WEEK 8
Computer Controlled Machining
Equipment
- Hardware: Shopbot
- Software: Fusion360, AutoCAD, VCarve
- Material: Plywood 15mm
Fusion Design
My housemate and I are on the shorter side and have trouble reaching things on the top shelf of our cabinet. To keep us from having to climb on the kitchen counter everytime we want something, I decided to build us a small step stool.Sketching step stool
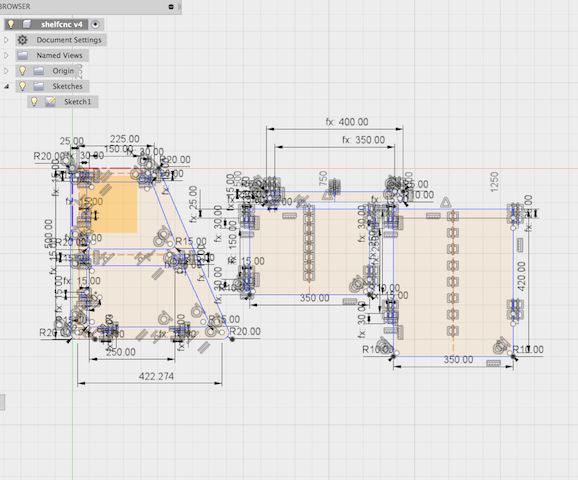
VCarve
From your 2d design software, save DXF file and import vectors into VCarveVectors
Before making toolpaths, you need to prepare your vectors by deleting duplicate vectors and looking for open vectors.Duplicate Vectors
Right click to check for Duplicate Vectors & Open Vectors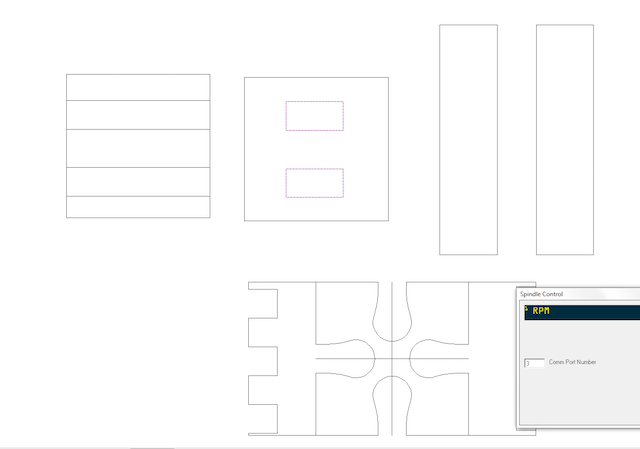
Duplicates will be shown by a purple outline. Delete any duplicates until you get a No Duplicate Vectors message.
Open Vectors
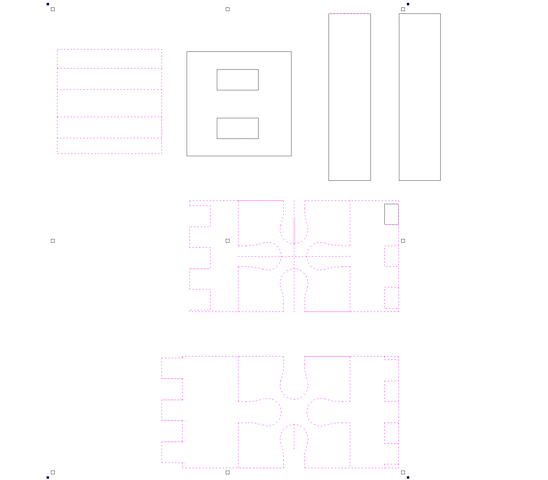
Duplicate vectors will also be indicated by purple outlines. You need to join the vectors by right clicking and chosing join options.
*I encountered a lot of problems here with regards to open vectors. You can read through how I fixed these problems below.
Fillet
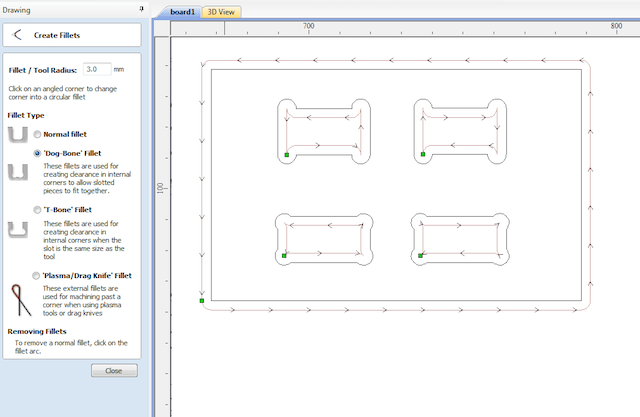
For any joints, you'll want to create fillets at the corners. This is because the mill can't create an angle due to the shape of the endmills, so you need create rounded corners for your press fit construction to fit properly.
Toolpaths
Tool Settings: Feedrate and RPM
I used a 6mm 1F downcut endmill for the 15 mm softplywood. Referencing the Chipload Chart recommended from our lab, I found that the optimal chip load for softplywood with a 1/4 1F endmill is from .011'' to .013''.Chip load = feedrate (in/min) / (RPM x no. of flutes)
We started with an RPM=10,000 as this was a recommended place to begin. To get the optimal chipload of .012 we should set the Speed rate from 110-130.
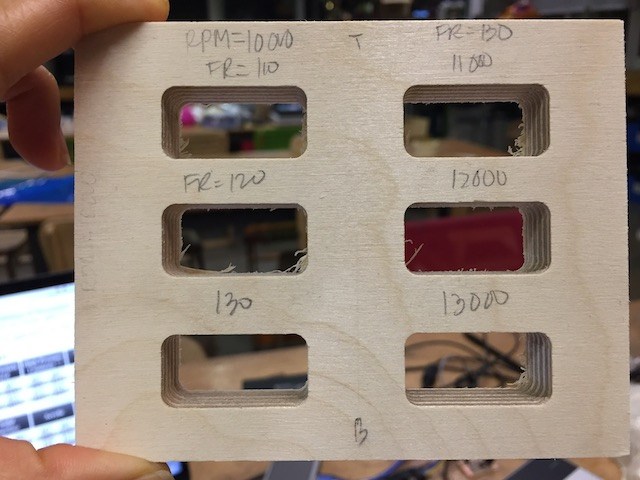
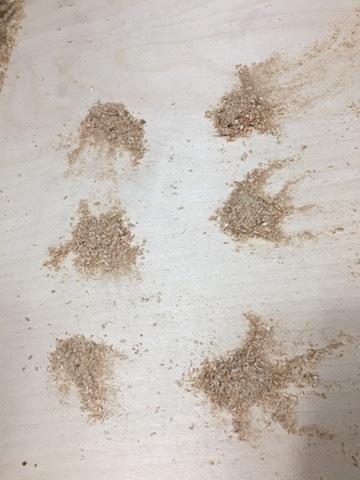
At a speedrate of 110, it seemed that the chipload was too fine. 130 looked pretty good.
Keeping the feedrate constant at 130, I changed the RPM from 11,000-13,000 using the equation to stay within the range of the optimal chipload. The chipload results all looked pretty similar with the exception of the RPM 10,000 FR=110. I decided that somewhere in the middle of this range would be acceptable for cutting this material. The RPM 11,000 with a feedrate of 130 looked to be a bit of a cleaner cut in the back so this is what I used for my settings.
Pass depth should be half of endmill diameter
Stepover 40% of diameter
Incut
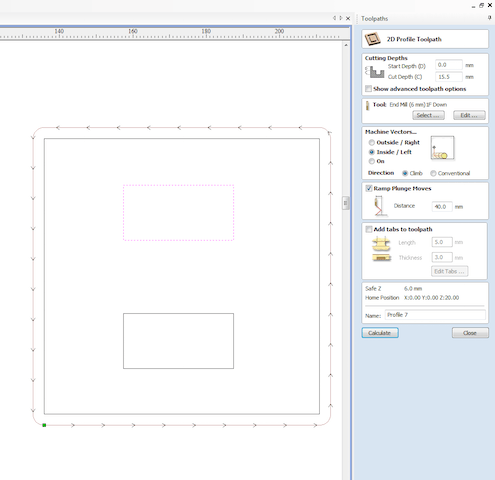
Cut Depth= thickness of material being cut + (.5-1.5 mm) to ensure the mill cuts all way through Tool: Select endmill. We are using 6mm 1 Flute *always select ramp as to not break the endmill Select tabs for larger incut pieces
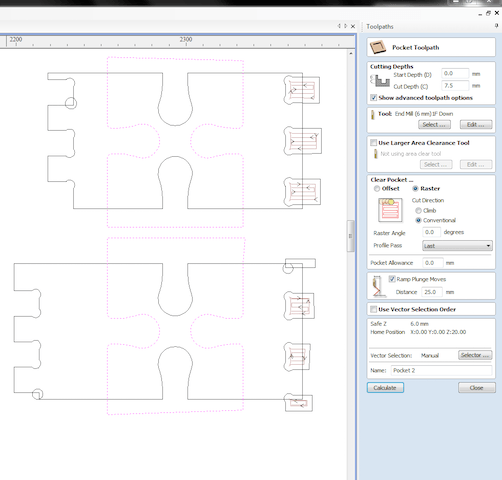
Cut Depth= set to half of material thickness so that when put together, pieces would sit flush on top of one another
Again select Ramp
Outcut
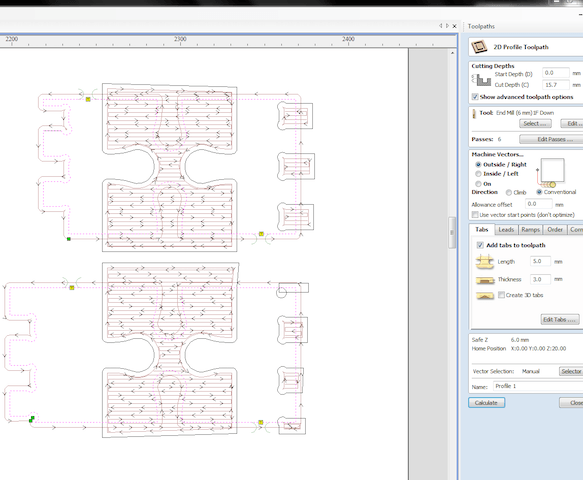
Machine Vectors: Outside/ Right
Always Use tabs for outcuts to hold the piece in place while it is being cut
Calculate
Save Toolpaths
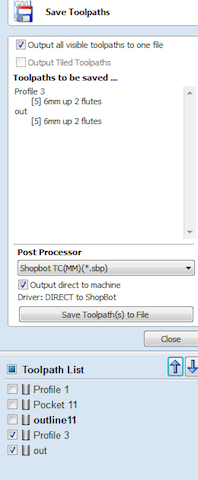
Select toolpaths from the list and save .sbp file. This should open automatically in shopbop
ShopBot
- Release the emergency brake
- Press Reset button to reconnect fuses
Turning on the Machine
- Screw material being cut into the sacrificial board
- Change tool to appropriate endmill for the type of job that you are doing
- Set XY by lining up endmill to the bottom left corner of the material
- Line endmill to bottom left corner to set X/Y origin.
Use Clamp and plate to set automatic Z
- Warm up Spindle
- RPM window must be open when cutting
Setting up for cut
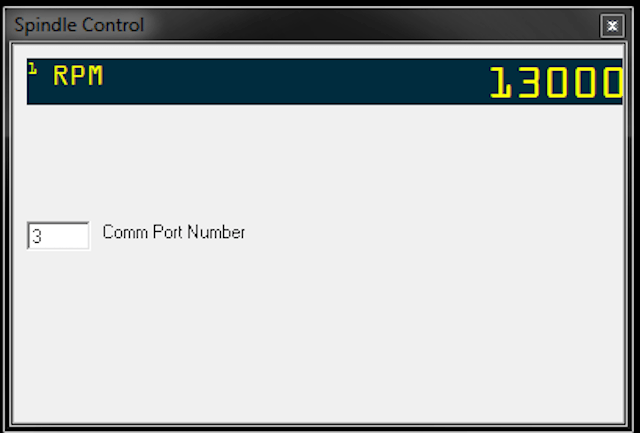
Assignment
Toolpaths
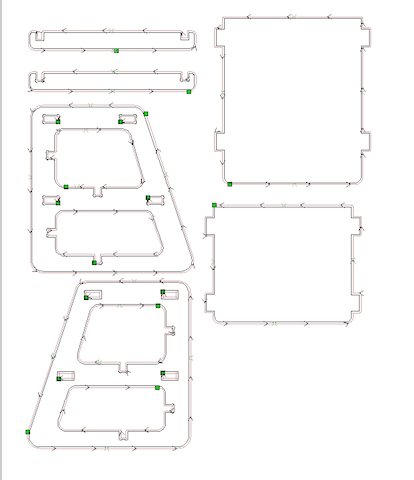
Cut pieces
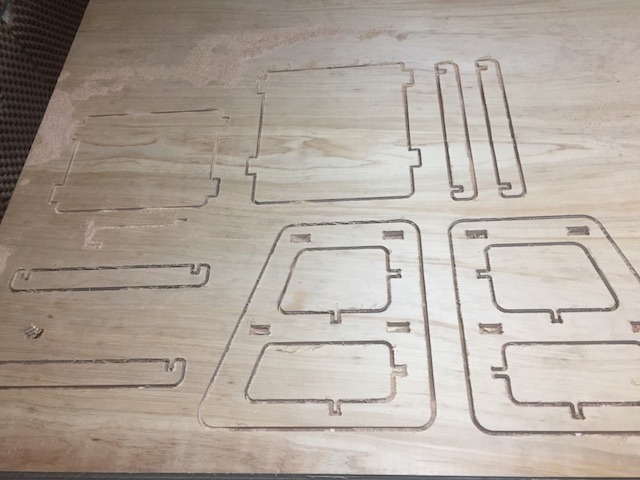
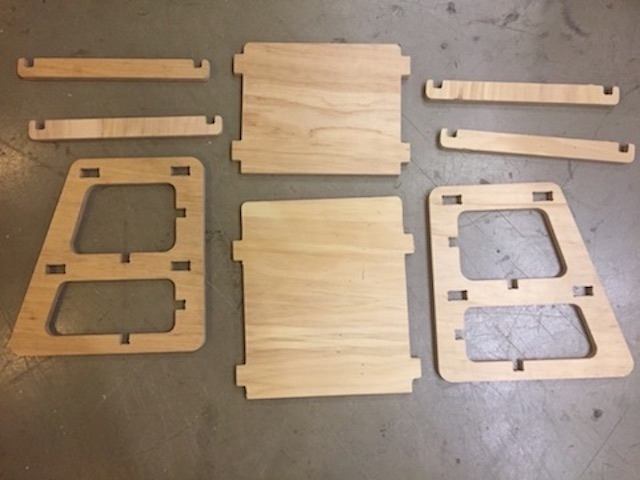
Assembled Step Stool
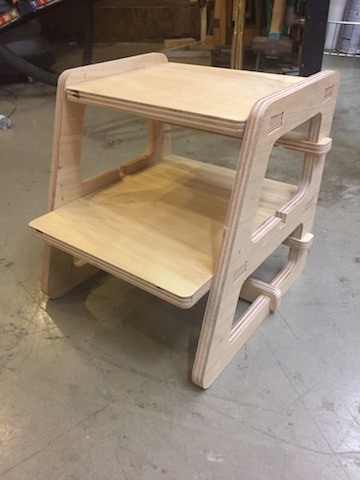
Troubleshooting
When trying to join vectors in VCarve, there were some lines that wouldn't allow me to join them. When looking back at my Fusion file, I couldn't understand why the lines weren't joined as they appeared to have coincident points. A resident of the lab said they encountered similar problems when making sketches in Fusion and graciously offered a tip on how to join them using AUTOCAD.Pedit
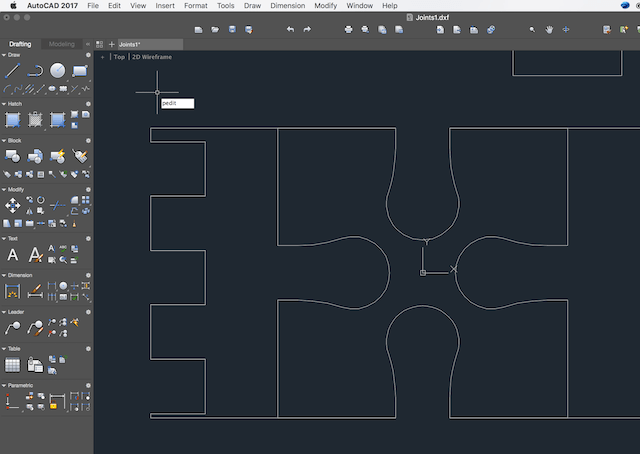
Type pedit and select join.
Select the lines that you want to connect
Break
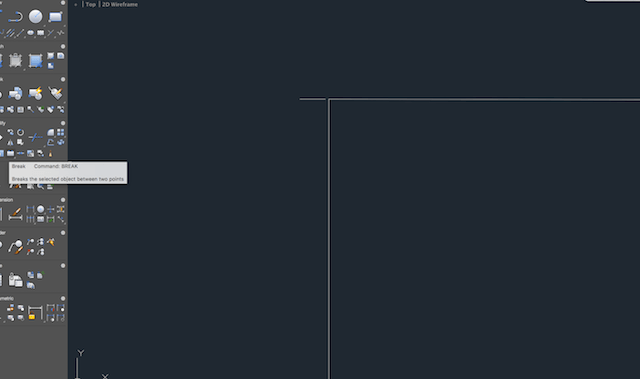
If the lines selected don't join, zoom in a check that there are no overlaps. If the line goes over break and delete unwanted lines and pedit again.