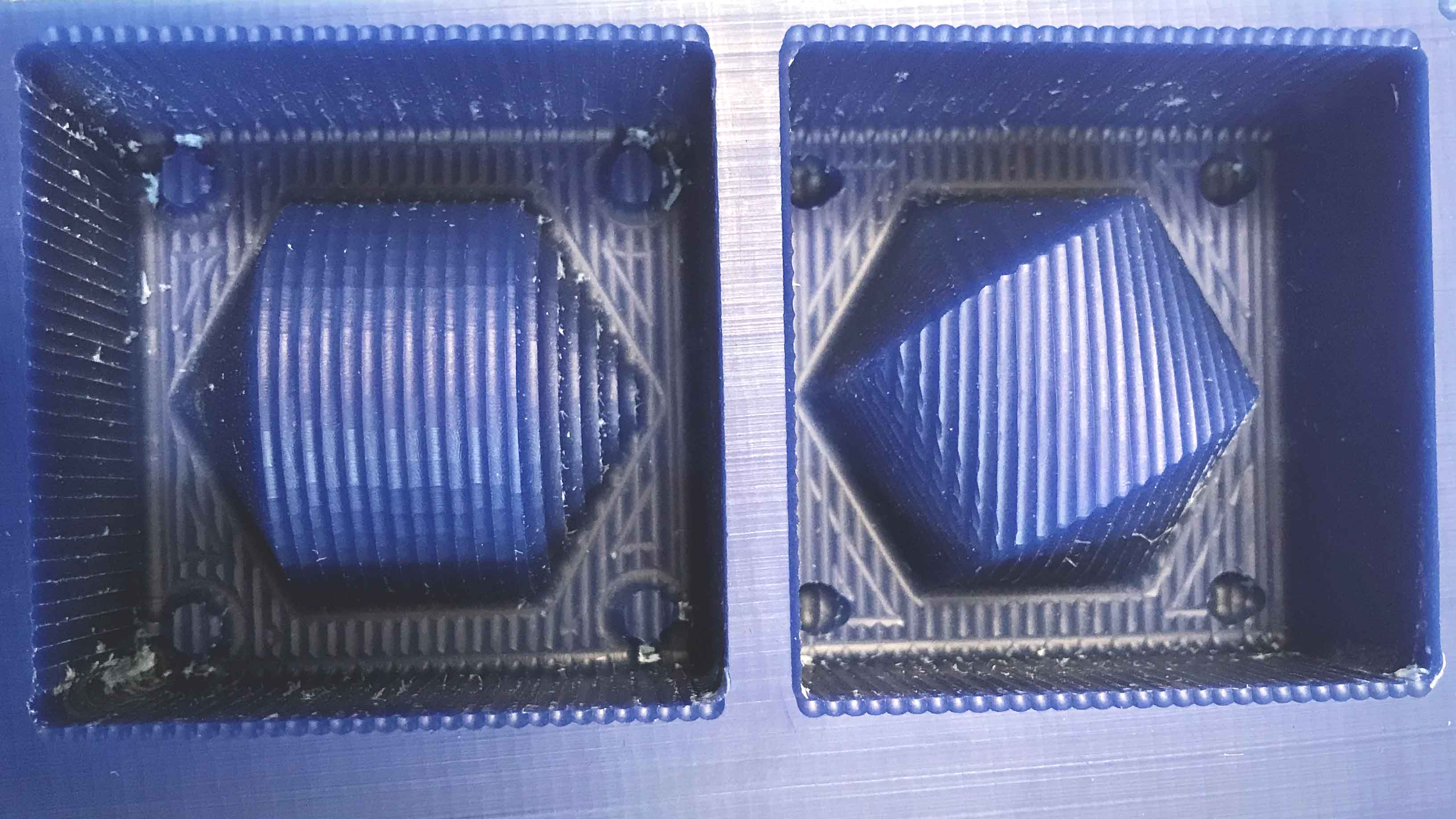
For milling positive mold, I used 175x76x38mm blue wax block
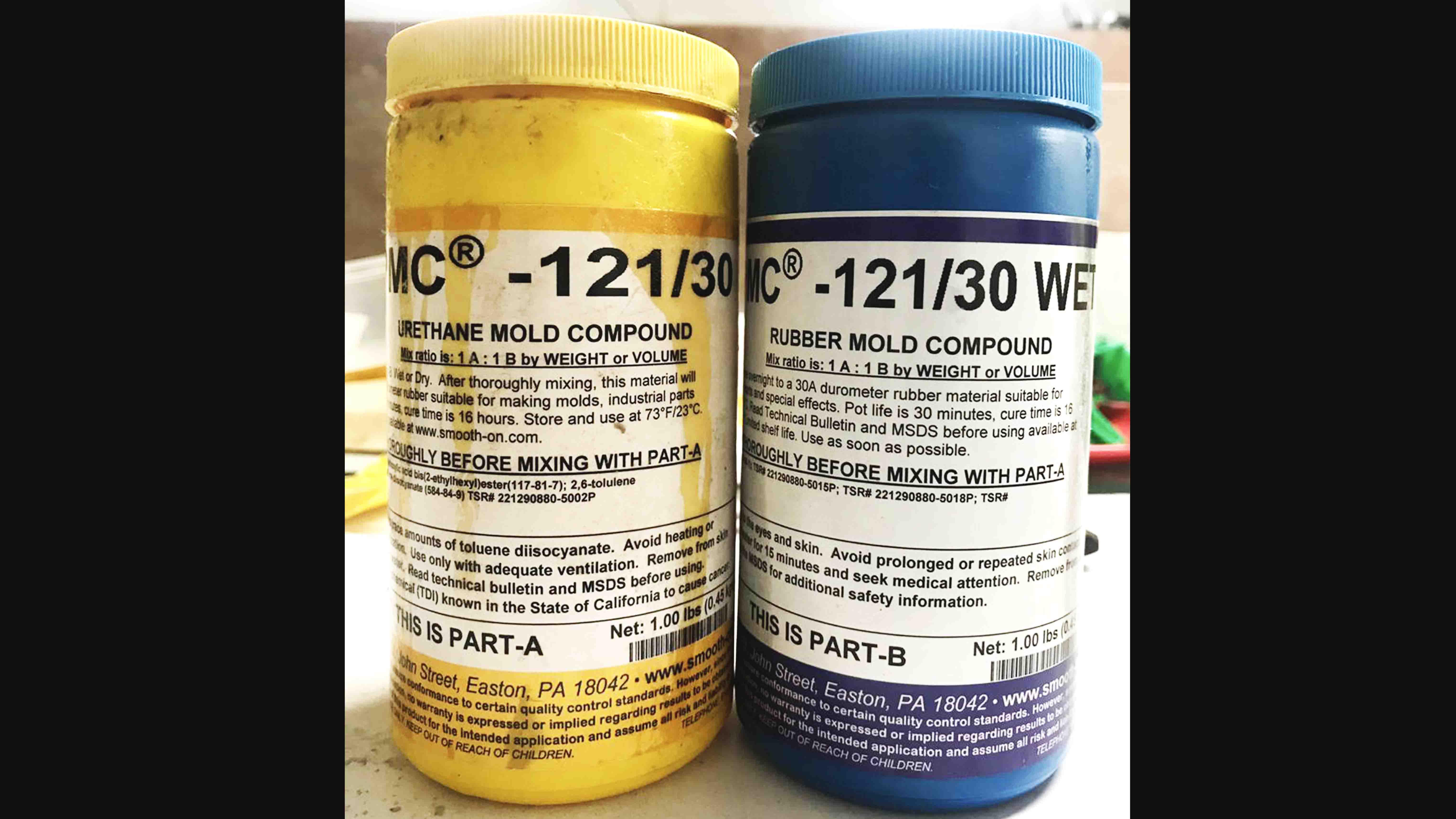
I made first negative mold using Smooth-on oomoo 30 which is a rubber mold compund
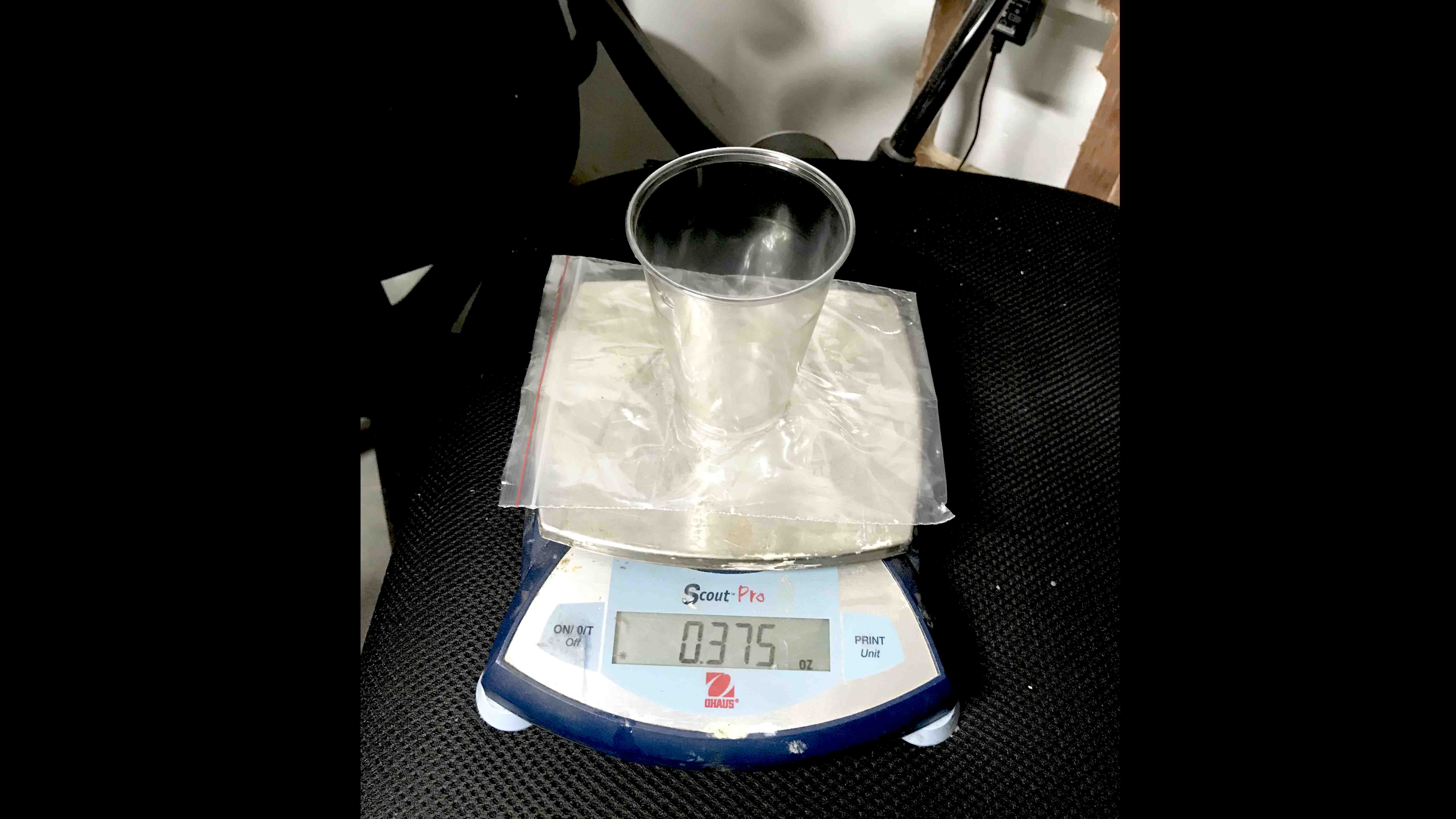
For this compund the part A and B are mixed 1:1 ratio for both by weight and volume
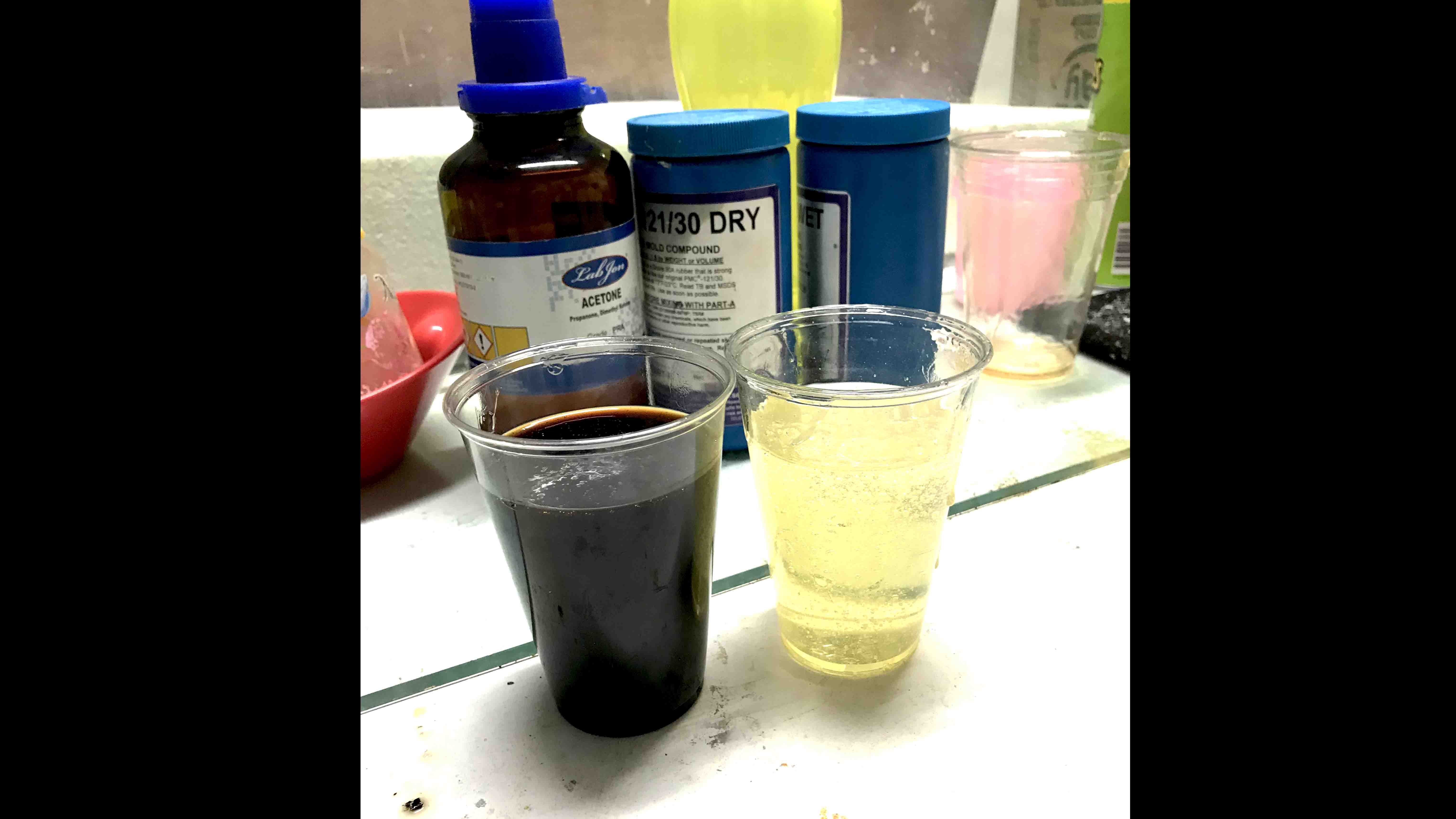
Allways wear glowes while handling such chemicals
To find the the quantity of material first I filled water in the milled portion of wax and transfered it into glass and added some extra materials because some of the material is going to stick to the walls of the glass.
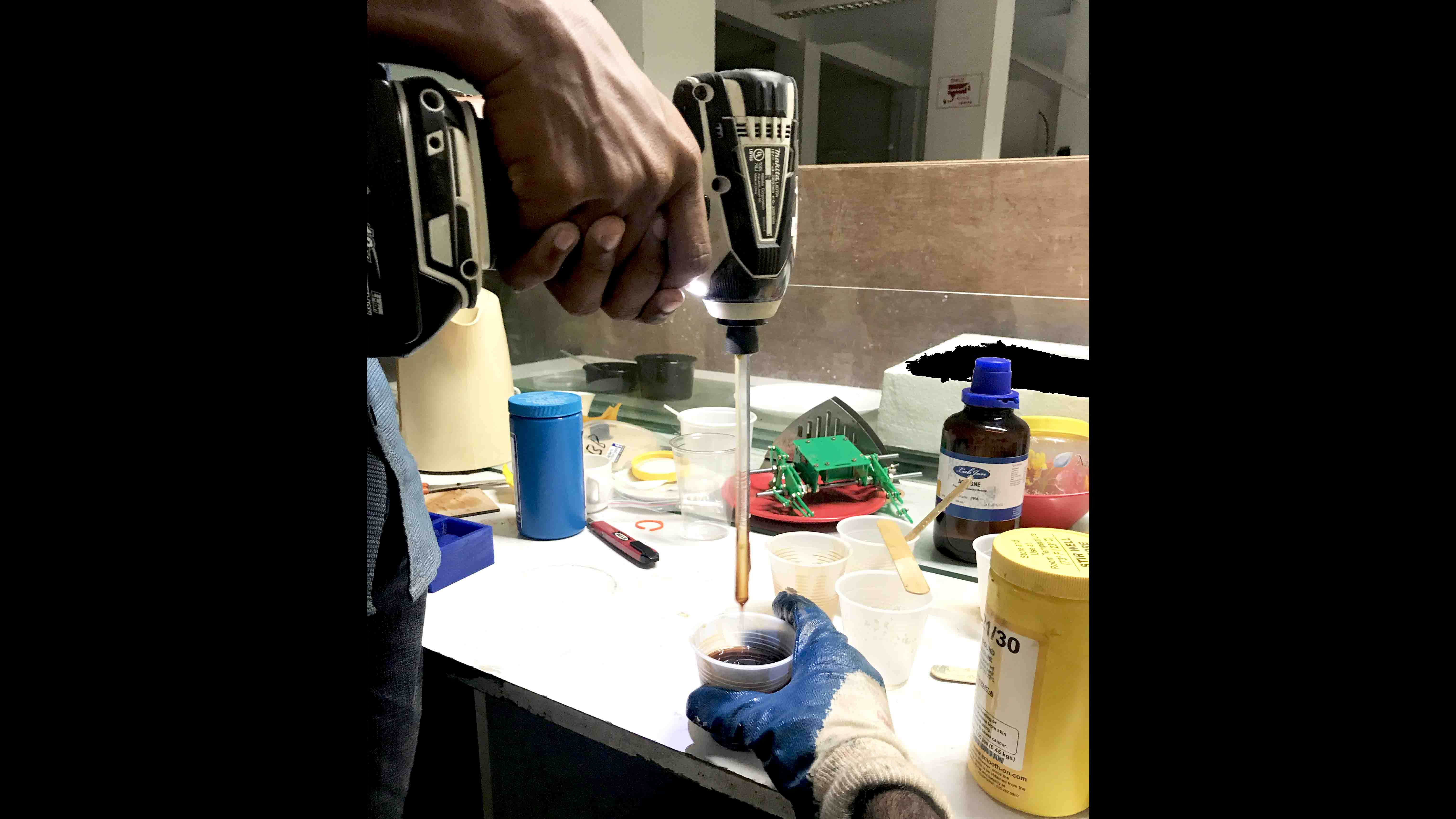
The compound was very thick and it is very difficult to mix it properly so I fixed a acrylic stick to the drilling machine and used as a beater
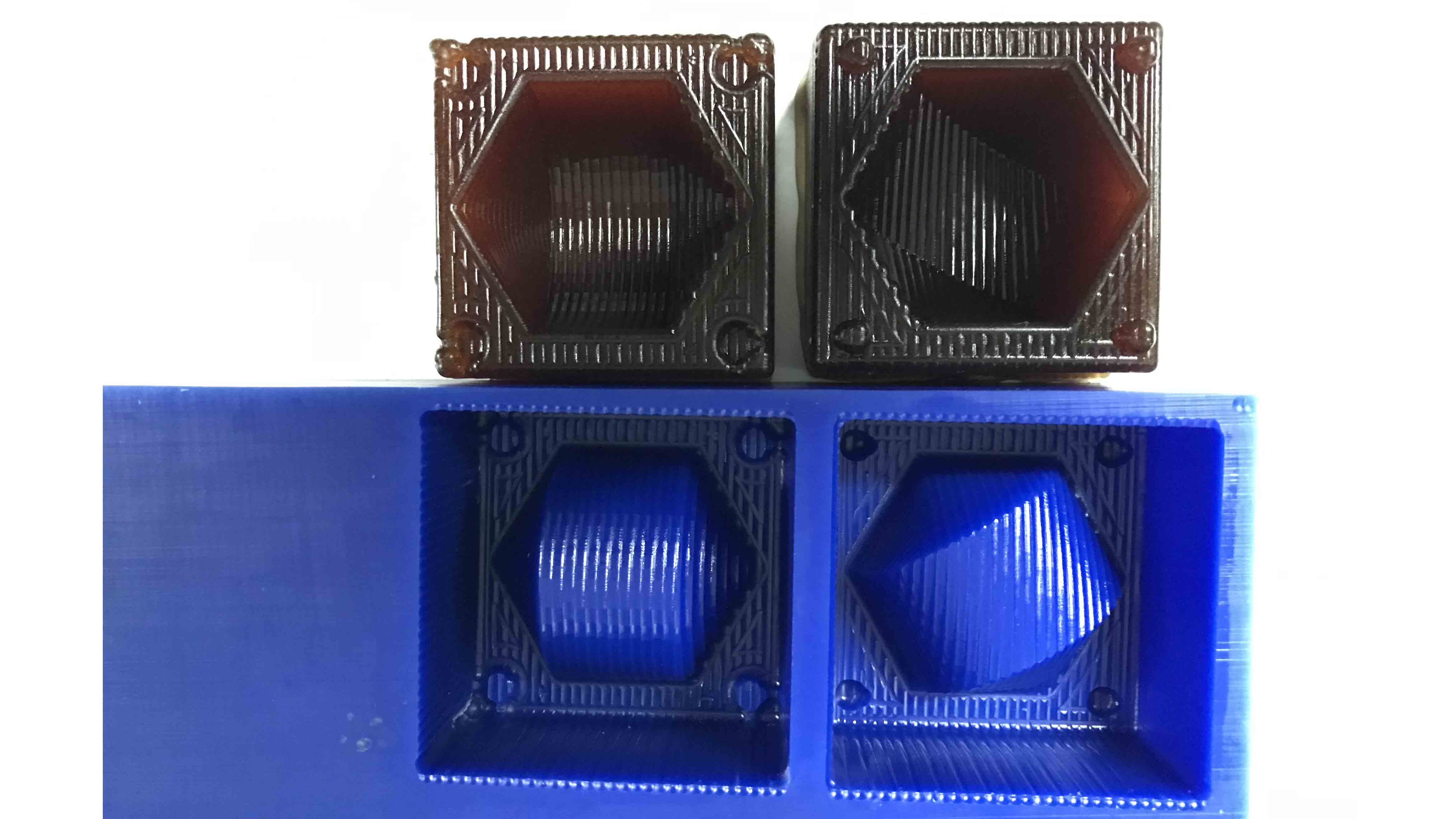
I forgot to give taper to the the walls of the positive mold, this made it difficult to remove the negative mold later
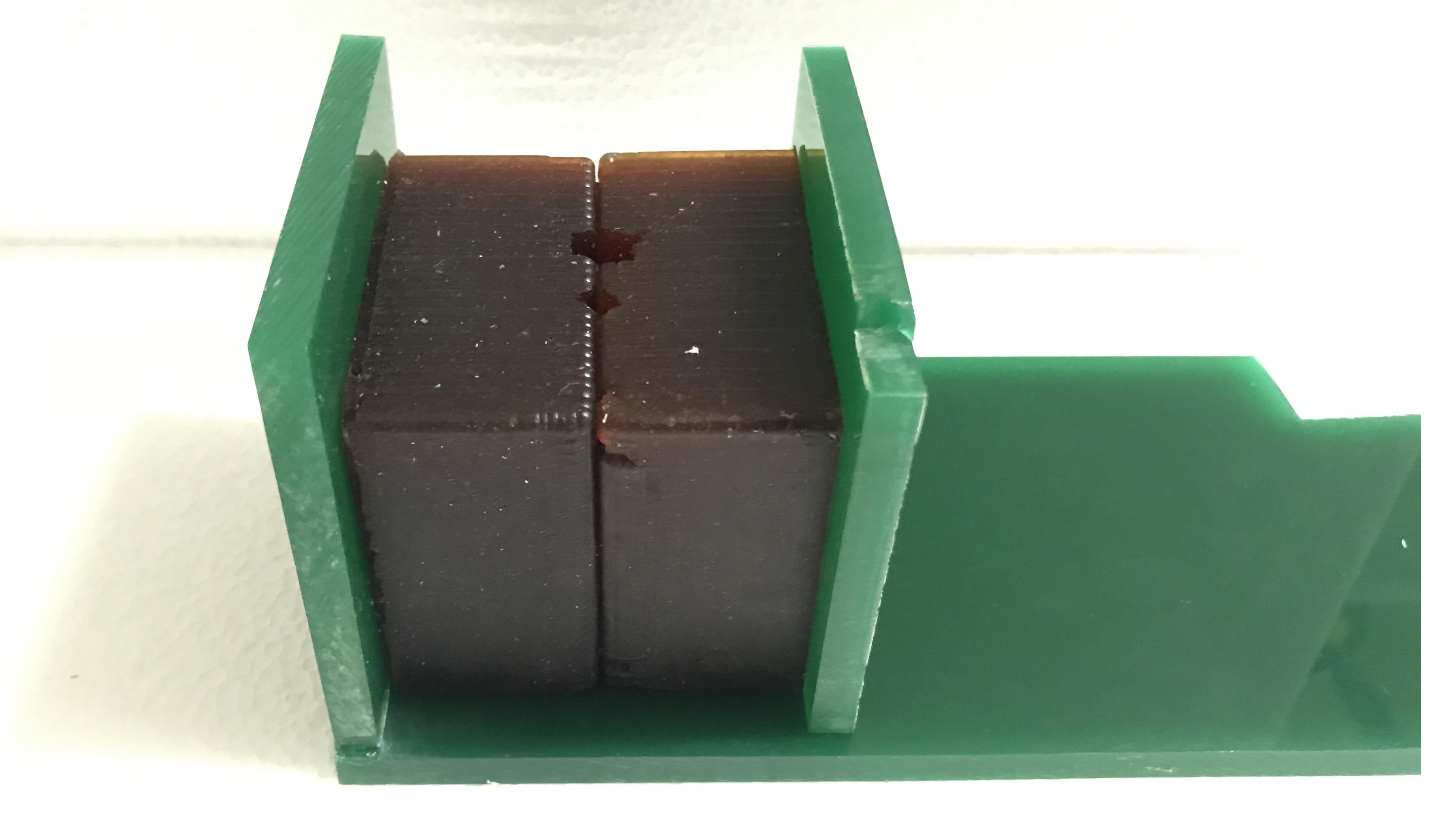
Since it is two piece mold, I tried different ways to keep the mold together. First I used cello tape, then tried thin copper wire later I made this setup using waste acrylic pieces
Aditya easy cast transparent epoxy resin
First I decided to cast using transparent resin. The mixing ratio is Part A 100 parts : Part B 50 parts
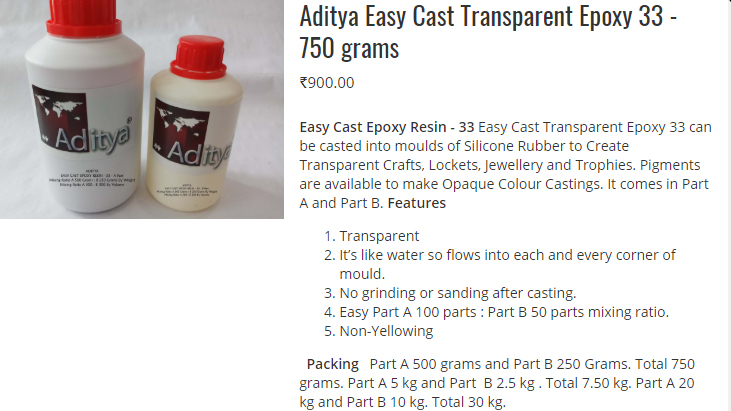
source
Use gloves while handling resin ans molding material or it will be difficult to remove it from hands.
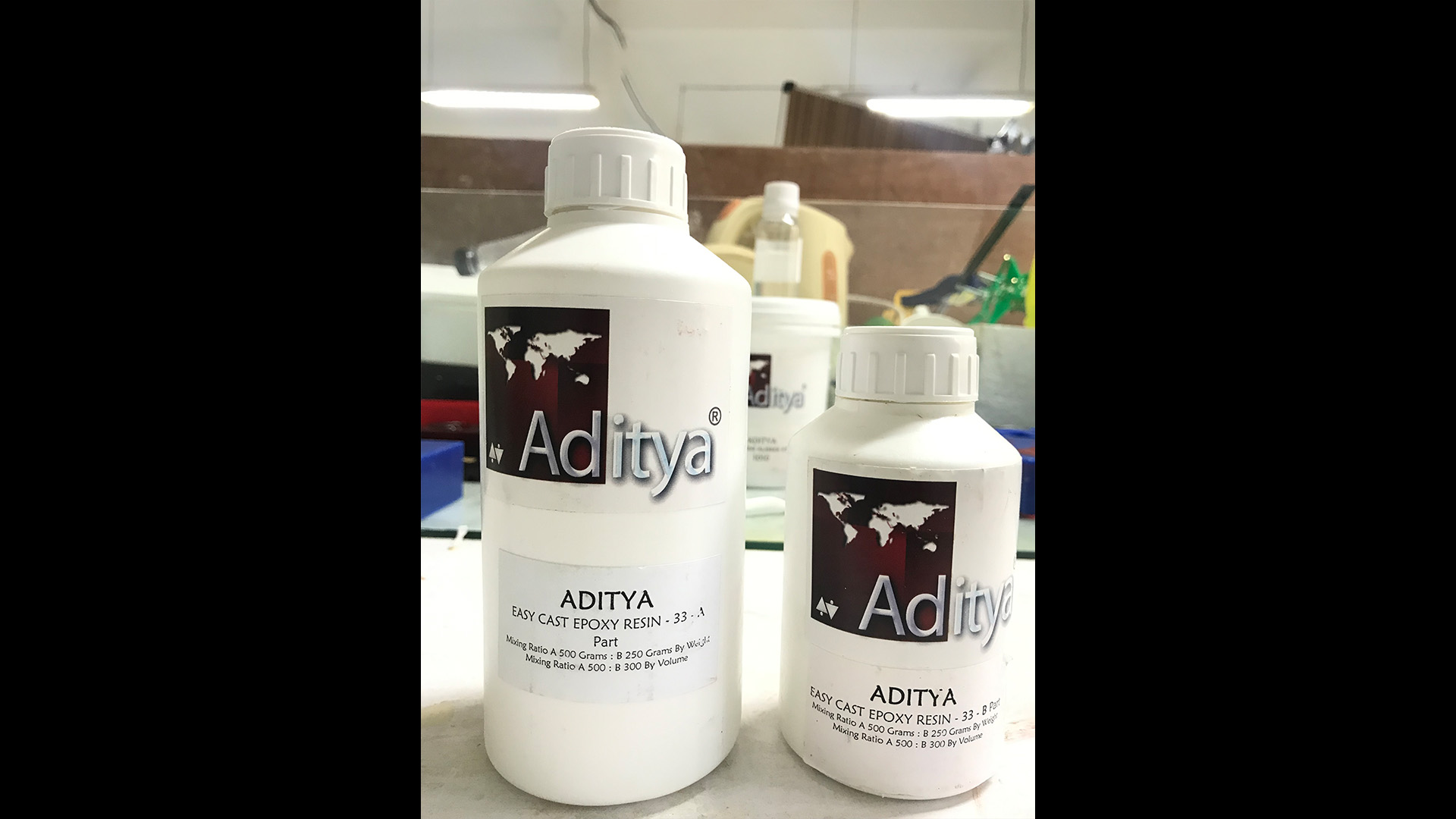
keep the the caps closed immidiately after pouring resin
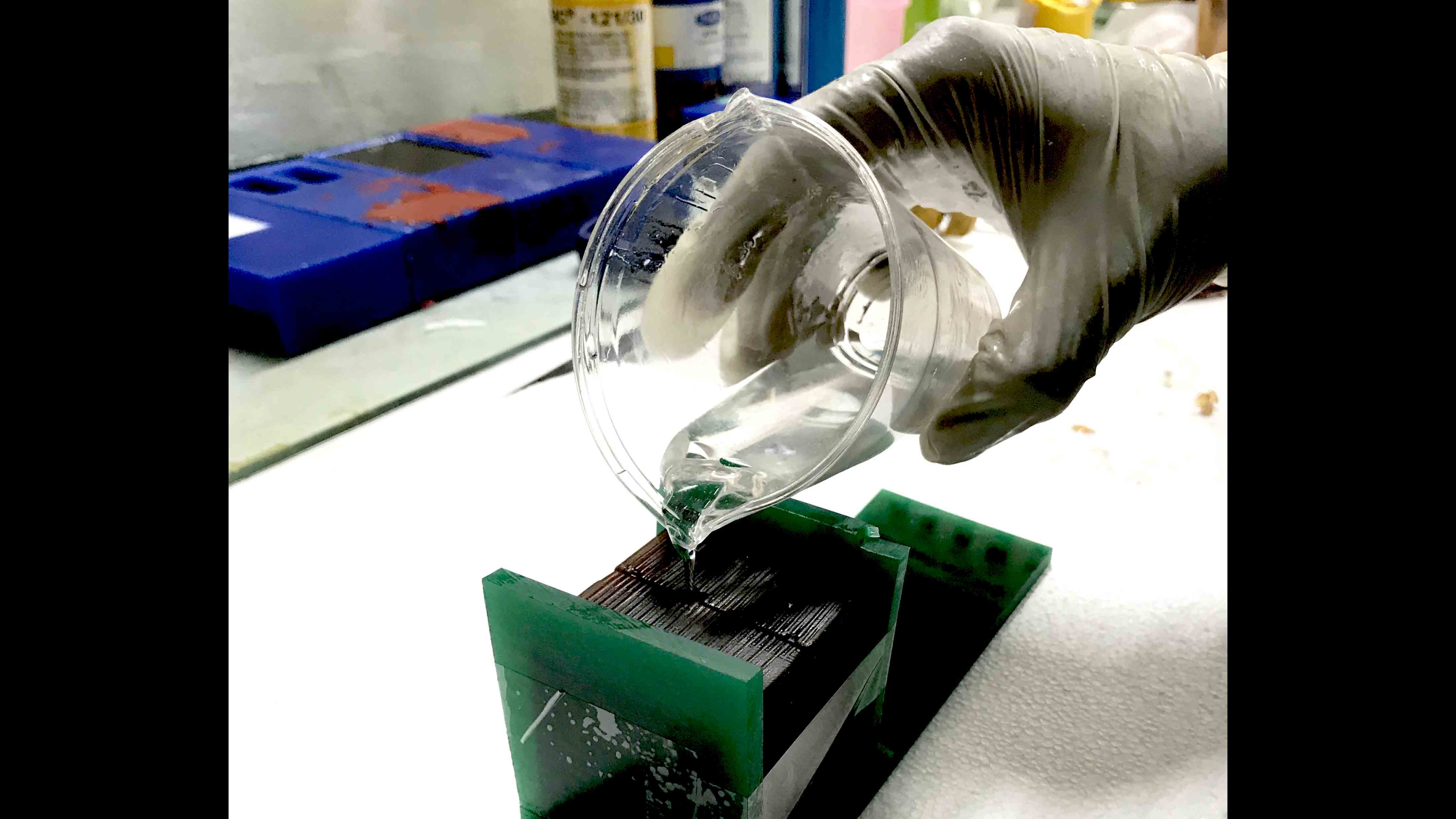
Pour carefully and shake the mold for a while after filling resin to remove air bubbles trapped inside
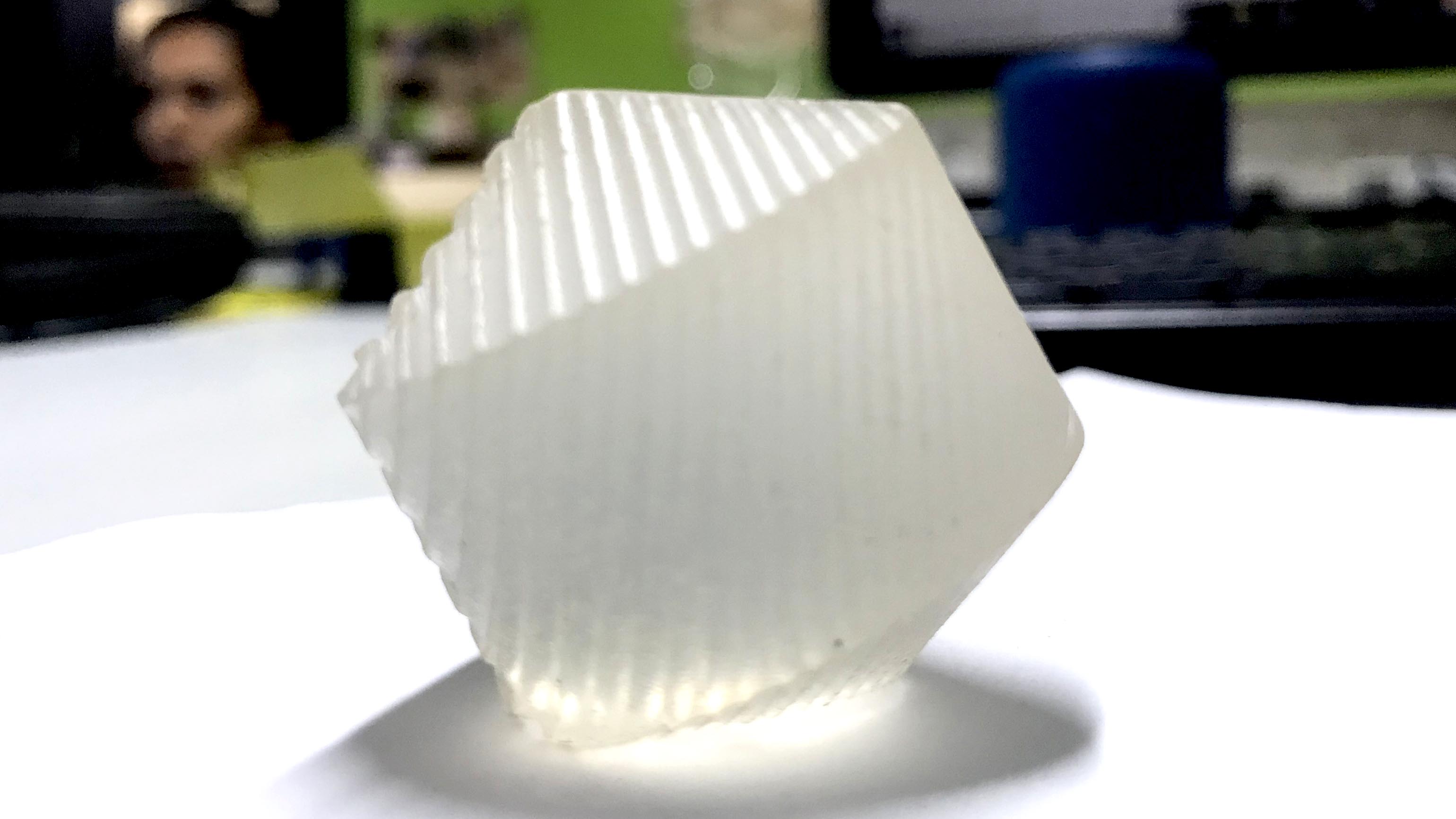
Here is the finished cast
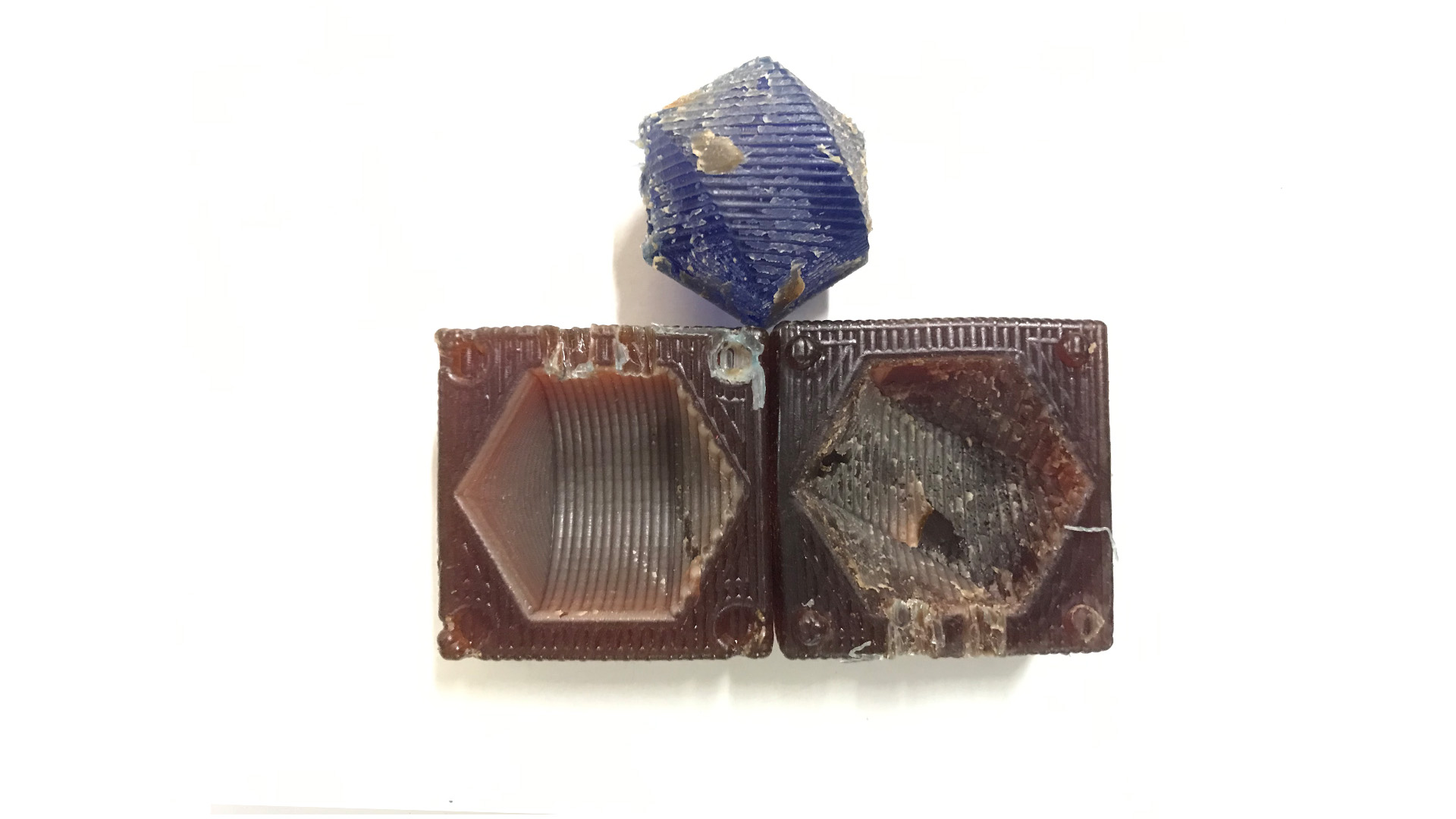
My friend added blue pigment to the resin and had some excess resin, so I made another cast but this time the mold surface was dry and I forgot to put releasing agent. The cast was struck inside the mold and i had to apply a lot of force to remove it from the mold which destroyed the mold.
Making mold using silicone rubber RTV
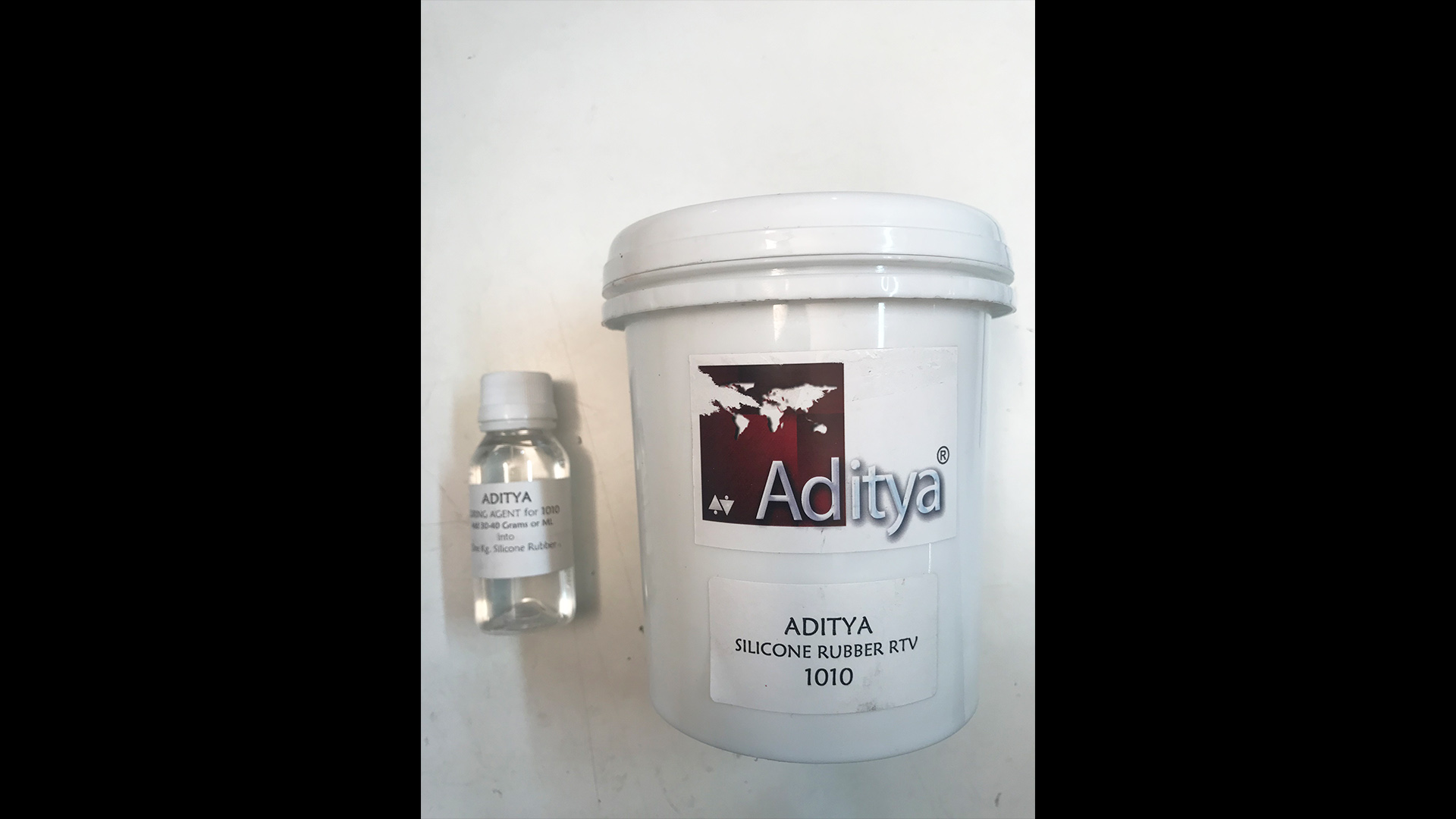
I decide to make another mold using silicone which can be withstand upto 300 degree celsius, which is suitable for casting bismuth. The melting point of bismuth is 271.4
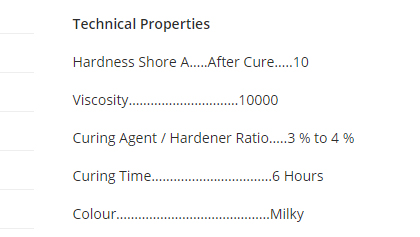
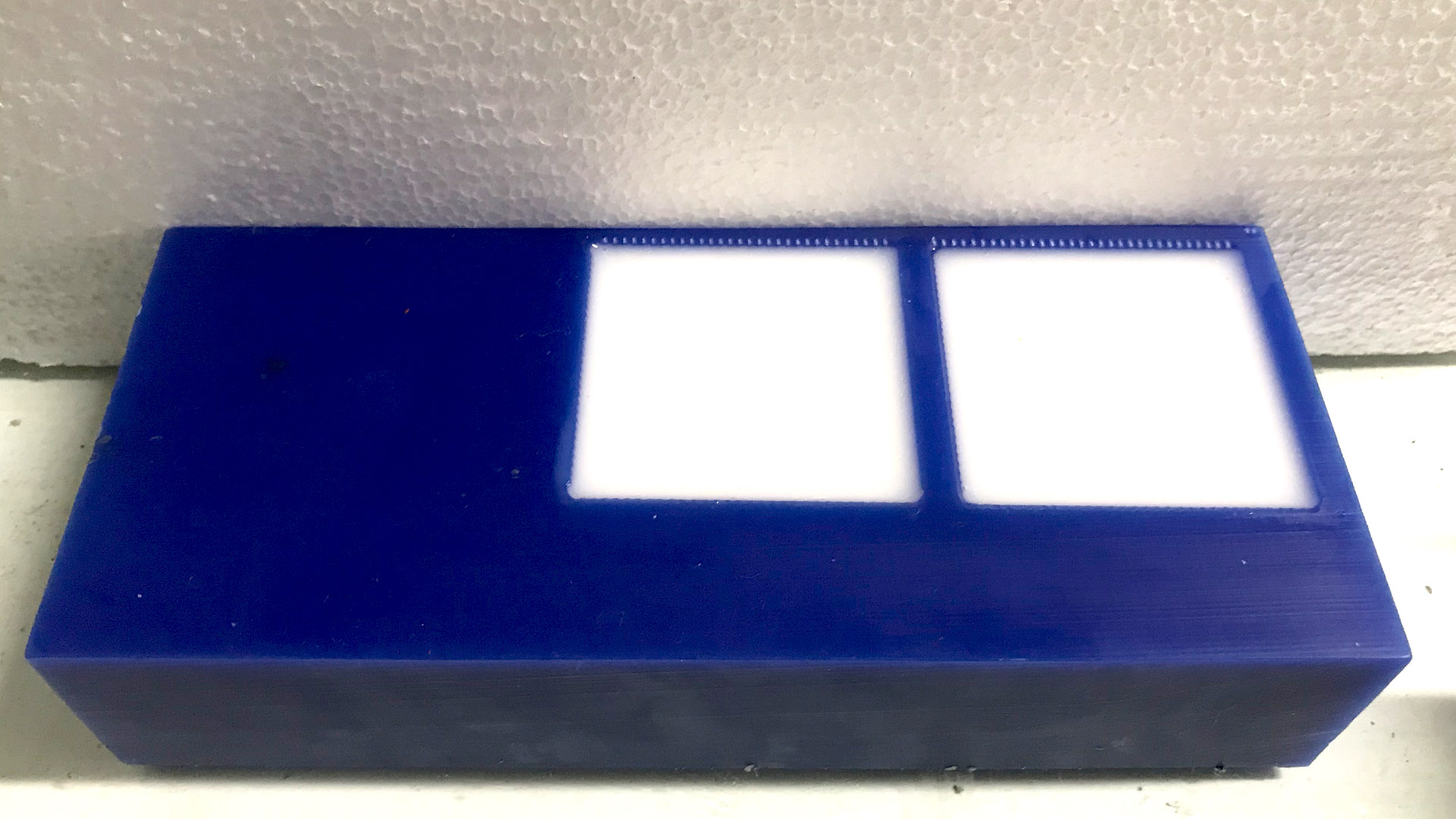
Again removing the mold was a difficult task
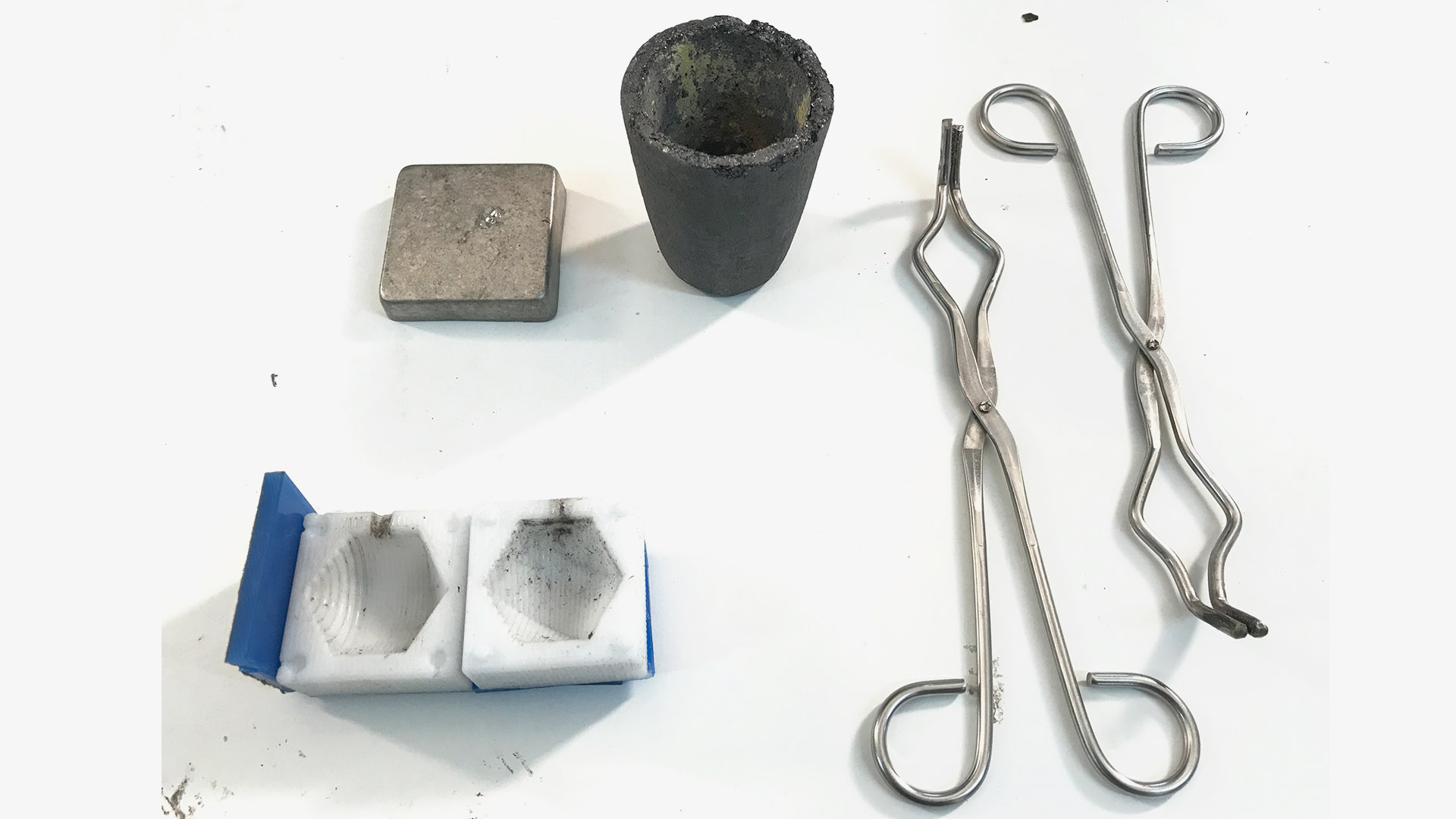
- Bismuth block
- Silicon carbide crucible
- Crucible tong
- Silicone mold
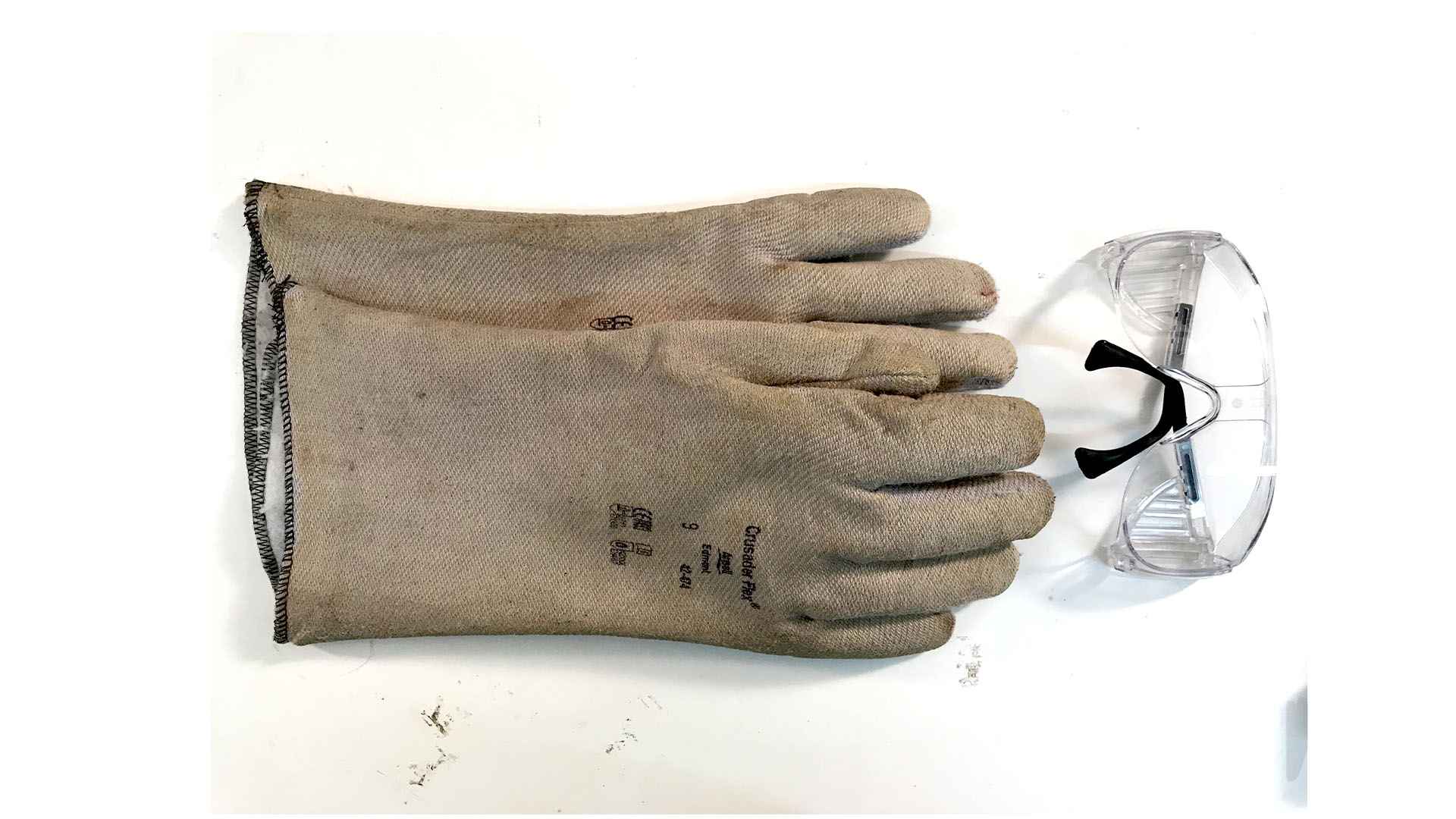
Always make sure that you have safety equipment before using the furnace. Make sure that you wear good shoes before handling molten metal
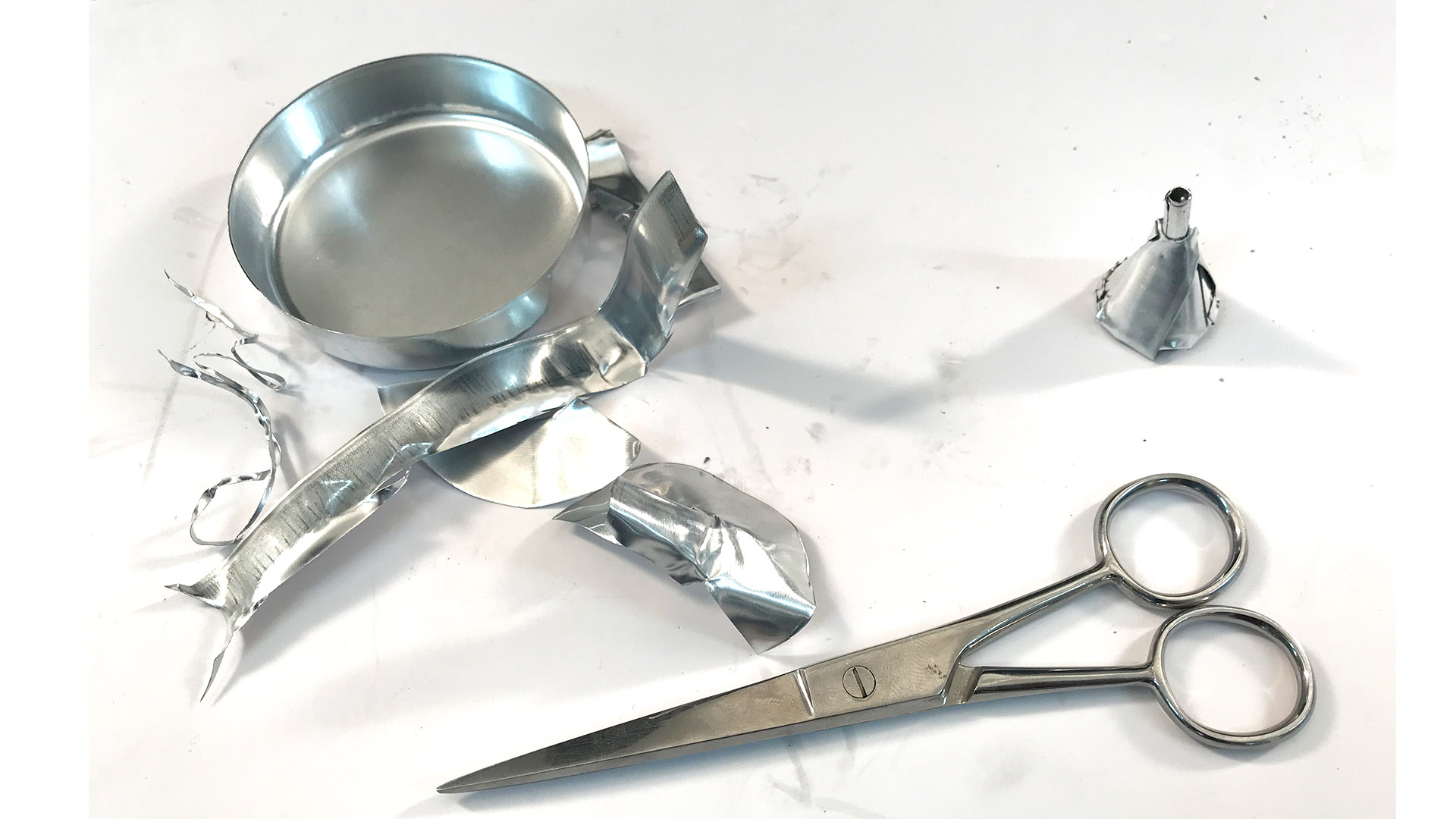
It is very difficult to pour moltem metal through small hole So i decide to make a small finnel using thin aluminium sheet
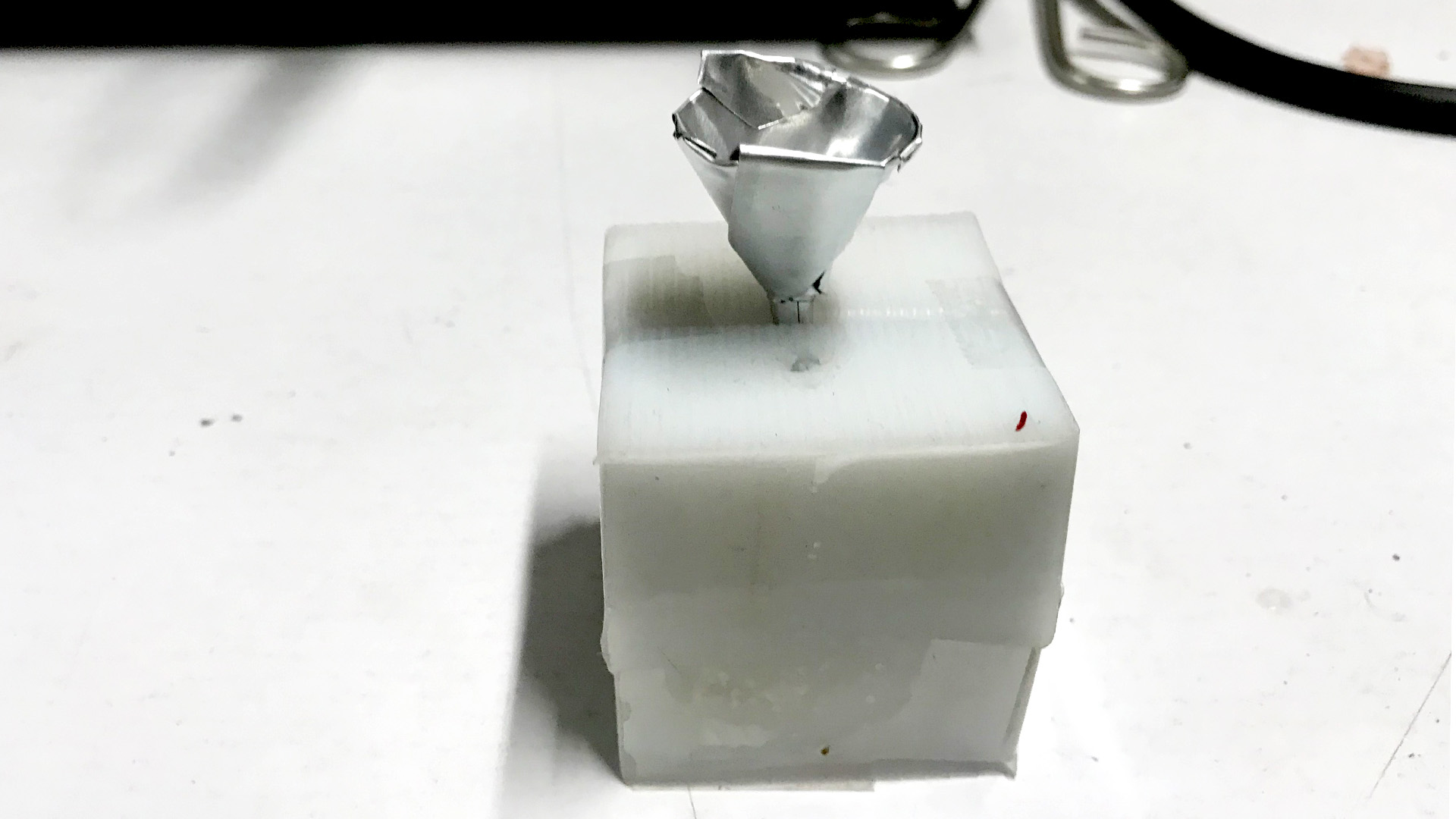
The strength of the funnel is not so good but it serves the purpose
Use proper safety equipments while handling hot metals.
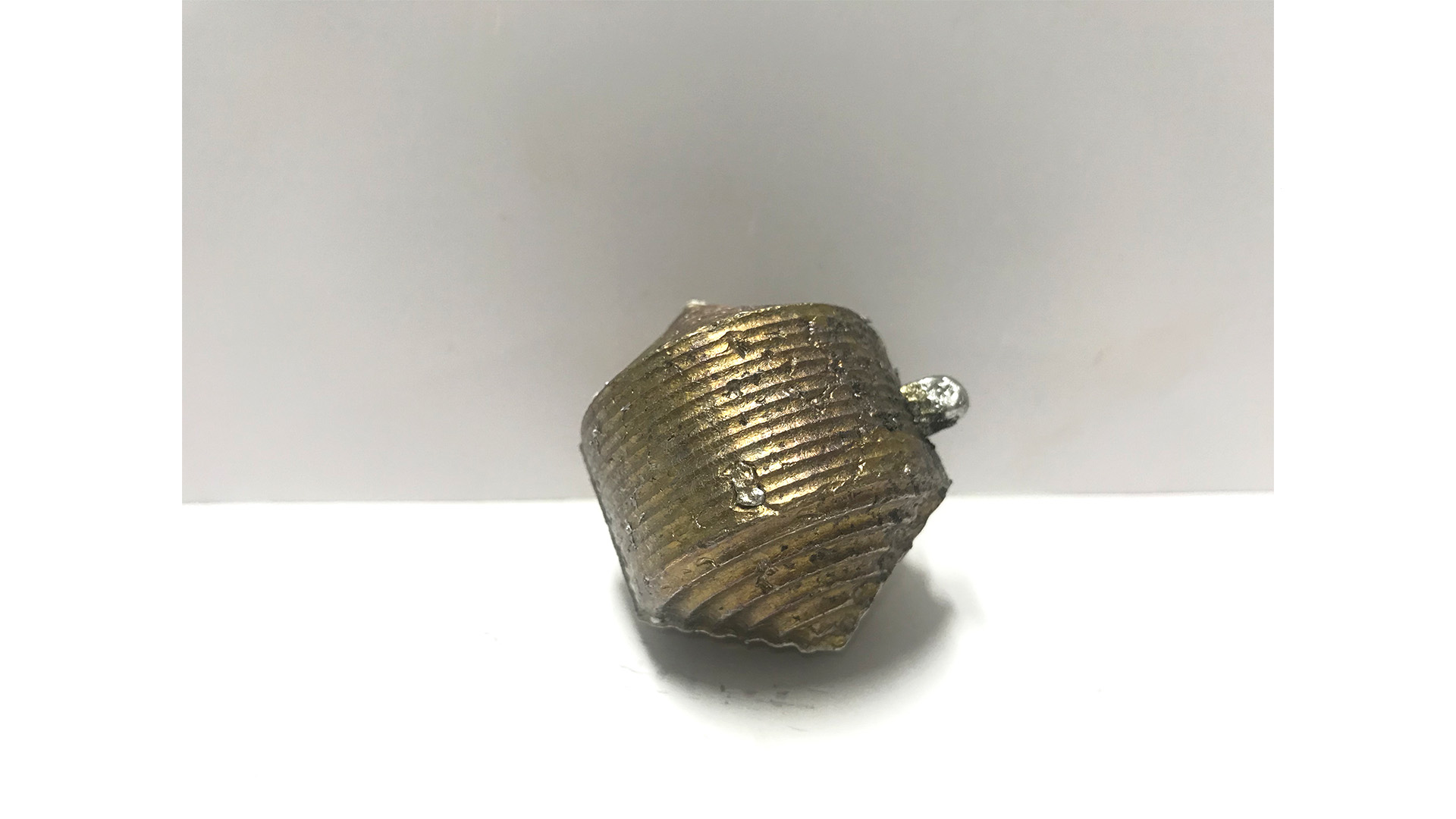
This is the hexasphericon before finishing the surface. I didn't use finishing cut while milling in modella.
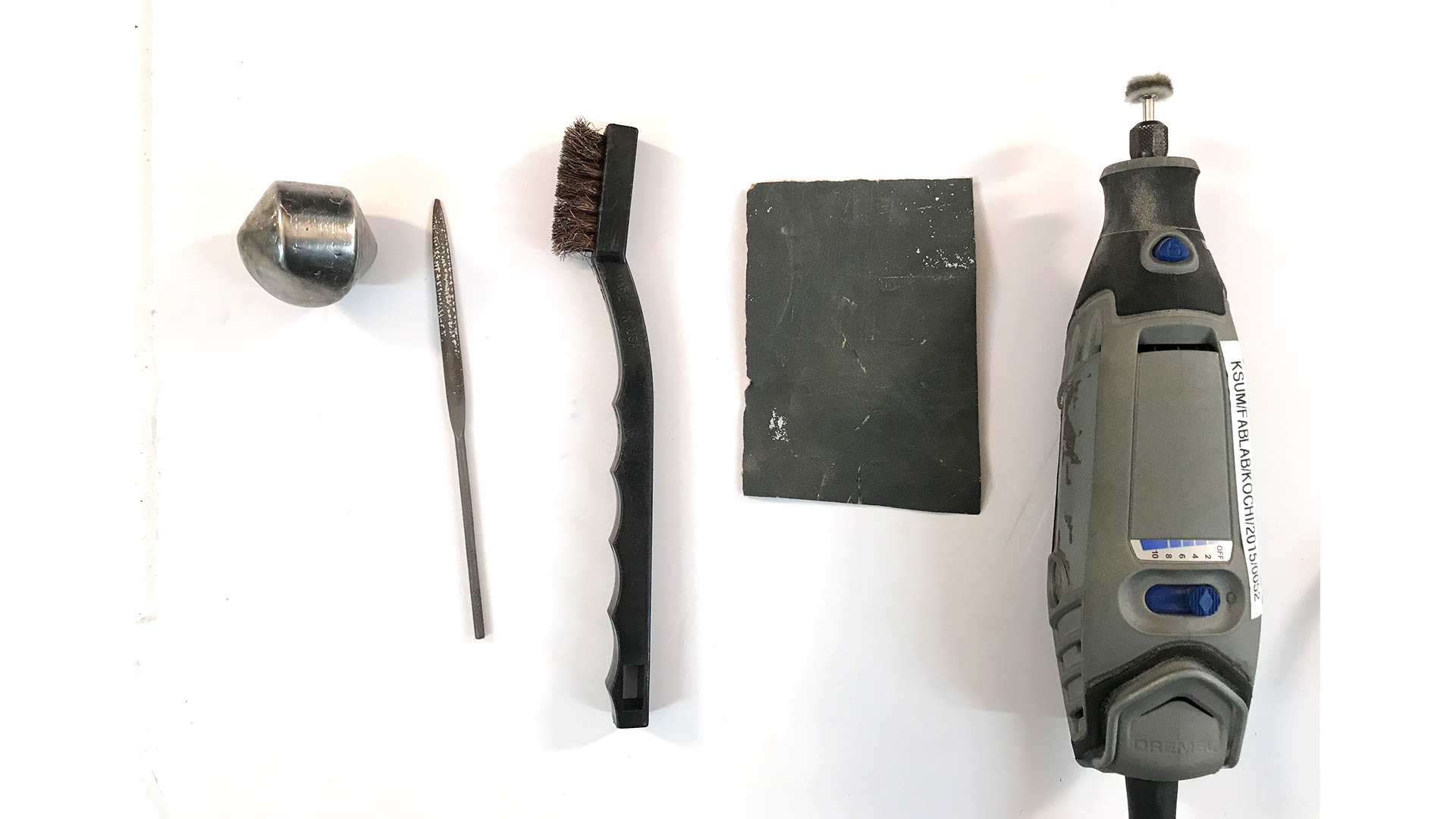
I have used dremel, wire brush, sand paper & file to finish the surface. Is was not easy task, because is I remove more material from one area then it will effect the symetry of the object.
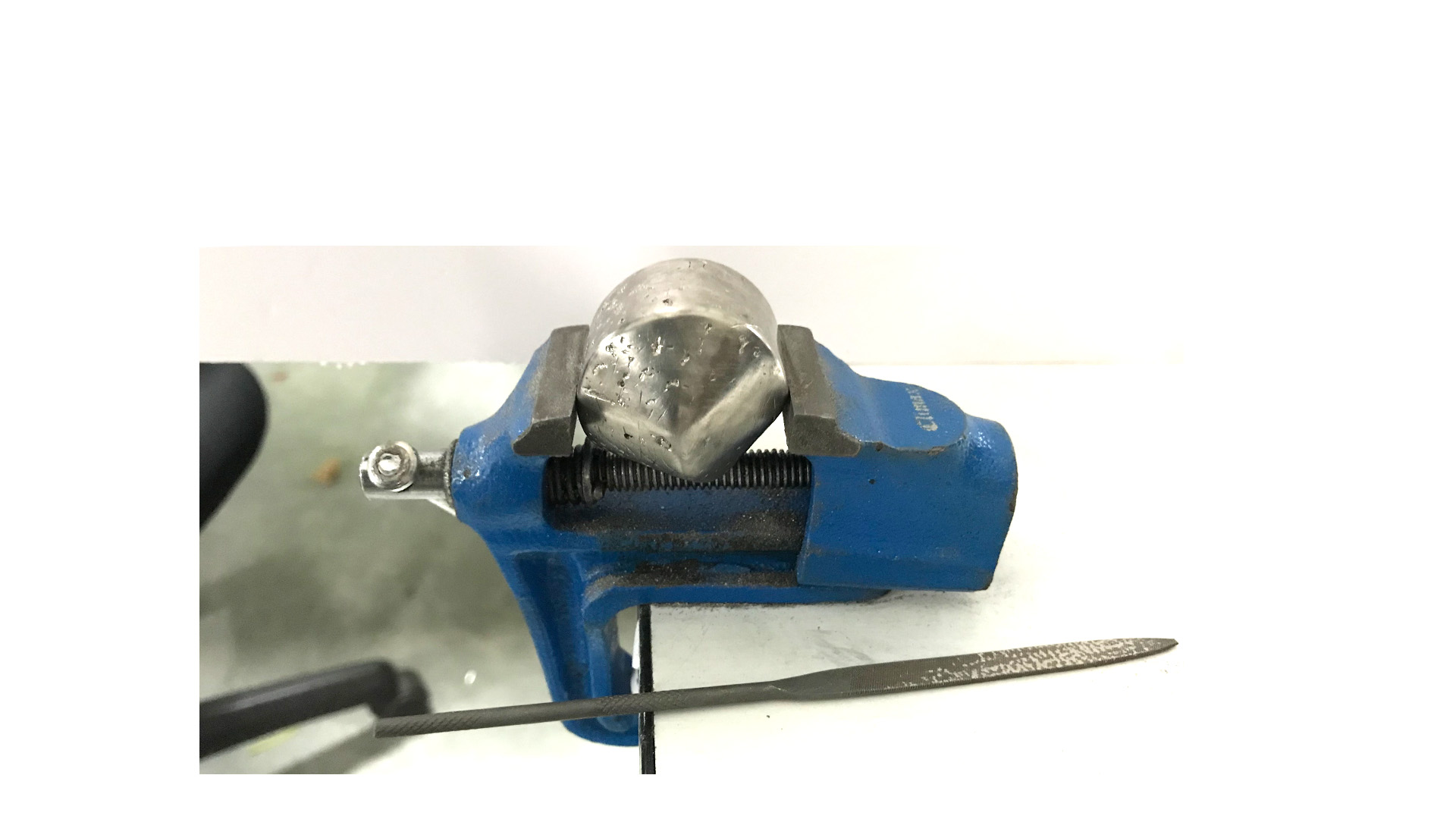
I used thi miini vice to keep it in position.
Here is the rolling video of hexasphericon.
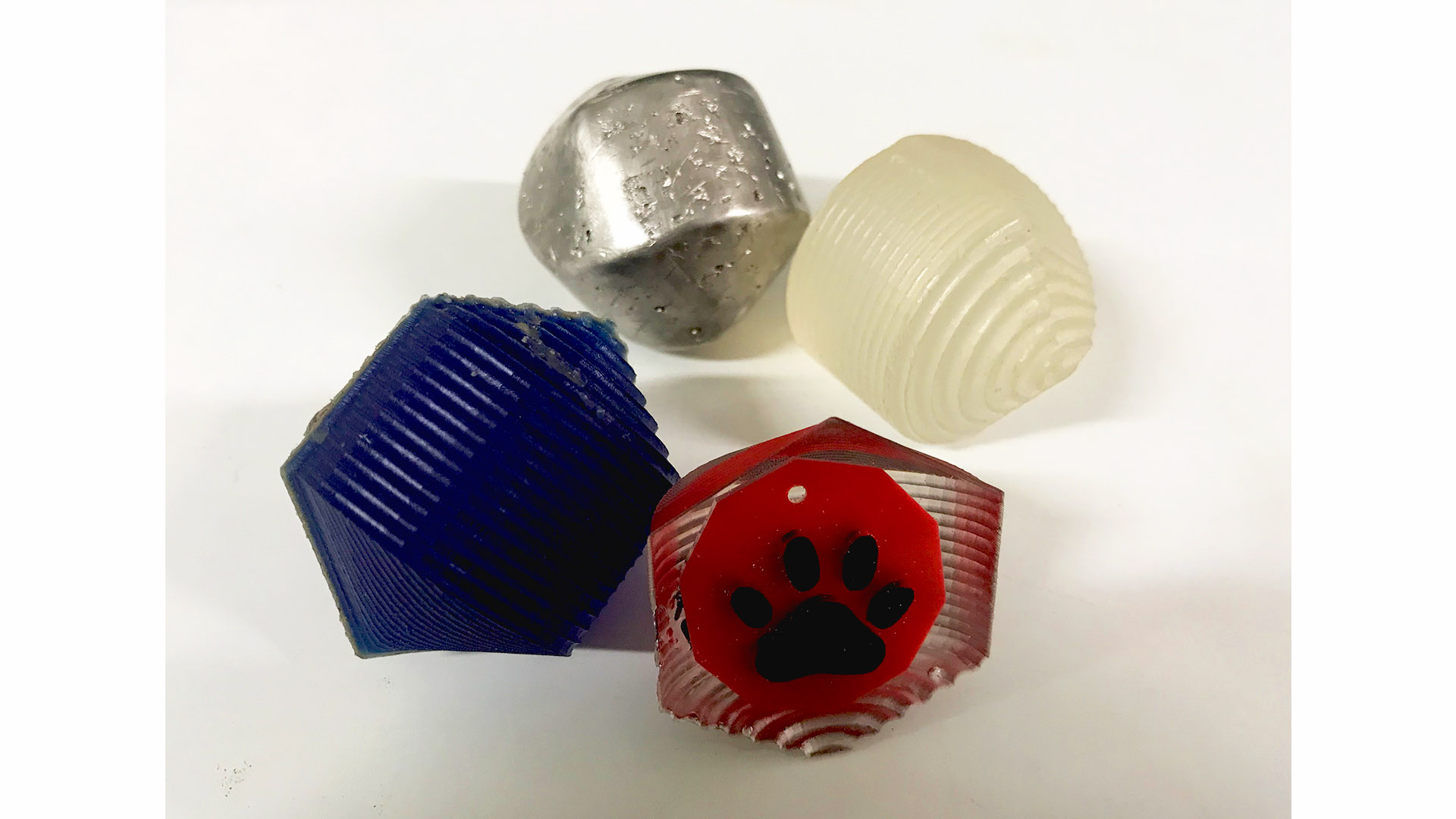
I have used normal resin first then used blue pigment for the cast.
Group assignment
Review the safety data sheets for each of your molding and casting materials, then make and compare test casts with each of them
SMOOTH CAST
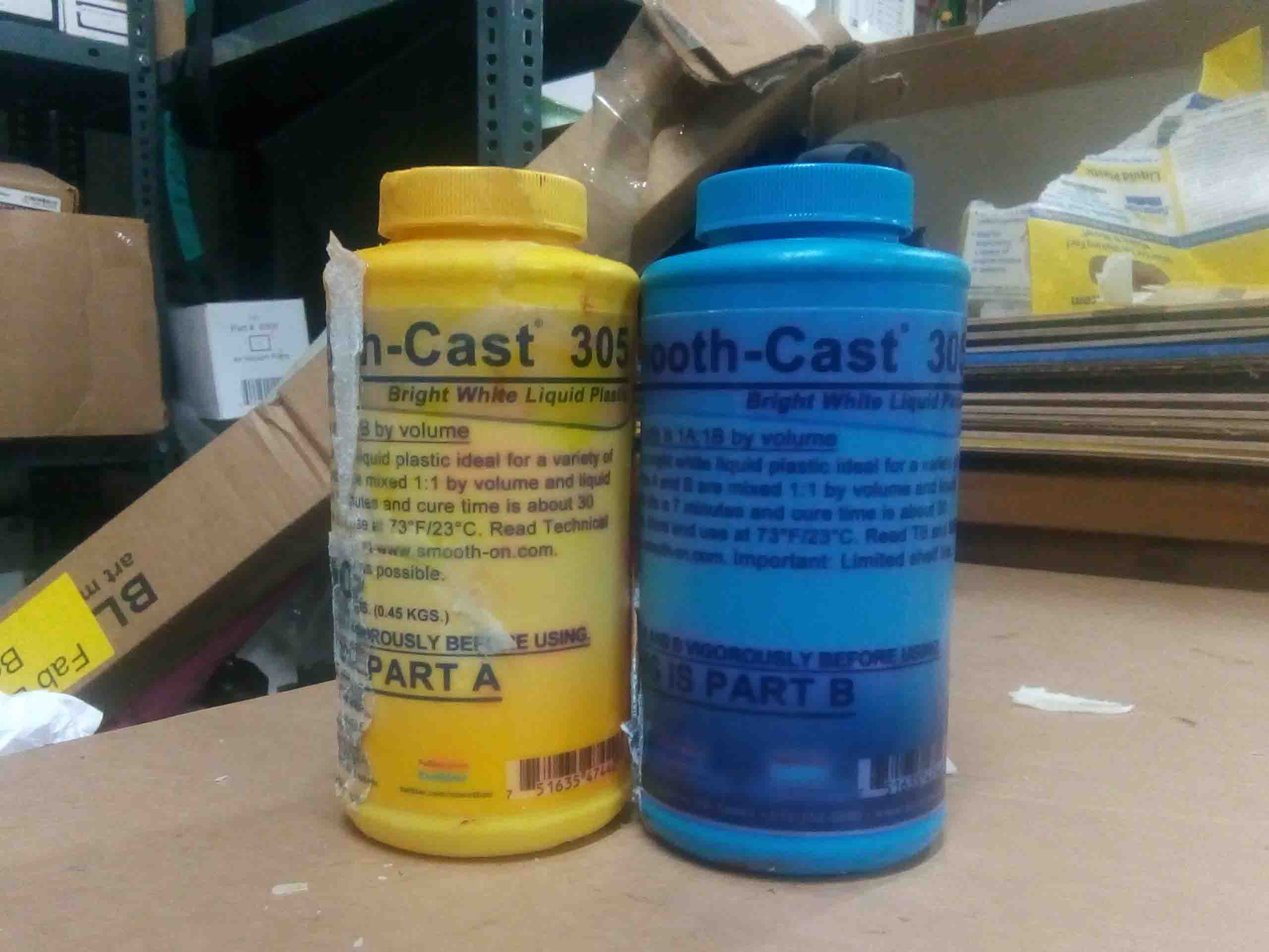
The Smooth-Cast™ 300 Series of liquid plastics are ultra-low viscosity casting resins that yield castings that are bright white and virtually bubble free. Vacuum degassing is not necessary. They offer the convenience of a 1A:1B by volume or 100A:90B by weight mix ratio. The differences between them are pot life and demold time
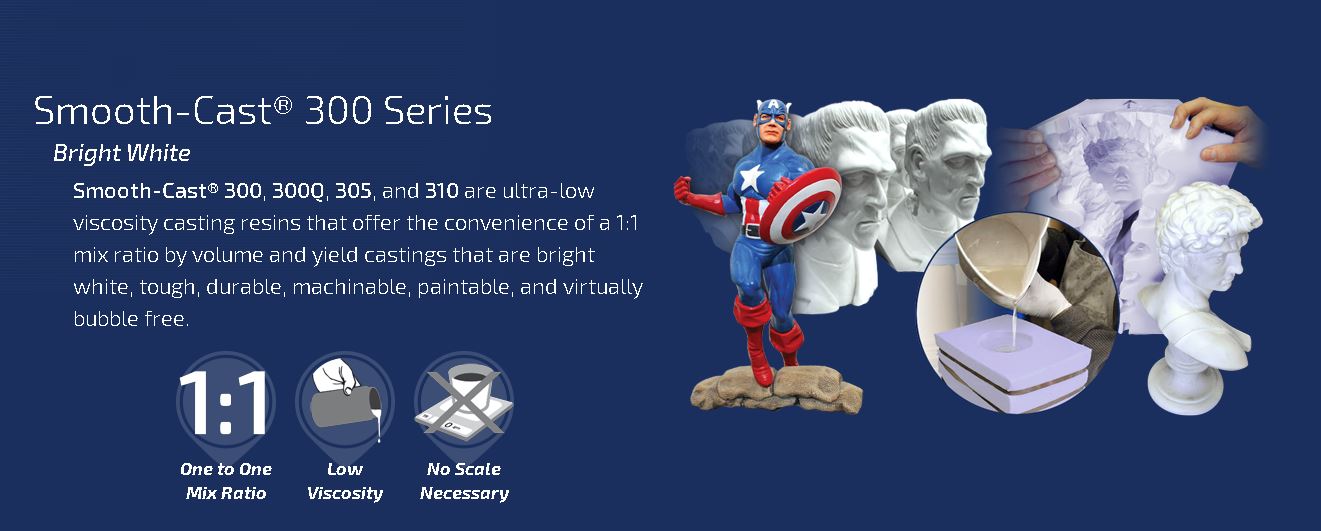
Instructions
- Safety - Materials should be stored and used in a warm environment (73° F / 23° C). These products have a limited shelf life and should be used as soon as possible. All liquid urethanes are moisture sensitive and will absorb atmospheric moisture. Mixing tools and containers should be clean and made of metal, glass or plastic. Mixing should be done in a well-ventilated area. Wear safety glasses, long sleeves and rubber gloves to minimize contamination risk. Because no two applications are quite the same, a small test application to determine suitability for your project is recommended if performance of this material is in question.
- Applying A Release Agent - A release agent is necessary to facilitate demolding when casting into or over most surfaces. Use a release agent made specifically for mold making (Universal® Mold Release or Mann’s Ease Release® 200 available from Smooth-On or your Smooth-On distributor). A liberal coat of release agent should be applied onto all surfaces that will contact the plastic.
- IMPORTANT:To ensure thorough coverage, apply release and brush with a soft brush over all surfaces. Follow with a light mist coating and let the release agent dry for 30 minutes. Smooth-On silicone rubber molds usually do not require a release agent unless casting silicone into the mold. Applying a release agent will prolong the life of the mold.
- MEASURING & MIXING... Liquid urethanes are moisture sensitive and will absorb atmospheric moisture. Mixing tools and containers should be clean and made of metal, glass or plastic. Materials should be stored and used in a warm environment (73°F/23°C). Stir or shake both Part A & Part B thoroughly before dispensing. After dispensing equal amounts of Parts A and B into mixing container (100A:90B by weight) and mix thoroughly. Stir deliberately making sure that you scrape the sides and bottom of the mixing container several times. Be careful not to splash low viscosity material out of the container.
- POURING, CURING & PERFORMANCE... Pour your mixture in a single spot at the lowest point of the containment field and let the mixture seek its level. This will help minimize air entrapment.Best results are obtained using a pressure casting technique. After pouring the mixed compound, the entire casting assembly (mold, dam structure, etc.) is placed in a pressure chamber and subjected to 60 PSI (4.2 kg/cm2) air pressure for the full cure time of the material.Use this product with at least room size ventilation or in proximity to a forced outlet air vent and do not inhale/breath fumes. Fumes, which may be visible with a significant mass concentration, will quickly dissipate with adequate ventilation. Castings with significant mass may be hot to the touch and irritate skin immediately following cure. Let casting cool to room temperature before handling.
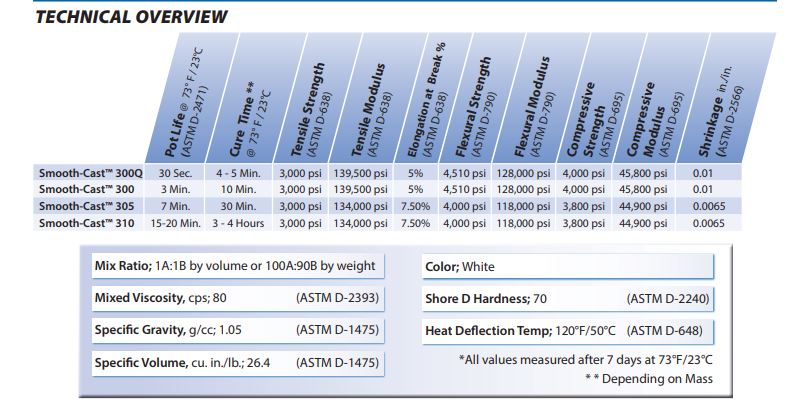
- Inhalation: Remove source(s) of contamination and move victim to fresh air. If breathing has stopped, give artificial respiration, then oxygen if needed. Contact physician immediately.
- Eye Contact: Flush eyes with plenty of water. If irritation persists, seek medical attention. Skin Contact: In case of skin contact, wash thoroughly with soap and water.
- Ingestion: Do not induce vomiting unless instructed by a physician. Never give anything by mouth to an unconscious person.
Casting restin
For casting we are using Aditya Easy Cast Transparent Epoxy Resin - 33-750gm. It is very easy to use.
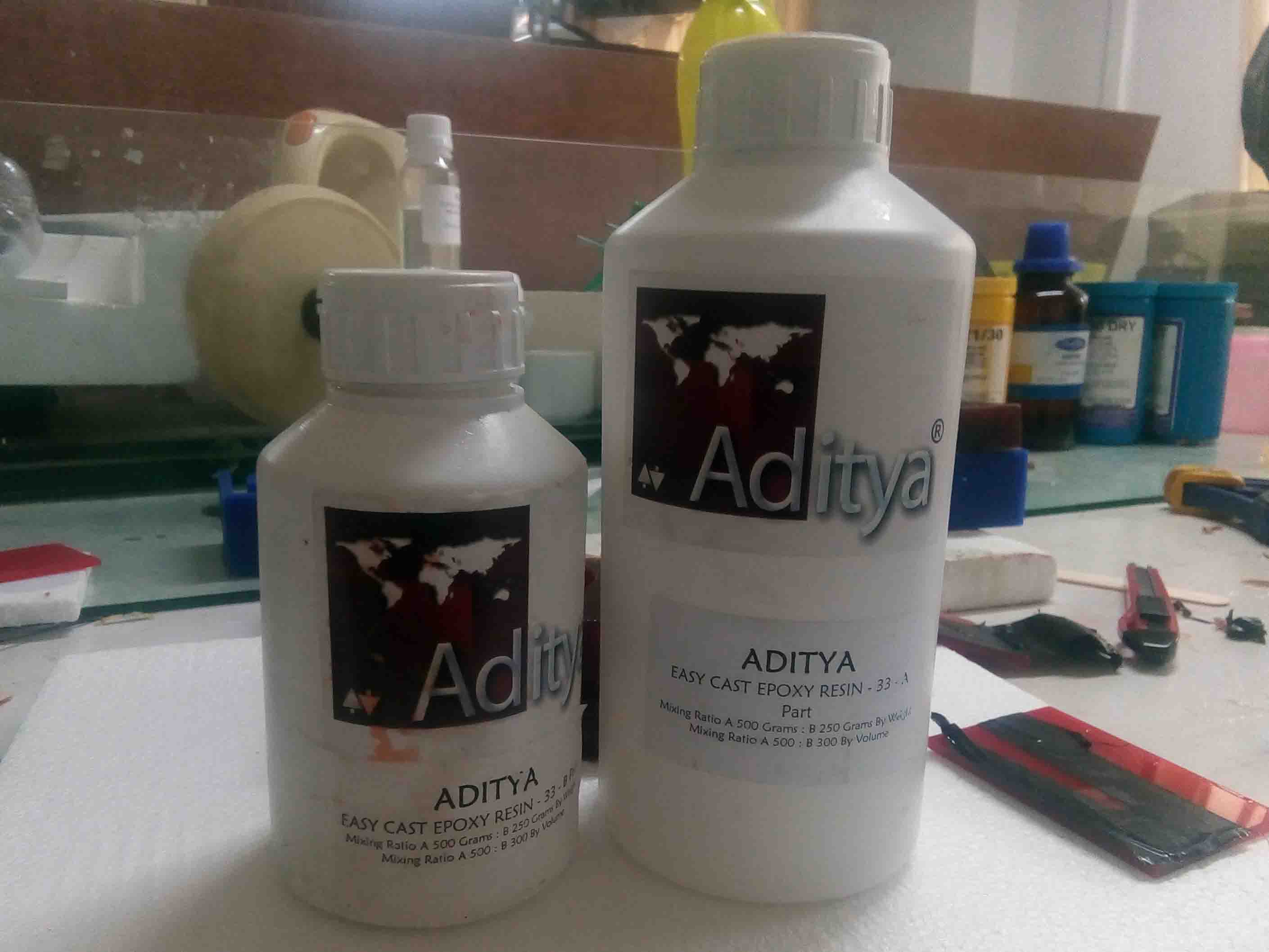
Description
Aditya Transparent Epoxy Resin is specially created for embedding and making small statue's casting. Ratio in Grams not ml....A Part 100 grams : B Part 50 Grams
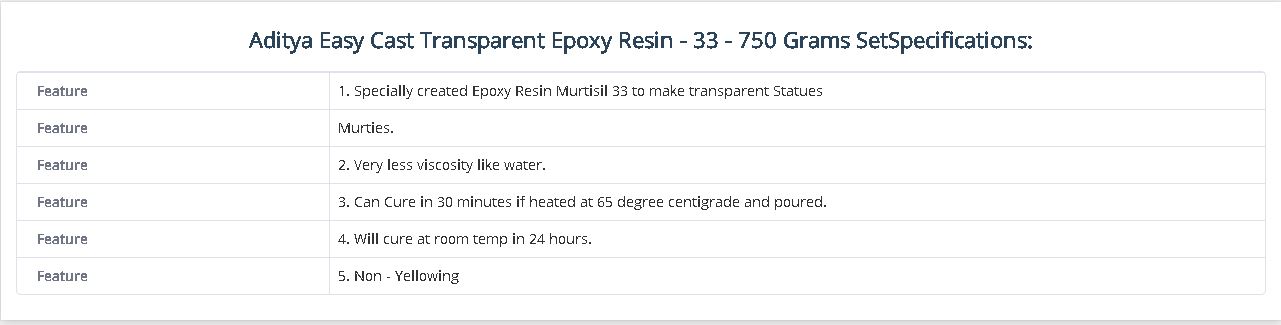