FabLab Academy 2012
Manchester Lab
David Forgham-Bailey
The assignment this week was to
measure something - add a sensor to a microcontroller board and read it.
I decided to make all the example
boards to investigate the different sensors, and evaluate which whould
be appropriate for my final project.
When starting to mill the boards with the Modela the results were very
poor - part of the first board was not milled.
I decided to change the bit - I also ended up refitting the sacrificial
base plate.
Below shows a comparison of the bits under a microscope -
1/64th End Mill bits - under microscope to show worn tool:
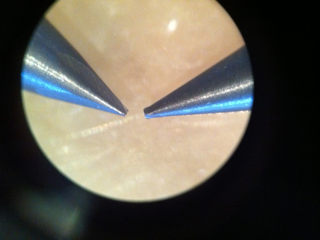
Completed boards: button/temp/mic/light/load/TxRx
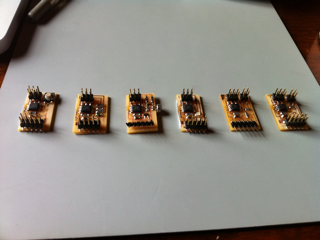
Each board was programmed by
compiling the c file using -
'sudo make -f hello.button.45
make' (substitute button with:
temp/mic/light/load/load/txrx)
and the board programmed by connecting the fabisp board -
'sudo make -f hello.button.45
make program-usbtiny' (substitute button with:
temp/mic/light/load/load/txrx)
The Fabisp was then disconnected and the FTDI cable was used to connect
the board to my computer via the usb.
To find out the FTDI port address type: 'ls /dev' in terminal - FTFAZYNF
To read the output using Python Ptinker type:
'python term.py /dev/tty.usbserial-FTFAZYNF 9600' - or -
'python rx.py /dev/tty.usbserial-FTFAZYNF 9600' - in
terminal
Button: term.py/ rx.py - should read 'd' when pressed/ 'u' when
not pressed: not always accurate with spurious characters being
output...
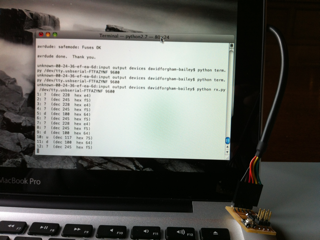
Temp: reading 181.6 at room temp/ 993.9 when touched with finger:
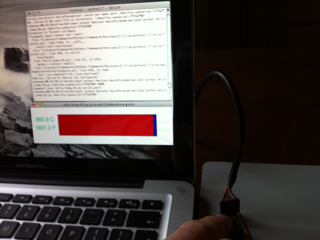
Mic: showing response to whistle (single tone):
Light: showing response 381.1 to ambient light/ 808.4 to shade
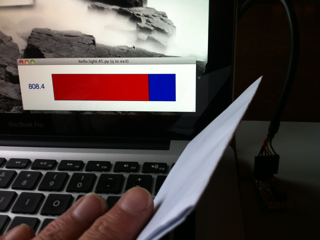
Step (TxRx): showing response 6234 open/ 32806 touched
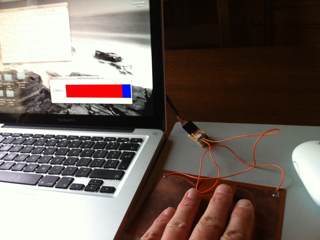
although each board gave an output the value od the result was not
calibrated.