Moulding and casting
Week 10
ASSIGNEMENT
- Design a 3D mould
- Machine it
- and cast parts from it
SOFTWARE USED
LEARNING EXPERIENCE
This week, I decided to cast a piece in elastomere.
I wanted to make a shock absorber that you can add on an existing bike fork.
First I made some research on the web and saw that there was few system for that.
It was always attached to a specific model of bike.
Nothing exists separately.
I learned about materials to cast, silicone, elastomere, PU...,helped by Denis, Axel and his lab.
I learned also to design taking into account the tool used :a CNC 3 axis, the bits ...
FILES
Shock absorber fusion 360
Shock absorber STL
Mould fusion 360
Mould STL
MATERIAL SPECIFICATIONS AND SAFETY DATASHEET
silicone rubber
silicone rubber Safety datasheet
P90 polyurethane
P9O semi-flex Safety datasheet
PVA mould agent
PVA mould agent Safety datasheet
DESIGNING THE MOULD

This is the kind of shock absorber that exists
Let us begin to design ...

I designed the bike frame parts to join with the shock absorber

Designed it on fusion 360 with a sketch to design the profile and revolve tool to construct the form in 3D

After designing the part I wanted to produce,
I designed the mould in adding the shock absorber design with a cube to make half of the mould
I made the positive to be able to make two parts the same to cast with opposite cylinders in positive and negative .
PRODUCING THE MOULD
To mill our assignments , Denis and I used the CNC of
Yourlab in Andenne during a training course of Fusion 360.
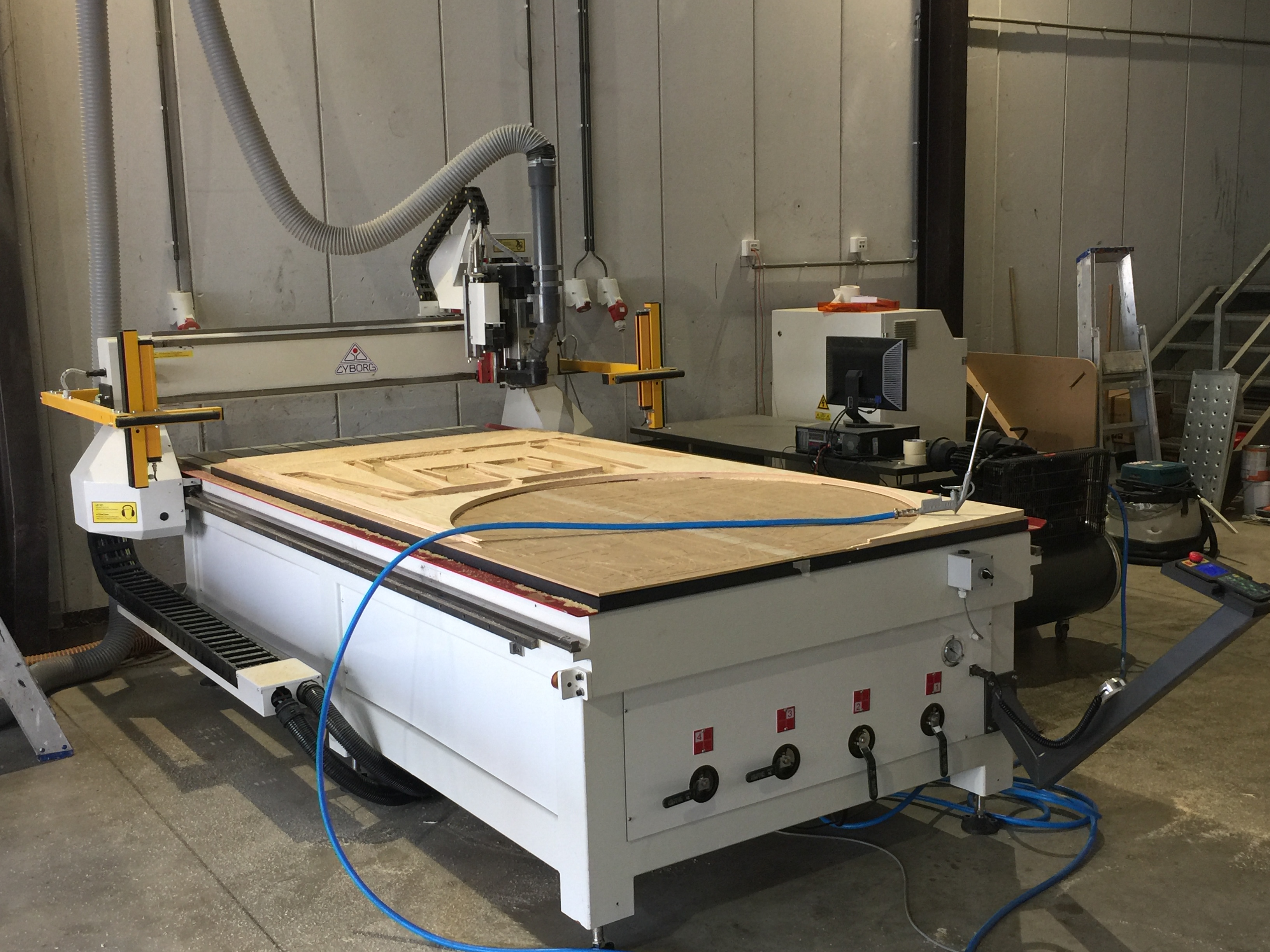
To make the mold I used polyurethane of 4 cm.
The method used was to prepare the cam files on Fusion by doing a 3D pocketing and then a finishing pass.
Unfortunately, I don't have the files anymore of those steps.
With Xavier, the fabmanager, we entered the parameter in the CNC,see image below.
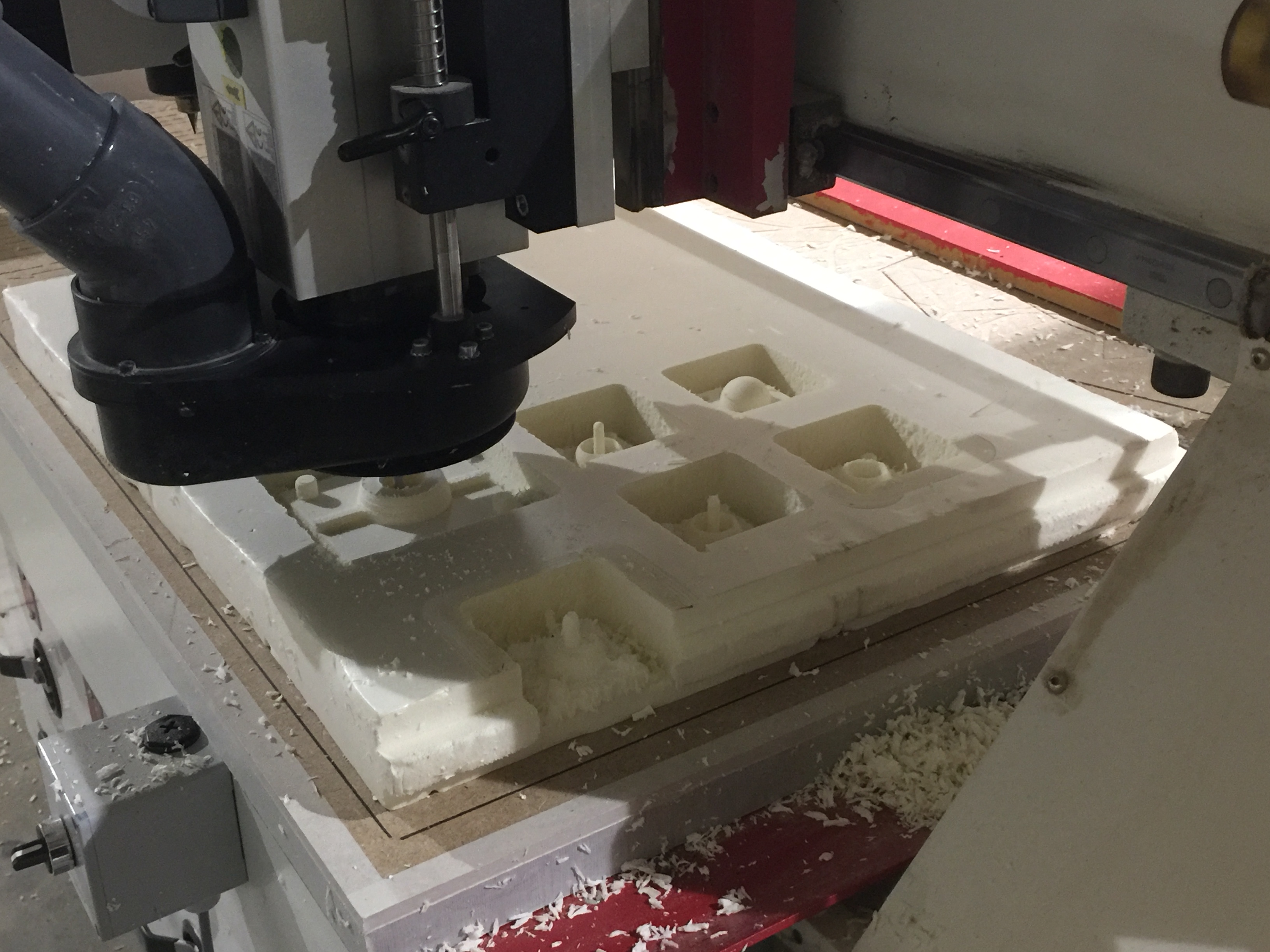
We milled the 2 project at the same time : Denis's spinning top and my bike shock absorber.
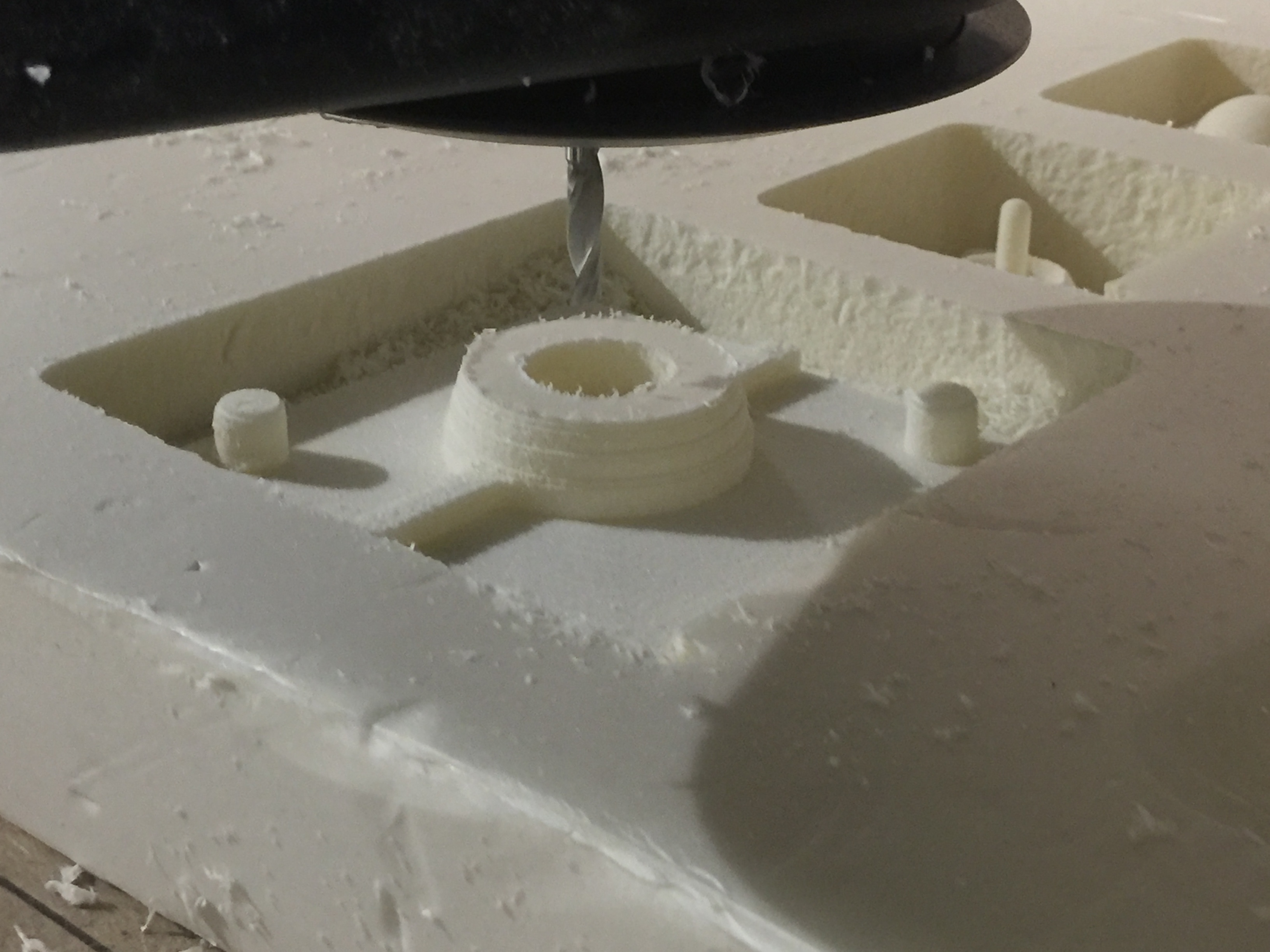
Back to Brussels ...
I made walls in plexiglass on the laser cutter to retain the silicone around the positive part made in PU

This is the mould prepared to receive the silicone

I put a PVA mould release agent on top of the polyurethane from
Easy composites.
With this product, it is made possible to unmold.
I used
silicone rubber from Easy composites to make the mould
I mixed the 2 components(proportion 10/1) of the resin and poured it into the mould
SAFEY FROM THE DATASHEET: