Composite!
First time we tried the process was a mess, we applied way to much epoxy resin on our potatobag fabric, the environment was really not well taken care of and we were really dirty doing the job.
also the fabric was really tick and would'nt take the form of our board. We also didn't wait the proper time fot the epoxy to dry.
We also didn't use the proper security equipment and put ourselves in exposition with harmfull material, we uses short sleeves after a few minutes because of the heat and we didn't had the proper security gloves.
they finally disolve with the contact of the epoxy resin.
One thing that is super cool with making mistakes is that we learn a lot from them! So when we went for ous second try everything was really smooth and easy.
We went to the store and bought some fiberglass, this had a cleaner look and the fabric of potatobag seems to thick for what we wanted.
Once we had the fiberglass, we cut it into the correct form for envelopping our surf.
Then we cover the carboard with the fiberglass and gently applied way less epoxy resin than the first time. we did a clean job and wait for the first side to dry.
Also, Damn we look badass.
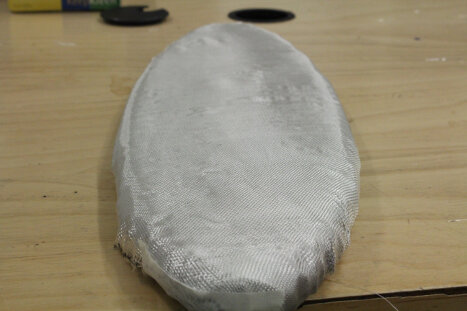
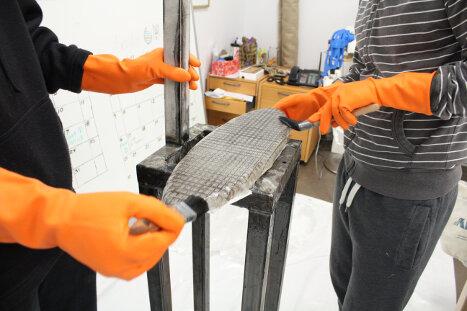
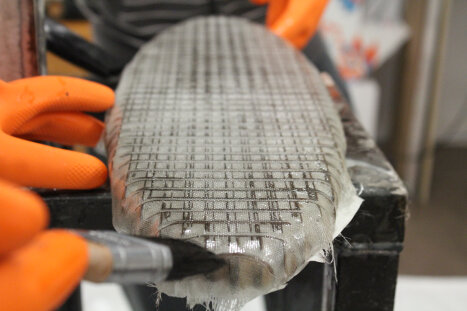
The surf is a sucess, one both side was applied, all we had to do is trim the borders and here we are! The thing I learn is that when working with these kind of process, you really need to prepare your space and thhe way you will
procede in advance, once you know how to proceed everything goes well.