José J. Lazarte R.
Assignment
Design and make a 3D mold (~ft2), ...
I
stood aim to design a lamp that allows to combine different materials
in the structure of different textures and types, as in the case of
jute and epoxy resin by a process to collate both materials and given
shape by applying pressure to a mold to obtain two pieces which then
can fit in shaping the structure of the lamp shall be added to each
piece a few LED diodes to generate light by applying a continuous
voltage to the power terminals.
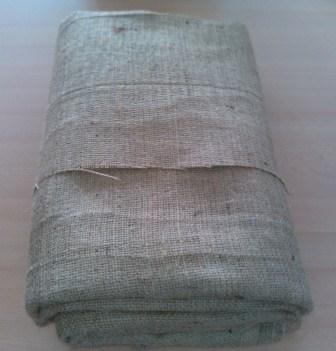 Fabric burlap fiber | 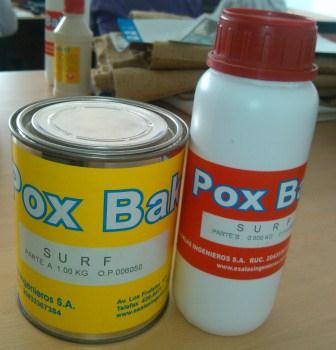 Epoxy | 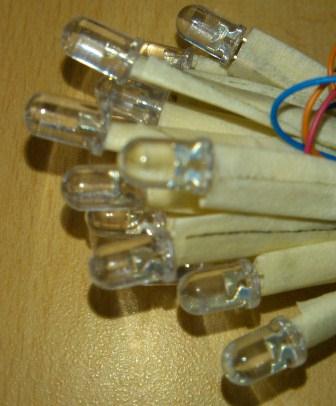 LEDs |
Begin
by describing the design made using Rhinoceros software, by which the
shape of the two parts of the lamp conforming both in terms of the
dimensions that allow us to splice them then these designs are made
first 2D diagrammed. Then perform the appropriate device 3D models of
the two pieces and fit to have a 3D model of the structure of the lamp.
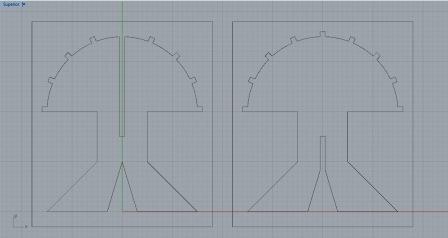 2D Design 41cmX36cm mold each piece part 1 | 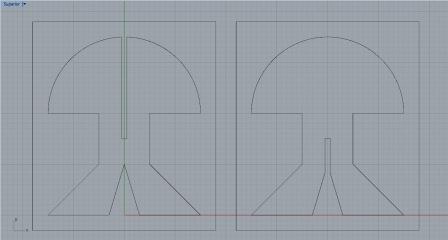 2D Design 41cmX36cm mold each piece part 2 |
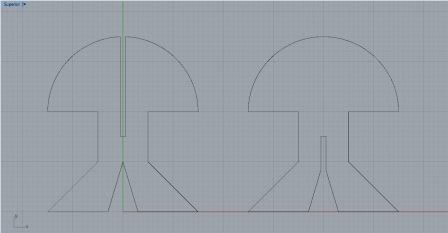 2D Design 35cmX30cm mold to cut the burlap fiber cloth | 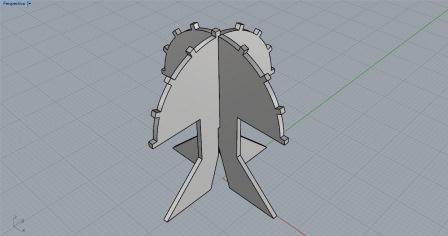 3D Model of lamp assembles |
After
2D models the transfer to DXF format for use in the process of making
molds that will be used for parts. In this case the molds to press the
timber materials were made in 18mm plywood. Each mold consists of two
parts, where the parts will embedded burlap resin and LEDs; and cap
mold with which we can apply pressure to form a mixed structure of an
approximate width of 1cm. The following figures show the process of
preparation of the molds are shown in the following figures.
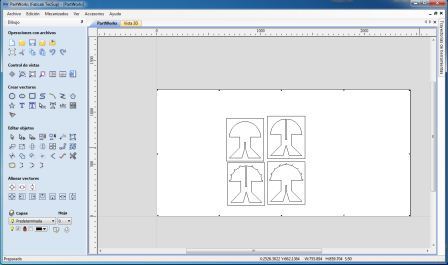 Figures 2D shows that the process will be used | 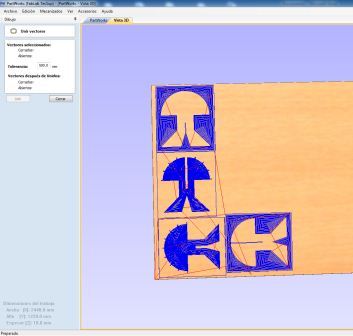 View the molds to be made. | 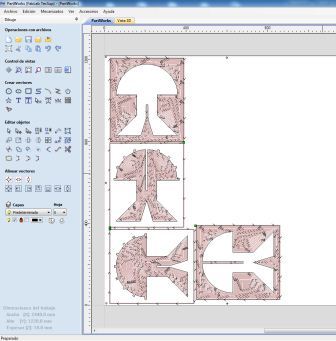 View of drill paths for the realization of the molds in low relief and high relief. |
Here are the configuration parameters In the process to draft and cut is.
The distribution of spaces in the molds were made as follows.
Then the machining process of the mold is shown.
The result of the machining process shown below.
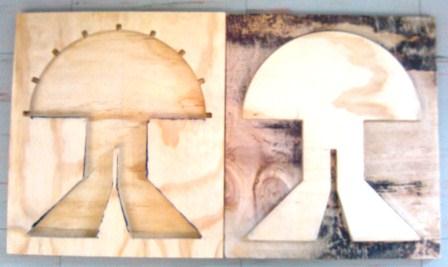 Mold Part 1 | 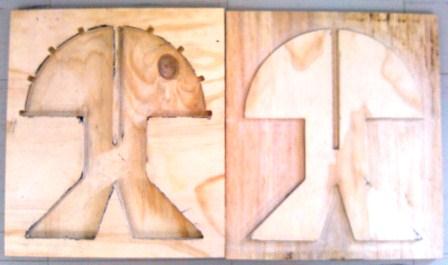 Molde Part 2 |
Finally; in this part of the cutting is done by laser acrylic mold molds proceeds to cut the fabric.
And produce a fiber composite part in it.
We will describe the steps to follow for the two models designed using the above materials.
First
we prepare the molds to save them, for this we must pierce the inner
parts with plastic surface so that the resin does not stick to the
wood.
Which
will carry it out using petrolatum and polyethylene plastic marerial
coating interior surfaces of the molds, both the cap and the inside
cover.
Proceed
to mix the components of the resin in a plastic resipiente as indicated
on the label containing the base plate. The ratio used is prepared 2x1
about 525gr. mixing which was casting layer by layer alternating with
jute templates (12 for each mold) to a thickness of about 1cm.
The
process was placed in the center of the LEDs with the connection cables
for this remain internally. The circuit diagram is used is shown below.
Against
placing among the top polyethylene plastic to prevent the resine
revalces ipregnaran the wooden mold and proceeded to press was placed.
The same procedure was performed with the other mold part and waited,
after about 25 minutes the mixture began to warm and from that moment I
hope 2 hours. After that time the top of the mold was removed and it
was found that the material was not done apparently by solidifying the
plastic did not allow air to penetrate the mix. to open it and leave it
so slow 35-minute get completely solid.
For
the process of stripping the plastic allowed the use of very easy way
do it without a problem and the two parts of the model are obtained
quickly and stay mold ready to be reused.
protruding parts were cut and burrs generated and mold pressing process and the two sides are smoothed lace.
When
assembling the two parts to be applied much force and broke one side of
the model so that we repair using the same material burlap and epoxy
resin mixture.
Finally
connectors LEDs joined and connected to a source of 25 volts thereby
achieving a model designed to obtain the LED lamp based on a structure
made of composite fiber material.
Thanks: Special thanks to instructors Alejandro, Roberto and assistants Eduardo and Jhon who supported me in the execution of the assignment.